In the world of hydraulic hoses, two prominent categories stand out: reinforced and standard hoses. Reinforced hoses feature additional layers that enhance their strength and durability, making them ideal for high-pressure environments. In contrast, standard hoses, typically lighter and more flexible, are well-suited for low-pressure applications and everyday tasks. Each type has its own set of advantages and disadvantages, influencing its suitability for specific uses.
Understanding Hoses
A. Definition of Hoses and Their Uses
Hoses are flexible tubes designed to transport fluids, gases, and sometimes solids from one point to another. They are essential components in various systems, enabling the efficient movement of substances under pressure or suction. Hoses come in various lengths, diameters, and material compositions, tailored to meet specific application requirements. Their primary uses include delivering water, oil, fuel, chemicals, and air in both industrial and domestic settings.

B. Different Types of Hoses in the Market
Material Types
Hoses are constructed from a variety of materials, each chosen based on the intended application and environmental conditions. Common materials include:
Rubber: Known for its flexibility and resistance to wear and tear, rubber hoses are often used for water and air applications.
PVC (Polyvinyl Chloride): Lightweight and cost-effective, PVC hoses are widely used in gardening and light industrial applications.
Nylon: Durable and resistant to abrasion, nylon hoses are suitable for high-pressure applications and chemical transport.
Silicone: Excellent for high-temperature applications, silicone hoses are commonly used in automotive and food processing industries.
Pressure Ratings
Hoses are rated according to the maximum pressure they can safely handle, which is crucial for ensuring safety and functionality. Common pressure ratings include:
Low Pressure: Typically rated under 150 PSI (pounds per square inch), suitable for water and air transport in domestic settings.
Medium Pressure: Ranging from 150 to 300 PSI, these hoses are often used in light industrial applications.
High Pressure: Rated above 300 PSI, high-pressure hoses are essential in heavy-duty industrial settings where durability and strength are paramount.
C. Common Applications for Hoses
Hoses serve various functions across different industries, each requiring specific features to meet operational demands.
Industrial Applications
In industrial settings, hoses play a vital role in processes such as fluid transfer, cooling, and air supply. Common uses include:
Hydraulic Systems: High-pressure hoses are essential for hydraulic machinery, transferring hydraulic fluid to operate various components.
Chemical Handling: Specialized hoses made from chemical-resistant materials are used to transport hazardous materials safely.
Air and Water Supply: Hoses are integral in supplying compressed air for tools and machinery, as well as in cooling systems that require water transport.
Agricultural Applications
In agriculture, hoses are fundamental for irrigation, chemical application, and livestock care. Key applications include:
Irrigation Systems: Flexible hoses deliver water to crops, ensuring efficient watering across large areas.
Pesticide and Fertilizer Application: Reinforced hoses are often used to spray chemicals, requiring durability to handle various substances.
Livestock Watering: Hoses supply clean water to livestock, contributing to their health and productivity.
Reinforced Hoses
A. Definition and Construction
Reinforced hoses are specially designed to withstand higher pressures and more demanding conditions compared to standard hoses. Their construction typically involves a core material, which can be made from various substances like PVC, rubber, or nylon, and additional reinforcement layers that provide strength and stability.
Materials Used
PVC (Polyvinyl Chloride): PVC is a common material for reinforced hoses due to its flexibility and chemical resistance. It can be combined with various additives to enhance durability and performance.
Rubber: Rubber hoses are known for their flexibility and resilience. They can withstand extreme temperatures and are often used in heavy-duty applications.
Nylon: Nylon is a lightweight yet strong material that is highly resistant to abrasion and punctures. It’s often used in applications where high strength-to-weight ratios are essential.
Reinforcement Layers
Reinforcement in hoses typically consists of one or more layers of textile or wire, which are embedded in the hose structure to improve its overall strength:
Textile Reinforcement: This is usually made from high-strength synthetic fibers such as polyester or nylon. These fibers enhance flexibility while providing excellent tensile strength and resistance to bursting.
Wire Reinforcement: Metal wires can be woven into the hose structure to provide superior strength, especially in high-pressure applications. This reinforcement is particularly crucial for hydraulic hoses, which must withstand intense internal pressures without failing.
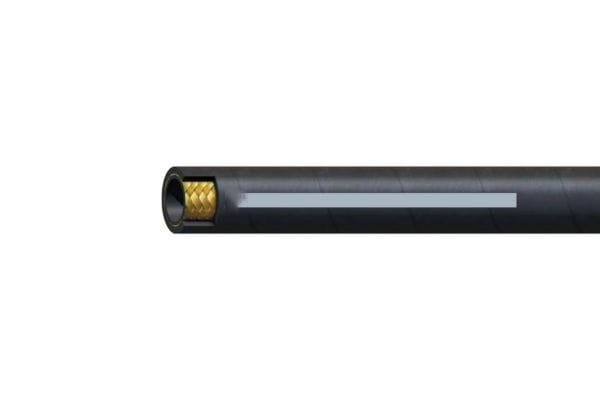
B. Advantages of Reinforced Hoses
Reinforced hoses offer several advantages that make them suitable for demanding applications:
Increased Durability and Longevity: The additional layers of reinforcement significantly extend the lifespan of the hose. They resist wear and tear better than standard hoses, making them ideal for frequent use in harsh environments.
Higher Pressure Tolerance: Reinforced hoses can handle higher pressure ratings, often exceeding 300 PSI. This makes them suitable for hydraulic systems and other applications where pressure fluctuations are common.
Resistance to Kinks and Abrasion: The structural integrity provided by the reinforcement helps prevent kinking, which can disrupt flow and damage the hose. Additionally, reinforced hoses are more resistant to abrasion, making them ideal for environments where contact with rough surfaces is a concern.
C. Disadvantages of Reinforced Hoses
While reinforced hoses have many benefits, they also come with certain drawbacks:
Higher Cost: The manufacturing process for reinforced hoses is more complex, which typically results in higher prices compared to standard hoses. This initial investment can be a consideration for budget-conscious consumers or businesses.
Heavier Weight: The additional materials used for reinforcement increase the overall weight of the hose. While this can enhance durability, it may also make handling and maneuvering the hose more cumbersome, especially in applications where flexibility and lightness are essential.
D. Best Use Cases for Reinforced Hoses
Reinforced hoses excel in specific applications where their unique properties provide significant advantages:
High-Pressure Applications: Industries that require the transportation of fluids under high pressure, such as hydraulic systems in manufacturing, construction, and automotive sectors, benefit greatly from reinforced hoses. These hoses ensure safe and efficient operation, minimizing the risk of failure under pressure.
Industrial Settings: In industrial environments, reinforced hoses are often used for chemical transfer, air supply, and fluid management. Their ability to withstand harsh conditions, resist chemicals, and endure frequent handling makes them indispensable in factories, workshops, and processing plants.
Agricultural Use: In agriculture, reinforced hoses are employed for irrigation systems and pesticide spraying. Their durability and resistance to kinking ensure consistent performance in the field, even under challenging conditions.
Automotive Applications: Reinforced hoses are also common in automotive settings, where they are used for fuel delivery, coolant transfer, and air intake systems. Their resistance to heat and pressure ensures reliable performance in demanding environments.
Standard Hoses
A. Definition and Construction
Standard hoses are flexible tubes designed for transporting fluids and gases in various applications, particularly where lower pressures and lighter materials are acceptable. These hoses are typically made from simpler materials compared to reinforced hoses, which allows for greater ease of use and versatility.
Materials Used
Rubber: Rubber is one of the most common materials for standard hoses. It provides flexibility and a good level of resistance to various environmental factors, such as temperature fluctuations and UV exposure. Rubber hoses are often used for water and air transport.
Vinyl: Vinyl, or PVC (Polyvinyl Chloride), is another widely used material for standard hoses. It is lightweight and resistant to chemical corrosion, making it suitable for light-duty applications, such as watering gardens and washing cars. Vinyl hoses are typically less expensive than rubber alternatives.
Polyurethane: This material is gaining popularity for standard hoses due to its excellent flexibility and abrasion resistance. Polyurethane hoses are often used in pneumatic applications and can be more durable than vinyl.
B. Advantages of Standard Hoses
Standard hoses come with several benefits that make them suitable for a wide range of applications:
Lightweight and Flexible: One of the most significant advantages of standard hoses is their lightweight nature. This makes them easy to handle, transport, and maneuver, especially in domestic and light industrial settings. Their flexibility allows them to be easily coiled and stored without taking up much space.
Lower Cost: Standard hoses are generally more affordable than reinforced hoses, making them an attractive option for budget-conscious consumers or businesses. Their lower manufacturing costs often translate to lower retail prices, enabling wider accessibility for various users.
Easier to Handle: Due to their lightweight and flexible design, standard hoses are user-friendly. They are easier to connect and disconnect, making them ideal for applications that require frequent repositioning or movement. This ease of use is particularly beneficial in home gardening and maintenance tasks.
C. Disadvantages of Standard Hoses
Despite their advantages, standard hoses also have limitations that users should be aware of:
Lower Pressure Tolerance: Standard hoses typically have a lower pressure rating compared to reinforced hoses. Most standard hoses are designed for low-pressure applications (under 150 PSI), which makes them unsuitable for high-pressure environments like hydraulic systems. Using them in inappropriate settings can lead to hose failure and potential hazards.
More Prone to Wear and Tear: Standard hoses are generally less durable than reinforced hoses. Their simpler construction and materials make them more susceptible to damage from abrasion, UV rays, and environmental factors. Over time, standard hoses may develop leaks or cracks, requiring more frequent replacements.
Limited Application Range: While standard hoses are versatile for light-duty tasks, they are not suitable for heavy-duty industrial or high-pressure applications. This limitation can restrict their use in specific environments where stronger, more durable hoses are necessary.
Comparison of Reinforced vs Standard Hose
A. Performance in Various Conditions
Pressure Handling
One of the most significant differences between reinforced and standard hoses is their ability to handle pressure. Reinforced hoses are designed to withstand high-pressure applications, often rated above 300 PSI. This makes them suitable for industrial settings where fluid dynamics can be extreme, such as hydraulic systems and heavy machinery. In contrast, standard hoses typically have a lower pressure tolerance, generally below 150 PSI, making them unsuitable for high-pressure environments. This limitation can lead to safety hazards if standard hoses are used inappropriately.
Flexibility and Maneuverability
Standard hoses excel in flexibility and maneuverability due to their lighter weight and simpler construction. They can easily bend around corners and fit into tight spaces, which is advantageous for domestic tasks like gardening and washing cars. While reinforced hoses are also flexible, their additional layers of reinforcement can make them stiffer and heavier, potentially limiting their maneuverability in certain situations. This trade-off means that for applications requiring frequent repositioning or tight angles, standard hoses may be the more practical choice.
B. Cost-Effectiveness Analysis
When analyzing cost-effectiveness, it’s essential to consider both the initial purchase price and long-term value. Standard hoses are generally less expensive upfront, making them an attractive option for those on a budget or for light-duty tasks where high performance is not critical. However, their shorter lifespan and susceptibility to wear and tear may lead to more frequent replacements, increasing long-term costs.
On the other hand, while reinforced hoses have a higher initial cost, their durability and ability to withstand harsher conditions often result in lower replacement frequency. For users in industrial or high-pressure applications, investing in reinforced hoses can lead to better long-term savings due to reduced downtime and maintenance costs. Ultimately, the choice between reinforced and standard hoses should consider not just the initial price, but also the expected lifespan and maintenance needs based on the intended application.
C. Lifespan and Maintenance Considerations
The lifespan of hoses can vary significantly between the two types. Reinforced hoses, due to their robust construction, typically have a longer lifespan. They can endure harsh conditions, including extreme temperatures, high pressure, and exposure to chemicals, making them ideal for demanding environments. Regular maintenance practices, such as inspecting for signs of wear and ensuring proper storage, can further extend their service life.
Standard hoses, while convenient for lighter tasks, are more prone to damage from abrasion and environmental factors. Their lifespan can be significantly shorter, especially if used outside their recommended pressure range. Users must be diligent about maintenance, checking for leaks, kinks, and other signs of wear. Proper storage—such as coiling hoses correctly and protecting them from UV exposure—can help maximize their lifespan.
Making the Right Choice
Choosing between reinforced and standard hoses requires careful consideration of several factors to ensure optimal performance and safety for your specific applications. Understanding these factors will help guide your decision-making process.
Application Requirements
The first step in selecting the right hose is to assess the specific requirements of your application. Consider the type of fluid or gas being transported, the pressure levels involved, and the hose’s intended use. For high-pressure applications, such as hydraulic systems or industrial machinery, reinforced hoses are essential due to their superior pressure tolerance. Conversely, for light-duty tasks, such as watering a garden or washing a car, standard hoses are often sufficient and more cost-effective.
Environmental Factors
Environmental conditions play a crucial role in hose performance. Factors such as temperature extremes, exposure to chemicals, and UV radiation can significantly impact the lifespan and effectiveness of the hose. For instance, if the hose will be used in environments with high temperatures or exposure to harsh chemicals, reinforced hoses made from resistant materials may be necessary. Standard hoses may degrade faster under such conditions, leading to potential failures.
Budget Constraints
Budget is another critical factor. While reinforced hoses generally have a higher upfront cost, their durability and longer lifespan can result in cost savings over time. In contrast, standard hoses are more affordable initially but may require more frequent replacements, increasing long-term costs. Evaluate your budget against the expected frequency of use and the operational demands of your tasks to determine the most economically viable option.
Conclusion
We encourage you to take the time to evaluate your specific needs and consider how different types of hose can meet your requirements. Whether you choose a reinforced hose for strength or a standard hose for convenience, making the right choice will ensure you have the best tool for the job.
FAQ
What is the main difference between reinforced and standard hoses?
Reinforced hoses are designed to handle higher pressures and are more durable due to additional layers of material, while standard hoses are lighter, more flexible, and suited for lower-pressure applications.
When should I choose a reinforced hose over a standard hose?
Choose a reinforced hose for high-pressure applications, industrial use, or environments that expose the hose to harsh conditions, such as extreme temperatures or chemicals.
Are standard hoses suitable for outdoor use?
Yes, standard hoses can be used outdoors, but their lifespan may be shorter if exposed to UV rays and extreme weather conditions. Regular maintenance can help extend their durability.
How do I determine the right hose length for my needs?
Consider the distance between your water source and the area of use. Measure the required length, adding a little extra to accommodate bends or connections.
Can I use a standard hose for high-pressure tasks?
It is not recommended. Standard hoses typically have lower pressure ratings and may fail or burst under high pressure, posing safety risks.
What maintenance do hoses require?
Regularly inspect hoses for wear and leaks, clean them after use, store them properly (coiled and out of sunlight), and replace any damaged sections promptly to ensure safety and performance.