Hydraulic hose design plays a critical role in ensuring that your system operates at peak efficiency. A system with well-designed hoses reduces wear and tear, extends the lifespan of components, and improves overall performance. Proper design also minimizes fluid loss, prevents leaks, and ensures that the system can handle the necessary pressure and temperature ranges without failure.
Choose the Right Hose Material for the Application
One of the most critical factors in hydraulic hose design is selecting the right material for the hose. The material impacts everything from the hose’s flexibility to its durability under pressure and exposure to environmental factors. Understanding the characteristics of the most common hydraulic hose materials—rubber, thermoplastic, and PTFE (polytetrafluoroethylene)—is essential in making the right selection for your system’s specific needs.
Overview of Common Hydraulic Hose Materials
Rubber Hoses: Rubber is one of the most widely used materials in hydraulic hoses due to its flexibility, durability, and cost-effectiveness. Rubber hoses are generally reinforced with textile or steel braiding, giving them added strength and pressure resistance. These hoses are excellent for standard hydraulic applications and can withstand moderate temperature and pressure variations.
Thermoplastic Hoses: Thermoplastic hoses are lightweight and offer excellent flexibility, making them ideal for applications that require movement or when weight is a concern. They are also resistant to many chemicals and UV exposure, making them a good choice for outdoor environments. Thermoplastic hoses tend to have better abrasion resistance than rubber and can perform well in cold environments.
PTFE Hoses: PTFE hoses, made from a type of Teflon, are known for their superior chemical resistance and ability to handle extreme temperatures. These hoses are often used in environments with high chemical exposure or where heat resistance is critical, such as in chemical processing plants or high-temperature hydraulic applications. PTFE hoses are more expensive than rubber or thermoplastic hoses, but they offer excellent durability and performance in harsh environments.
Material Considerations for Different Environments
Each hydraulic application has its unique set of demands, and selecting the right hose material is key to ensuring long-term performance and reliability. Here are the primary factors to consider based on the operating environment:
Temperature: The operating temperature range is a major factor in material selection. Rubber hoses can generally handle temperatures between -40°C and 100°C, whereas thermoplastic hoses can operate at even lower temperatures, down to -54°C, and are suitable for high-temperature applications as well. PTFE hoses are the best choice for extreme heat, withstanding temperatures up to 260°C, making them ideal for high-temperature applications.
Chemical Resistance: If the hydraulic system is exposed to chemicals, oils, or solvents, it is crucial to choose a material that will not degrade when in contact with these substances. PTFE offers the best chemical resistance, followed by thermoplastic hoses, which can also handle exposure to a variety of chemicals. Rubber hoses are less resistant and may degrade over time when exposed to certain fluids, requiring more frequent replacement.
Abrasion and Wear Resistance: For applications where hoses are exposed to rough surfaces, frequent movement, or harsh external conditions, abrasion resistance is vital. Thermoplastic hoses are generally more abrasion-resistant than rubber hoses, but some rubber hoses come with protective coatings or external sleeves to enhance their durability. PTFE hoses, although resistant to chemicals and heat, may need additional protection in environments with high wear and tear.
Tips on Selecting Materials Based on the Operating Environment
For High-Temperature Applications: Opt for PTFE hoses if your system operates in extreme heat. Their high heat tolerance ensures reliable performance without the risk of material breakdown.
For Outdoor or Mobile Applications: Thermoplastic hoses are a great choice due to their UV resistance and flexibility, making them ideal for outdoor machinery or applications with frequent movement.
For Standard Hydraulic Systems: Rubber hoses remain the most economical option for standard applications with moderate pressure and temperature ranges. However, ensure that the rubber hose is adequately rated for your operating pressure and temperature.
For Chemical Exposure: Always select PTFE or specially formulated thermoplastic hoses that can resist the specific chemicals present in your system.
Performance Impact: Matching Material Properties with Operating Conditions
Selecting the right material based on your specific operating environment ensures that your hydraulic hoses will perform reliably over the long term. Using materials suited to temperature extremes, chemical exposure, or high abrasion not only extends hose life but also reduces the risk of system failure, downtime, and costly repairs. By matching the hose material properties with the conditions in which the system operates, you can significantly enhance the overall durability and efficiency of your hydraulic system.
Correct Hose Size Selection: Diameter Matters
Choosing the correct hydraulic hose size is crucial for maintaining system efficiency and preventing operational issues. Selecting the wrong hose size can lead to problems such as pressure drops, inadequate flow rates, and even system failure. Proper sizing ensures that the hydraulic system operates at optimal capacity, with adequate fluid flow and minimal pressure losses.
How to Measure the Size of Hydraulic Hoses
To ensure you’re selecting the right size hose, it’s important to accurately measure three key dimensions: internal diameter (ID), outer diameter (OD), and length.
Internal Diameter (ID): The internal diameter of a hose determines how much fluid can pass through it at a given time. Measuring the ID is critical because an undersized hose can restrict flow, leading to pressure drops, while an oversized hose can cause issues such as excessive fluid turbulence. The ID is typically measured in inches or millimeters and is the most important dimension for hydraulic hose selection.
Outer Diameter (OD): The outer diameter is important for fitting compatibility and installation in confined spaces. While the OD doesn’t affect fluid flow, it determines whether the hose can fit in areas with limited clearance. It’s also essential for selecting appropriate fittings and clamps.
Length: The length of the hose is another crucial measurement. It should allow for some flexibility in installation while avoiding sharp bends or kinks. Hoses that are too short may become overstressed and lead to failures, while hoses that are too long can cause sagging and additional wear.
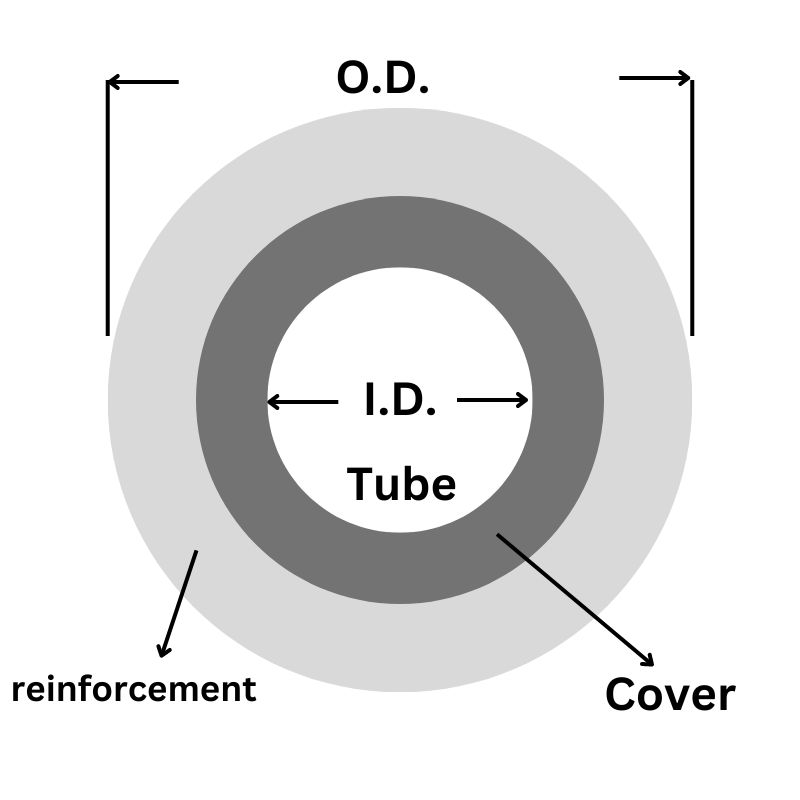
Impact of Incorrect Sizing on Flow Rate, Pressure Drop, and Overall System Performance
Incorrectly sizing a hydraulic hose can have significant negative consequences on system performance:
Flow Rate: The flow rate of hydraulic fluid is directly related to the internal diameter of the hose. If the hose ID is too small, it can restrict fluid flow, causing the system to work harder to push fluid through. This leads to inefficiencies, slower system responses, and higher energy consumption.
Pressure Drop: An undersized hose increases fluid velocity, which in turn raises friction within the hose, leading to a pressure drop. Even a slight pressure drop can affect the performance of actuators, motors, and other hydraulic components, potentially causing them to underperform or fail prematurely.
Heat Generation: When the hose is undersized, fluid velocity increases, leading to higher friction and heat generation. Excessive heat can degrade hydraulic fluid and hose materials, ultimately shortening the life of the hose and causing premature wear on other system components.
System Strain: Incorrect hose sizing can put unnecessary strain on the pump and other system components as they work harder to maintain pressure and flow. This can lead to equipment failure, increased maintenance costs, and reduced overall system efficiency.
Tools and Guidelines for Calculating the Correct Hose Size
To properly size hydraulic hoses, several tools and guidelines can help:
Flow Rate and Velocity Charts: Use hydraulic hose flow rate charts that correlate hose size with desired flow rates and pressure. These charts will guide you in choosing the correct ID based on the system’s required flow.
Hose Sizing Calculators: Many manufacturers provide online hose sizing calculators where you input operating conditions (such as flow rate, pressure, and fluid type) to receive recommendations for the correct hose diameter.
The “Dash Size” System: Hydraulic hoses are often referred to by their “dash size,” which corresponds to their ID in sixteenths of an inch. For example, a -04 hose has an ID of 1/4 inch. Understanding this system can help ensure that you select the correct hose for your application.
Use of Calipers: A vernier caliper can be used to precisely measure the ID and OD of an existing hose to ensure that replacements are of the same size.
Performance Impact: Ensuring Optimal Flow and Pressure Retention
By selecting the correct hose size, you ensure that the hydraulic system operates at its optimal flow and pressure levels. Properly sized hoses minimize pressure drops, maintain adequate flow rates, and prevent system strain. This leads to improved efficiency, reduced energy consumption, and a longer lifespan for both the hose and the system components. Accurate sizing ultimately enhances the overall performance and reliability of the hydraulic system, preventing costly downtimes and repairs.
Consider Hose Bend Radius and Flexibility
In hydraulic hose design, adhering to the recommended bend radius is crucial for maintaining hose performance and longevity. The bend radius refers to the minimum radius a hose can be bent without causing damage, and each hose type comes with specific recommendations based on its material and construction.
The Importance of Adhering to Minimum Bend Radius Recommendations
Each hydraulic hose is engineered to handle a certain degree of flexibility without compromising its integrity. The minimum bend radius is the smallest curve the hose can be bent around without causing structural damage. Bending the hose beyond this point creates undue stress on the inner layers of the hose, potentially causing cracks, leaks, or even bursts. Following manufacturer guidelines ensures that hoses remain functional under pressure and prevent avoidable breakdowns.
How Improper Bending Leads to Hose Wear, Failure, or Kinking
When a hose is bent tighter than its minimum bend radius, several issues can arise:
Kinking: When the hose is bent too sharply, it can kink, restricting fluid flow and reducing system efficiency. Over time, kinking can permanently damage the hose structure.
Internal Wear: Excessive bending stresses the inner tube and can lead to micro-cracks, which compromise the hose’s ability to contain hydraulic fluid under pressure.
External Abrasion: Bending a hose improperly can cause it to rub against equipment or other hoses, leading to external wear and damage over time.
Premature Failure: Hoses that are regularly bent beyond their limits will deteriorate quickly, leading to more frequent replacements and unexpected failures.
Best Practices for Routing Hoses to Avoid Stress Points and Optimize Space
Proper hose routing is essential to prevent over-bending and extend hose life:
Plan for Natural Hose Movement: When routing hoses, ensure that they follow natural curves rather than forcing tight bends. Use fittings to redirect hoses when necessary, rather than trying to bend the hose itself.
Avoid Stress Points: Keep hoses away from areas where they may be pinched, twisted, or exposed to mechanical stress. Use hose clamps and supports to secure hoses and prevent excessive movement.
Optimize Space: Make sure hoses are routed in a way that maximizes available space while avoiding interference with other components. Avoid sharp angles and route hoses in wide, smooth curves.
Select the Right Hose End Fittings
Choosing the correct hose end fittings is critical to ensuring a reliable hydraulic system. Fittings form the connection points between hoses and various components, such as valves, pumps, and cylinders.
Overview of Common Fittings: JIC, ORB, BSP, NPT, and Metric
JIC (Joint Industry Council): JIC fittings have a 37-degree flare seating surface and are commonly used in high-pressure hydraulic systems. They are valued for their leak-resistant connections, even in demanding environments.
ORB (O-Ring Boss): ORB fittings use an O-ring seal, which provides a reliable and leak-proof connection. They are ideal for applications where maintaining a secure, leak-free connection is essential.
BSP (British Standard Pipe): BSP fittings are commonly used in Europe and Australia. They come in two types: BSPP (parallel thread) and BSPT (tapered thread). These fittings rely on a threaded connection and may require sealing components like O-rings or washers for leak prevention.
NPT (National Pipe Thread): NPT fittings are widely used in North America and are distinguished by their tapered threads. The tapered design provides a tight seal, but thread sealants like PTFE tape are often required to prevent leaks.
Metric Fittings: These fittings are common in systems designed according to European standards. They typically have parallel threads and rely on an O-ring or a sealing washer to ensure a leak-proof connection.
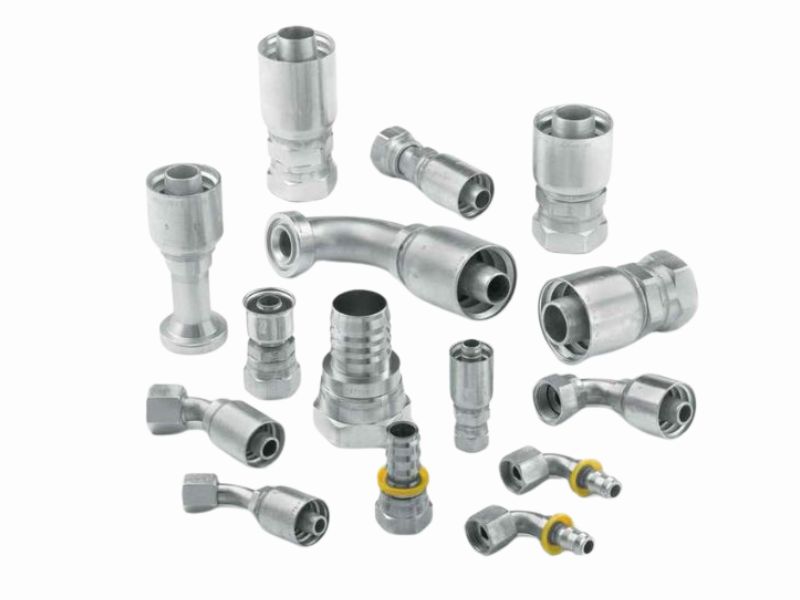
Ensuring Compatibility Between Hose and Fitting Types
For a secure, leak-proof connection, it is essential to match the fitting type with the hose type and the system’s specifications. Misaligned fittings or mixing different thread standards can result in poor sealing and system inefficiency. Always verify that the fitting and hose are compatible in terms of thread type, sealing mechanism, and pressure rating. Using adapters to connect mismatched fittings can introduce weak points in the system, increasing the likelihood of leaks.
The Impact of Using Improper Fittings on Leak Prevention
Using improper or incompatible fittings can have a significant impact on the performance of a hydraulic system:
Leaks: Mismatched or poorly sealed fittings can cause leaks, leading to loss of hydraulic fluid, pressure drops, and inefficiency.
System Downtime: Leaks require system shutdowns for repairs, which leads to downtime and increased maintenance costs.
Pressure Loss: Incorrect fittings can introduce restrictions in the system, causing pressure drops and reducing the effectiveness of the system’s components.
Safety Risks: Hydraulic fluid leaks pose a safety hazard, as high-pressure fluid can cause equipment malfunctions or injuries.
Understand Operating Pressure and Temperature Ratings
Hydraulic hoses operate under high pressure and temperature conditions, making it essential to select hoses with ratings that match the system’s requirements. Ensuring the hose can handle both the maximum pressure and temperature of the system is key to maintaining the safety, efficiency, and longevity of the hose.
Importance of Matching Hose Pressure Rating to System Pressure
Each hydraulic hose is designed with a specific pressure rating, indicating the maximum pressure it can safely withstand. It is crucial to match the hose’s pressure rating with the operating pressure of the system to avoid failure. Operating a hose beyond its pressure capacity can cause leaks, bursts, or hose deformation, resulting in equipment damage and downtime.
Working Pressure: This is the maximum continuous pressure the hose can handle without failure. Always ensure the hose’s working pressure exceeds or matches the system’s highest operating pressure.
Burst Pressure: This represents the pressure at which the hose will burst. While it’s important to know, your system should never approach this pressure level, and the working pressure is the critical figure to follow.
Operating with undersized pressure-rated hoses increases the risk of catastrophic failure, leading to system shutdowns and safety hazards.
How Operating Temperature Affects Hose Life and Performance
Temperature plays a significant role in hydraulic hose performance and durability. Operating a hose outside of its recommended temperature range can result in early degradation and failure. Both high and low temperatures impact the hose in different ways:
High Temperatures: Elevated temperatures cause hoses to soften and lose their structural integrity. Over time, the material weakens, leading to cracks, leaks, and eventual failure. Excess heat also accelerates the breakdown of hydraulic fluids, which can damage the hose from within.
Low Temperatures: In cold environments, hoses can become brittle and lose flexibility, increasing the risk of cracking, especially during movement. Special hoses rated for extreme cold conditions are necessary for these applications.
Tips for Selecting Hoses that Can Handle Extreme Pressures and Temperatures
To ensure your hoses can withstand the extreme pressures and temperatures in your hydraulic system, consider the following tips:
Use Manufacturer Guidelines: Always select hoses based on the manufacturer’s recommended pressure and temperature ratings for your specific application.
Factor in Safety Margins: Choose a hose with a pressure rating that exceeds your system’s operating pressure by at least 25%. This safety margin accounts for pressure spikes or surges that occur during operation.
Consider Temperature Range: Select hoses with a temperature rating that matches or exceeds the highest and lowest temperatures your system may encounter. If the system operates at extreme temperatures, such as in industrial or outdoor environments, opt for hoses designed to handle those specific conditions, like PTFE or thermoplastic hoses for high-heat or cold environments.
Incorporate Hose Protection Solutions
Hydraulic hoses are exposed to harsh environments, including high abrasion, extreme temperatures, and physical stress. Incorporating hose protection solutions can significantly extend the lifespan of your hoses, reduce downtime, and prevent costly damage.
Types of Hose Protection: Sleeves, Guards, Clamps, and Wraps
There are several effective hose protection solutions available, each designed to protect against specific hazards:
Hose Sleeves: Sleeves are typically made of nylon, fabric, or rubber materials. They protect against abrasion, heat, and UV exposure. Sleeves are flexible and wrap around the hose, providing a barrier between the hose and external elements that could cause wear or damage.
Hose Guards: Spiral hose guards are made from durable plastic or metal and are used to prevent abrasion and impact damage. They wrap around the hose and offer protection against rough surfaces or contact with sharp edges. Guards are ideal for protecting hoses in environments where they may rub against machinery or other surfaces.
Hose Clamps: Clamps are used to secure hoses in place and prevent excessive movement, which can cause stress or wear at connection points. They keep hoses from sagging or bending at sharp angles, thus reducing the risk of kinking and failure.
Hose Wraps: These protective wraps are made from spiral-wound plastic or fabric and are designed to wrap around hoses for extra abrasion resistance. Wraps are often used in mobile equipment where hoses are frequently exposed to movement and external wear.
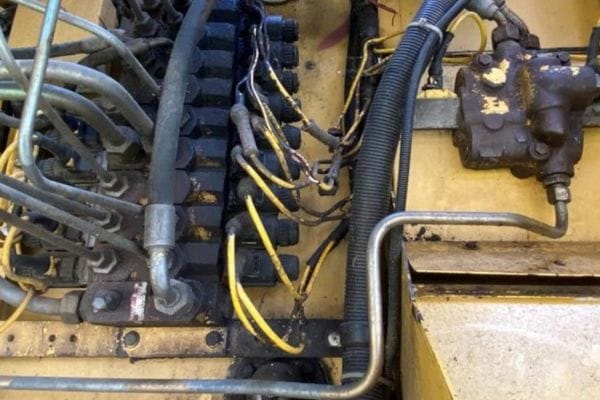
When and Where to Use Hose Protection
Certain environments require additional protection to ensure the longevity of your hoses:
High-Abrasion Areas: Hoses that come into contact with other machinery, or rough surfaces, or are dragged across the ground are susceptible to abrasion. In these situations, using sleeves or guards is essential to prevent wear and tear that could lead to leaks or hose failure.
Extreme Heat Zones: In applications where hoses are exposed to high temperatures, such as near engines or industrial furnaces, heat-resistant sleeves or insulation wraps are recommended. These protection solutions help prevent the hose material from degrading due to prolonged heat exposure.
Vibrations and Movements: Hoses that are subject to constant movement or vibration, such as in mobile equipment or industrial machinery, benefit from clamps and wraps to secure them in place and reduce strain.
Benefits of Protecting Hoses from External Wear and Environmental Damage
Protecting hydraulic hoses from external factors not only extends their life but also improves overall system reliability. Some key benefits of incorporating hose protection solutions include:
Reduced Maintenance Costs: By preventing abrasion, heat damage, and wear, hose protection solutions minimize the need for frequent replacements and repairs, resulting in cost savings.
Increased Hose Lifespan: Protective measures shield hoses from environmental damage, such as UV exposure, chemicals, and debris, which would otherwise cause premature wear and failure.
Improved Safety: Protected hoses are less likely to rupture or leak, reducing the risk of hazardous fluid spills and enhancing the safety of the system.
Consider Fluid Compatibility
Fluid compatibility is a crucial factor in hydraulic hose design, as different fluids interact with hose materials in various ways. Using the wrong hose material for the type of hydraulic fluid in your system can lead to chemical degradation, leaks, or hose failure. By selecting hoses specifically designed to handle the type of fluid in your system, you can ensure safe and efficient operation.
How Different Hydraulic Fluids Interact with Hose Materials
Hydraulic fluids come in several forms, including mineral oils, synthetic fluids, and bio-oil. Each of these fluids has different chemical properties that can affect the hose material:
Mineral Oils: Mineral-based hydraulic fluids are commonly used in many industrial applications. Rubber hoses, such as those made from nitrile (NBR), are generally compatible with mineral oils. However, over time, exposure to high temperatures or contaminants can degrade rubber hoses if they are not properly rated for the application.
Synthetic Fluids: Synthetic fluids often contain additives designed to improve performance, such as fire resistance or wear protection. These fluids can be more chemically aggressive than mineral oils, making it essential to use hoses made from materials that are specifically resistant to synthetic fluids, such as EPDM or fluoropolymer (PTFE).
Bio-Oils: Environmentally-friendly hydraulic fluids, such as bio-oils, are growing in popularity due to their biodegradable properties. While bio-oils offer an eco-friendly solution, they can be more aggressive on traditional rubber hose materials. Hoses made from bio-compatible materials, such as thermoplastic or certain types of PTFE, should be used to avoid degradation.
Tips for Selecting Hoses Based on Fluid Type
To ensure optimal performance and avoid chemical degradation, follow these tips when selecting hoses based on fluid type:
Consult Fluid Compatibility Charts: Most manufacturers provide fluid compatibility charts that outline which hose materials work best with specific hydraulic fluids. Use these charts as a guide when choosing hoses for your system.
Consider Hose Material’s Resistance: Select hose materials that are resistant to the chemical properties of your hydraulic fluid. For example, if using fire-resistant fluids, opt for hoses rated for high-temperature and flame resistance.
Account for Fluid Additives: Many hydraulic fluids contain additives that enhance their performance, such as anti-wear agents or fire retardants. Ensure the hose material can withstand these additives without compromising its integrity.
Avoiding Chemical Degradation Through Proper Hose Material Selection
Choosing the wrong hose material for your hydraulic fluid can lead to chemical degradation. Over time, incompatible hoses can crack, swell, or deteriorate, which not only reduces hose life but also increases the risk of leaks and system failure. Proper material selection helps avoid this issue:
Check for Swelling or Softening: Incompatible fluids can cause hoses to soften or swell, making them more susceptible to leaks and pressure failure.
Use Hoses with Enhanced Chemical Resistance: For aggressive fluids, such as synthetic or bio-oils, select hoses made from materials like PTFE, which provide superior chemical resistance.
Conclusion
Now is the time to evaluate your hydraulic hose designs and consider implementing these tips to enhance system reliability and performance. Whether you’re designing a new hydraulic system or improving an existing one, these best practices can help ensure that your hoses are well-suited for the task at hand. By investing in better hose design today, you’ll save on future costs and ensure that your hydraulic system operates smoothly and efficiently for years to come.
FAQ
What is the minimum bend radius for hydraulic hoses?
The minimum bend radius is the smallest curve a hose can be bent without causing damage. This varies by hose type and must be adhered to prevent kinking or premature wear.
How do I choose the right hydraulic hose material?
The choice of material depends on the operating environment. Rubber, thermoplastic, and PTFE are common materials, each suited for different temperature, chemical, and abrasion conditions.
What happens if I use a hose with the wrong pressure rating?
Using a hose with a lower pressure rating than the system requires can lead to leaks, bursts, or hose failure due to the system’s inability to handle pressure properly.
Why is fluid compatibility important for hydraulic hoses?
Different fluids interact with hose materials differently. Using incompatible materials can cause degradation, swelling, or leaks, reducing hose life and system performance.
What are hose protection solutions?
Hose protection solutions like sleeves, guards, clamps, and wraps protect hoses from external damage, such as abrasion, extreme heat, and environmental wear.
How can I prevent hydraulic hose leaks?
To prevent leaks, ensure that the correct hose end fittings are used, follow proper installation techniques, and regularly inspect the hoses for wear and damage.