The challenges of material selection are multifaceted—engineers must balance factors like temperature resistance, pressure endurance, and chemical compatibility, while also considering the environmental conditions the system will operate in. The wrong material choice can result in costly downtime, frequent repairs, or worse, a complete system breakdown. Thus, careful and informed material selection is not just a technical necessity, but a critical safeguard for both performance and safety.
The STAMP Method: Key Factors in Material Selection
A. Size
Compatibility
Proper size compatibility is critical in hydraulic systems to ensure that the fittings match the dimensions of the connecting hoses, tubes, or ports. When the sizes do not align, the system can suffer from various operational inefficiencies. Fittings that are too large or too small may result in improper sealing, leading to system leaks or fluid loss, which ultimately reduces the efficiency and safety of the system. Correct sizing ensures the system maintains adequate pressure, flow rates, and structural integrity throughout its operation.
Consequences of Incorrect Sizing
Improper sizing can have severe consequences, such as fluid leaks, stress fractures, and premature wear of hydraulic components. Leaks can lead to contamination of the hydraulic fluid, potential hazards in the working environment, and increased operational costs due to frequent maintenance. Stress fractures often occur when fittings are forced to work outside their specified size range, causing localized strain and eventual material failure. Premature wear due to incorrect sizing can shorten the lifespan of the hydraulic components, causing frequent breakdowns and the need for expensive repairs or replacements.
Material Considerations
Hydraulic fittings material choice plays a key role in how hydraulic fittings perform under different size requirements. For example, metals like stainless steel are more rigid and durable, making them well-suited for high-pressure systems with specific sizing tolerances. Conversely, more flexible materials like polymers or composites may accommodate slight sizing variations without the same level of stress but may have limitations regarding pressure or temperature handling. Additionally, some materials may be prone to deformation under stress, which could further affect sizing if not carefully selected based on the application.
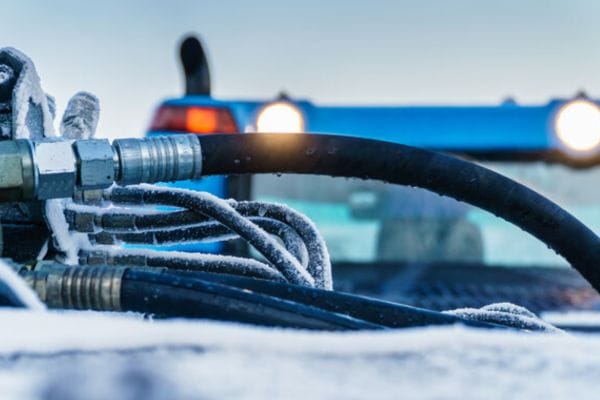
B. Temperature
Material Performance:
Temperature is a critical factor affecting the performance of materials in hydraulic fittings. Elevated temperatures can cause materials to expand, lose strength, or degrade over time, while lower temperatures may lead to contraction, brittleness, and reduced flexibility. For instance, metals like aluminum and stainless steel expand at different rates, which can affect the tightness of seals in hydraulic systems. Materials exposed to extreme temperature fluctuations must maintain their integrity to prevent system failures.
Extreme Environments:
In high-temperature environments, materials such as stainless steel and specialized high-temperature alloys are ideal because they resist thermal degradation and maintain strength at elevated temperatures. Conversely, in low-temperature conditions, materials like PTFE (Polytetrafluoroethylene) and certain grades of nylon are preferred due to their ability to remain flexible without cracking or breaking under thermal stress. These materials also exhibit low thermal conductivity, which helps in minimizing temperature-induced stresses in the system.
Material Comparison:
When selecting materials for temperature-sensitive environments, it’s essential to compare their thermal properties. Metals such as stainless steel and brass are highly resistant to temperature-induced wear and tear but may require additional insulation or protection in extreme environments. Alloys with high nickel content, like Inconel, can withstand both extreme heat and corrosion, making them suitable for specialized applications like aerospace. On the other hand, synthetics like PTFE and certain polymers offer better resistance to chemical degradation in extreme temperatures but may lack the mechanical strength of metals. Thus, the choice of material depends not only on the temperature range but also on the specific application requirements and performance expectations.
C. Application
Application Demands:
The application of hydraulic fittings plays a significant role in determining material selection. Different industries, such as aerospace, marine, and industrial manufacturing, place unique demands on hydraulic systems. For example, aerospace applications require materials that are lightweight but extremely strong and capable of withstanding high pressure and temperature fluctuations. Marine environments demand materials with high corrosion resistance due to constant exposure to moisture and salt water.
Specific Material Needs:
Each application has specific requirements that dictate the material choice. In aerospace, high-strength alloys like titanium and Inconel are often used for their ability to withstand both pressure and temperature extremes while maintaining a low weight. In marine applications, stainless steel and brass are popular choices for their excellent corrosion resistance and durability in harsh, wet environments. Industrial applications may require a balance of strength, flexibility, and cost-effectiveness, leading to the use of materials such as carbon steel or reinforced polymers in hydraulic fittings.
Selection Criteria:
When selecting materials for hydraulic fittings based on application demands, engineers must consider factors like mechanical strength, flexibility, resistance to corrosion and chemical exposure, and thermal stability. For example, a hydraulic system in an offshore drilling rig will need fittings that can resist not only the pressure of hydraulic fluid but also the corrosive effects of saltwater and chemicals. High-strength materials like duplex stainless steel or corrosion-resistant alloys are typically used in such demanding environments.
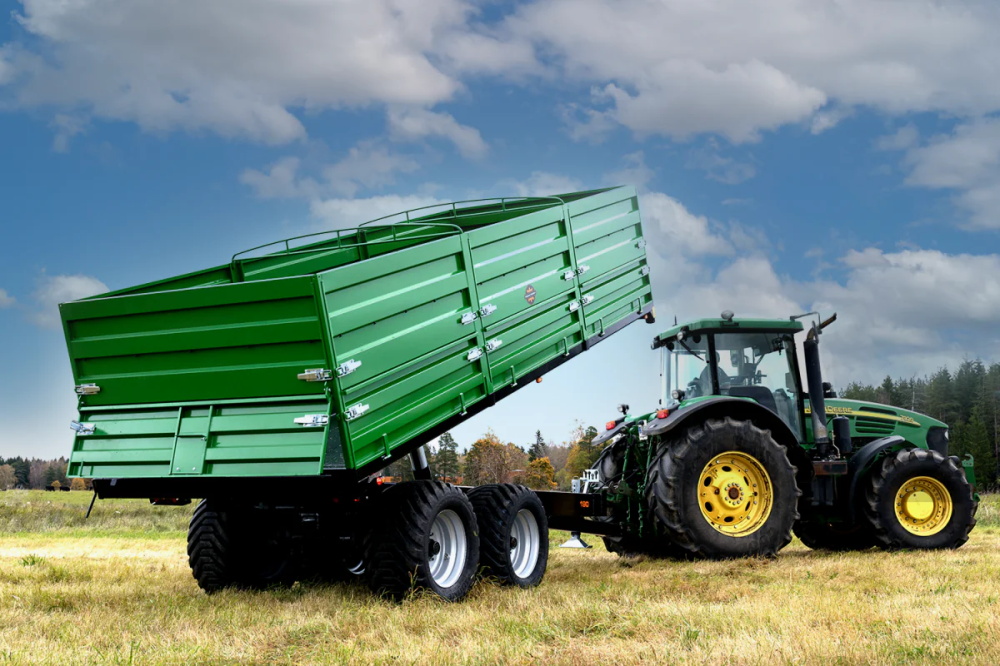
D. Media
Media Compatibility:
The media—or the fluid or gas—running through a hydraulic system must be compatible with the material of the fittings. Incompatibility can lead to chemical reactions that cause corrosion, swelling, embrittlement, or even catastrophic failure. Common hydraulic media include petroleum-based oils, water-glycol mixtures, and synthetic fluids, each of which interacts differently with various materials.
Chemical Reactions:
Certain materials, like carbon steel, are susceptible to rust and corrosion when exposed to water or certain chemicals. Stainless steel and PTFE, on the other hand, offer high resistance to most chemicals and are often chosen in systems where aggressive fluids are used. Understanding the potential reactions between the media and the material is crucial for preventing issues like pitting, corrosion, and material degradation, which can lead to leaks or fitting failure.
Material Selection:
For hydraulic systems that use petroleum-based fluids, carbon steel, and stainless steel are reliable choices due to their robustness and resistance to standard hydraulic oils. However, in systems where water or aggressive chemicals like acids are present, stainless steel or specialized plastics like PTFE are better suited because of their superior corrosion resistance. Choosing the right material is vital to ensure the longevity of the fittings and the safe operation of the hydraulic system.
E. Pressure
Material Integrity:
The pressure within a hydraulic system places immense stress on the materials used in the fittings. High-pressure systems, such as those found in industrial or aerospace applications, require materials with high tensile strength and excellent fatigue resistance. Low-pressure systems may have more flexibility in material choices but still require fittings that maintain integrity over time.
Failure Risks:
In high-pressure systems, the risk of material fatigue and burst strength failures increases. Materials that cannot withstand the continuous cycles of pressure may crack, deform, or burst, leading to potentially dangerous system failures. For example, carbon steel may be suitable for many high-pressure applications, but in extreme-pressure scenarios, stainless steel or reinforced alloys with higher tensile strength might be necessary.
Material Comparison:
Different materials are suited for different pressure ranges. For low to medium-pressure systems, carbon steel and brass are often used due to their good balance between strength, ductility, and cost. However, in high-pressure applications, stainless steel or high-performance alloys are preferred because of their superior resistance to pressure-induced fatigue and failure. These materials can endure the repeated stress cycles of high-pressure systems without compromising their structural integrity, ensuring safer and more reliable performance over time.
Material Categories for Hydraulic Fittings
A. Metals and Alloys
Common Metals Used in Hydraulic Fittings:
Metals and alloys are the most commonly used materials in hydraulic fittings due to their strength, durability, and reliability under high-pressure conditions. The most prevalent metals include steel, stainless steel, brass, and aluminum.
Steel:
Steel is one of the most widely used materials in hydraulic fittings, especially carbon steel. It provides excellent strength and is cost-effective, making it ideal for high-pressure industrial applications. However, carbon steel is prone to rust and corrosion when exposed to moisture, so protective coatings or treatments are often required.
Stainless Steel:
Stainless steel is highly resistant to corrosion, which makes it suitable for applications exposed to moisture, chemicals, or corrosive environments (such as marine and offshore industries). It maintains its strength under both high and low-temperature conditions. The downside is that stainless steel is more expensive than carbon steel, and its higher weight can be a drawback in applications where weight reduction is essential, such as aerospace.
Brass:
Brass is widely used in low to medium-pressure applications and is particularly valued for its resistance to corrosion and ease of machining. It is a softer metal, making it less ideal for high-pressure applications but well-suited for systems involving water, air, or non-corrosive fluids. Brass fittings are commonly found in plumbing, marine, and low-pressure hydraulic systems.
Aluminum:
Aluminum is a lightweight metal with good corrosion resistance and is often used in aerospace and automotive applications where weight savings are crucial. While it is not as strong as steel or stainless steel, its lower weight makes it ideal for applications that prioritize mobility and energy efficiency. The primary limitation of aluminum is its reduced strength under high-pressure environments, making it less suitable for heavy-duty hydraulic systems.
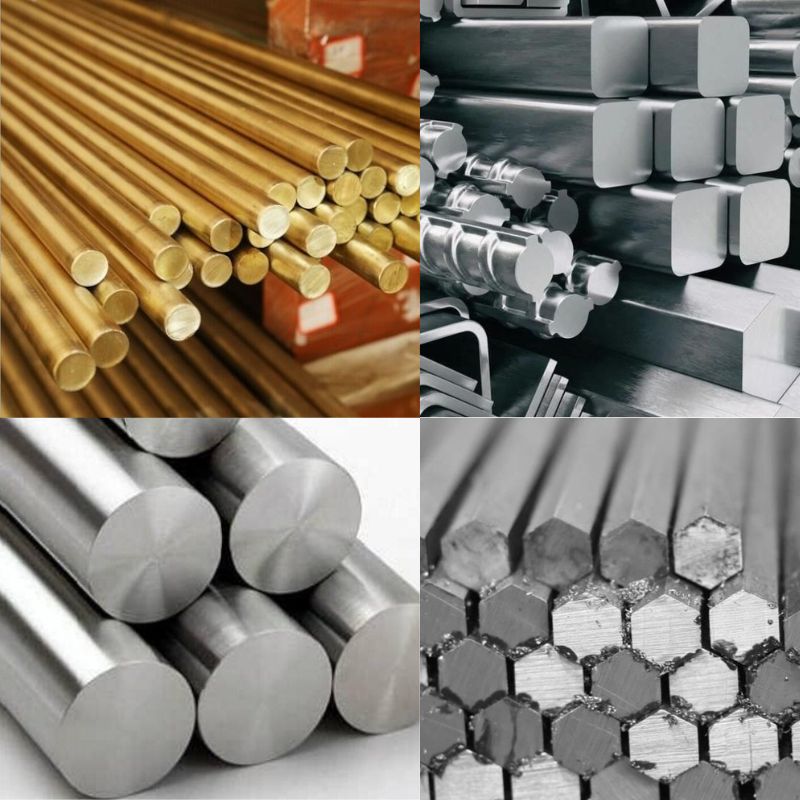
B. Polymers and Plastics
When to Use Plastics:
Polymers and plastics like PTFE (Polytetrafluoroethylene) and nylon are increasingly being used in hydraulic fittings, especially in applications where low-pressure conditions or exposure to chemically harsh environments are involved. These materials are suitable when the system operates under lower stress and temperature conditions, or when chemical resistance is paramount, such as in fluid handling or chemical processing industries.
PTFE (Teflon):
PTFE is highly resistant to a wide range of chemicals and extreme temperatures. Its non-reactive nature makes it an ideal choice for hydraulic systems handling aggressive media, such as acids or solvents. PTFE is commonly used in applications where corrosion resistance is more critical than mechanical strength.
Nylon:
Nylon is another plastic that is favored in hydraulic systems for its durability, flexibility, and resistance to wear. It is often used in pneumatic and hydraulic systems where moderate pressure and temperatures are involved. Nylon’s lightweight and chemical resistance makes it a good choice for fluid transfer and other similar applications.
Benefits of Plastics:
Flexibility: Plastics can provide a flexible solution for hydraulic systems, which can be crucial in preventing material fatigue and breakage over time.
Resistance to Chemicals: Plastics like PTFE have high resistance to chemicals and corrosion, making them ideal for systems dealing with harsh or corrosive media.
Cost-Effective: Plastics are generally less expensive to produce and machine compared to metals, reducing the overall system cost.
C. Composite Materials
Composites in Modern Systems:
Composite materials combine the benefits of both metals and plastics, offering a unique balance of strength, weight, and corrosion resistance. These materials are created by blending fibers (such as carbon or glass) with a resin matrix, resulting in components that can be tailored to meet specific performance requirements. Composites are particularly valuable in applications requiring high strength-to-weight ratios, corrosion resistance, and fatigue endurance.
Carbon Fiber Composites:
Carbon fiber composites are lightweight yet extremely strong, making them ideal for high-performance hydraulic systems, such as those found in aerospace, automotive, and sporting industries. These materials can withstand significant loads and stresses while maintaining a lower weight than metals. They also offer excellent fatigue resistance, which is critical for components that undergo repeated stress cycles.
Glass Fiber Composites:
Glass fiber composites are more affordable than carbon fiber but still offer considerable strength and corrosion resistance. These composites are often used in marine and chemical processing applications where exposure to corrosive environments is frequent. Glass fiber composites are less expensive than metals and carbon fiber, but they do not match the same strength or fatigue resistance.
Usage of Composite Materials:
Aerospace: In aerospace applications, composites are used to reduce weight while maintaining strength and rigidity, which is vital for fuel efficiency and overall performance.
Marine: Composite materials are widely used in marine hydraulic systems because of their excellent corrosion resistance and lightweight properties. For example, fiberglass-reinforced pipes and fittings are popular in offshore oil and gas applications.
Automotive: Composites are increasingly being used in automotive hydraulic systems, particularly in electric vehicles, where weight reduction contributes to improved battery life and vehicle performance.
Conclusion
By addressing these five critical factors, engineers can make informed decisions that enhance the overall reliability and performance of the hydraulic system.
FAQ
What are hydraulic fittings used for?
Hydraulic fittings are used to connect hoses, pipes, and tubes within a hydraulic system, ensuring a secure and leak-free flow of hydraulic fluid.
What is the importance of proper sizing in hydraulic fittings?
Proper sizing ensures compatibility between fittings and components, preventing leaks, pressure drops, and system failures.
What materials are commonly used for hydraulic fittings?
Common materials include steel, stainless steel, brass, aluminum, and sometimes polymers like PTFE, depending on the application and environment.
How do I choose the right hydraulic fitting for my system?
Use the STAMP method (Size, Temperature, Application, Media, and Pressure) to evaluate the fitting requirements based on your system’s specific needs.
What happens if I use the wrong fitting material?
Using the wrong material can lead to corrosion, leaks, material fatigue, and even complete system failure over time.
How often should hydraulic fittings be inspected?
Hydraulic fittings should be inspected regularly as part of routine maintenance to check for signs of wear, leaks, or damage.