Blow-out protection refers to safety mechanisms designed to prevent catastrophic failures in high-pressure hydraulic hoses. These failures, or “blow-outs,” can occur when a hose bursts or leaks under extreme pressure, potentially leading to hazardous situations, equipment damage, or production downtime. Blow-out protection is crucial for high-pressure hydraulic hoses because it ensures the integrity and reliability of hydraulic systems operating under intense conditions. Without adequate protection, a minor failure can escalate into a major incident, impacting both safety and operational efficiency.
Understanding High-Pressure Hydraulic Hoses
What are High-Pressure Hydraulic Hoses?
High-pressure hoses are specialized tubes designed to transport hydraulic fluids within a hydraulic system, which operates at elevated pressures. These hoses are built to withstand the high stresses and strains associated with hydraulic applications, ensuring that the fluid is delivered efficiently and safely from one component to another.
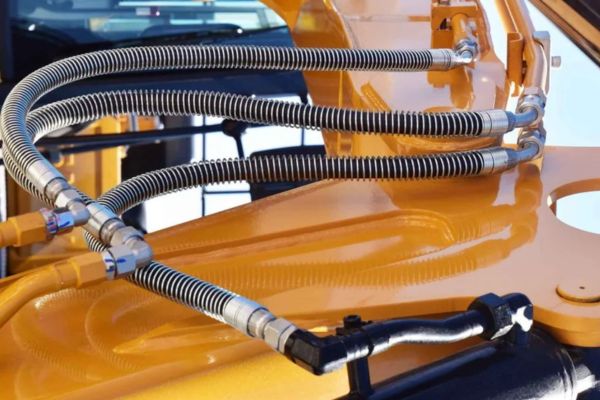
Basic Definition and Applications:
Definition: High-pressure hydraulic hoses are flexible conduits made from durable materials such as reinforced rubber or synthetic compounds. They are reinforced with layers of textile or steel wire to handle the internal pressure exerted by the hydraulic fluid.
Applications
Construction Equipment: Used in excavators, bulldozers, and cranes to power hydraulic cylinders and motors.
Agricultural Machinery: Found in tractors combine harvesters, and other farming equipment for efficient fluid transfer.
Industrial Machinery: Employed in manufacturing systems, presses, and other equipment that require fluid power.
Automotive and Aerospace: Used in hydraulic systems for braking, steering, and other critical functions.
Typical Operating Conditions
Pressure Ranges: High-pressure hydraulic hoses are designed to handle various pressure ranges depending on the application and the requirements of the hydraulic system. These hoses can withstand pressures ranging from a few hundred psi (pounds per square inch) to several thousand psi. For instance:
Low to Medium Pressure Hoses: Typically handle pressures up to 1,000 psi and are used in less demanding applications.
High Pressure Hoses: Designed for pressures from 1,000 psi to over 6,000 psi, suitable for heavy-duty equipment and systems.
Environments: The operating environment plays a crucial role in the selection and performance of high-pressure hydraulic hoses. These environments can include:
Temperature Extremes: Hoses must endure high temperatures from the hydraulic fluid and external conditions. Some hoses are engineered to withstand temperatures ranging from -40°F to over 250°F.
Chemical Exposure: In industries where chemicals or corrosive substances are present, hoses need to be resistant to chemical degradation.
Physical Abrasion: Hoses used in rugged environments, such as construction sites, must resist abrasion and physical damage.
Typical Use Cases
High-pressure hydraulic hoses are employed in various scenarios that require reliable fluid transfer under intense conditions:
Hydraulic Lifting and Loading: Essential in cranes and forklifts to lift and move heavy loads.
Fluid Power Systems: Used in hydraulic pumps, motors, and cylinders to transfer power and control machinery.
Emergency Response Equipment: Utilized in fire trucks and other emergency vehicles where high-pressure fluid is required for operations.
The Risk of Blow-Outs
Causes of Blow-Outs
Material Failure
Material failure is one of the primary causes of blow-outs in high-pressure hydraulic hoses. This can occur due to several factors:
Fatigue and Aging: Over time, hydraulic hoses can degrade due to exposure to heat, pressure, and chemicals. This degradation weakens the hose material, making it more susceptible to failure.
Manufacturing Defects: Flaws in the hose’s construction, such as improper reinforcement or defective materials, can lead to premature blow-outs.
Chemical Corrosion: Exposure to corrosive substances or incompatible fluids can erode the hose material, compromising its strength.
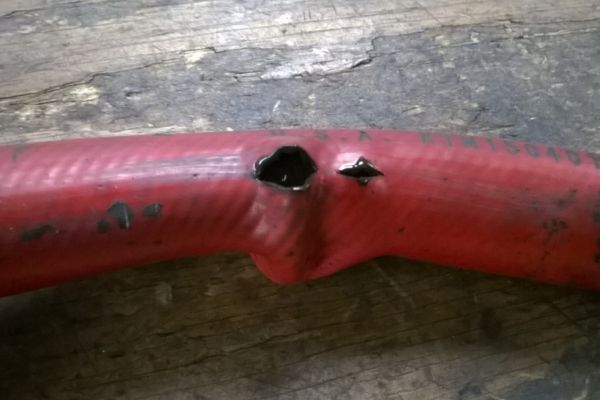
Pressure Surges:
Pressure surges, or “water hammer,” occur when there is a sudden increase in pressure within the hydraulic system. These surges can exceed the hose’s pressure rating and lead to:
Bursting: Sudden pressure spikes can cause the hose to burst if it cannot handle the increased load.
Weak Points: Surges can exploit existing weaknesses in the hose, leading to localized blow-outs.
Improper Installation
Incorrect Assembly: Using the wrong fittings or failing to secure the connections properly can lead to leaks and eventual blowouts.
Bending and Kinking: Hoses that are bent too sharply or kinked during installation can experience increased stress, leading to premature failure.
Over-tightening: Excessive tightening of hose fittings can damage the hose and cause leaks or blow-outs.
Signs of Potential Blow-Outs
Visual Indicators: Visual signs of potential blow-outs include:
Cracks and Bulges: Inspect hoses regularly for cracks, blisters, or bulges, which indicate that the hose is under stress or deteriorating.
Leaks: Any visible leakage from the hose or fittings is a red flag. Leaks often signal that the hose is failing and may soon burst.
Discoloration: Color changes, such as darkening or fading, can indicate chemical damage or exposure to extreme temperatures.
Performance Indicators
Reduced Fluid Flow: A noticeable decrease in fluid flow can indicate internal damage or blockages.
Unusual Noise: Hissing, whining, or banging noises often signal pressure issues or the presence of air in the system.
Inconsistent Pressure: Fluctuations in pressure readings can be a sign of hose wear or system imbalances.
Consequences of Blow-Outs
Safety Hazards
Injury to Personnel: The high-pressure fluid ejected during a blow-out can cause severe injuries to anyone nearby. This includes potential burns from hot fluid or physical injuries from flying debris.
Fire Risks: Hydraulic fluids are often flammable. A blow-out can lead to fluid spraying onto hot surfaces or ignition sources, resulting in fires or explosions.
Equipment Damage
Component Damage: The force of a blow-out can damage surrounding components, including hydraulic cylinders, pumps, and fittings. This can lead to costly repairs or replacements.
System Downtime: Equipment failure from a blow-out results in unexpected downtime. This disrupts operations and can lead to lost productivity and revenue.
Downtime Costs
Repair Costs: Repairing or replacing damaged hoses and components involves significant expenses. This includes both parts and labor.
Operational Disruption: Downtime affects productivity and can delay project timelines. In critical industries, such as construction or manufacturing, these delays can have far-reaching consequences.
Safety Investigations: After a blow-out, safety investigations, and compliance checks may be necessary, adding to the overall cost.
Blow-Out Protection Mechanisms
Types of Blow-Out Protection
Internal Reinforcements
Internal reinforcements are critical for enhancing the structural integrity of high-pressure hydraulic hoses. They provide the strength needed to withstand the intense forces exerted by hydraulic fluids. Various types of internal reinforcements include:
Steel Wire Braiding:
Description: This involves weaving steel wires around the hose’s inner core. The braiding provides excellent tensile strength and helps the hose resist pressure surges and external forces.
Effectiveness: Steel wire braided hoses are widely used in high-pressure applications due to their ability to handle pressures up to several thousand psi. They are effective in preventing blow-outs by distributing internal stresses evenly and reducing the risk of hose failure.
Spiral Wire Reinforcement:
Description: Spiral wire reinforcement consists of layers of high-tensile steel wires wound in a helical pattern around the hose. This design offers greater flexibility compared to braided reinforcements.
Effectiveness: Spiral-reinforced hoses are ideal for extremely high-pressure applications, capable of withstanding pressures beyond 6,000 psi. The spiral arrangement provides superior strength and flexibility, reducing the risk of blowouts even under fluctuating pressure conditions.
Textile Reinforcements:
Description: Textile reinforcements use fibers such as aramid or polyester woven into the hose structure. These reinforcements provide added strength and flexibility.
Effectiveness: While textile-reinforced hoses may not handle the highest pressures like steel wire reinforcements, they are effective for moderate pressure applications. They offer improved flexibility and resistance to abrasion, contributing to overall hose durability.
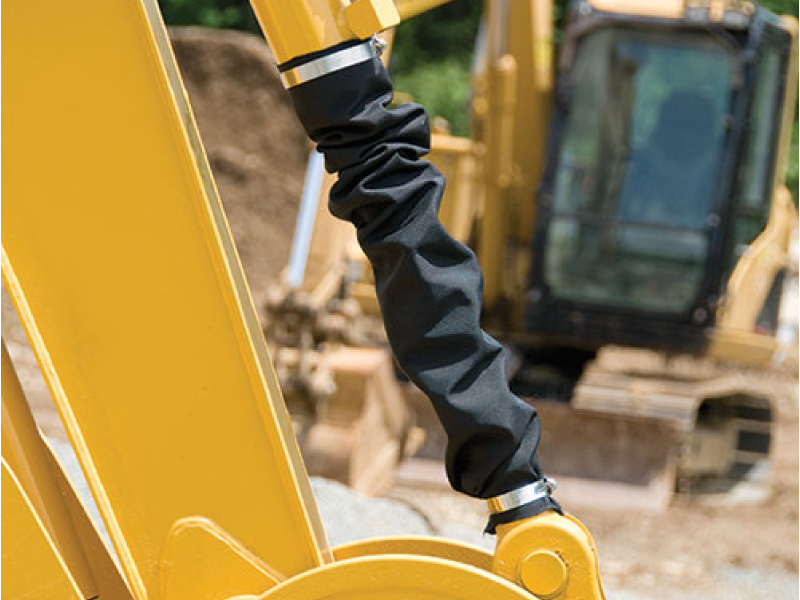
External Protective Layers
External protective layers safeguard hydraulic hoses from environmental damage and contribute to blow-out protection. These layers are designed to enhance the hose’s resistance to external factors:
Rubber Covers:
Description: Rubber covers provide a protective outer layer that shields the hose from abrasion, weathering, and chemical exposure.
Effectiveness: Rubber covers help prevent external damage that could lead to hose failure. They also provide some resistance to temperature fluctuations and chemicals, extending the hose’s service life and reducing blow-out risks.
Thermoplastic Covers:
Description: Thermoplastic covers are made from materials like polyurethane or nylon. They offer excellent abrasion resistance and chemical compatibility.
Effectiveness: These covers are particularly effective in harsh environments where chemical resistance and abrasion are critical. They enhance the hose’s overall durability and contribute to preventing blow-outs by protecting the underlying reinforcements.
Metal Guards:
Description: Metal guards or spiral wraps are used to protect hoses from physical damage and extreme abrasion. They encase the hose in a metal coil or mesh.
Effectiveness: Metal guards provide robust protection against external mechanical damage, including impacts and abrasions. They are often used in applications with high mechanical stress or where the hose is exposed to sharp objects.
Integrated Safety Features
Integrated safety features are built into hydraulic systems to provide additional protection and prevent blow-outs. These mechanisms help manage pressure and enhance safety:
Pressure Relief Valves:
Description: Pressure relief valves automatically release excess pressure when it exceeds a preset limit, preventing overpressure conditions that could lead to hose blowouts.
Effectiveness: By regulating pressure within the hydraulic system, these valves prevent excessive stress on the hoses, reducing the likelihood of failure and blowouts.
Burst Discs:
Description: Burst discs are designed to rupture at a specific pressure, providing a fail-safe mechanism to release pressure and protect the hose from catastrophic failure.
Effectiveness: Burst discs act as a safety valve, ensuring that pressure does not exceed safe levels. They provide a controlled method for pressure relief, minimizing the risk of sudden blowouts.
Pressure Sensors and Monitoring Systems:
Description: Pressure sensors and monitoring systems continuously track the pressure within the hydraulic system. They provide real-time data and alerts for abnormal pressure conditions.
Effectiveness: These systems allow for early detection of pressure anomalies, enabling preventive measures before a blowout occurs. They contribute to proactive maintenance and enhanced safety.
Standards and Regulations
Industry Standards for Blow-Out Protection
Several industry standards govern the design, testing, and performance of hydraulic hoses and blow-out protection mechanisms. These standards ensure that hoses meet safety and performance requirements:
SAE Standards (Society of Automotive Engineers):
Overview: SAE standards, such as SAE J517, specify the performance and testing requirements for hydraulic hoses. They cover aspects like pressure ratings, construction, and testing methods.
Relevance: SAE standards provide guidelines for ensuring that hydraulic hoses are designed to withstand high-pressure conditions and include necessary blow-out protection features.
ISO Standards (International Organization for Standardization):
Overview: ISO standards, such as ISO 18752, outline specifications for hydraulic hoses, including their construction, performance, and safety requirements.
Relevance: ISO standards ensure global consistency and safety in hydraulic hose manufacturing, including the integration of blow-out protection mechanisms.
EN Standards (European Norms):
Overview: EN standards, such as EN 853 and EN 856, define the performance and testing criteria for hydraulic hoses in Europe.
Relevance: EN standards ensure that hydraulic hoses used in European markets meet stringent safety and performance requirements, including effective blow-out protection.
API Standards (American Petroleum Institute):
Overview: API standards, such as API 7K, cover the specifications for hoses used in the oil and gas industry, including those for high-pressure applications.
Relevance: API standards provide guidelines for hoses operating in extreme conditions, ensuring that blow-out protection mechanisms are robust and effective.
Selecting the Right Blow-Out Protection for Your Hoses
Assessing Your Needs
1. Evaluate Pressure Requirements:
Maximum Operating Pressure: Determine the highest pressure your hydraulic system will operate under. This includes both normal operating pressure and potential pressure surges. Hoses and blow-out protection mechanisms should be rated for pressures higher than your maximum operating pressure to ensure safety and durability.
Pressure Fluctuations: Assess whether your system experiences frequent or significant pressure fluctuations. Systems with high variability may require more robust blow-out protection features to handle sudden pressure spikes effectively.
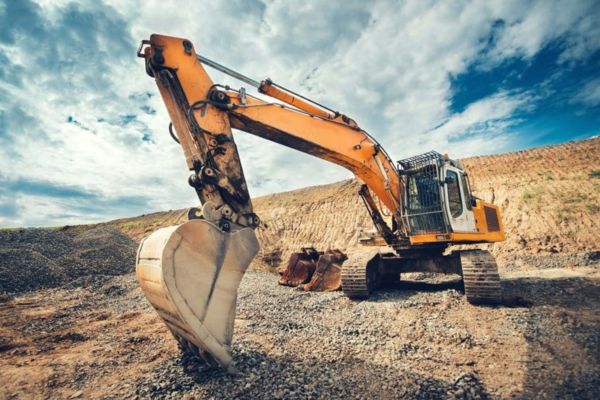
2. Analyze Application Environment:
Environmental Conditions: Consider the environmental factors to which the hoses will be exposed. This includes temperature extremes, chemical exposure, and abrasive conditions. For example, hoses used in harsh, outdoor environments may need additional external protection layers.
Mechanical Stress: Evaluate the level of mechanical stress on the hoses, such as abrasion, impact, or vibration. Environments with high mechanical stress may require hoses with enhanced external protective layers or metal guards to prevent damage and blow-outs.
3. Identify Fluid Types and Compatibility:
Fluid Properties: Identify the types of fluids that will be transported through the hoses. The chemical composition, temperature, and viscosity of the fluids can affect the choice of hose material and blow-out protection features. Ensure that the protection mechanisms are compatible with the fluids used to prevent degradation or failure.
Choosing Suitable Products
Criteria for Selecting Blow-Out Protection Features:
Reinforcement Type: Choose the appropriate internal reinforcement based on your pressure requirements. For high-pressure applications, steel wire braided or spiral-reinforced hoses offer superior strength. For moderate pressures, textile reinforcements may suffice.
External Protection: Select external protective layers based on environmental conditions. Rubber covers provide general protection, while thermoplastic covers offer enhanced resistance to chemicals and abrasion. Metal guards are ideal for environments with high mechanical stress.
Integrated Safety Features: Ensure that your hydraulic system includes essential safety features such as pressure relief valves or burst discs. These components help manage excess pressure and prevent blowouts. Consider the integration of pressure sensors and monitoring systems for real-time pressure management.
Conclusion
We encourage you to assess your current hydraulic systems and review the blow-out protection mechanisms in place. Upgrading to higher-quality protection can prevent costly downtime, enhance safety, and improve overall system reliability. Don’t wait for a blow-out incident to prompt action—invest in robust blow-out protection today to safeguard your equipment and operations.
FAQ
What is blow-out protection in hydraulic hoses?
Blow-out protection refers to safety mechanisms designed to prevent hydraulic hoses from failing or bursting under high pressure. It includes features like internal reinforcements, external protective layers, and integrated safety devices.
Why is blow-out protection important for high-pressure hydraulic hoses?
Blow-out protection is crucial because it helps prevent dangerous failures that can lead to safety hazards, equipment damage, and costly downtime. It ensures the hose can handle high pressures and reduces the risk of sudden burst incidents.
What are the common causes of blow-outs in hydraulic hoses?
Common causes include material failure, pressure surges, improper installation, and environmental factors such as abrasion or chemical exposure.
How can I tell if my hydraulic hoses are at risk of blow-out?
Signs of potential blow-outs include visible wear or damage on the hose, sudden changes in performance, and unusual pressure fluctuations.
What types of blow-out protection mechanisms are available?
Protection mechanisms include internal reinforcements like steel wire braiding or spiral wire, external protective layers such as rubber or metal guards, and integrated safety features like pressure relief valves and burst discs.
How do I choose the right blow-out protection for my hoses?
Evaluate your system’s pressure requirements, environmental conditions, and fluid compatibility.