The braid layer is a crucial component in the construction of hydraulic hoses. It is a woven reinforcement layer that encases the inner tube, adding strength, flexibility, and durability to the hose. The braid layer helps the hose withstand high-pressure conditions, resisting both internal pressure and external forces.
What is a Hydraulic Hose Braid Layer?
The Basics: Definition and Function of a Braid Layer
A hydraulic hose braid layer is a woven reinforcement structure that surrounds the inner tube of a hydraulic hose, providing additional strength, durability, and pressure resistance. It is typically made from materials like steel wire, synthetic fibers, or a combination of both. The braid serves as a vital support structure to prevent the hose from expanding, bursting, or collapsing under high-pressure conditions.
The primary function of the braid layer is to enhance the mechanical properties of the hose. By tightly wrapping around the inner core, it supports the hose under external stresses such as high fluid pressure, bending, and external abrasion. This reinforcement allows hydraulic hoses to perform effectively in demanding environments, providing a combination of strength and flexibility.
The braid layer also plays a key role in protecting the hose from damage caused by external factors, such as rough handling, friction, or exposure to chemicals. It is essential in ensuring that the hose can continue to safely and efficiently transmit hydraulic fluid over long periods, reducing the risk of failure.
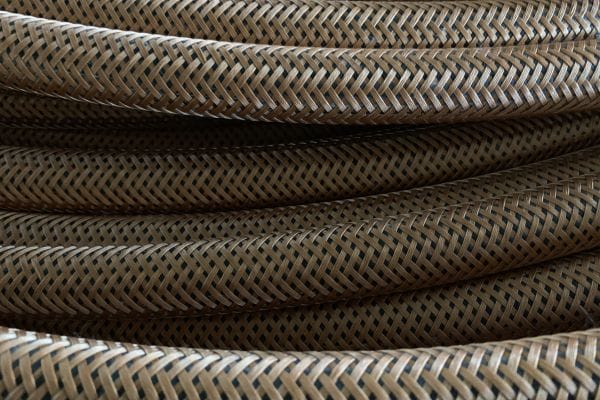
Key Components of a Hydraulic Hose: Layers and Reinforcement
A typical hydraulic hose is constructed with multiple layers, each designed to serve a specific purpose. These layers work together to provide the hose with the strength, flexibility, and durability necessary for high-performance hydraulic systems. Here’s a breakdown of the key components:
Inner Tube: The innermost layer that comes into direct contact with the hydraulic fluid. It is made from materials like rubber or thermoplastic that are resistant to the specific fluids it will carry. This layer ensures that the fluid flows smoothly without leakage or contamination.
Braid Layer (Reinforcement Layer): The next layer surrounding the inner tube, this is where the braid layer is located. It is typically made from steel wire or synthetic fibers like polyester, aramid, or nylon. The braid layer acts as reinforcement, providing the hose with high-pressure resistance, flexibility, and tensile strength.
Intermediate Layer: Some hoses feature an intermediate layer between the inner tube and the braid layer. This layer may be made from materials like fabric or rubber and serves as an additional barrier for fluid containment, especially in hoses carrying aggressive chemicals.
Outer Cover: The outermost layer of the hydraulic hose, which provides protection against external damage such as abrasion, UV exposure, and environmental conditions. The outer cover is typically made of tough rubber or thermoplastic materials.
Additional Reinforcements: Depending on the application, some hoses may have additional reinforcement layers, such as spiral wound layers or more complex braid structures. These reinforcements help handle even higher pressures or improve the hose’s resistance to twisting and kinking.
The Importance of Braid Layer in Hydraulic Hose Construction
How the Braid Layer Contributes to Hose Strength and Durability
The braid layer is a cornerstone in hydraulic hose construction because it provides the essential reinforcement needed to handle high-pressure applications. This reinforcement enhances the hose’s ability to withstand internal pressures without expanding or bursting, which is a critical factor in hydraulic systems where pressure can fluctuate significantly.
Here’s how the braid layer contributes to hose strength and durability:
Pressure Resistance: The primary function of the braid layer is to resist the internal pressure exerted by the hydraulic fluid. The braided fibers (whether steel or synthetic) act as a barrier, preventing the hose from distending under pressure. This allows the hose to maintain its structural integrity even under extreme conditions.
Enhanced Tensile Strength: The tight weave of the braid adds to the hose’s tensile strength, which means it can resist being pulled or stretched. This is particularly important in dynamic applications where the hose is subjected to tension or movement, such as in robotic arms, machinery, or vehicles.
Increased Flexibility: While the braid layer provides reinforcement, it doesn’t compromise the hose’s ability to bend. It maintains flexibility while still protecting against crushing or collapsing. This is especially crucial in tight spaces or applications where the hose needs to flex or twist without losing its shape.
Abrasion and Impact Resistance: The braid layer also acts as a shield against external wear and tear, such as abrasion from rubbing against surfaces or being dragged across rough terrains. The tough, woven material deflects these forces, ensuring the hose’s longevity in challenging environments.
Protection from Environmental Damage: Beyond pressure and mechanical forces, the braid layer helps protect the hose from external elements like UV rays, chemicals, and moisture. This is especially true in synthetic braided hoses, which are often engineered to provide additional protection against these factors.
Braid Layer vs. Other Hose Layers: What Sets it Apart?
While all layers of a hydraulic hose serve a specific purpose, the braid layer stands out because of its unique role in reinforcement and protection. Let’s compare the braid layer to other critical components of a hydraulic hose:
Inner Tube:
Function: The inner tube is the layer that comes into direct contact with the hydraulic fluid. It ensures the fluid can flow freely without leakage or contamination. It’s often made of rubber or thermoplastic materials that are resistant to the particular hydraulic fluid being used.
Difference: While the inner tube is responsible for fluid containment, the braid layer does not interact with the fluid itself but provides mechanical support to ensure that the fluid stays inside the hose, even under high-pressure conditions. Without the braid layer, the inner tube alone would not be able to handle the pressure in demanding applications.
Intermediate Layer (Optional):
Function: The intermediate layer is often made from fabric or rubber and may be added to improve the overall structural integrity of the hose. This layer can also serve as a barrier to prevent chemical interaction between the fluid and the braid layer.
Difference: Unlike the braid layer, which is primarily focused on reinforcing the hose under pressure and providing tensile strength, the intermediate layer is generally designed to provide extra protection for the inner tube or to separate the braid layer from the fluid. The braid layer’s specific focus is on preventing hose failure due to pressure and mechanical stress.
Outer Cover:
Function: The outer cover provides protection from external elements such as dirt, abrasives, UV light, and chemicals. It is typically made from materials like rubber or thermoplastic elastomers.
Difference: The outer cover’s role is protective, guarding the hose from environmental damage. However, it does not contribute directly to the hose’s internal pressure resistance. The braid layer, on the other hand, is focused on providing strength and durability under the forces exerted by the hydraulic fluid and mechanical stress.
Spiral Reinforcement (In Some Hoses):
Function: Spiral reinforcement is used in hoses that require an extremely high level of pressure resistance, often in applications involving hydraulic fluids under very high pressures. This is achieved by winding steel wire around the hose in a spiral configuration.
Difference: While spiral reinforcement offers excellent pressure resistance, it is generally more rigid than braided hoses, which tend to be more flexible. Spiral reinforcement is typically used in hoses where extreme pressure resistance is required, while the braid layer is commonly used in hoses that also require flexibility in addition to strength.
Different Types of Hydraulic Hose Braid Layers
Steel Braid: The Standard for High-Pressure Applications
Steel braid is one of the most commonly used materials for hydraulic hose reinforcement, especially in high-pressure applications. This braid layer is made from interwoven steel wires that provide exceptional strength and durability. It is commonly used in industries that require robust and reliable hydraulic hoses, such as construction, automotive, and aerospace.
Key Advantages of Steel Braid:
High Pressure Resistance: Steel braid provides superior strength to withstand high pressure, making it ideal for hydraulic systems with demanding fluid flow and pressure requirements.
Abrasion Resistance: Steel offers excellent protection against abrasion, which is crucial in environments where the hose is exposed to rough surfaces, sharp edges, or other wear factors.
Temperature Resistance: Steel braided hoses can handle extreme temperatures, both high and low, without losing their structural integrity.
Long-Term Durability: Steel is highly resistant to fatigue, making it an excellent choice for long-lasting performance in systems with frequent pressure cycling or high mechanical stresses.
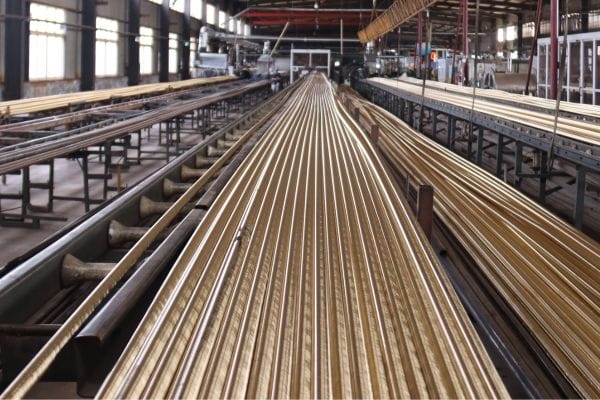
Synthetic Braid: Flexibility, Weight, and Resistance Benefits
Synthetic braid layers, made from materials such as polyester, aramid, or nylon, are becoming increasingly popular in hydraulic hoses due to their combination of flexibility, lighter weight, and high resistance to external elements. These materials are typically woven into a tight braid, providing reinforcement without the stiffness associated with steel.
Key Advantages of Synthetic Braid:
Flexibility and Lightweight: Synthetic braided hoses are generally more flexible than steel-braided hoses, making them easier to install and maneuver in tight spaces. They are also much lighter, reducing the overall weight of the hydraulic system.
Corrosion Resistance: Unlike steel, synthetic fibers are resistant to corrosion from chemicals and moisture. This makes them ideal for use in environments where the hose may be exposed to corrosive substances or humid conditions.
Chemical Resistance: Synthetic materials can be engineered to resist a wide variety of chemicals, making them suitable for use in fluid systems that handle aggressive or corrosive substances.
Abrasion Resistance: While not as strong as steel, synthetic braid still offers excellent resistance to abrasion, especially in moderate-pressure systems and environments with light external wear.
Key Factors to Consider When Choosing a Hydraulic Hose Braid Layer
Pressure Resistance
Pressure resistance is one of the most critical factors when selecting the right hydraulic hose braid layer. Hydraulic systems often operate under varying levels of pressure, and choosing a braid layer with the appropriate pressure rating ensures the hose can withstand the demands of the system without failure.
Burst Pressure vs. Working Pressure: When selecting a braid layer, it’s essential to consider both the burst pressure (the maximum pressure the hose can withstand before failure) and the working pressure (the maximum pressure the hose can handle during normal operation). A well-chosen braid layer should comfortably handle the working pressure with a sufficient safety margin, while also being rated for burst pressure to prevent catastrophic failure.
High-Pressure Systems: For systems that operate at extremely high pressures, such as industrial machinery, aerospace, or oil and gas applications, steel braided hoses are often the best option due to their superior pressure resistance. Synthetic braids can also handle moderate pressures but may not be suitable for extremely high-pressure environments.
Pressure Cycling: In systems where the pressure fluctuates or cycles rapidly, the braid layer must not only resist high pressure but also be durable enough to withstand repeated pressure changes. Steel braid excels in this regard due to its resistance to pressure fatigue.
Temperature Resistance
Temperature fluctuations are common in hydraulic systems, and the ability of the hose braid layer to maintain its performance in extreme conditions is crucial for ensuring the longevity and safety of the system.
High-Temperature Applications: Steel braided hoses generally offer better resistance to high temperatures than synthetic braids. Steel can handle temperatures up to 600°F (315°C) or more, making it ideal for systems where extreme heat is present, such as engine cooling, mining, or high-performance machinery.
Low-Temperature Applications: Some synthetic materials, such as polyester or nylon, are better equipped to handle low temperatures, remaining flexible and durable even in freezing environments. Steel braided hoses, in contrast, may become brittle at low temperatures, reducing their flexibility and performance.
Thermal Expansion and Contraction: When exposed to temperature extremes, both steel and synthetic braids may experience thermal expansion and contraction. Choosing a braid that can handle these changes without compromising its structural integrity is key to avoiding hose failure.
Chemical and Abrasion Resistance
Hydraulic hoses often come into contact with harsh chemicals, abrasive materials, and external environmental factors that can degrade their performance over time. A braid layer that offers chemical and abrasion resistance is essential for maintaining the hose’s integrity under such conditions.
Chemical Resistance: Different hydraulic systems carry various fluids, some of which can be highly corrosive. Synthetic braid materials, such as aramid or polyester, can be engineered to resist specific chemicals, making them a better choice for systems that involve aggressive or caustic fluids. Steel braid, while durable, is more susceptible to rust and corrosion when exposed to chemicals like acids, alkalis, or salts.
Abrasion Resistance: External wear and tear are common in environments where hoses are subject to physical damage, such as construction sites, factories, or mining operations. Steel braid is highly resistant to abrasion and provides excellent protection against rough surfaces and mechanical wear. Synthetic braids, though not as robust as steel, still offer decent protection for lighter applications and less abrasive environments.
Environmental Protection: Beyond chemicals and abrasion, the braid layer can also protect the hose from UV radiation, moisture, and temperature extremes. Certain synthetic materials are designed with additional UV and weather-resistant properties, making them ideal for outdoor applications exposed to sunlight, rain, and humidity.
Conclusion
Hydraulic hose failure, especially in high-pressure systems, can lead to catastrophic accidents, posing risks to both machinery and personnel. A properly reinforced hose minimizes these risks, providing the strength needed to handle extreme conditions without bursting or degrading over time.
FAQ
What is a hydraulic hose braid layer?
A hydraulic hose braid layer is a woven reinforcement that surrounds the inner tube of a hydraulic hose. It provides added strength, flexibility, and pressure resistance, helping the hose withstand high pressure and external stresses.
Why is the braid layer important in hydraulic hoses?
The braid layer enhances the hose’s ability to handle high pressure, extreme temperatures, and abrasion. It also ensures the hose maintains its structural integrity and flexibility, preventing failure under mechanical stress.
What is the difference between steel and synthetic braid layers?
Steel braid layers offer superior pressure resistance, abrasion resistance, and durability, making them ideal for high-pressure applications. Synthetic braids, on the other hand, are lighter, more flexible, and more resistant to corrosion, making them suitable for lighter-duty or chemical-resistant applications.
How do I know which braid layer to choose for my system?
Consider factors like pressure resistance, temperature range, and environmental conditions. For high-pressure systems, steel braid is generally recommended, while synthetic braid is ideal for lower-pressure or chemical-resistant applications.
Can a hydraulic hose with the wrong braid layer cause problems?
Yes, using the wrong braid layer can lead to hose failure, leaks, or system inefficiencies. It may not handle the pressure or environmental conditions properly, leading to reduced performance and potential safety risks.
How long do hoses with braided layers typically last?
The lifespan of a braided hose depends on the material, operating conditions, and maintenance. Steel braided hoses typically last longer under high-pressure conditions, while synthetic braided hoses may need replacement sooner in harsher or more abrasive environments. Regular inspection and maintenance can extend their lifespan.