Braid bands are essential components in hydraulic and industrial applications, designed to secure woven braided sleeves on corrugated metal hoses. They play a critical role in enhancing the strength and durability of hoses, preventing wear and tear caused by abrasion and environmental factors. The importance of braid bands extends beyond mere functionality; they contribute to the overall safety and efficiency of hydraulic systems. In applications where hoses are subjected to high pressures and dynamic movements, properly selected and installed braid bands can significantly reduce the risk of hose failure, thereby minimizing downtime and maintenance costs.
Understanding Hydraulic Braid Bands
A. What are Braid Bands?
Braid bands are specialized fastening components utilized primarily in hydraulic and industrial applications to secure woven braided sleeves onto corrugated metal hoses. These bands are typically constructed from robust materials such as stainless steel or carbon steel, providing the necessary strength to withstand various operational conditions. Their design allows them to tightly grip the braided material, ensuring that it remains in place during the hose’s operation.
The primary function of braid bands is to prevent the braided sleeve from slipping or unraveling, which could lead to significant failures in the hydraulic system. By maintaining the integrity of the sleeve, braid bands help ensure that the hose remains flexible and capable of withstanding high pressures without compromising safety. The effective deployment of braid bands can enhance the overall reliability of hydraulic systems, making them a crucial component in applications ranging from automotive to industrial machinery.
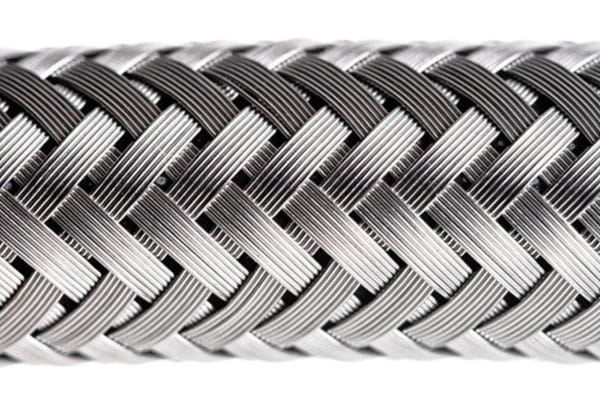
B. Importance in Hose Performance
The performance of hydraulic hoses is critically influenced by the use of braid bands. One of the key benefits they provide is enhanced strength and durability. By securing the braided sleeve firmly, braid bands minimize the risk of hose rupture, particularly under high-pressure conditions. This is particularly important in environments where hoses are subject to extreme pressures and fluctuating temperatures, as any failure can lead to hazardous situations and costly downtime.
In addition to bolstering strength, braid bands also play a vital role in protecting hoses against abrasion. Hydraulic hoses are often exposed to various environmental factors, including rough surfaces, chemicals, and sharp objects that can wear down the outer layer of the hose. Braid bands act as a protective barrier, shielding the braided sleeve from direct contact with these elements. This protective function is crucial in extending the lifespan of hoses and ensuring consistent performance over time.
Moreover, the combination of strength and abrasion resistance provided by braid bands allows for safer operation in demanding environments. For instance, in construction sites or manufacturing facilities where hoses are frequently moved and manipulated, the added security of braid bands helps prevent accidents caused by hose failures. By enhancing both the performance and safety of hydraulic systems, braid bands prove to be indispensable components in a wide range of applications.
Types of Braid Bands
A. Standard Braid Bands
Definition and Use Cases
Standard braid bands are the most common type used in various hydraulic applications. Typically made from materials such as stainless steel or carbon steel, they are designed to provide a reliable hold on braided sleeves. These bands come in various sizes to accommodate different hose diameters and configurations, making them versatile for numerous applications.
Examples of Applications
Standard braid bands are widely used in automotive systems, where they secure hoses in engines and cooling systems. They are also employed in industrial machinery, such as pumps and compressors, to ensure that hydraulic hoses remain intact during operation. Additionally, standard braid bands find application in agricultural equipment, securing hoses that transport hydraulic fluids essential for equipment functionality.
B. Heavy-Duty Braid Bands
Characteristics and Benefits
Heavy-duty braid bands are specifically engineered to withstand extreme pressures and harsh environmental conditions. They are typically thicker and made from higher-grade materials, such as heavy-gauge stainless steel, which enhances their durability. These bands are designed to provide a stronger grip and are often coated to resist corrosion, making them suitable for long-term use in demanding applications.
Situations Requiring Heavy-Duty Options
Heavy-duty braid bands are essential in applications where hoses are exposed to high-stress or abrasive conditions. For instance, in construction machinery, where hoses are frequently moved and subjected to impacts, heavy-duty bands help ensure that the hose remains secure and protected. Similarly, in marine applications, where hoses are exposed to saltwater and other corrosive elements, heavy-duty braid bands provide the necessary resilience to maintain functionality and safety.
C. Specialty Braid Bands
Custom Designs and Unique Features
Specialty braid bands are designed for specific applications that require unique features or configurations. These bands can be custom-made to meet particular size requirements or to include additional functionalities, such as integrated locking mechanisms or specialized coatings. Specialty braid bands are often crafted with precise tolerances to ensure a perfect fit for non-standard hoses.
Applications in Niche Industries
Specialty braid bands find their use in various niche industries, including aerospace, where precision and reliability are paramount. In these applications, custom-designed bands ensure that hoses meet strict safety standards while providing optimal performance. They are also used in food and pharmaceutical industries, where hygiene and material compatibility are crucial, necessitating specialized designs that comply with industry regulations.
D. Comparison of Different Types
To help visualize the differences between the various types of braid bands, the following summary table compares their features, benefits, and typical uses:
Specific industry needs, precision applications | Material | Typical Applications | Key Features | Ideal Use Cases |
Standard Braid Bands | Stainless/Carbon Steel | Automotive, Industrial Machinery | Versatile sizes, reliable hold | General-purpose applications |
Heavy-Duty Braid Bands | Heavy-Gauge Stainless Steel | Construction, Marine | Thicker, corrosion- resistant | High-stress environments extreme conditions |
Specialty Braid Bands | Custom Materials | Aerospace Food/Pharma | Custom designs, unique features | Specific Industry needs, precision applications |
Materials Used in Braid Bands
A. Stainless Steel
Benefits
Stainless steel is the most commonly used material for braid bands due to its excellent corrosion resistance and high strength. This type of steel contains chromium, which forms a passive layer that protects the metal from rust and deterioration, making it ideal for use in harsh environments. Additionally, stainless steel offers good tensile strength, allowing braid bands to withstand high pressures without failing.
Common Applications
Stainless steel braid bands are widely used in various applications, including automotive systems, chemical processing, and food and beverage industries. In automotive applications, they secure hoses in engines and cooling systems where exposure to heat and chemicals is prevalent. In chemical processing, stainless steel braid bands help secure hoses that transport corrosive fluids, while in the food and beverage sector, they ensure compliance with hygiene standards, as stainless steel is easy to clean and sanitize.
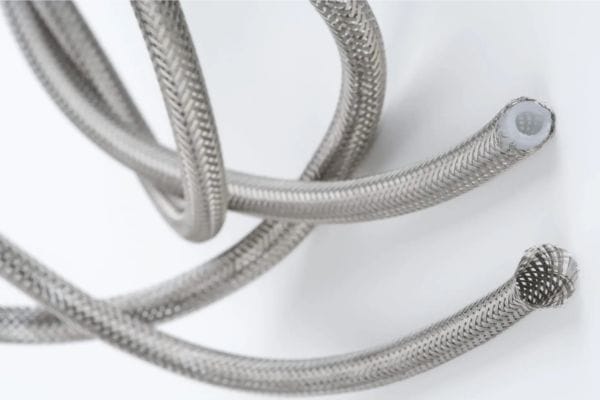
B. Carbon Steel
Characteristics and Uses
Carbon steel is another material used for braid bands, known for its high strength and cost-effectiveness. Unlike stainless steel, carbon steel does not have the same level of corrosion resistance, which limits its applications in environments where exposure to moisture or chemicals is a concern. However, its strength makes it suitable for applications where cost is a significant factor, and the risk of corrosion is minimal.
When to Choose Carbon Steel Over Stainless
Choosing carbon steel over stainless steel is often dictated by budget considerations and specific application requirements. If the application involves a controlled environment where exposure to corrosive substances is limited, carbon steel braid bands can be a viable option. For example, they are commonly used in structural applications or environments where hoses are not exposed to harsh elements. However, for applications requiring durability and corrosion resistance, stainless steel remains the preferred choice.
C. Other Materials (e.g., Plastic, Aluminum)
Overview of Alternative Materials
While stainless and carbon steel are the most prevalent materials for braid bands, other alternatives exist, such as plastic and aluminum. Plastic braid bands are often used in lightweight applications where corrosion resistance is essential, but the strength requirements are lower. These bands are typically made from high-density polyethylene (HDPE) or nylon, offering good flexibility and ease of installation.
Aluminum braid bands are another alternative, known for their lightweight properties and resistance to corrosion. They provide a good balance between strength and weight, making them suitable for applications where reducing overall weight is critical, such as in aerospace.
Advantages and Limitations of Each
Plastic Braid Bands:
Advantages: Lightweight, corrosion-resistant, flexible.
Limitations: Generally not suitable for high-pressure applications or extreme temperatures.
Aluminum Braid Bands:
Advantages: Lightweight, good corrosion resistance, decent strength.
Limitations: Less durable under extreme mechanical stress compared to steel options.
D. Environmental Considerations
Material Sustainability and Recycling
As environmental awareness grows, the sustainability of materials used in manufacturing braid bands becomes increasingly important. Stainless and carbon steels are recyclable, making them a more sustainable choice compared to non-recyclable plastic options. The recycling process for metals is well-established, allowing for the reuse of materials in new products, which helps reduce waste and energy consumption.
Furthermore, advancements in manufacturing processes aim to minimize the environmental impact of producing braid bands. Selecting materials with a lower carbon footprint and improving production efficiency are vital steps toward sustainable practices in the industry. Additionally, companies are increasingly exploring biodegradable alternatives for specific applications, though these materials are still in the developmental stage.
Sizing Tips for Braid Bands
A. Importance of Proper Sizing
Consequences of Incorrect Sizing
Proper sizing of braid bands is crucial for ensuring the safety and effectiveness of hydraulic systems. Incorrectly sized bands can lead to a variety of issues, including inadequate gripping, which may cause the braided sleeve to slip or unravel under pressure. This can result in hose failures, fluid leaks, and even hazardous situations, potentially causing injury to personnel or damage to equipment. Additionally, improperly sized bands can lead to excessive wear and tear, shortening the lifespan of hoses and necessitating more frequent replacements.
Overview of Sizing Standards
To facilitate proper sizing, industry standards exist that provide guidelines on the dimensions and tolerances for braid bands. These standards help ensure compatibility across different manufacturers and applications. Familiarizing oneself with these standards is essential for selecting the right braid band, as they provide baseline measurements for different hose types and sizes. Adhering to these standards can minimize risks and enhance the reliability of hydraulic systems.
B. Measuring Techniques
Tools and Methods for Accurate Measurement
Accurate measurement is key to selecting the appropriate size of braid bands. Several tools can assist in this process, including:
Calipers: Ideal for measuring the inner and outer diameters of hoses with precision.
Tape Measure: Useful for measuring longer hoses or when calipers cannot reach.
Hose Sizing Tools: Specialized tools designed for measuring hose diameters and fittings, often including markings for standard sizes.
Step-by-Step Guide to Measuring Hose Diameters
Prepare the Hose: Ensure the hose is clean and free of debris. If the hose is flexible, straighten it out as much as possible to avoid distortions in measurement.
Measure the Outer Diameter (OD): Use calipers to measure the widest part of the hose. This measurement is critical for ensuring the braid band fits securely around the hose.
Measure the Inner Diameter (ID): If applicable, measure the inner diameter as well, especially if the braid band needs to fit snugly against the inner sleeve.
Consider Hose Thickness: If the hose has a substantial wall thickness, consider this when measuring for braid bands, as it may affect the overall size needed.
Record Measurements: Document your measurements accurately, noting both OD and ID for reference when selecting a braid band.
C. Sizing Chart and Guidelines
Sample Sizing Chart with Specifications
A sizing chart can serve as a valuable reference when selecting braid bands. Below is a sample sizing chart illustrating typical braid band sizes and corresponding hose dimensions:
Hose Diameter (OD) | Braid Band Size | Material Type | Recommended Use |
1 inch | 1.25 inch | Stainless Steel | Standard applications |
1.5 inches | 1.75 inches | Heavy-Duty Stainless | High-pressure applications |
2 inches | 2.25 inches | Carbon Steel | Cost-effective structural applications |
3 inches | 3.5 inches | Plastic | Lightweight,non-high-pressure uses |
Recommendations for Different Hose Types
When selecting braid bands, consider the specific type of hose being used. For instance, high-pressure hoses typically require heavier gauge bands to withstand the increased stress. Conversely, lightweight hoses may be adequately secured with standard bands. Consulting the manufacturer’s recommendations for each hose type can further enhance the selection process.
D. Common Sizing Mistakes to Avoid
Highlight Common Pitfalls and How to Correct Them
Ignoring Hose Flexibility: Hoses may expand or contract under pressure, so it’s essential to account for this variability when measuring. Always select a braid band that allows for slight movement without compromising the grip.
Not Considering Wall Thickness: Overlooking the wall thickness of the hose can lead to selecting an incorrect size. Ensure measurements account for the hose’s full diameter, including its thickness.
Choosing Incompatible Materials: Different materials react differently under various conditions. For instance, using a plastic braid band in a high-pressure application can lead to failure. Always match the braid band material with the application’s requirements.
Skipping the Measurement Step: Some users may opt to guess the size based on previous experiences or visual estimates. This approach can lead to costly errors. Always measure to ensure accuracy.
Overtightening or Undertightening: When installing braid bands, it’s important to apply the correct tension. Over-tightening can damage the hose while under-tightening can lead to slippage. Follow manufacturer guidelines for the correct installation techniques.
Conclusion
Choosing the right braid bands is fundamental to the reliability and durability of hydraulic hoses. The implications of selecting the wrong type or size can lead to serious consequences, including system failures and increased maintenance costs. By being well-informed and referring back to this guide, users can make educated decisions that enhance the performance of their hydraulic systems.
FAQ
What are braid bands?
Braid bands are fasteners used to secure woven braided sleeves on hoses, enhancing their strength and preventing wear.
What materials are commonly used for braid bands?
Common materials include stainless steel for corrosion resistance, carbon steel for cost-effectiveness, and alternatives like plastic and aluminum for specific applications.
Why is proper sizing important for braid bands?
Proper sizing ensures a secure fit, preventing hose slippage or failure, which can lead to leaks and safety hazards.
How do I measure for the right size braid band?
Use calipers or a tape measure to determine the outer diameter of the hose and record this measurement to select the appropriate braid band size.
What are heavy-duty braid bands?
Heavy-duty braid bands are designed for high-stress applications, offering greater durability and strength compared to standard bands, making them suitable for extreme conditions.
Can braid bands be recycled?
Yes, materials like stainless steel and carbon steel are recyclable, making them a more sustainable choice compared to non-recyclable options.