Known for their fine pitch and precision, UNF threads offer increased tensile strength and are ideal for applications where vibration, pressure, or tight spaces require a secure and reliable connection. These threads are engineered to provide a strong hold while allowing for easy assembly and disassembly, making them a preferred choice in environments where precise adjustments are critical. UNF threads are designed to maximize performance, minimize the risks of loosening under stress, and ensure stability even in challenging conditions.
What are UNF Threads?
Definition and Background
Unified National Fine (UNF) threads are part of the Unified Thread Standard (UTS), which includes various thread forms commonly used across North America. The UNF designation specifically refers to threads with a fine pitch—meaning the distance between the thread crests is smaller compared to coarse threads like Unified National Coarse (UNC). The finer pitch of UNF threads allows for increased tensile strength and a more secure fit, making them particularly suited for precision applications where tight tolerances and secure connections are essential.
The origin of the Unified Thread Standard dates back to the early 20th century when the United States and Canada sought a unified system to standardize thread forms, ensuring interchangeability and consistency in manufacturing. This collaboration led to the creation of the Unified National Thread standard, which comprises UNF, UNC (Unified National Coarse), and other specialized variations like UNJF (Unified National Fine with a larger root radius). The standard aimed to harmonize thread types used in different industries, simplifying production and reducing compatibility issues.
Comparison to Other Thread Types (UNC, UNJF)
While UNF threads standard are characterized by their fine pitch, other thread types under the Unified Thread Standard have different purposes:
UNC (Unified National Coarse):
Thread Pitch: Coarser compared to UNF, resulting in fewer threads per inch.
Applications: Commonly used in general-purpose applications where strength and rapid assembly are required, such as in structural assemblies or less precise mechanical systems.
Key Differences: UNC threads are better for materials prone to thread stripping due to their larger root and more substantial structure. However, they lack the precision and tight fit offered by UNF threads, making them less suitable for high-pressure or vibration-prone environments.
UNJF (Unified National Fine with Increased Root Radius):
Thread Pitch: Similar to UNF, but with a larger root radius, which enhances fatigue resistance and reduces the risk of stress concentrations at the thread root.
Applications: Frequently used in critical aerospace and automotive applications where components experience high stress and require superior fatigue strength.
Key Differences: While both UNF and UNJF have fine pitches, UNJF’s larger root radius makes it more robust in high-stress environments. However, it also requires more precise manufacturing and assembly, leading to higher costs and more complex installation processes compared to standard UNF threads.
Overall, the primary distinction of UNF threads is their balance between pitch and strength, which allows for a secure fit suitable for a wide range of applications. While not as robust as UNJF threads, they provide enough precision for most hydraulic, automotive, and aerospace uses.
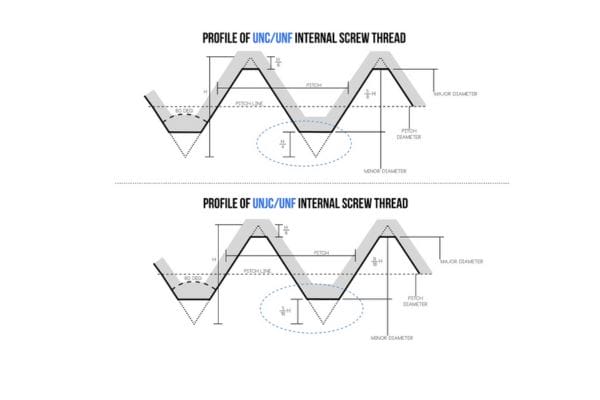
Common Applications of UNF Threads
UNF threads are widely adopted in various industries due to their fine pitch and secure fit, which ensures stability and precision. Some common applications include:
Precision Hydraulic Fittings: UNF threads are frequently used in hydraulic systems, where maintaining a leak-free and secure connection is critical. The fine pitch allows for a tight seal, essential for preventing fluid leaks under high pressure.
Automotive Assemblies: In the automotive industry, UNF threads are utilized in components like brake fittings, engine parts, and suspension systems. Their fine pitch helps create strong, reliable connections in areas subject to vibration and movement, ensuring that parts remain securely fastened even under dynamic conditions.
Aerospace Components: Given their high strength-to-size ratio, UNF threads are a preferred choice in the aerospace sector. They are used in high-stress components such as aircraft fasteners, engine parts, and hydraulic systems, where weight reduction and reliability are crucial.
Industrial Machinery: UNF threads are also common in industrial equipment and machinery where precise assembly is required, and components must withstand high pressures or frequent adjustments without compromising system integrity.
The Three Classes of UNF Threads: 1A, 2A, and 3A
Overview of Thread Classes
Thread classes are essential in defining the level of tolerance and fit for threaded components. They determine how loose or tight a thread engagement will be, which directly influences the performance, reliability, and durability of the assembled components. In the context of UNF threads, the thread classes are categorized as 1A, 2A, and 3A for external threads. Each class offers varying levels of fit, with 1A being the loosest and 3A being the tightest.
The proper selection of thread class is vital for achieving the desired performance, especially in systems where pressure, vibration, or thermal variations can affect the integrity of connections. Understanding the differences between the three classes of UNF threads allows engineers and technicians to make informed choices that balance ease of assembly, performance reliability, and cost-effectiveness.
UNF 1A Thread Class
Characteristics:
The UNF 1A thread class is designed with the loosest tolerance among the three UNF classes, offering the most flexibility during assembly. This loose tolerance allows for easy alignment and insertion, making it suitable for situations where components need to be rapidly assembled and disassembled. The loose fit also helps prevent cross-threading during the assembly process, reducing the risk of damage to the threads.
Applications:
UNF 1A threads are ideal for components that require frequent maintenance, adjustment, or replacement. Examples include machinery parts that need regular inspection, bolts used in temporary setups, and components in systems where quick assembly is prioritized. They are commonly found in low-pressure systems where precision is less critical, and convenience and speed are more important.
Advantages & Disadvantages:
Advantages: The primary benefit of the 1A class is its ease of assembly. The looser fit makes it less susceptible to cross-threading, and components can be assembled quickly, even in environments where precise alignment is challenging. This flexibility is advantageous for applications that prioritize maintenance accessibility.
Disadvantages: The downside of the 1A class is its lack of precision. Due to its loose tolerance, the connection is less secure and may not be suitable for high-pressure or high-vibration environments. Over time, the looser fit may also lead to issues such as loosening or thread wear, especially under stress.
UNF 2A Thread Class
Characteristics:
The UNF 2A thread class offers a medium tolerance level, making it the most commonly used and versatile thread class. It provides a balance between precision and ease of assembly, ensuring a secure fit while still allowing for relatively easy assembly and disassembly. This thread class is designed to fit general-purpose needs in a wide range of mechanical systems and is suitable for components that require moderate precision and reliability.
Applications:
UNF 2A threads are widely used in hydraulic and mechanical systems due to their versatility. They are suitable for components that need to maintain a secure fit under moderate pressure and vibration. Examples include hydraulic fittings, automotive fasteners, and general machinery components where a balance of reliability and ease of use is required. UNF 2A threads are often the standard choice for bolts, screws, and other fasteners in manufacturing and construction industries.
Advantages & Disadvantages:
Advantages: The 2A thread class strikes an ideal balance between assembly ease and connection reliability. Its medium tolerance provides a secure fit that can withstand moderate pressures and vibrations, making it suitable for various applications. The 2A class offers enough precision to ensure system integrity while still allowing for quick and efficient assembly.
Disadvantages: While the 2A class is versatile, it may not be precise enough for high-pressure or safety-critical applications that require the utmost accuracy. It may also require periodic checks and maintenance in environments where extreme conditions could lead to loosening or wear over time.
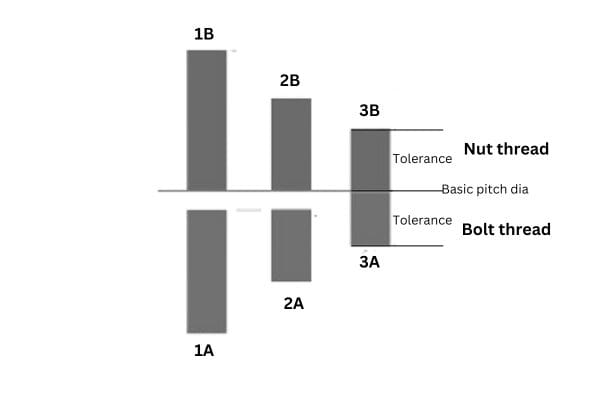
UNF 3A Thread Class
Characteristics:
The UNF 3A thread class is designed with the tightest tolerance of the three classes, offering the highest level of precision and fit. This tight tolerance ensures a very secure connection, making it ideal for applications where even the slightest movement or loosening could lead to system failure. The 3A thread class requires careful alignment during assembly due to its tighter fit, which demands greater precision.
Applications:
UNF 3A threads are typically used in critical systems where a highly secure and stable connection is essential. They are often found in high-pressure hydraulic systems, aerospace components, and safety-critical parts where failure is not an option. In such environments, the secure fit provided by the 3A thread class minimizes the risk of leaks, loosening, or failures under stress. These threads are also used in applications that experience extreme vibrations or thermal variations, where maintaining system integrity is paramount.
Advantages & Disadvantages:
Advantages: The primary advantage of the 3A thread class is its precision and reliability. The tight fit ensures a secure, leak-free connection, making it ideal for high-stakes and high-performance environments. The 3A class is particularly beneficial when long-term stability and safety are critical, as it minimizes the risk of thread failure under stress or vibration.
Disadvantages: The 3A thread class’s high precision comes at the cost of ease of assembly. Due to its tight tolerance, it requires careful alignment during installation, making the assembly process more challenging and time-consuming. This also increases the likelihood of cross-threading if not assembled with precision, potentially leading to component damage. Additionally, components with 3A threads may have higher manufacturing and maintenance costs, as they require stricter quality control and periodic checks to maintain their tight fit.
Tolerance Levels and Fit in UNF Threads
Understanding Tolerance and Fit
Tolerance refers to the allowable variation in the dimensions of a thread, specifically the degree of tightness or looseness in the connection between mating components. In thread manufacturing, tolerance levels determine how closely the threads on bolts, screws, and other fasteners align with their corresponding nuts or fittings. A higher tolerance level (looser fit) allows for easier assembly and flexibility, while a lower tolerance level (tighter fit) requires more precision but provides a more secure and stable connection.
The fit between threaded components affects the overall performance, alignment, and stability of mechanical systems. For example, loose-fitting threads may be beneficial for quick assembly or when frequent disassembly is needed, but they may not hold up under high pressure or vibration. Conversely, tight-fitting threads offer superior strength and stability but may require careful alignment during assembly to prevent damage and ensure a proper fit. The appropriate tolerance level must be chosen based on the application requirements, including load conditions, environmental factors, and the frequency of assembly or maintenance.
Comparative Analysis: 1A vs. 2A vs. 3A
Each UNF thread class—1A, 2A, and 3A—has a distinct tolerance level that affects its fit and, consequently, its suitability for different applications:
UNF 1A (Loose Tolerance):
The 1A class has the loosest tolerance among the UNF thread classes, making it the most flexible option. The loose fit allows for easy assembly, particularly in scenarios where components need to be quickly put together or taken apart. This flexibility reduces the risk of cross-threading and facilitates fast installation, even when precise alignment is not possible. However, this looser tolerance also means that 1A threads are less secure, and the connection may be prone to movement or loosening under stress, pressure, or vibration.
Application: The 1A class is best suited for low-pressure, low-vibration environments where quick assembly and disassembly are needed, such as temporary fixtures or frequently adjusted machinery.
UNF 2A (Medium Tolerance):
The 2A class offers a medium tolerance level, balancing the ease of assembly with a secure fit. As the most common UNF thread class, 2A threads provide a moderate level of precision, making them versatile enough for general-purpose applications. The tighter fit compared to the 1A class ensures that the connection remains stable under moderate pressure and vibration, while still allowing for relatively quick assembly and disassembly. The 2A class is the standard choice for most hydraulic and mechanical systems because it offers a reliable fit without the need for high-precision alignment.
Application: UNF 2A threads are typically used in hydraulic fittings, automotive assemblies, and industrial machinery components where a balance between precision and ease of use is necessary.
UNF 3A (Tight Tolerance):
The 3A class has the tightest tolerance among the UNF threads, providing the most secure and precise fit. This tight tolerance level minimizes movement and ensures a strong, stable connection, making 3A threads ideal for high-pressure systems, critical components, and environments subject to extreme vibration. However, the tight fit requires precise alignment during assembly, making the process more challenging and time-consuming. Additionally, due to their precision, 3A threads are often more costly to manufacture and maintain, as they need strict quality control to achieve the required specifications.
Application: UNF 3A threads are most suitable for aerospace components, high-pressure hydraulic systems, and other safety-critical applications where even slight loosening or movement could lead to system failure.
Factors to Consider When Choosing the Right Thread Class
When selecting the appropriate UNF thread class—1A, 2A, or 3A—there are several key factors to consider. Each class offers different tolerance levels that influence its suitability based on the application’s specific requirements, the environment in which it will operate, the frequency of assembly, and the materials used.
Application Type and Environment
The environment in which a threaded component operates plays a critical role in determining the appropriate thread class. Factors such as vibration, temperature extremes, pressure levels, and exposure to corrosive substances directly impact the performance and longevity of threads.
Vibration:
Applications that involve high levels of vibration, such as those found in automotive engines or industrial machinery, require a secure and stable connection. In such cases, UNF 3A threads, with their tightest tolerance, are ideal because they minimize the risk of loosening under vibration. Conversely, UNF 1A threads, with their loose fit, may not provide the necessary stability, making them unsuitable for these environments.
For moderate vibration levels, UNF 2A threads strike a balance, providing enough stability while still being easier to assemble and adjust.
Temperature Extremes:
Extreme temperatures can cause the expansion and contraction of materials, potentially affecting thread integrity. In high-temperature environments, such as those encountered in aerospace or heavy machinery, UNF 3A threads are preferred due to their precision and ability to maintain a secure fit even when materials expand. Low-tolerance threads like 1A may loosen under temperature changes, leading to failures.
For applications where temperature variations are moderate and do not critically affect material expansion, 2A threads can offer a practical solution without the need for the precision of 3A.
Pressure Levels:
High-pressure systems, especially those found in hydraulic applications, demand tight and secure connections to prevent leaks and maintain operational integrity. UNF 3A threads are particularly suitable for these high-pressure environments, as their precise fit ensures a leak-proof seal. In contrast, for low-pressure applications where the risk of leakage is minimal, UNF 1A threads may be adequate due to their ease of assembly.
Systems with moderate pressure requirements can benefit from 2A threads, as they provide a stable fit without the complexity and cost associated with 3A threads.
Corrosive and Hazardous Environments:
In environments exposed to corrosive agents or hazardous substances, such as chemical processing plants, thread integrity is paramount. The secure fit of UNF 3A threads can help prevent leaks that might lead to contamination or exposure. For less demanding environments, 2A threads can suffice, while 1A threads may be avoided if the risk of exposure or leakage poses safety concerns.
Assembly Frequency
The frequency of assembly and disassembly is another crucial consideration when choosing a thread class. Different applications require varying levels of ease and precision during assembly, directly influencing which class is most appropriate.
Frequent Assembly and Disassembly:
When components need to be assembled and disassembled regularly, as seen in maintenance-heavy systems or temporary setups, UNF 1A threads are the most suitable. Their loose tolerance allows for quick assembly without the need for precise alignment, minimizing the risk of cross-threading or damage. For example, bolts used in machinery that undergo frequent inspections or part replacements benefit from the ease of use provided by 1A threads.
Moderate Assembly Frequency:
Applications that require occasional assembly but still demand a secure fit benefit from UNF 2A threads. These threads provide enough precision to ensure stability while remaining easy to assemble and disassemble when necessary. Hydraulic systems, for instance, often use 2A threads for fittings that need to be adjusted or replaced during maintenance but must also maintain a reliable seal when in operation.
Permanent or Static Setups:
For components that are assembled once and are not intended to be frequently adjusted, such as structural components in aerospace or critical hydraulic fittings, UNF 3A threads are the best choice. Their tight tolerance ensures a strong, stable fit that remains secure over long periods, even under stress. The added precision, while making assembly more challenging, is justified by the need for a permanent, leak-free connection.
Precision Requirements
Precision is a key determinant in selecting a thread class, particularly in applications where even the smallest deviations can have significant consequences. High-precision environments, such as aerospace and medical device manufacturing, often require the use of UNF 3A threads.
Critical Applications:
In aerospace systems, where precision and stability are vital for safety, UNF 3A threads are commonly used for components such as fasteners, fittings, and other critical parts. The high precision of 3A threads minimizes the risk of component movement, ensuring that connections remain tight and stable under various stress conditions, such as high speeds, extreme temperatures, or vibrations.
Standard Precision Needs:
For applications with moderate precision requirements, like automotive assemblies or general machinery, UNF 2A threads are ideal. They provide a balance between ease of assembly and precision, making them versatile for components that need a secure fit but do not experience the extreme conditions seen in aerospace systems.
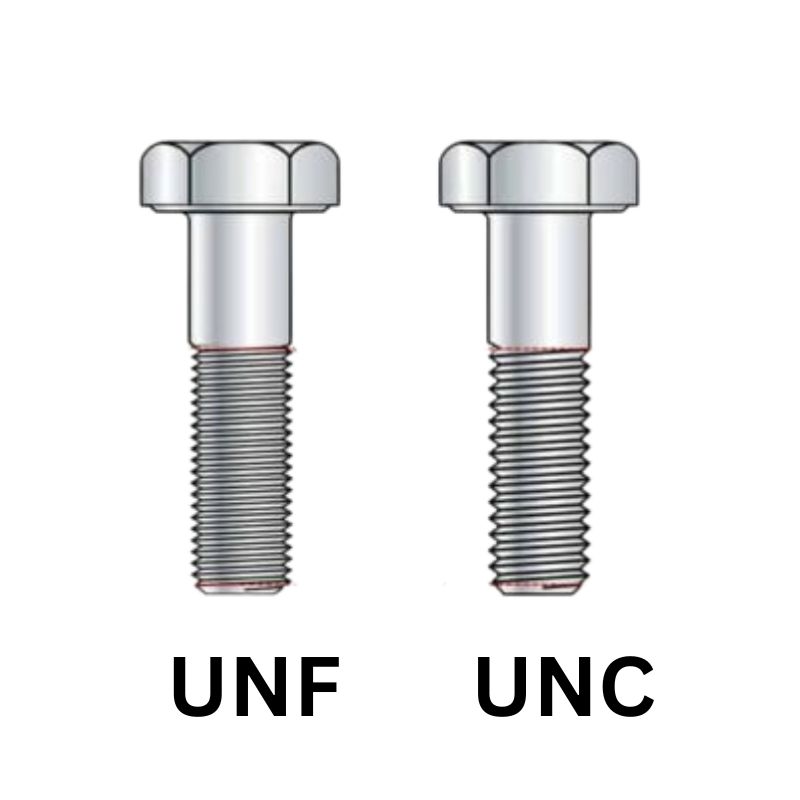
Material Compatibility
The interaction between materials is another crucial factor when selecting a thread class. Different materials can behave differently when threaded, especially under high-tolerance conditions like those of UNF 3A.
Avoiding Galling:
Galling, a form of wear caused by adhesion between sliding surfaces, is a concern when using high-tolerance threads, particularly with softer metals like aluminum or stainless steel. In applications involving these metals, using 3A threads may require additional precautions, such as using anti-seize lubricants or coatings, to prevent thread damage during assembly.
For softer metals, UNF 2A or 1A threads might be preferable, as their looser tolerances reduce the risk of galling. However, engineers must weigh this against the need for precision and stability.
Hard vs. Soft Material Pairings:
When pairing hard materials (e.g., hardened steel) with softer ones (e.g., aluminum), the choice of thread class must account for the difference in wear characteristics. For instance, 3A threads, with their tight tolerance, may be used if the softer material is coated or treated to withstand the pressure. Alternatively, using 2A threads can offer a compromise, providing enough fit precision without excessive stress on softer components.
Corrosion Resistance and Material Choices:
In corrosive environments, selecting the right material and thread class combination is vital. For stainless steel fittings in marine or chemical applications, choosing a 3A class may be essential to prevent leaks and maintain integrity. However, ensuring that the thread surfaces are treated or lubricated appropriately can extend the life of both the threads and the fittings.
Conclusion
Understanding these differences is crucial for making informed decisions when selecting thread classes. Choosing the correct UNF thread class directly impacts system performance, reliability, and safety. An incorrect choice can lead to leaks, loose connections, or even system failures, especially in high-pressure or high-vibration environments. Selecting the appropriate thread class based on the application, environment, and precision requirements ensures that components remain securely fastened, maintaining the efficiency and safety of the overall system.
FAQ
What are UNF threads?
UNF (Unified National Fine) threads are a type of thread with a fine pitch used for secure, precise connections in various applications, including hydraulics, automotive, and aerospace.
What is the difference between UNF 1A, 2A, and 3A threads?
UNF 1A threads have the loosest tolerance for easy assembly, 2A threads provide a balanced fit for general use, and 3A threads have the tightest tolerance for high-precision applications.
When should I use UNF 1A threads?
Use UNF 1A threads when components need frequent assembly and disassembly, as they offer flexibility and easy alignment, suitable for non-critical, low-pressure environments.
Why are UNF 2A threads the most common choice?
UNF 2A threads are the most versatile, offering a balanced fit that ensures both ease of assembly and a secure connection, making them ideal for most hydraulic and automotive applications.
In which situations are UNF 3A threads best used?
UNF 3A threads are ideal for high-pressure or high-vibration applications where precision and a tight fit are critical, such as in aerospace components and critical hydraulic systems.
How do I choose the right UNF thread class for my application?
Consider the application’s environment, the frequency of assembly, and the precision required. For guidance, consult professionals or industry experts to ensure the best fit for your system’s needs.