Understanding the fundamentals of hose sizing is more than just technical knowledge; it’s a critical skill for protecting equipment, increasing productivity and ensuring the longevity of your hydraulic system. Whether you’re managing industrial machinery, aerospace applications or mobile equipment, choosing the right hose assembly size is key to maintaining optimal flow, pressure and operational integrity. In this guide, we’ll explore hose assembly sizing details to help you make an informed decision.
Why Hose Assembly Sizing Matters
In hydraulic systems, functionality, efficiency, and safety are critically dependent on selecting the correct hose size. Proper sizing is not just a recommendation—it is essential to ensure that systems operate reliably under various operating conditions.
The Importance of Inner Diameter (ID)
The Inner Diameter (ID) of a hose plays a crucial role in controlling fluid flow throughout the hydraulic system.
- If the ID is too small, the fluid velocity will increase dramatically. This excessive velocity leads to:
- Higher pressure buildup within the hose
- Increased risk of hose wear, internal erosion, and eventual rupture
- Potential damage to fittings and connected system components due to turbulence
- Conversely, if the ID is too large for the system requirements:
- The system must expend more energy to maintain adequate flow and pressure
- Overall efficiency decreases, leading to higher operational costs and reduced system responsiveness
Maintaining an optimal ID ensures a balance between fluid velocity and pressure, minimizing the chances of premature wear or catastrophic system failure.
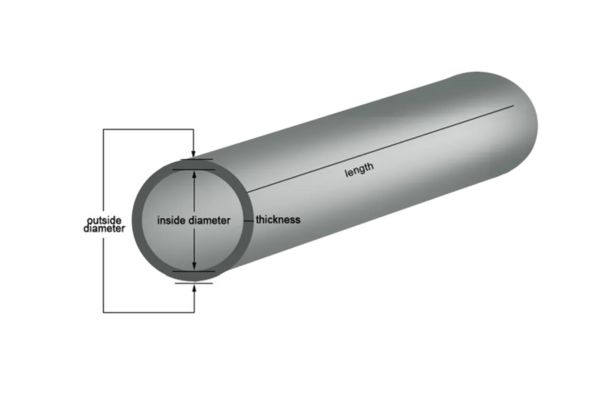
The Role of Outer Diameter (OD)
The Outer Diameter (OD) is equally critical because it directly impacts:
- The ability to fit hoses into tight spaces within machinery or equipment
- The compatibility with fittings and connectors that secure the hose in place
An incorrectly sized OD can lead to installation difficulties, improper sealing, or even mechanical interference with adjacent components, which could compromise the system’s integrity.
Risks of Incorrect Hose Sizing
Selecting the wrong hose size can trigger a chain of negative effects:
- System Overheating: High-velocity fluids can generate excessive heat due to friction, stressing system components.
- Leaks: Elevated pressure and mechanical strain can lead to leaks at connections or hose walls.
- Accelerated Wear: Hoses operating outside their design parameters suffer faster degradation, increasing maintenance needs.
- Safety Hazards: In high-pressure environments, hose failure could cause accidents, injuries, or significant downtime.
Each of these issues not only reduces efficiency but also raises operational costs and poses risks to personnel and equipment.
Importance of Following Industry Standards
To avoid these problems, adherence to industry standards is crucial. Organizations such as:
- SAE (Society of Automotive Engineers) with standards like SAE J517
- ISO (International Organization for Standardization)
These bodies provide comprehensive guidelines that cover:
- Recommended hose sizes based on pressure ratings
- Material selection according to fluid type and temperature
- Environmental considerations such as exposure to abrasion, chemicals, or extreme temperatures
By following these standards, engineers and technicians can select hoses that meet minimum performance and safety requirements, significantly reducing the probability of failures due to incorrect sizing.
Tools and Techniques for Accurate Measurement
Accurate measurement is the foundation of a reliable and efficient hydraulic system. Using the proper tools and following best practices ensures that hose assemblies are correctly sized, installed, and maintained, preventing future failures and unnecessary downtime.
Calipers and Micrometers
Calipers and micrometers are precision instruments essential for measuring:
- Inner Diameter (ID): The width of the hose opening, critical for determining proper fluid flow.
- Outer Diameter (OD): The external width of the hose, which impacts fitting compatibility and installation space.
- Thread Sizes: Accurate measurement of fittings’ threads is vital for ensuring correct mating and sealing.
Using Calipers:
- Internal jaws are used to measure the ID by expanding them inside the hose.
- External jaws are used for OD by fitting them around the outer surface of the hose.
- Always measure at multiple points to account for any manufacturing irregularities.
Using Micrometers:
- Ideal for very fine measurements, particularly for small components like threads.
- Provides high precision and helps differentiate between similar thread types such as NPT and BSP.
Bend Radius Gauges
Bend radius gauges are specialized tools used to verify that hoses are installed without exceeding their minimum bend radius.
Why It Matters:
- Exceeding the recommended bend radius can cause internal damage to the hose structure.
- Sharp bends lead to reduced flow efficiency, increased internal stresses, and a higher risk of hose rupture.
How to Use:
- Align the hose along the curve of the gauge to check if it meets the required radius.
- Adjust routing as necessary to maintain compliance with manufacturer specifications.
Measuring Tape and Rulers
Measuring tapes and rulers are commonly used for:
- Measuring hose length accurately, accounting for routing paths, bends, and any slack requirements.
- Verifying installation spaces to ensure that hoses will fit appropriately within system designs.
Tips for Effective Use:
- Lay hoses along their intended path before measuring.
- For short sections or precise fitting areas, use a rigid ruler for added accuracy.
- Factor in potential changes in length under system pressure conditions.
Common Measurement Mistakes and How to Avoid Them
Mistake | Description | Prevention |
Single-point measurement error | Measuring only at one location can miss inconsistencies in the hose material. | Always measure at multiple points around the hose. |
Ignoring pressure-induced stretch | Hoses can expand or contract under operating pressures. | Account for expected dimensional changes in system design. |
Misidentifying thread types | Different thread profiles can look very similar (e.g., NPT vs BSP). | Use a thread pitch gauge and calipers; reference fitting identification charts. |
Overlooking bend radius limitations | Tight bends weaken the hose and lead to failure. | Use a bend radius gauge and design with adequate space for curves. |
Key Measurements for Hose Assembly
Correct measurement of hose components is essential to ensure hydraulic systems operate safely and efficiently. Each dimension—Inner Diameter (ID), Outer Diameter (OD), hose length, bend radius, and overall assembly size—plays a vital role in system performance.
Inner Diameter (ID)
Definition: The inner diameter (ID) is the measurement of the internal width of the hose. It determines the amount of fluid that can pass through the hose at any given time.
Impact:
- A smaller ID increases fluid velocity, potentially leading to higher pressure drops, turbulence, and accelerated wear.
- A larger ID may reduce fluid velocity, lowering efficiency and responsiveness in the hydraulic system.
Measurement Method:
- Use calipers to measure the ID.
- Always take multiple measurements at different points to account for manufacturing variations or material inconsistencies.
- Ensuring an accurate ID is critical to maintaining system flow and pressure requirements.
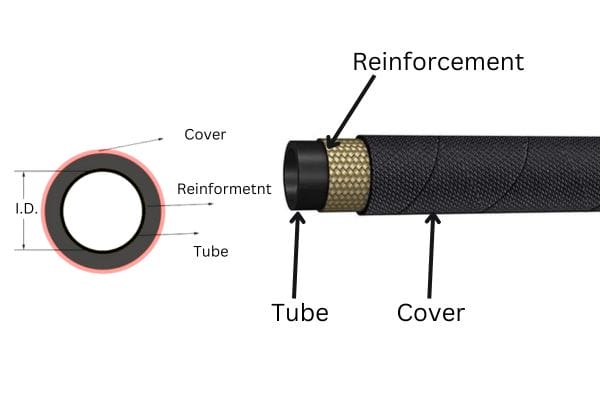
Outer Diameter (OD)
Importance: The outer diameter (OD) affects the selection and compatibility of fittings and the ability to route hoses through restricted spaces.
Typical Application Scenarios:
- Compact Systems: Automotive, aerospace, and robotics applications often demand precise OD sizing to fit hoses into tight compartments.
- Reinforced Hoses: Layers of reinforcement or protective covers add to the OD without affecting the ID.
Measurement Tool:
- Use a caliper or a micrometer to measure the external width of the hose, again sampling multiple points.
Hose Length
Importance of Accuracy:
- A hose that is too short creates tension on the connections and fittings, leading to potential failures.
- A hose that is too long may sag, creating loops that are prone to abrasion, wear, and damage.
Considerations:
- Hoses expand or contract slightly under pressure. High-pressure hoses can lengthen; low-pressure hoses might contract.
- Allowance must be made for this behavior during installation.
Measurement Method:
- Lay the hose along the actual installation path it will follow, including bends and curves.
- Use a measuring tape and account for any anticipated pressure-induced dimensional changes.
Bend Radius
Definition: The bend radius is the minimum radius a hose can be bent without kinking, collapsing, or damaging its internal structure.
Measurement Method:
- Measure the distance from the centerline of the hose to the center of the bend.
- Always refer to the manufacturer’s specifications or industry standards (such as SAE or ISO) for the minimum allowable bend radius based on the hose type and size.
Why It Matters:
- Bending hoses beyond their rated bend radius leads to internal damage, loss of flow efficiency, and significantly reduces hose lifespan.
Overall Hose Assembly Size
Definition: The overall hose assembly size combines:
- Inner Diameter (ID)
- Outer Diameter (OD)
- Length
These dimensions together determine if the hose fits properly within the system design constraints and performs reliably.
Importance:
- Overlooking any one of these measurements can result in misalignment, stress points, and reduced performance.
- Accurate sizing ensures that hoses withstand both operational and environmental stresses without compromising system integrity.
The Seven-Step Hose Selection Process (STAMPED Model)
Choosing the correct hose for your application requires a systematic and comprehensive approach. The STAMPED model offers a structured method to ensure all critical factors are considered during hose selection. Here’s what each letter stands for:
S – Size
Focus: Matching flow rate, flow velocity, and hose diameter.
Details:
- The hose must have an appropriate Inner Diameter (ID) to support the required fluid flow without excessive velocity, which can lead to friction loss, overheating, and pressure drops.
- Consider the Outer Diameter (OD) for fitting compatibility and space constraints during installation.
Key Tip: Use flow charts and nomographs to match flow rate and velocity to the correct hose size.
T – Temperature
Focus: Understanding both the fluid and environmental temperature ranges.
Details:
- Fluid Temperature: Hoses must tolerate the temperature of the media being conveyed (e.g., hot oils, steam, chilled water).
- Ambient Temperature: Consider external conditions, such as engine compartments or outdoor environments where hoses might be exposed to extreme heat or cold.
Key Tip: Always check the manufacturer’s rated temperature range for the hose material.
A – Application
Focus: Analyzing the specific use and operational environment.
Details:
- Determine if the hose will be used for suction, discharge, pressure, or return lines.
- Understand the hose’s required flexibility, movement, vibration resistance, or abrasion exposure.
Key Tip: Applications involving dynamic movement may require reinforced hoses with high flexibility and fatigue resistance.
M – Material
Focus: Identifying the fluid or gas that will pass through the hose.
Details:
- Ensure compatibility between the hose tube material and the conveyed substance (e.g., petroleum oils, chemicals, food products).
- Some fluids may require special inner tube linings to prevent degradation or contamination.
Key Tip: When handling aggressive chemicals or specialty fluids, refer to chemical resistance charts.
P – Pressure
Focus: Determining the working pressure and understanding pressure surges.
Details:
- Select a hose that can handle the system’s maximum operating pressure.
- Factor in pressure spikes and surges, which can greatly exceed normal operating conditions.
- Verify the hose’s burst pressure rating; standard practice recommends at least a 4:1 safety factor (burst pressure:working pressure).
Key Tip: Never exceed the recommended working pressure for a hose, even temporarily.
E – End Fittings
Focus: Selecting the correct type of fittings for both hose ends.
Details:
- Choose fittings based on thread type, connection standard (e.g., NPT, JIC, BSP), and required orientation (e.g., straight, 45°, 90°).
- Consider reusability or special coatings if needed (e.g., anti-corrosion).
Key Tip: Always confirm thread type and sealing method (e.g., O-ring face seal, tapered thread) to prevent leaks.
D – Delivery
Focus: Understanding logistics, special packaging, and time constraints.
Details:
- Specify required delivery timelines, packaging requirements (e.g., cleanroom packaging for food-grade hoses), and special labeling if necessary.
- Urgent or customized orders may require additional lead time.
Key Tip: Communicate clearly with suppliers regarding delivery expectations to avoid installation delays.
Conclusion
Remember, hydraulic systems operate under demanding conditions where precision matters. A properly sized and specified hose assembly not only ensures smooth operation but also protects your equipment investment and the safety of your team.
Take the time to measure carefully, consult industry standards, and choose the right hose for your specific application. If you need expert advice or customized hose assembly solutions, contact our team today—we’re here to help you build safer, more efficient systems from the inside out!
FAQ
What is the Inner Diameter (ID) of a hose, and why is it important?
The Inner Diameter (ID) is the measurement of the inside width of the hose. It’s important because it determines the flow rate and pressure of the fluid moving through the hose.
What role does the Outer Diameter (OD) play in hose assembly?
The Outer Diameter (OD) affects fitting compatibility and installation. It helps ensure that the hose fits securely with fittings and prevents leaks.
How do I measure the length of a hydraulic hose accurately?
To measure the hose length, stretch the hose along its path, including any bends, and use a measuring tape to get the exact length required for your system.
Why is bend radius important in hose sizing?
Bend radius refers to how tightly a hose can be bent without kinking. Following the correct bend radius prevents hose damage and prolongs its life.
What are the most common thread types used in hydraulic systems?
Common thread types include NPT, BSP, JIC, and ORFS. Each type has specific characteristics, and selecting the right one ensures compatibility and a leak-free connection.
How do I ensure compatibility between my hose and fittings?
Use precise measurements for ID, OD, and thread size, and follow the manufacturer’s guidelines to select fittings that match the hose dimensions and pressure requirements.