In hydraulic and plumbing applications, the integrity of connections is paramount, and this is where thread sealants play a critical role. Proper sealing ensures that brass fittings maintain their effectiveness under varying pressure and environmental conditions. Without appropriate sealants, even the slightest imperfection can lead to leaks, compromising system efficiency and safety.
Are you looking for brass fitting sealants that can handle high pressures or extreme temperatures? The right choice of sealant can make all the difference in maintaining system performance and preventing costly leaks.
Understanding Brass Fittings and Their Applications
Brass fittings are a fundamental component in many hydraulic, plumbing, and industrial systems. Their versatility, durability, and compatibility with various fluids and gases make them a preferred choice across numerous applications.
What Are Brass Fittings?
Brass fittings are components used to connect, redirect, or terminate sections of piping or tubing within systems that transport liquids or gases. Made primarily from a copper-zinc alloy, brass fittings are designed to provide secure and leak-free connections. Commonly found in hydraulic systems, plumbing infrastructure, and other industrial setups, these fittings ensure efficient fluid transfer and system integrity under different operating conditions.
Why Brass?
Brass is favored for several key reasons:
Corrosion Resistance: Brass is naturally resistant to rust and corrosion, especially when exposed to water and non-corrosive fluids, making it ideal for plumbing and hydraulic systems.
Malleability: Brass is easier to shape and mold compared to harder metals like stainless steel. This malleability allows for precision manufacturing and tighter connections.
Temperature and Pressure Tolerance: Brass fittings can withstand a range of temperatures and pressures, though they are generally used in moderate conditions rather than extreme environments. This makes them suitable for a variety of residential, commercial, and light-industrial applications.
Suitability for Different Environments: Brass fittings are compatible with diverse environmental conditions, making them effective indoors and outdoors. Their resistance to temperature fluctuations and moisture contributes to their versatility.
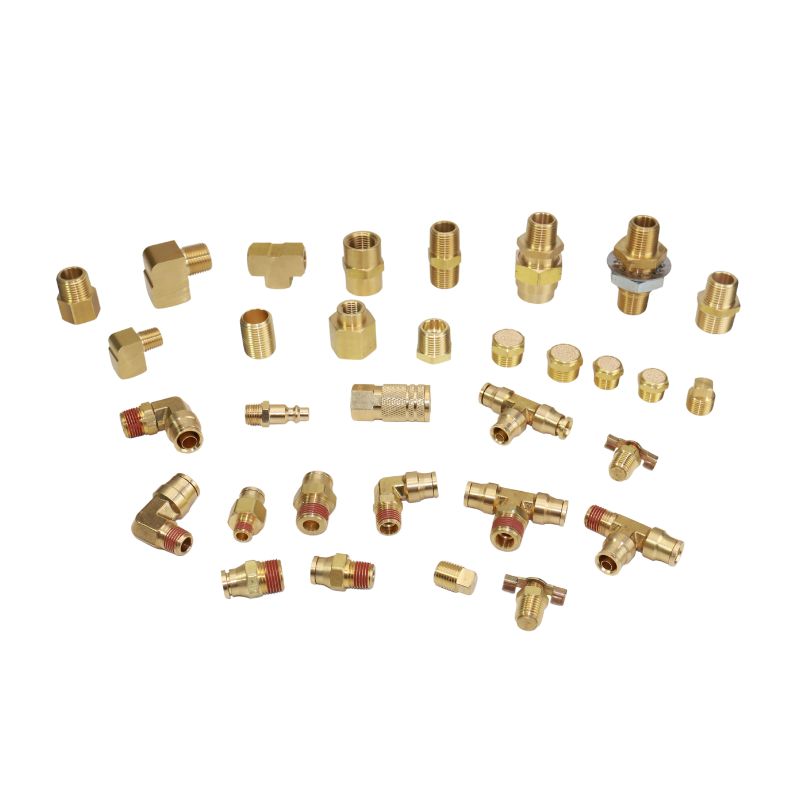
Types of Brass Fittings
There are several types of brass fittings, each suited for specific applications and sealing methods:
Fitting Type | Typical Use | Sealant Requirement |
Compression Fitting | Plumbing, pipe joining without heat | Thread sealant usually applied to threads |
Flare Fitting | High-pressure systems | Flare seals itself; sealant optional on threads |
Push-to-Connect | Quick install, low-pressure plumbing | Uses O-ring or thread sealant for watertight seal |
Barbed/Hose Fitting | Flexible hose connections | Sealant may be used; hose clamps add security |
Threaded (NPT) | Hydraulic & plumbing systems | Requires thread sealant or Teflon tape |
Industrial Applications of Brass Fittings
Hydraulic & Pneumatic Systems
Brass fittings are widely used in high-pressure hydraulic systems and pneumatic applications, such as:
Heavy machinery: Excavators, cranes, and industrial presses require robust fittings that can handle hydraulic oil under high pressure without leaking.
Air compressors: Brass fittings provide airtight connections in pneumatic systems, ensuring efficient air flow without pressure loss.
Manufacturing automation: Robotics and automated conveyor systems rely on brass fittings for precise and leak-free connections in pneumatic actuators.
Chemical & Processing Industries
Brass fittings are used in chemical processing plants, pharmaceutical manufacturing, and food production, where they must withstand exposure to acids, solvents, and other aggressive chemicals.
Example Applications:
Chemical transfer lines: Brass fittings ensure safe and corrosion-resistant connections for handling mild acids and industrial solvents.
Beverage and food processing: Used in breweries, dairy plants, and soft drink production lines due to their non-toxic properties.
Industry / System | Example Applications | Key Role of Brass Fittings |
Hydraulic & Pneumatic | Heavy machinery (excavators, cranes, presses) | Withstand high-pressure hydraulic oil without leaks |
Air compressors | Provide airtight connections, prevent pressure loss | |
Manufacturing automation (robots, conveyors) | Ensure precise, leak-free pneumatic control | |
Chemical & Processing | Chemical transfer lines | Corrosion-resistant connections for mild acids/solvents |
Food & beverage (breweries, dairy, soft drinks) | Non-toxic, safe for hygienic fluid handling |
Overview of Thread Sealants for Brass Fitting
Choosing the right thread sealant is essential for ensuring leak-free connections in brass fittings. Various types of sealants are available, each with distinct characteristics and applications. Below is an overview of the three primary types of thread sealants commonly used with brass fittings.
Types of Thread Sealants
Teflon Tape
Teflon tape, also known as PTFE (Polytetrafluoroethylene) tape, is a white, thin, and flexible tape used to wrap around the threads of fittings. It is chemically inert and resistant to moisture, making it suitable for a wide range of fluids.
Benefits:
Easy to apply and remove.
Provides a good seal against leaks.
Chemically resistant to most fluids.
Suitable for both high and low-pressure applications.
Limitations:
Can be prone to over-wrapping, which may lead to difficulties in tightening fittings.
Not recommended for large gaps or uneven surfaces as it cannot fill voids.
May degrade over time when exposed to certain chemicals or extreme temperatures.
Liquid Pipe Sealants
Composition: Liquid pipe sealants are typically made from a blend of synthetic resins and fillers that cure to form a solid seal. They can be used on various materials, including metals and plastics.
Effectiveness: These sealants effectively fill gaps and imperfections in the threads, creating a robust seal that prevents leaks under pressure. They cure quickly, providing immediate sealing capabilities.
Ideal Applications: Liquid sealants are ideal for hydraulic systems, high-pressure gas lines, and situations where Teflon tape may not provide a sufficient seal due to irregular thread surfaces or large gaps.
Anaerobic Sealants
Usage: Anaerobic sealants are designed to cure in the absence of air, making them particularly effective for sealing threaded metal connections, including brass fittings. They form a strong bond and are often used in high-pressure applications.
Benefits:
Excellent resistance to vibration and thermal cycling.
Provides a robust seal that can handle extreme pressures.
Ideal for permanent applications as they harden into a solid mass.
Limitations:
Requires clean surfaces for optimal adhesion; any contamination can reduce effectiveness.
Generally not suitable for disassembly without breaking the bond.
Sealant Type | Advantages | Disadvantages | Best For |
Teflon Tape | -Easy to apply and remove -Chemically resistant -Works for high/low pressure | -Can over-wrap and impede fitting -Not for large gaps -May degrade over time | High-pressure hydraulic systems |
Liquid Sealants | -Fills gaps effectively Cures quickly -Versatile for various materials | -Can be messy to apply -May require curing time for full strength | -Can be messy to apply -May require curing time for full-strength |
Anaerobic Sealants | -Excellent pressure resistance -Ideal for permanent seals -Handles vibration well | -Requires clean surfaces -Hard to disassemble after curing | General plumbing and low-pressure systems |
Factors to Consider When Choosing a Thread Sealant
When selecting a thread sealant for brass fittings, several critical factors must be considered to ensure optimal performance and longevity. Understanding these factors can help prevent leaks, reduce maintenance costs, and enhance the overall efficiency of the hydraulic or plumbing system.
Compatibility with Hydraulic Fluids and Other Media
Importance of Matching Sealant with Fluid Type: Different fluids—such as water, oil, and various chemicals—interact differently with sealants. It’s essential to choose a sealant that is chemically compatible with the medium it will be exposed to.
Water: Most sealants perform well with water; however, some sealants may degrade over time when constantly exposed to moisture.
Oil: Ensure that the selected sealant can withstand oil-based fluids, as certain sealants may not hold up under these conditions.
Chemicals: For systems involving aggressive chemicals, it’s vital to consult compatibility charts or manufacturer specifications to avoid sealant degradation.
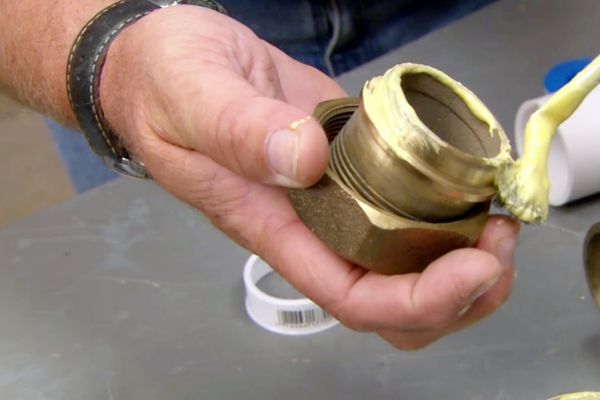
Operating Temperature and Pressure
Selection Based on Temperature: Each sealant has a specified temperature range. It’s crucial to select a sealant that can operate effectively within the temperature limits of the application.
Low Temperatures: Some sealants may become brittle or lose their sealing properties at low temperatures.
High Temperatures: Sealants must be able to withstand heat without breaking down or losing adhesion, especially in high-temperature applications like automotive or industrial systems.
Pressure Considerations: The sealant must also be rated for the specific pressure conditions it will face. High-pressure systems, such as those found in hydraulic machinery, require robust sealants that can maintain integrity under stress.
Environmental Conditions
Indoor vs. Outdoor Use: Sealants used indoors may not need to withstand the same environmental stresses as those used outdoors. Outdoor sealants should be resistant to UV light, temperature fluctuations, and moisture.
Resistance to Moisture and Corrosion: In environments where exposure to water or chemicals is common, choosing a sealant that offers excellent moisture resistance and corrosion protection is vital. This ensures long-lasting seals that do not degrade over time.
Vibration Resistance: For applications prone to vibration—such as machinery or vehicles—selecting a sealant that can maintain its sealing properties under these conditions is critical. Anaerobic sealants often excel in these scenarios.
Ease of Application and Maintenance
Application Process: The ease of applying the sealant can influence the choice, especially for those who may not have extensive experience. Teflon tape is generally easier for DIY projects, while liquid and anaerobic sealants may require more skill.
Curing Time: Some sealants cure quickly, allowing for faster system reassembly, while others may require extended curing times. This can impact project timelines and operational downtime.
Maintenance Considerations: Understanding the maintenance needs of the chosen sealant is crucial for longevity. Some sealants may require periodic checks or reapplication, while others may be more permanent. Selecting a sealant with lower maintenance needs can reduce long-term costs and improve system reliability.
Choosing the Right Sealant for Different Scenarios
Case 1: High-Pressure Hydraulic System
Application Scenario: You are repairing a high-pressure hydraulic oil pipe used in industrial machinery, operating at 3,000 psi (approximately 207 bar).
Challenges: The sealant must withstand extreme pressure and resist chemical degradation from hydraulic oil to prevent leaks that could lead to serious mechanical failures.
Recommended Sealant: Anaerobic Sealant
Reason: This type of sealant fills thread gaps and cures in the absence of air, forming a strong, high-pressure-resistant bond that prevents leaks.
Application Steps:
Clean the threads thoroughly.
Apply the anaerobic sealant evenly.
Assemble the fitting securely.
Allow the sealant to cure according to the manufacturer’s instructions.
Case 2: Residential Plumbing Repair
Application Scenario: A household hot water pipe has developed a minor leak and needs to be repaired. The system operates at temperatures between 0 and 80°C and a pressure of 50 to 100 psi.
Challenges: The sealant must be easy to apply, removable, and provide effective waterproof sealing.
Recommended Sealant: PTFE Thread Seal Tape (Teflon Tape)
Reason: Teflon Tape is ideal for low-pressure water pipes, easy to use, and does not require curing time.
Application Steps:
Wrap 2-3 layers of Teflon Tape around the male threads, moving in the same direction as the threading.
Smooth the tape onto the threads to ensure a secure fit.
Assemble the fitting and tighten it securely.
Impact of Environmental Factors & Selection Recommendations
Impact / Situation | Recommended Sealant Type | Example Applications | Key Recommendation |
Extreme Temperatures (< -40°C / > 150°C) | High/low-temp resistant sealants (liquid or silicone-based) | Cold storage (Permatex High-Temp Sealant), Steam pipelines, automotive exhaust (Loctite 592) | Avoid regular Teflon tape; use certified sealants |
Vibration & Mechanical Stress | Vibration-resistant anaerobic sealants (e.g., Loctite 567), rubber-based sealants | Automotive engines, industrial pumps, vibrating machinery | Do not use Teflon tape; choose vibration-resistant sealants |
Moisture & Corrosive Exposure | PTFE liquid sealants, corrosion-resistant compounds | Marine pipelines (marine-grade), chemical plants (chemical-resistant sealants) | Avoid standard PTFE tape; use corrosion-proof sealants |
Step-by-Step Guide: Applying Thread Sealant to Brass Fittings
Proper application of thread sealants is essential for ensuring reliable and leak-free connections in brass fittings. This step-by-step guide covers the preparation, application techniques, and best practices for using different types of sealants, ensuring optimal performance and longevity.
Preparing the Surface
Cleaning the Threads:
Before applying any sealant, thoroughly clean the threads of the brass fittings to remove any dirt, oil, or debris. This can be done using a brush and a solvent such as isopropyl alcohol or a dedicated thread-cleaning solution.
Inspecting the Threads:
Check for any damage or irregularities in the threads. Damaged threads may not seal properly even with the application of a sealant, so ensure the fittings are in good condition before proceeding. Replace any fittings with visible wear or deformation.
Applying Teflon Tape
Choosing the Right Tape:
For brass fittings, use PTFE (Teflon) tape suitable for plumbing or hydraulic applications. Make sure the tape is of appropriate thickness (typically 0.0035 inches) for effective sealing.
Wrapping Technique:
Start wrapping the tape around the male threads of the fitting, beginning one or two threads back from the end to avoid obstructing the opening.
Wrap the tape in the direction of the threads (clockwise if viewed from the front of the fitting). This ensures that the tape does not unravel when the fitting is screwed in.
Apply 2-3 layers of tape, making sure it is snug and evenly distributed. Avoid over-wrapping, as this can make it difficult to tighten the fitting properly.
Smoothing the Tape:
Once wrapped, press the tape into the threads to ensure it conforms and adheres properly. This provides a better seal when the fitting is tightened.
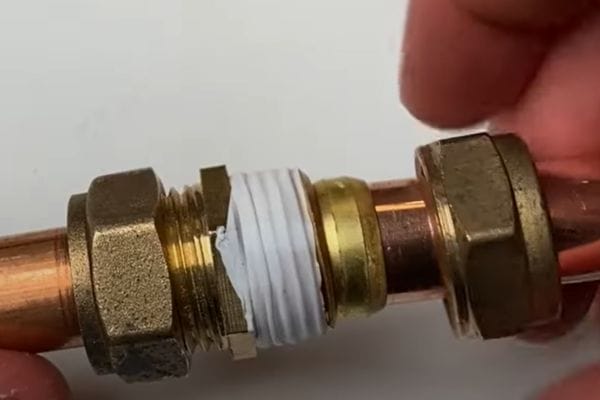
Using Liquid Sealants
Selecting the Appropriate Sealant:
Choose a liquid sealant compatible with brass and the type of fluid the system will carry. For hydraulic or high-pressure applications, anaerobic sealants are often recommended as they provide a stronger bond.
Application Technique:
Apply a small amount of the liquid sealant directly to the male threads. Avoid applying too much, as excess sealant can squeeze out and potentially clog the system.
Distribute the sealant evenly by spreading it around the threads using a brush or the nozzle provided with the product. Ensure that all threads are covered for a uniform seal.
Allowing for Curing:
Depending on the type of liquid sealant, some may require a short curing period before assembly. Follow the manufacturer’s instructions to determine the appropriate curing time.
Best Practices for Ensuring a Leak-Free Connection
Tightening the Fittings:
When connecting the fittings, tighten them according to the manufacturer’s torque specifications. Over-tightening can damage the threads, while under-tightening may result in leaks.
Use appropriate tools, such as an adjustable wrench, and apply even pressure. For fittings sealed with Teflon tape, ensure the tape does not bunch up or tear during tightening.
Testing for Leaks:
After assembly, conduct a pressure test or run the system with the appropriate fluid to check for leaks. Inspect all connections visually and use a leak detection spray or soapy water to identify any escaping air bubbles.
Adjusting as Needed:
If any leaks are detected, disassemble the connection, reapply the sealant, and reassemble. Ensure that the surfaces are clean and the sealant is applied correctly to avoid repeated issues.
Common Mistakes and How to Avoid Them
Ensuring leak-free connections in brass fittings requires attention to detail and adherence to best practices. Here are common mistakes to avoid, along with strategies to prevent them.
Over-tightening the Fittings
Explanation: Over-tightening can cause significant damage to the threads of brass fittings, leading to deformities and increasing the risk of leaks. Brass is a relatively soft metal, and excessive torque can strip threads or crack the fitting.
How to Avoid:
Always use a torque wrench or follow the manufacturer’s specifications for tightening. Aim for a snug fit without excessive force, and check for leaks after initial tightening, making minor adjustments as needed.
Using the Wrong Sealant
Examples of Incompatible Sealants:
Some sealants, such as those designed for plastic pipes, may not adhere properly to brass, leading to premature failure. For instance, rubber-based sealants can degrade when in contact with certain hydraulic fluids or high temperatures.
Effects:
Incompatible sealants can cause leaks, require frequent reapplication, and lead to system failures. Always verify the compatibility of the sealant with the fluids and materials involved.
How to Avoid:
Consult the product specifications and compatibility charts before selecting a sealant. Choose a sealant specifically designed for use with brass fittings and the type of fluid being conveyed.
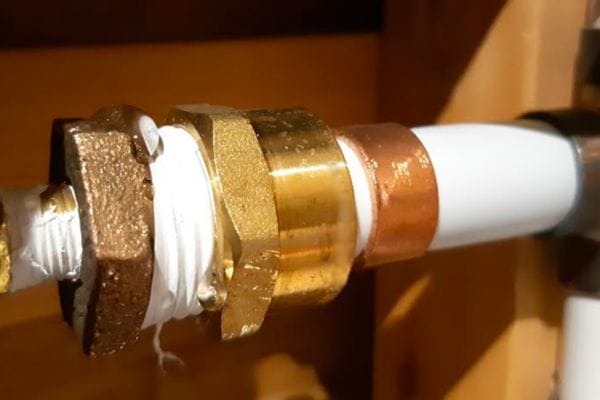
Inadequate Preparation of Fittings
Importance of Cleaning and Preparing Threads:
Failing to clean the threads can result in poor adhesion of the sealant, leading to weak seals and leaks. Contaminants like oil, dirt, or old sealant residues can compromise the effectiveness of any sealant applied.
How to Avoid:
Thoroughly clean the threads of both the male and female fittings using a brush and solvent. Inspect for damage and ensure the surfaces are dry and free of contaminants before applying any sealant. Proper preparation sets the foundation for a strong, reliable seal.
Conclusion
In conclusion, selecting the appropriate thread sealant for brass fittings is crucial for ensuring reliable, leak-free connections in hydraulic and plumbing systems. Proper application techniques, such as preparing the threads and using the correct sealant for the specific fluid and temperature conditions, play a key role in maintaining system integrity and efficiency. Choose sealants based on system requirements, environmental conditions, and ease of application. Always consult product specifications, seek professional advice when uncertain, and implement regular maintenance to ensure long-term system efficiency and reliability.
Ready to find the perfect sealant? Explore our recommended sealants today and follow our step-by-step guide for a hassle-free installation. If you need expert advice, don’t hesitate to reach out to a professional for tailored recommendations. Ensure your connections stay secure—choose the right sealant now!
FAQ
Can I use any thread sealant on brass fittings?
No, it’s important to choose a sealant compatible with brass and the type of fluid the system uses. For example, some sealants work well with water but may degrade in oil-based systems.
Is Teflon tape enough for sealing brass fittings?
Teflon tape is suitable for many low- to medium-pressure applications but may not be sufficient for high-pressure systems or irregular threads where liquid or anaerobic sealants provide a stronger seal.
How many layers of Teflon tape should I use on brass fittings?
Typically, 2-3 layers of Teflon tape are sufficient. Over-wrapping can cause the fitting to be difficult to tighten and may lead to improper sealing.
What happens if I over-tighten brass fittings?
Over-tightening can deform or damage the threads, leading to leaks. Always tighten to the manufacturer’s recommended torque specifications.
Can I use anaerobic sealants for all types of fittings?
Anaerobic sealants are ideal for high-pressure brass fittings but are not recommended for applications where the connection may need to be disassembled frequently, as they create a permanent bond.
How often should I check brass fittings for leaks?
It’s recommended to inspect fittings regularly, especially in high-pressure systems, and after installation or maintenance. Depending on the application, monthly checks might be necessary.