Given the variety of hose clamps available, selecting the appropriate type for your specific needs can be challenging. Different applications require different clamps based on factors like hose material, pressure conditions, and environmental exposure. This post aims to demystify the process of choosing the right hose clamp by providing essential tips and insights into the various types available.
Types of Hose Clamp
Worm Gear Clamps
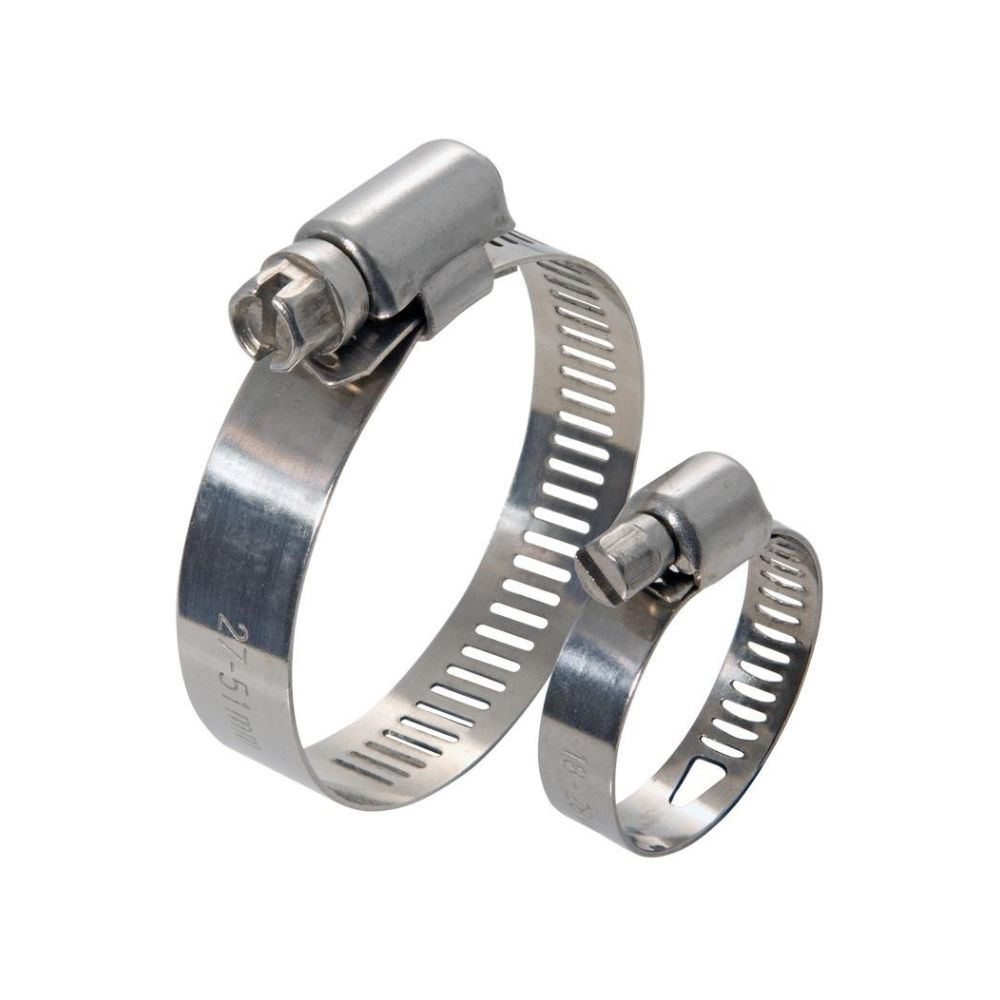
Description: Worm gear clamps, also known as screw clamps, feature a metal band with a screw mechanism that tightens the band around the hose. The screw threads engage with a worm gear to adjust the diameter of the clamp, providing a secure fit.
Applications: These clamps are versatile and commonly used in automotive, plumbing, and industrial applications. They are ideal for securing hoses to fittings in environments where varying pressure levels and hose diameters are encountered.
Advantages:
Adjustability: This can be tightened to fit various hose sizes.
Ease of Use: Simple to install and adjust with basic tools.
Availability: Widely available and cost-effective.
Disadvantages:
Corrosion Risk: Metal bands and screws may corrode over time, especially in harsh environments.
Potential for Over-tightening: Excessive tightening can damage the hose or fitting.
Spring Clamps
Description: Spring clamps use a spring mechanism to provide constant clamping pressure. They are typically made from stainless steel and have a curved band that snaps into place around the hose.
Applications: Ideal for use in automotive and industrial settings where hoses experience fluctuations in pressure or temperature. Commonly used in applications where a constant clamping force is required.
Advantages:
Self-tightening: The spring mechanism adjusts to changes in hose diameter or pressure.
Durability: Resistant to corrosion and can withstand high temperatures.
Consistency: Provides a constant clamping force without manual adjustment.
Disadvantages:
Limited Adjustability: Fixed size may not be suitable for varying hose diameters.
Installation Difficulty: Can be challenging to install and remove without specialized tools.
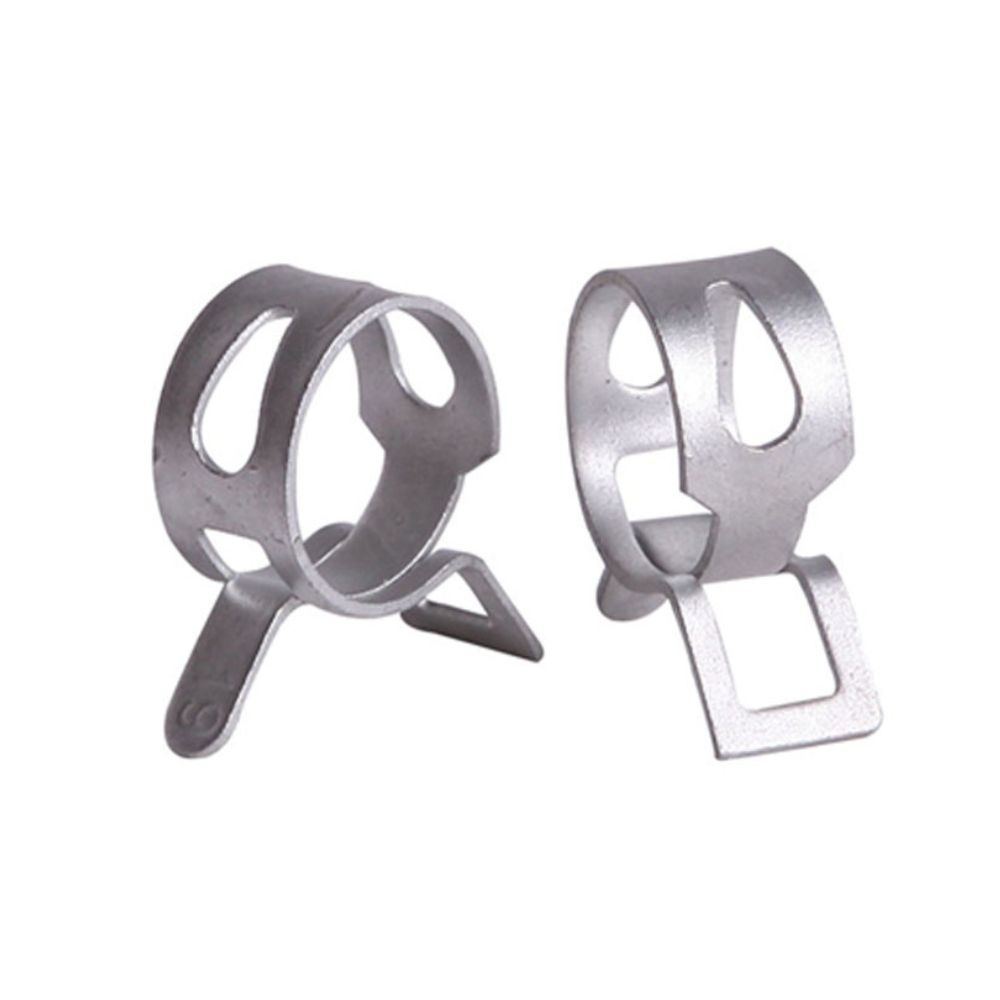
Constant Torque Clamps
Description: Constant torque clamps are designed to maintain a consistent clamping force despite changes in temperature or pressure. They feature a band with a built-in spring mechanism or adjustment screw that ensures a uniform clamping force.
Applications: Used in high-pressure and high-temperature applications, such as in automotive engines and hydraulic systems. Ideal for situations where maintaining a constant clamping pressure is crucial.
Advantages:
Consistent Performance: Maintains a constant clamping force, reducing the risk of leaks.
Adaptability: Adjusts to changes in hose diameter and pressure.
Durability: Resists temperature fluctuations and corrosion.
Disadvantages:
Cost: Generally more expensive than other types of clamps.
Complexity: This may require more complex installation and adjustment.
T-Bolt Clamps
Description: T-bolt clamps are heavy-duty clamps that use a T-shaped bolt and nut to tighten the band around the hose. They are designed for high-pressure applications and provide a robust, secure fit.
Applications: Commonly used in automotive and industrial applications where high pressure and vibration are present. Suitable for securing hoses in high-performance engines and heavy machinery.
Advantages:
Strength: Provides a strong and secure clamping force, suitable for high-pressure applications.
Durability: Made from high-quality materials, often resistant to corrosion and extreme conditions.
Adjustability: Can be adjusted to fit various hose sizes and pressures.
Disadvantages:
Bulkiness: Larger and bulkier than other types of clamps, which may be unsuitable for tight spaces.
Cost: Typically more expensive than other clamp types due to their heavy-duty design.
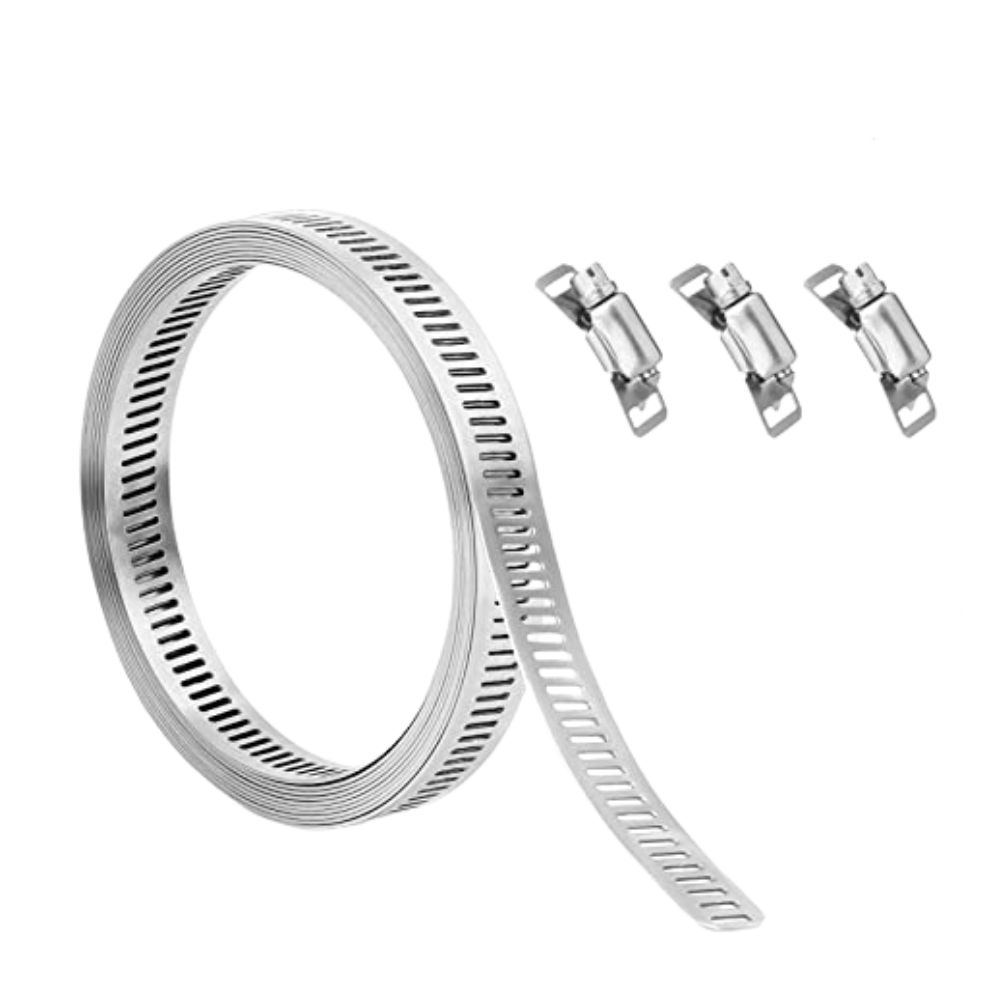
Band Clamps
Description: Band clamps consist of a flat metal band that wraps around the hose and a mechanism to tighten the band. They can be either adjustable or fixed-size, depending on the design.
Applications: Used in a variety of applications, including plumbing, automotive, and industrial settings. Suitable for securing hoses that need a uniform clamping force over a larger surface area.
Advantages:
Even Distribution: Provides an even clamping force across the hose.
Flexibility: Available in both adjustable and fixed sizes to fit different needs.
Versatility: Can be used in a wide range of applications and environments.
Disadvantages:
Installation: May require more effort to install compared to other types of clamps.
Maintenance: Adjustable clamps may need periodic tightening to maintain a secure fit.
Material Considerations
Stainless Steel
Benefits and Drawbacks: Stainless steel is known for its excellent resistance to corrosion and high temperatures. It offers robust strength and durability, making it suitable for harsh environments. The main drawbacks include its higher cost compared to other materials and the potential for rust in extremely aggressive environments if not properly treated.
Best Applications: Stainless steel clamps are ideal for use in marine, chemical, and food processing industries due to their resistance to corrosion and ability to withstand high temperatures. They are also used in automotive and aerospace applications where high strength and reliability are required.
Zinc-Plated Steel
Benefits and Drawbacks: Zinc-plated steel clamps are coated with a layer of zinc to improve resistance to corrosion. They are generally more affordable than stainless steel and provide good strength for moderate applications. However, the zinc coating can wear off over time, especially in harsh environments, which may lead to rust and reduced lifespan.
Best Applications: These clamps are suitable for general-purpose applications where moderate corrosion resistance is sufficient. Commonly used in automotive and agricultural settings, they are also appropriate for standard plumbing and HVAC systems.
Plastic Clamps
Benefits and Drawbacks: Plastic clamps are lightweight and resistant to corrosion, making them ideal for use in environments where metal clamps may not be suitable. They are often cost-effective and easy to install. However, plastic clamps may not offer the same strength and durability as metal clamps and can be affected by extreme temperatures and UV exposure.
Best Applications: Plastic clamps are best suited for light-duty applications such as securing hoses in garden irrigation systems, low-pressure plumbing, and some automotive and HVAC applications where corrosion resistance is important but extreme strength is not required.
Specialty Materials
Benefits and Drawbacks: Specialty materials, such as titanium or high-performance alloys, offer exceptional strength, corrosion resistance, and durability. These materials are often used in specialized applications that require superior performance under extreme conditions. The main drawbacks include their high cost and limited availability.
Examples of Applications:
Titanium Clamps: Used in aerospace and high-performance motorsport applications due to their lightweight and strength.
High-Performance Alloys: Employed in chemical processing and high-temperature environments where standard materials would fail.
Rubber Coated Clamps: Used in automotive and machinery where vibration absorption and protection against abrasion are needed.
How to Choose the Right Size
Measuring Hose Diameter
Tools and Techniques: Accurate measurement of the hose diameter is crucial for selecting the right size clamp. Here are the tools and techniques to ensure a precise measurement:
Calipers: For a high level of accuracy, use a caliper to measure the inner diameter of the hose. Digital calipers provide the most precise readings.
Tape Measure: If calipers are not available, a flexible tape measure can be used to measure the circumference of the hose. Convert this measurement to diameter using the formula: Diameter = Circumference / π (3.14159).
Hose Measurement Tool: Specialized hose measurement tools are designed for quick and accurate readings, often including a gauge that provides both diameter and circumference measurements.
When measuring, ensure that the hose is at its normal operating pressure and temperature, as it may expand or contract under different conditions.
Clamp Size Chart
How to Use: Clamp size charts are useful for selecting the correct clamp based on the hose diameter. Here’s how to use them:
Identify Hose Diameter: Measure the inner diameter of the hose as described above.
Refer to the Chart: Locate the measured diameter on the clamp size chart. Charts typically list a range of diameters that each clamp size can accommodate.
Select the Appropriate Clamp: Choose a clamp that fits within the range specified for the diameter of your hose. Ensure that the clamp’s size range slightly exceeds the hose diameter to provide a secure fit.
Size charts are usually provided by clamp manufacturers and can be found in product catalogs or on their websites. Some charts also indicate the range of hose pressures and temperatures that the clamp can handle.
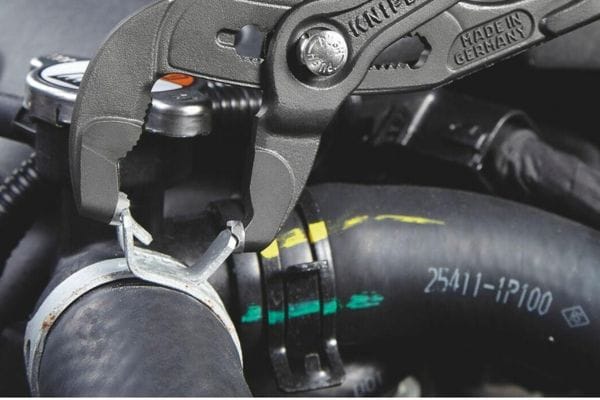
Adjustable vs. Fixed Sizes
Adjustable Clamps
Pros:
Versatility: Can fit a range of hose diameters, making them suitable for applications where the exact size may vary.
Ease of Installation: Adjustability allows for easier installation on hoses of different sizes without requiring multiple clamps.
Cost-Effective: Often less expensive than having to purchase multiple fixed-size clamps.
Cons:
Potential for Over-tightening: Adjustability can lead to over-tightening if not properly set, which may damage the hose or fitting.
Less Secure Fit: This may not provide as tight a fit as a clamp that is specifically sized for the hose, potentially leading to leaks.
Fixed-Size Clamps
Pros:
Secure Fit: Provides a snug, precise fit for hoses of a specific diameter, reducing the risk of leaks.
Durability: Typically stronger and more durable for applications where the hose diameter is consistent.
Cons:
Limited Flexibility: Not suitable for hoses that vary in diameter. Multiple sizes may need to be stocked, increasing costs and inventory management.
Installation Complexity: Requires accurate measurement of the hose diameter before installation, which may be inconvenient if multiple hose sizes are used.
Installation Tips
Proper Tools for Installation
Recommended Tools:
Screwdriver: For worm gear and T-bolt clamps, a screwdriver is essential for adjusting the tightening mechanism.
Socket Wrench: Used for T-bolt clamps and some specialty clamps, providing a more secure and even tightening.
Pliers: Useful for spring clamps and plastic clamps to compress and secure them around the hose.
Caliper or Tape Measure: For verifying hose and clamp sizes before installation.
Lubricant: A light lubricant can help slide clamps into place, especially for larger sizes or when working with tight-fitting hoses.
Installation Techniques
Prepare the Hose and Fitting:
Ensure that the hose and fitting are clean and free of debris.
If needed, lightly lubricate the hose or fitting to facilitate easier installation of the clamp.
Measure and Select the Clamp:
Use a caliper or tape measure to verify the hose diameter.
Select the appropriate size clamp based on your measurement and the manufacturer’s size chart.
Position the Clamp:
Place the clamp over the hose end, ensuring it is centered and properly aligned with the fitting. For clamps with a screw or bolt mechanism, position it so that the tightening mechanism is easily accessible.
Tighten the Clamp:
For worm gear and T-bolt clamps, use a screwdriver or socket wrench to tighten the clamp evenly around the hose. Ensure that the band is snug but not excessively tight.
For spring clamps, use pliers to compress the spring and slide the clamp into place. Release the clamp to ensure it grips the hose securely.
For plastic clamps, ensure that the clamp’s locking mechanism is engaged properly, either by snapping it into place or by tightening the screw, depending on the design.
Check the Fit:
After installation, verify that the clamp is evenly tightened and that there are no gaps between the clamp and the hose.
For adjustable clamps, double-check the size and ensure the clamp is positioned correctly to prevent slipping.
Test the Installation:
If possible, pressurize the system to check for leaks around the clamp. Adjust the tightness if necessary to ensure a secure seal.
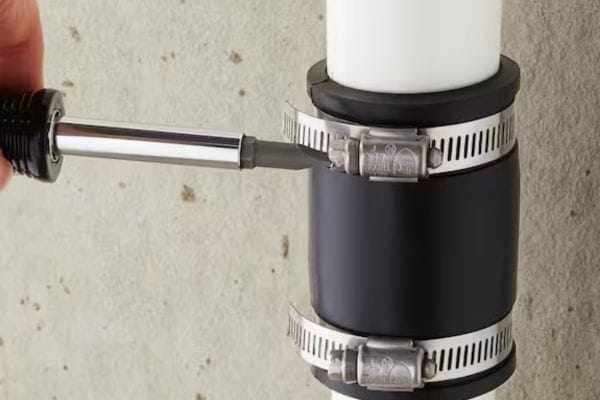
Common Mistakes to Avoid
Incorrect Sizing:
Error: Using a clamp that is too large or too small for the hose.
Prevention: Always measure the hose diameter accurately and refer to the clamp size chart. Consider using adjustable clamps if precise sizing is challenging.
Over-tightening:
Error: Applying too much pressure when tightening the clamp, can damage the hose or fitting.
Prevention: Tighten the clamp until it is snug but not excessively tight. If using a torque wrench, follow the manufacturer’s recommended torque specifications.
Misalignment:
Error: Positioning the clamp incorrectly, leading to uneven pressure distribution and potential leaks.
Prevention: Ensure that the clamp is centered and aligned properly on the hose. Verify that the clamp covers the entire area where the hose meets the fitting.
Ignoring Manufacturer Guidelines:
Error: Not following specific installation instructions or recommendations provided by the clamp manufacturer.
Prevention: Review and adhere to the installation guidelines provided by the manufacturer. This ensures optimal performance and longevity of the clamp.
Inadequate Inspection:
Error: Failing to check the clamp installation after it is completed.
Prevention: Perform a final inspection to ensure that the clamp is properly tightened and the hose is securely attached. Test the system to check for leaks and make necessary adjustments.
Industry Standards and Regulations
Relevant Standards
ISO (International Organization for Standardization):
ISO 9001: This standard ensures quality management systems are in place, which affects the overall manufacturing and performance of clamps.
ISO 14540: Specifically related to clamps, detailing the design, materials, and performance requirements for various types of clamps used in hydraulic and industrial applications.
SAE (Society of Automotive Engineers):
SAE J20: Provides specifications for hose and hose assemblies, which includes guidelines for the clamps used to secure these hoses in automotive applications.
SAE J231: Defines performance standards for automotive clamps, including dimensions and testing methods.
DIN (Deutsches Institut für Normung):
DIN 3017: Covers clamps and their requirements, including dimensions and performance criteria, ensuring compatibility with various hoses and fittings.
ANSI (American National Standards Institute):
ANSI/ASME B18.6.1: Includes specifications for clamps, detailing dimensions, and performance standards for American-made products.
Conclusion
Selecting the right hose clamp is crucial for the reliability and efficiency of your system. By carefully evaluating the type, material, and size of the clamp, and adhering to proper installation techniques, you can prevent leaks, ensure safety, and extend the lifespan of your hoses and fittings. Make informed choices based on your specific needs to achieve the best performance and avoid costly repairs or replacements.
FAQ
What is the primary function of a hose clamp?
Clamps are used to secure hoses onto fittings or connections, preventing leaks and ensuring a tight seal. They are essential for maintaining the integrity of fluid or gas systems.
How do I measure the correct size for a hose clamp?
To measure the correct size, use a caliper or tape measure to determine the inner diameter of the hose. Refer to the clamp size chart provided by the manufacturer to select a clamp that fits within this measurement range.
What materials are commonly used for clamps?
Common materials include stainless steel, zinc-plated steel, and plastic. Stainless steel offers high corrosion resistance, while zinc-plated steel is cost-effective for moderate conditions. Plastic clamps are lightweight and resistant to corrosion.
What are the differences between adjustable and fixed-size clamps?
Adjustable clamps can accommodate a range of hose diameters and are versatile for various applications. Fixed-size clamps are designed for specific hose diameters and offer a more precise and secure fit.
How do I install a hose clamp correctly?
Position the clamp over the hose and fitting, then tighten it using the appropriate tool, such as a screwdriver or pliers. Ensure the clamp is evenly tightened and check for leaks once the system is pressurized.
How can I ensure my clamps meet industry standards?
Verify that your clamps come with certification and documentation from the manufacturer. Regularly test clamps for compliance with relevant standards.