Unified National Fine (UNF) threads are a standard in the inch-based screw thread system, characterized by their fine pitch and closely spaced threads. Unlike coarse threads (UNC), UNF threads are designed for applications where precise adjustments and strong connections are necessary. These threads are commonly used in industries such as hydraulics, automotive, and aerospace, where the need for precision and reliability is paramount. In these sectors, components like bolts, nuts, and fittings often rely on UNF threads to maintain structural integrity, ensure fluid-tight connections, and prevent loosening under vibration or dynamic loads.
What Are UNF 2A and 2B Threads?
A. Definition of UNF 2A (External Threads)
UNF 2A threads are designated for external applications, such as bolts, screws, and other threaded components that fit into corresponding internal threads. These threads are characterized by:
Allowance: UNF 2A threads have a slight allowance, which is the intentional difference between the maximum material limits of the internal and external threads. This small clearance ensures that the external threads can be easily assembled and disassembled with their matching internal counterparts.
Tolerance: 2A threads maintain tighter tolerances compared to the more lenient 1A class, providing a precise fit without compromising on ease of assembly. The tighter tolerance also allows for better control over the dimensions of the thread, ensuring consistency and reducing the chances of fitting issues.
Fit: The 2A fit is a medium-tolerance fit, offering a balance between strength and ease of assembly. This makes 2A threads suitable for most general-purpose applications where both performance and convenience are important. Examples include automotive bolts, hydraulic connections, and general machinery fasteners.
By using UNF 2A threads, manufacturers can achieve a precise, stable connection while allowing for some minor flexibility to account for wear and variations in assembly conditions.
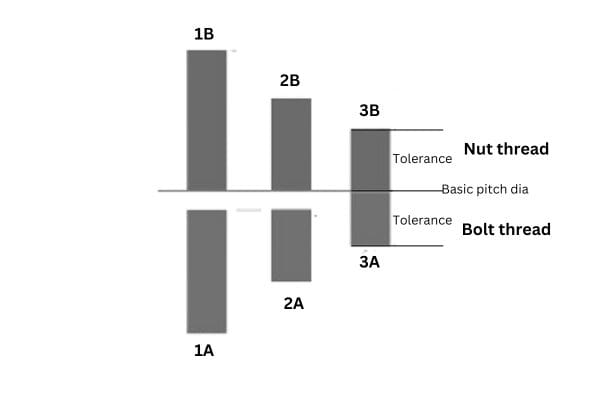
B. Definition of UNF 2B (Internal Threads)
UNF 2B threads are designed for internal applications, such as nuts, tapped holes, and threaded inserts that receive external threads like those specified as 2A. Key characteristics of 2B threads include:
Allowance: 2B threads incorporate a slightly larger allowance than their external counterparts (2A), which provides a small gap between the mating threads. This design feature ensures that components can be easily assembled and adjusted without binding or seizing, even when there are slight imperfections or contaminants present.
Tolerance: The tolerance for 2B threads is greater compared to 2A threads to accommodate the additional clearance needed for ease of assembly. This makes 2B threads more forgiving during manufacturing and assembly, ensuring compatibility with a wide range of external threads.
Fit: The fit of 2B threads is designed to match perfectly with 2A external threads, creating a secure connection. However, due to the additional allowance, 2B threads are slightly looser than 2A, facilitating easy assembly and disassembly. This fit is ideal for most industrial applications, including fasteners, hydraulic systems, and other components where repeatability and ease of maintenance are crucial.
Overall, UNF 2B threads provide a reliable and adaptable solution for internal threading, especially in applications where the consistency of fit and ease of assembly are vital.
C. Historical Context
The development of Unified National Fine (UNF) threads originated as part of the Unified Thread Standard (UTS), established during World War II to standardize thread types across the United States, the United Kingdom, and Canada. The goal was to unify thread forms and pitches to facilitate interchangeability and reduce compatibility issues between different nations’ equipment.
The 2A and 2B thread classes were standardized as part of this system to provide a practical balance between precision and assembly ease:
UNF 2A threads were standardized for external applications, allowing for precision while maintaining some flexibility to ensure components could be assembled even if slightly imperfect or dirty.
UNF 2B threads were established to provide an internal match for 2A threads, with a slight allowance and greater tolerance to facilitate easy assembly and accommodate minor variances in manufacturing.
Key Differences Between UNF 2A and 2B Threads
A. Dimensional Differences
Pitch Diameter Variations: The pitch diameter, which is the diameter of an imaginary cylinder that passes through the thread profile where the width of the thread and the width of the space between threads are equal, varies slightly between 2A and 2B threads. For 2A (external) threads, the pitch diameter is smaller compared to 2B (internal) threads to account for the necessary clearance during assembly.
Allowance: UNF 2A threads incorporate a small allowance to ensure that external components can fit into internal threads without difficulty. This allowance is an intentional gap that ensures ease of assembly and disassembly. Conversely, 2B threads feature a larger allowance than their external counterparts to accommodate the external threads comfortably, even in conditions where there might be minor imperfections or variations.
Thread Height Differences: The thread height of external threads (2A) tends to be slightly shorter than that of internal threads (2B) to allow for the mating of the components without interference. This ensures that when an external 2A thread is assembled with a corresponding 2B internal thread, they fit together smoothly.
B. Tolerance and Fit
Tolerance Levels: The tolerance level for UNF 2A threads is tighter than that of UNF 2B threads. A tighter tolerance means that 2A threads are manufactured with precise control over dimensions, which is critical for external threads that need to align perfectly with the corresponding internal threads.
2B Thread Allowance: UNF 2B threads are designed with a greater allowance compared to 2A threads. This larger clearance makes the internal threads more accommodating when receiving external threads, reducing the likelihood of binding or difficulty during assembly. This is particularly beneficial in environments where external threads may be slightly worn or contaminated.
Impact on Fit: The looser fit of 2B threads is intended to make assembly easier and quicker, especially when dealing with large volumes of components or in environments where precision tooling might not always be available. On the other hand, the tighter fit of 2A threads provides better alignment and strength, which is essential for applications where secure and stable connections are critical.
C. Application-Specific Differences
Use Cases for 2A Threads (External):
Precision Components: In applications like automotive, aerospace, and hydraulic systems, where precise alignment is crucial for performance and safety, 2A threads are commonly used for bolts, screws, and other external components.
Load-Bearing Connections: For components that need to bear significant loads or are subject to dynamic forces, 2A threads provide the necessary precision and strength. This is especially important in structural or high-pressure systems where a secure fit is vital.
Situations Requiring Stability: In contexts where vibration or movement might cause loosening, the tighter fit of 2A threads helps maintain stability and reduces the risk of component failure.
Use Cases for 2B Threads (Internal):
General-Purpose Fasteners: 2B threads are widely used in nuts, tapped holes, and other internal threaded components for general applications. They provide a balance between precision and ease of assembly, making them suitable for mass-production environments where components must fit reliably with minimal adjustment.
Maintenance-Focused Environments: In situations where components need to be disassembled and reassembled frequently, such as in maintenance operations or field repairs, 2B threads provide the necessary allowance to facilitate easy, repeated use without damaging the threads.
Assembly Tolerance Requirements: 2B threads are preferred in cases where external threads might be subject to slight wear, dirt, or minor deformities. The greater tolerance and allowance of 2B threads ensure that assembly can still be achieved smoothly, even under less-than-ideal conditions.
D.Applications and Industries Using UNF 2A and 2B Threads
Automotive Industry
Precision Components: In the automotive industry, UNF 2A and 2B threads are commonly used for critical components such as engine parts, transmission systems, and chassis assemblies. The precise fit offered by these threads ensures that fasteners remain secure under high vibration and dynamic loads typical in vehicle operations.
Engine Assembly: UNF threads are often applied in engine blocks and cylinder heads where the need for precision and alignment is paramount. Bolts with 2A threads secure these components tightly to ensure no movement or displacement occurs during operation, while 2B threads are used in corresponding nuts or tapped holes to maintain stability and prevent leaks.
Suspension and Brake Systems: Fasteners with UNF threads are preferred in areas such as suspension systems and brake components, where precision and secure connections are necessary to maintain vehicle safety and performance.
Hydraulic Systems
Leak Prevention: In hydraulic systems, where fluid integrity is crucial, UNF threads (2A for fittings and 2B for ports or connectors) are often used to minimize leakage. The precise fit between these threads ensures that hydraulic connections are secure, reducing the risk of fluid escape that could lead to system failure.
Compatibility: Hydraulic components require consistent thread specifications to ensure compatibility between various parts like hoses, fittings, and valves. The use of standardized UNF 2A and 2B threads simplifies the design and assembly process, ensuring reliable and compatible connections across different parts of the system.
Durability in High-Pressure Applications: The precision offered by 2A threads is critical for components exposed to high pressure in hydraulic systems. The tighter fit prevents any shifting or loosening under pressure, maintaining system integrity and performance.
How to Identify and Measure UNF 2A and 2B Threads
A. Tools for Measurement
To accurately identify and measure UNF 2A (external) and 2B (internal) threads, it’s essential to use the right tools. These tools help verify the dimensions, pitch, and fit of threads to ensure they conform to specifications:
Calipers: Calipers are used to measure the diameter of the threads (major, minor, and pitch diameters). Digital calipers are recommended for precise measurements, especially when working with fine threads like UNF.
Thread Gauges: Thread gauges, also known as thread pitch gauges or thread checkers, are essential for determining the pitch of the threads. They come in various configurations for identifying both coarse (UNC) and fine (UNF) threads, and they help ensure that the pitch matches the specification (e.g., 16 threads per inch for 3/8″-16).
Micrometers: Micrometers offer a higher level of accuracy than calipers, particularly when measuring the pitch diameter. They are valuable for confirming the precise dimensions required for tight tolerance threads like UNF 2A and 2B.
Optical Comparator: In professional settings, an optical comparator can be used to visually inspect and compare the profile of the threads against a standard profile, ensuring conformity with specifications.
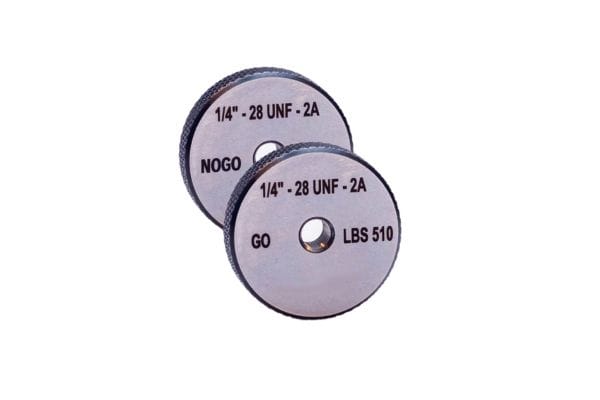
B. Step-by-Step Guide to Measuring External (2A) and Internal (2B) Threads
Preparation:
Ensure the components being measured are clean and free of debris or oil, as contaminants can interfere with measurements.
Gather the necessary tools, such as calipers, thread gauges, and micrometers.
Measuring External Threads (2A):
Step 1: Measure the Major Diameter:
Use calipers to measure the major diameter (the outermost points) of the external thread. This gives you a preliminary measurement to confirm the size (e.g., 3/8″, 1/2″, etc.).
Step 2: Check the Pitch Using a Thread Gauge:
Align the appropriate thread gauge with the threads to confirm the pitch. Ensure it fits snugly along the thread’s profile, matching the number of threads per inch.
Step 3: Measure the Pitch Diameter with a Micrometer:
The pitch diameter is crucial for identifying UNF 2A threads accurately. Use a thread micrometer to measure the pitch diameter and confirm it falls within the specified tolerance for the class.
Step 4: Verify the Profile (Optional for precision settings):
Use an optical comparator to inspect the thread profile visually, ensuring the angle and shape conform to UNF standards.
Measuring Internal Threads (2B):
Step 1: Measure the Minor Diameter:
For internal threads, use calipers to measure the minor diameter (the innermost points) of the threads. This gives an initial indication of whether the internal thread matches the expected size.
Step 2: Verify the Pitch Using a Thread Gauge:
Insert the appropriate thread gauge into the internal threads to confirm the pitch. Make sure the gauge aligns with the thread without gaps or movement.
Step 3: Measure the Pitch Diameter with a Micrometer:
Use a micrometer or a specialized thread plug gauge to measure the pitch diameter of the internal threads. Ensure it falls within the tolerance range specified for 2B threads, which will have a slightly looser fit than 2A threads.
Step 4: Inspect the Thread Profile (Optional):
An optical comparator can also be used to inspect the profile of the internal threads if precise confirmation is needed, especially for critical applications.
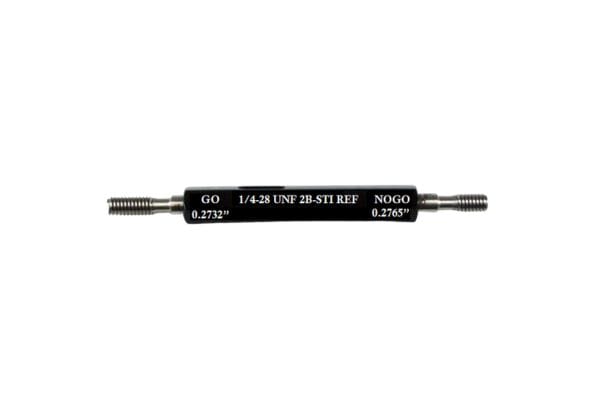
C. Common Mistakes to Avoid
Incorrect Gauge Selection:
One of the most common errors is using the wrong thread gauge for pitch measurement. Always ensure that the gauge corresponds to the UNF designation (e.g., 16 threads per inch for a 3/8″-16 UNF thread). Using an incorrect gauge can lead to misidentification.
Not Accounting for Wear:
Threads can wear over time, especially in high-use applications. When measuring older components, it’s crucial to consider wear and damage, as these can affect measurements. Check for deformation or flattening of threads before taking measurements.
Measuring Contaminated Threads:
Dust, oil, or other contaminants can interfere with accurate measurements. Always clean threads thoroughly before measuring to avoid inaccurate readings. In hydraulic or fluid system environments, it’s essential to use a degreaser or cleaning solution to remove all residues.
Ignoring Temperature Variations:
Measuring threads in environments with significant temperature fluctuations can result in dimensional changes. For the most accurate measurements, ensure that components are measured in a controlled environment where temperatures are stable, as metal expands or contracts with temperature changes.
Using Worn or Inaccurate Tools:
Ensure that tools like calipers, micrometers, and thread gauges are properly calibrated and not worn out. A worn tool can lead to incorrect readings, especially when measuring fine tolerances like those in UNF threads.
Best Practices for Choosing Between UNF 2A and 2B Threads
A. Factors to Consider
When selecting between UNF 2A and 2B threads, it’s crucial to evaluate several factors to ensure the best fit and functionality for your application:
Application Requirements:
Function and Load: Consider whether the component will bear significant loads or be subject to dynamic forces and vibrations. For load-bearing applications or those involving high precision, a tighter fit (2A external threads with 2B internal threads) ensures stability and security.
Ease of Assembly and Disassembly: If the application requires frequent assembly and disassembly, such as in maintenance scenarios or field repairs, 2B threads with a slightly larger allowance provide flexibility, making the process smoother.
Tolerance Requirements:
Precision: In industries like aerospace or hydraulics, where exact tolerances are critical to safety and performance, using threads with tighter tolerances (2A for external and 2B for internal) is essential. Evaluate whether the application demands precision over ease of assembly.
Fit Quality: Consider the fit quality needed. For applications where a more secure and tight fit is important, such as in fluid systems where leaks must be prevented, choosing 2A and 2B threads with precise matching tolerances helps maintain system integrity.
Material Compatibility:
Material Strength: Different materials (e.g., steel, aluminum, brass) have varying levels of strength and resistance to wear. Softer materials might require a more forgiving thread fit (2B) to accommodate slight deformities, while harder materials can maintain tighter tolerances without risk of damage.
Corrosion Resistance: For applications exposed to harsh environments (e.g., marine, chemical, or outdoor settings), materials with anti-corrosive properties should be chosen. Ensure that the material used for both the 2A and 2B threads is compatible to prevent galvanic corrosion and maintain a secure fit over time.
Environmental Conditions:
Temperature Extremes: If the components will be used in environments with high or low temperatures, metal expansion or contraction should be considered. Ensure that the chosen threads can maintain a secure fit under these conditions without risking loosening or deformation.
Exposure to Fluids or Chemicals: In hydraulic or chemical processing systems, selecting the appropriate thread fit and material (2A and 2B threads) helps prevent leaks and ensures the connection remains tight even under exposure to fluids. Use additional sealing techniques or thread coatings to enhance the connection’s durability.
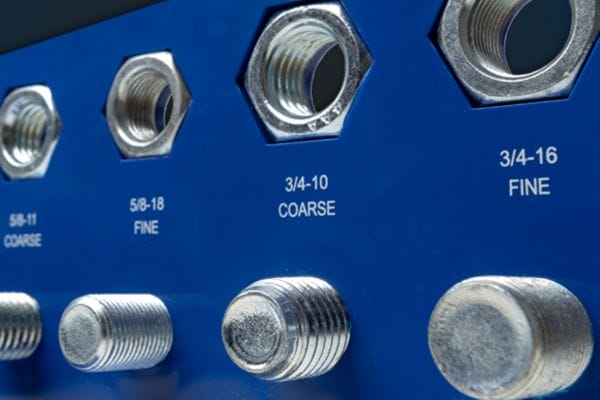
B. Matching Threads for Optimal Performance
Properly pairing UNF 2A and 2B threads is essential for achieving a reliable and effective connection. Here are some best practices:
Ensuring Compatibility Between 2A and 2B Threads:
Always match external 2A threads with internal 2B threads to maintain the intended tolerance and allowance balance. This pairing is designed to provide a secure and tight fit while allowing for sufficient clearance during assembly.
Avoid pairing a 2A thread with an incorrectly sized internal thread class, as this can result in misalignment, improper fit, or potential damage to the threads during assembly.
Checking Thread Specifications:
Verify that the threads conform to the same specifications (e.g., 3/8″-16 UNF) to ensure they are compatible. Using mismatched thread sizes or pitches, even if they appear similar, can compromise the connection’s integrity and lead to failure.
Use thread gauges and calipers to confirm that both the 2A and 2B threads are within the specified tolerance range for the application.
Balancing Precision and Flexibility:
For applications where both precision and ease of assembly are important, such as in hydraulic systems, pairing 2A and 2B threads allows for a fit that is precise enough to prevent leaks while providing enough clearance to avoid binding during installation.
In cases where exact precision is less critical, such as non-load-bearing fasteners or components that need to be adjusted frequently, the looser fit of 2B threads can be advantageous for quicker and easier assembly.
Utilizing Thread Sealants and Lubricants:
For high-pressure systems or environments where leakage is a concern, using thread sealants (like PTFE tape or liquid thread sealant) ensures a leak-proof connection between 2A and 2B threads. This practice helps enhance the seal, especially in hydraulic or pneumatic applications.
In high-friction or corrosive environments, applying thread lubricants or anti-corrosive coatings can help maintain the integrity of the 2A and 2B threads, reducing wear and making disassembly easier when needed.
Ensuring Proper Alignment During Assembly:
Misalignment during assembly can cause cross-threading or damage, especially with precise 2A threads. Make sure that components are aligned correctly and that tools like torque wrenches are used when necessary to achieve the correct tension without over-tightening, which can distort the threads.
Common Issues and Troubleshooting Tips for UNF Threads
A. Thread Damage and Wear
Thread Galling:
Galling is a common issue with UNF threads, especially when metal surfaces rub against each other under high pressure or friction. It occurs when material from one thread surface transfers to another, causing seizing or jamming. Galling can be particularly problematic with softer metals like aluminum or stainless steel. It is often exacerbated when threads are assembled without proper lubrication.
Thread Wear:
Repeated use or frequent assembly and disassembly of components can cause threads to wear down over time. This can lead to a reduction in the effective pitch diameter, making it difficult for the threads to engage properly and resulting in loose or insecure connections.
Deformation:
Threads can become deformed due to over-tightening, cross-threading, or exposure to excessive loads. When a thread is over-torqued, it can become stretched or distorted, reducing its ability to maintain a secure fit. Cross-threading, where the threads are misaligned during assembly, can also cause significant damage and affect the integrity of the component.
Corrosion:
Exposure to corrosive environments or chemicals can weaken and degrade threads, especially if they are not treated or coated for corrosion resistance. Corroded threads are more likely to seize or become damaged during assembly and disassembly, compromising the connection.
B. Proper Maintenance Techniques
Regular Inspection:
Periodically inspect threaded components for signs of wear, deformation, or corrosion. Use magnification tools if necessary to detect minor defects or damage that might not be visible to the naked eye. For critical applications, consider implementing a routine inspection schedule to ensure threads remain in good condition.
Lubrication:
Apply a suitable thread lubricant or anti-seize compound before assembly to reduce friction, prevent galling, and protect against corrosion. Lubricants are particularly important when assembling UNF threads in high-temperature environments or when using materials prone to galling, such as stainless steel.
Thread Cleaning:
Before assembly, ensure threads are clean and free of debris, dust, or metal particles that could cause binding or wear. Use a wire brush or compressed air to clean threads thoroughly. In hydraulic or fluid systems, consider using a solvent-based cleaner to remove any residual oil or contaminants that might affect the seal.
Use of Protective Coatings:
In environments where threads are exposed to moisture, chemicals, or other corrosive elements, consider applying protective coatings, such as zinc plating or anodizing, to enhance corrosion resistance and extend the life of the threads.
Proper Torque Application:
Always use a torque wrench to apply the correct amount of torque as specified for the particular thread and application. Over-torquing can deform threads, while under-torquing may result in loose connections. For critical applications, consider using calibrated tools to ensure the correct torque values are consistently applied.
C. Troubleshooting Assembly Problems
Cross-Threading:
Problem: Cross-threading occurs when the external and internal threads are misaligned during assembly, causing the threads to engage incorrectly. This can result in damage or jamming.
Solution: To avoid cross-threading, start threading the component by hand and ensure it is aligned properly before using tools. If resistance is felt early in the threading process, stop immediately, back out the fastener, and realign it before trying again. Using thread guides or fixtures can help maintain proper alignment during assembly.
Thread Sizing:
Problem: Thread seizing, often caused by galling, happens when the threads lock together during assembly, making it difficult or impossible to turn the fastener.
Solution: Applying a high-quality lubricant or anti-seize compound to the threads before assembly can prevent seizing. If seizing does occur, apply a penetrating oil and allow it to soak before attempting to loosen the fastener. If threads are frequently seizing, consider using components made from materials less prone to galling, such as coated or treated metals.
Loose Connections:
Problem: Loose connections can occur if threads wear out, the wrong torque is applied, or if incompatible threads (e.g., mixing different classes) are used.
Solution: Verify that the thread classes (2A and 2B) match and that they are of the correct specification (e.g., 3/8″-16 UNF). Use a torque wrench to apply the appropriate torque value. If components frequently loosen due to vibration, consider using thread lockers or locking fasteners designed to maintain tension.
Thread Corrosion:
Problem: Corroded threads can become difficult to engage or disengage and may lead to thread damage if forced.
Solution: Inspect threads for signs of rust or corrosion before assembly. If corrosion is present, clean the threads thoroughly using a wire brush or rust remover. Apply anti-corrosion treatments or coatings to the threads for protection, and use stainless steel or treated materials if corrosion is a recurring issue in the environment.
Thread Deformation:
Problem: Threads that become deformed due to over-tightening or excessive load may not fit properly or may create weak connections.
Solution: If threads show signs of deformation, replace the affected components. To prevent future deformation, ensure the correct torque values are used and avoid over-tightening. Using torque-limiting tools or calibrated torque wrenches helps prevent damage.
Conclusion
Selecting the appropriate thread type is essential for achieving the best performance, durability, and safety in threaded connections. The right choice ensures compatibility, prevents issues such as cross-threading and leakage, and supports the specific needs of the application. Adherence to standards, such as matching 2A and 2B threads, is crucial to maintaining consistency and reliability across industries. Understanding the specific requirements of your application, including load-bearing capacity, environmental conditions, and precision needs, is key to making informed decisions and avoiding common thread-related problems.
FAQ
What is the difference between UNF 2A vs 2B threads?
UNF 2A threads are used for external applications such as bolts and screws, while UNF 2B threads are used for internal applications such as nuts and threaded holes. 2A threads are tighter, while 2B threads have more clearance for easier assembly.
Why choose UNF 2A threads?
2A threads provide a more precise fit for applications that require high precision and stability, such as critical components in the automotive and aerospace sectors.
What are the benefits of 2B threads?
UNF 2B threads have a larger clearance for applications that require frequent assembly and disassembly for easy maintenance and quick installation.
In which industries are UNF threads widely used?
UNF 2A and 2B threads are widely used in industries such as automotive, aerospace, hydraulics, as well as manufacturing and construction to ensure precise and reliable connections.
How can I prevent wear and damage to UNF threads?
Regular inspection, cleaning, and lubrication of threads can prevent wear and galling. Also, use proper torque tools to avoid over-tightening.
Can I mix 2A and 2B threads?
2A and 2B threads should be used in matched pairs as specified, with 2A used externally and 2B internally, to ensure optimal fit and performance and avoid compatibility issues.