Hose clamps are crucial components in hydraulic systems, providing secure connections between hoses and fittings to ensure fluid containment and system integrity. Their role is fundamental in maintaining the efficiency and safety of hydraulic operations, as they prevent leaks, manage pressure fluctuations, and support system reliability. Without properly functioning hose clamps, even the most advanced hydraulic systems can suffer from performance issues and potential failures.
Understanding Hose Clamps
Definition and Types of Hose Clamps
Hose clamps are devices used to secure hoses over fittings or nozzles, preventing them from slipping off and ensuring a tight, leak-proof seal. They come in various designs, each suited for different applications and requirements. The primary types include:
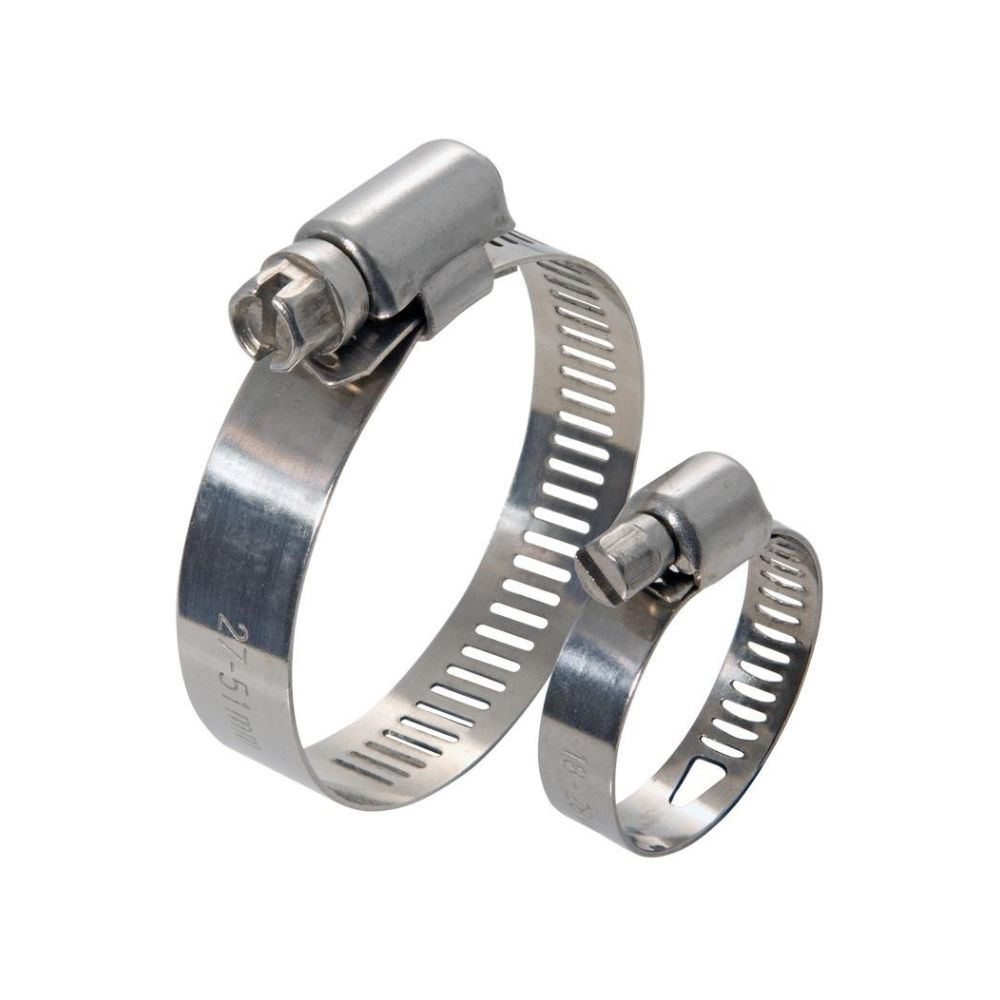
Spring Clamps: These use a spring-loaded mechanism to apply constant pressure on the hose, accommodating variations in hose size due to temperature changes. They are self-adjusting and commonly used in automotive applications.
Screw Clamps: Featuring a band with a threaded screw, these clamps can be tightened or loosened to adjust the clamp’s diameter. They are versatile and widely used in both automotive and industrial settings.
Ear Clamps: Made from a band of stainless steel with one or two ‘ears’ that are crimped to tighten the clamp around the hose. They offer a secure fit and are often used in high-pressure applications.
Worm Gear Clamps: These have a band with a worm gear mechanism for precise adjustment. They are used in various applications due to their ability to provide a tight, adjustable fit.
Permanently Mounted Clamps: These clamps are fixed in place and are not adjustable. They are used in applications where a permanent, tamper-proof solution is needed.
Key Components and How They Function
Band: The primary component that wraps around the hose and applies pressure. It is usually made of stainless steel or other durable materials to resist corrosion and wear.
Screw or Bolt: Used to adjust the tension of the clamp. In screw clamps, turning the screw tightens or loosens the band. In spring clamps, the spring exerts constant pressure without the need for manual adjustment.
Housing: The part that contains the screw mechanism in screw clamps or the spring mechanism in spring clamps. It provides the structural support necessary for the clamp’s operation.
Lining (optional): Some clamps have a lining to protect the hose from abrasion and to enhance the seal. This lining can be made from rubber, plastic, or other materials.
When installed correctly, these components work together to create a strong, durable seal that prevents leaks and maintains the hydraulic system’s efficiency.
Selection Criteria for Different Applications
Pressure and Temperature Requirements: Choose clamps based on the operating pressure and temperature of the system. High-pressure systems may require more robust clamps, such as worm gear or ear clamps, while standard applications may use spring or screw clamps.
Material Compatibility: Ensure that the clamp material is compatible with the hose and the environment. Stainless steel clamps are resistant to corrosion and are suitable for harsh environments, while plastic clamps may be appropriate for less demanding conditions.
Hose and Fitting Sizes: Select clamps that match the diameter of the hose and the fitting. Proper sizing is crucial for achieving a secure fit and preventing leaks.
Ease of Installation: Consider how easy the clamp is to install and adjust. Some applications may benefit from adjustable clamps like screw or worm gear clamps, while others may require the permanence of ear clamps.
Environmental Factors: Take into account factors like exposure to chemicals, moisture, or extreme temperatures. Clamps should be chosen based on their ability to withstand these conditions without degrading.
Common Hose Clamp Failures
Over-Tightening
Causes and Effects
Over-tightening occurs when a hose clamp is applied with excessive force, often due to the use of improper tools or incorrect installation practices. This issue can be caused by the desire to ensure a leak-proof seal or a misunderstanding of the appropriate torque specifications for the clamp. Over-tightening compresses the hose more than necessary, potentially causing damage to both the hose and the clamp.
The primary effects of over-tightening include:
Hose Deformation: Excessive pressure can cause the hose to collapse or deform, affecting its ability to carry fluids properly. This deformation may lead to reduced flow capacity or internal damage.
Clamp Damage: The clamp itself may become distorted or weakened, which can compromise its ability to maintain a secure connection.
Signs of Over-Tightening
Visible Hose Deformation: Look for signs that the hose is squeezed or flattened, indicating excessive pressure from the clamp.
Leakage: Ironically, over-tightening can sometimes cause leaks if the hose material is damaged or if the clamp cannot hold the excessive pressure.
Clamp Distortion: Examine the clamp for any bending or warping, which suggests that too much force was applied.
Under-Tightening
Causes and Effects
Under-tightening happens when a hose clamp is not tightened sufficiently, often due to improper torque settings or oversight during installation. This can result from a lack of familiarity with the correct specifications or the use of inadequate tools.
The primary effects of under-tightening include:
Leakage: An insufficiently tightened clamp may not create a secure seal, leading to fluid leaks around the connection. This can result in loss of pressure and contamination of the hydraulic system.
Reduced Clamp Efficiency: The clamp may fail to hold the hose in place, which can cause the hose to slip or move, further exacerbating the leakage problem.
Consequences of System Integrity
Under-tightening can compromise the entire hydraulic system’s integrity by causing:
Pressure Drops: Leaks resulting from under-tightening can lead to pressure drops within the system, affecting its overall performance and efficiency.
System Contamination: Leaking fluids can introduce contaminants into the system, potentially damaging other components and leading to further failures.
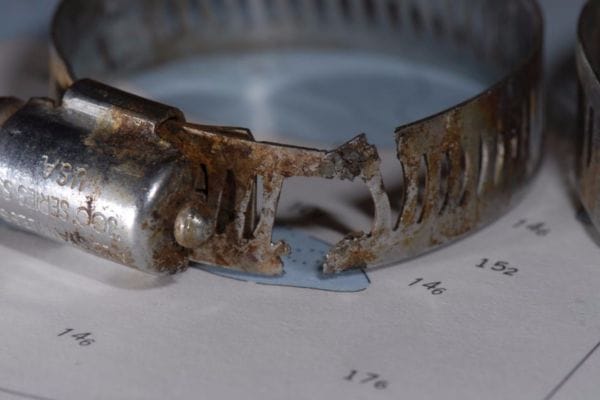
Corrosion and Material Degradation
Factors Leading to Corrosion
Corrosion occurs when the hose clamp material deteriorates due to exposure to moisture, chemicals, or extreme temperatures. Factors contributing to corrosion include:
Environmental Exposure: Clamps used in outdoor or industrial environments may be exposed to rain, chemicals, or high humidity, accelerating corrosion.
Material Composition: Clamps made from low-quality or non-corrosion-resistant materials, such as some types of steel or aluminum, are more prone to corrosion.
Impact on Performance and Longevity
Reduced Clamp Strength: Corrosion weakens the clamp material, reducing its ability to maintain a secure seal and increasing the risk of failure.
Hose Damage: Corroded clamps can become sharp or brittle, potentially causing damage to the hose and leading to leaks.
Increased Maintenance Costs: Regular replacement of corroded clamps and damaged hoses can increase maintenance costs and downtime.
Improper Installation
Common Mistakes During Installation
Improper installation of hose clamps can result from several common mistakes, including:
Incorrect Sizing: Using clamps that are too large or too small for the hose can prevent a secure fit and lead to leaks.
Misalignment: Failing to properly align the clamp with the hose and fitting can cause uneven pressure distribution and potential leaks.
Improper Torque: Not adhering to the manufacturer’s recommended torque settings for the clamp can result in over-tightening or under-tightening.
Effects on Clamp Efficiency and System Safety
Decreased Efficiency: Improper installation can lead to inefficient sealing, reducing the overall performance of the hydraulic system and increasing the likelihood of leaks.
Safety Risks: Leaks caused by improper clamp installation can create hazardous conditions, especially in systems carrying high-pressure fluids or volatile substances. This poses risks to both equipment and personnel.
System Failures: Consistent issues with clamp installation can lead to frequent system failures, increased maintenance needs, and potential damage to other components.
Solutions to Prevent Hose Clamp Failures
Correct Installation Techniques
Proper installation of hose clamps is crucial to ensuring a secure and leak-proof connection. Follow these step-by-step guidelines to avoid common installation issues:
Preparation:
Select the Correct Clamp: Ensure the clamp size matches the diameter of the hose and the fitting. Using a clamp that is too large or too small can lead to ineffective sealing.
Inspect Components: Check the hose and fitting for any signs of damage or debris that could affect the seal. Clean the surfaces thoroughly to remove any contaminants.
Positioning the Hose:
Align the Hose: Place the hose onto the fitting, ensuring it is fully seated. The hose should be pushed up to the base of the fitting to ensure maximum contact and seal integrity.
Applying the Clamp:
Position the Clamp: Slide the clamp over the hose and fitting, ensuring it is positioned evenly around the circumference. The clamp should cover the entire area where the hose meets the fitting.
Adjust the Clamp: If using a screw or worm gear clamp, align the screw or gear mechanism so it is easily accessible for tightening.
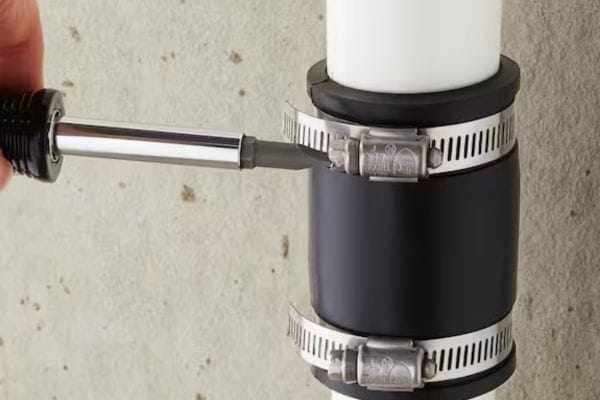
Tightening the Clamp:
Use the Right Tools: Employ appropriate tools such as a torque wrench or screwdriver to tighten the clamp. For screw clamps, a torque wrench can help achieve the correct torque specification.
Tighten Gradually: Tighten the clamp gradually to avoid over-tightening. For screw clamps, turn the screw until it feels snug but not excessively tight. For spring clamps, ensure the spring is properly compressed.
Final Inspection:
Verify Seal Integrity: Ensure there are no visible leaks or signs of deformation. Test the system under normal operating conditions to confirm the clamp is functioning correctly.
Material Selection and Maintenance
Choosing the right materials and maintaining them is essential to ensuring long-term performance and preventing clamp failures.
Choosing the Right Materials for Different Environments
Corrosion Resistance:
Stainless Steel: Opt for stainless steel clamps for environments exposed to moisture, chemicals, or high temperatures. Stainless steel is highly resistant to corrosion and wear.
Plastic or Nylon: For less demanding environments, plastic or nylon clamps may be appropriate. They are less expensive but offer limited durability compared to metal clamps.
Temperature Tolerance:
High-Temperature Materials: Select clamps rated for high temperatures if the system operates under extreme heat. Materials such as high-grade stainless steel or specialized alloys can withstand these conditions.
Chemical Compatibility:
Chemical-Resistant Coatings: Use clamps with chemical-resistant coatings if the system involves aggressive chemicals or fluids. Ensure the coating is compatible with the specific chemicals used.
Regular Inspection and Maintenance Practices
Scheduled Inspections:
Routine Checks: Conduct regular inspections of hose clamps as part of routine maintenance. Look for signs of wear, corrosion, or damage.
Operational Testing: Periodically test the system under normal operating conditions to ensure that clamps maintain a secure seal and performance.
Maintenance Practices:
Cleaning: Regularly clean clamps and surrounding areas to remove debris, grime, or corrosive materials. This helps prevent build-up that can affect clamp performance.
Replacement: Replace clamps that show signs of significant wear, corrosion, or damage. Timely replacement helps prevent system failures and maintains system integrity.
Preventing Corrosion
Protective Coatings and Treatments
Coatings:
Electroplating: Apply electroplated coatings to clamps to enhance their corrosion resistance. Zinc or chromium plating can provide additional protection.
Powder Coating: Use powder coatings for clamps exposed to harsh environments. This coating provides a durable barrier against moisture and chemicals.
Treatments:
Anodizing: For aluminum clamps, anodizing can create a protective layer that enhances resistance to corrosion and wear.
Passivation: Apply passivation treatments to stainless steel clamps to remove surface contaminants and enhance corrosion resistance.
Regular Cleaning and Monitoring
Cleaning:
Routine Cleaning: Clean clamps and hoses regularly to prevent the accumulation of corrosive substances. Use non-abrasive cleaning agents suitable for the materials involved.
Inspection During Cleaning: While cleaning, inspect clamps for any signs of wear, corrosion, or damage. Address any issues immediately to prevent further problems.
Monitoring:
Environmental Conditions: Monitor the environment where the clamps are used. High humidity, exposure to chemicals, or extreme temperatures can accelerate corrosion and other issues.
System Performance: Regularly check the performance of the hydraulic system to ensure that clamps are functioning correctly and maintain a secure seal.
Conclusion
Implementing the recommended installation techniques, selecting the right materials, and adopting preventive measures against corrosion will significantly improve the reliability of your hose clamps. Regularly reviewing and adjusting your maintenance procedures based on system performance and environmental factors will help address emerging issues before they escalate. Investing time and resources into proper hose clamp management is essential for maintaining the integrity and performance of hydraulic systems. Embrace these solutions and commit to ongoing monitoring to ensure long-term success and system reliability.
FAQ
What is a hose clamp and why is it important?
A hose clamp is a device used to secure hoses onto fittings or connectors, preventing fluid leaks and maintaining system integrity. It’s crucial for ensuring a tight, leak-proof connection and for maintaining the efficiency and safety of hydraulic systems.
What are the common causes of hose clamp failure?
Common causes include over-tightening, under-tightening, corrosion, material degradation, and improper installation. Each issue can lead to leaks, decreased performance, and potential system failures.
How can I prevent over-tightening of hose clamps?
To prevent over-tightening, use a torque wrench to apply the correct amount of pressure as specified by the manufacturer. Tighten gradually and ensure that the clamp does not deform the hose or fitting.
What materials should I choose for hose clamps in corrosive environments?
For corrosive environments, choose clamps made from stainless steel or those with protective coatings such as zinc or chromium plating. These materials are resistant to rust and corrosion.
How often should I inspect and maintain hose clamps?
Inspect hose clamps regularly, ideally as part of routine maintenance schedules. Check for signs of wear, corrosion, or damage, and replace clamps as needed to ensure continuous system reliability.
What are the best practices for installing hose clamps?
Best practices include using the correct size clamp, positioning it evenly around the hose, and tightening it to the manufacturer’s specifications.