ISO 8434-6 is a key standard within the ISO 8434 series, specifically focusing on 60° cone connectors used in fluid power and general applications. This standard outlines these connectors’ design, dimensions, and performance requirements, which are crucial for ensuring system integrity and efficiency. The significance of 60° cone threads lies in their ability to provide reliable sealing and secure connections, minimizing the risk of leaks and ensuring optimal fluid flow.
Understanding ISO 8434-6
ISO 8434-6 is a crucial standard in hydraulic connections, specifically addressing 60° cone connectors. Part of the broader ISO 8434 series, this standard sets forth guidelines for the design, dimensions, and performance characteristics necessary to ensure effective fluid power transfer. The connectors detailed in ISO 8434-6 are primarily utilized in hydraulic systems and general applications, making them essential for various industries that rely on fluid mechanics.
Definition and Scope of ISO 8434-6
ISO 8434-6 defines the specifications for 60° cone connectors, including their construction from materials such as stainless steel and carbon steel. The standard specifies dimensions for both tube outside diameters (ranging from 6 mm to 50 mm) and corresponding hose sizes (5 to 51), facilitating compatibility across a wide array of applications. This part of the ISO 8434 series is designed to ensure that the connectors provide robust, leak-free connections, thus enhancing the reliability and efficiency of hydraulic systems.
The scope of ISO 8434-6 includes the dimensional tolerances and mechanical properties required for optimal performance under specified conditions. It also addresses the design features that contribute to effective sealing, especially when used with O-rings or other sealing methods. These specifications are vital for manufacturers, engineers, and maintenance professionals who seek to maintain high standards of quality and performance in their hydraulic systems.
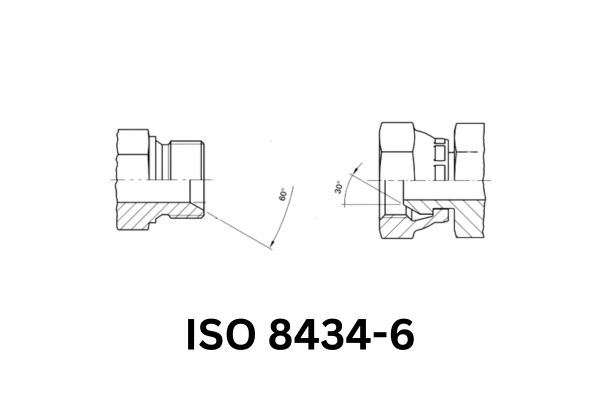
Importance in Fluid Power and General Applications
The relevance of ISO 8434-6 in fluid power systems cannot be overstated. As industries increasingly rely on hydraulic technology for efficient operation, the need for dependable and standardized connectors becomes critical. 60° cone connectors, as specified in ISO 8434-6, offer several advantages, including:
Enhanced Sealing Performance: The design of the 60° cone allows for tighter fits and better sealing capabilities, reducing the likelihood of leaks in hydraulic circuits. This is especially important in systems that operate under high pressures and varying temperatures.
Compatibility and Interchangeability: By adhering to ISO 8434-6, manufacturers can ensure that their 60° cone connectors will be compatible with other components designed to this standard. This interchangeability simplifies repairs and upgrades, minimizing downtime.
Versatility Across Applications: From automotive to aerospace, the applications for 60° cone connectors are vast. Their ability to connect tubes and hoses reliably makes them suitable for a variety of fluid power systems, enhancing efficiency and performance across different sectors.
The Design of 60° Cone Threads
The design of 60° cone connectors is critical for ensuring efficient fluid transfer and maintaining system integrity in hydraulic applications. These connectors, governed by the ISO 8434-6 standard, are engineered to provide reliable performance under varying conditions of pressure and temperature. This section delves into the specific design specifications, materials used, and dimensional requirements associated with 60° cone connectors.
Specifications for 60° Cone Connectors
60° cone connectors are designed to facilitate a secure, leak-free connection between tubes and ports. The key specifications outlined in ISO 8434-6 include:
Connection Type: The connectors feature a 60° conical seating surface, which allows for optimal alignment and sealing when mated with corresponding fittings or O-ring seals.
Pressure Ratings: These connectors are designed to withstand significant internal pressures, making them suitable for high-performance hydraulic systems. The standard defines specific pressure limits based on the diameter of the tubing or hose used.
Sealing Options: Connectors can be used with or without O-ring seals. When O-rings are employed, they enhance the sealing capability, further reducing the risk of leaks.
Compatibility: ISO 8434-6 connectors are intended for use with components that adhere to other related ISO standards, such as ISO 6149-1 and ISO 1179-1, ensuring a high degree of interoperability within hydraulic systems.
Materials Used
The choice of materials for 60° cone connectors is crucial to their performance and durability. The most commonly used materials include:
Stainless Steel: Known for its excellent corrosion resistance, stainless steel is often used in environments where the connectors are exposed to moisture, chemicals, or high temperatures. This material provides strength and longevity, making it ideal for applications in the automotive, aerospace, and industrial sectors.
Carbon Steel: Carbon steel is another popular choice, particularly for applications where cost-effectiveness is a priority. While it may not offer the same level of corrosion resistance as stainless steel, it provides adequate strength for many hydraulic applications when properly treated with coatings or finishes to mitigate corrosion.
Coatings and Treatments: To enhance durability, connectors may undergo various surface treatments, such as galvanization or plating, which provide additional resistance to corrosion and wear. These treatments are especially important in harsh environments, where exposure to chemicals or abrasive materials can lead to premature failure.
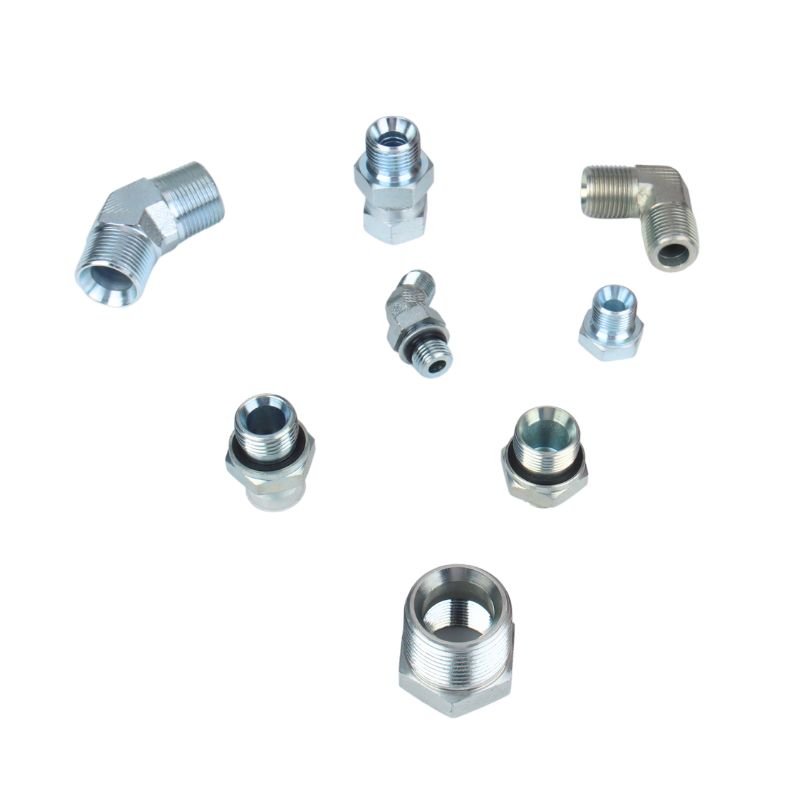
Dimensional Requirements and Tolerances
The dimensional accuracy of 60° cone connectors is critical for ensuring proper fit and function. ISO 8434-6 specifies several key dimensional requirements:
Cone Angle: The 60° angle is critical for creating the proper seating surface, which affects the sealing performance and overall connection strength. Deviations from this angle can lead to ineffective sealing and increased risk of leakage.
Outside Diameter: The outside diameter of the tube or hose to which the connector is mated must fall within specified ranges (6 mm to 50 mm). Tolerances on these diameters ensure compatibility with fittings and ports.
Length and Thread Specifications: The length of the connector and any threaded portions must adhere to specified tolerances to guarantee a secure fit. Threads must meet standard specifications (e.g., metric threads) to ensure proper engagement with mating components.
Surface Finish: The surface finish of the connector is also defined to ensure a smooth mating surface, which is vital for effective sealing and reducing wear during operation. The standard may specify maximum surface roughness values to maintain performance standards.
Comparison with Other Connector Types
24° Cone Connectors vs 60° Cone Connectors
Design Differences:
The primary distinction between 24° and 60° cone connectors lies in the angle of their conical seating surfaces. While 24° cone connectors feature a shallower angle, 60° connectors provide a steeper angle that allows for more effective sealing under high pressure. This design difference can affect the fit and sealing efficiency, particularly in dynamic applications.
Sealing Performance:
60° cone connectors typically offer better sealing capabilities compared to their 24° counterparts. The sharper angle of the 60° design allows for a tighter seal, which is particularly beneficial in high-pressure environments where the risk of leaks is heightened. Conversely, 24° cone connectors may be more prone to leaks under similar conditions.
Applications:
24° connectors are often used in applications where the sealing requirements are less stringent, such as low-pressure systems or non-critical hydraulic circuits. In contrast, 60° cone connectors are preferred in applications demanding higher reliability, such as in mobile machinery, aerospace, and other industries where safety is paramount.
O-Ring Face Seal Connectors vs 60° Cone Connectors
Design and Functionality:
O-ring face seal connectors utilize a flat face and an O-ring to create a seal, providing a different sealing mechanism compared to the conical design of 60° cone connectors. This design allows for greater flexibility in alignment and can accommodate slight misalignments, making O-ring face seal connectors suitable for dynamic applications.
Sealing Integrity:
While O-ring face seal connectors offer excellent sealing performance, they can be susceptible to wear and damage over time, especially in high-pressure applications. In contrast, 60° cone connectors provide a more robust mechanical seal, which can be advantageous in environments where vibration and shock are factors.
Applications:
O-ring face seal connectors are commonly used in hydraulic systems where the ability to tolerate misalignment is critical, such as in mobile equipment. On the other hand, 60° cone connectors are favored in static applications or where precise alignment is achievable, such as in stationary hydraulic systems.
When to Choose 60° Cone Threads Over Alternatives
Choosing the right connector type depends on the specific requirements of the application. Here are some key considerations for opting for 60° cone connectors:
High-Pressure Environments: If your application involves high-pressure conditions, 60° cone connectors are often the better choice due to their superior sealing capabilities.
System Integrity and Reliability: For critical systems where leaks can result in severe consequences, the robust sealing provided by 60° cone connectors makes them a preferred option.
Compatibility with Existing Systems: If your existing hydraulic components adhere to ISO standards that include 60° cone connectors, using these connectors can ensure compatibility and system integrity.
Installation and Maintenance Tips
Best Practices for Installing 60° Cone Connectors
Proper installation of 60° cone connectors is crucial for achieving optimal performance and ensuring leak-free connections. Here are some best practices:
Preparation: Before installation, ensure that the surfaces of the connectors and mating components are clean and free from debris, dirt, or old sealant. This preparation helps achieve a proper seal.
Alignment: Align the connectors carefully during installation. Misalignment can lead to uneven pressure distribution, which may cause leaks. Use proper tools to maintain alignment while tightening.
Torque Specifications: Adhere to the manufacturer’s torque specifications when tightening the connectors. Over-tightening can damage the connector or cause deformation, while under-tightening can result in leaks.
Maintenance Considerations to Ensure Longevity
Regular maintenance is essential for extending the life of 60° cone connectors:
Inspection: Regularly inspect connectors for signs of wear, corrosion, or damage. Look for leaks around the connection points, which may indicate deterioration.
Cleaning: Keep connectors clean by removing dirt and contaminants. Use appropriate cleaning agents that do not harm the material of the connectors.
Replacement of Seals: If O-rings or other sealing components show signs of wear or damage, replace them promptly to maintain sealing integrity.
Common Issues and Troubleshooting Advice
Common issues with 60° cone connectors include leaks, misalignment, and corrosion. Here’s how to troubleshoot:
Leaks: If leaks are detected, first check for proper torque and alignment. Inspect O-rings for damage and replace if necessary. Ensure that all surfaces are clean.
Misalignment: If connectors are misaligned, loosen them and realign carefully. Ensure that no components are under stress, which could lead to premature failure.
Corrosion: If corrosion is observed, consider whether the connector material is suitable for the operating environment. Replace corroded connectors to prevent system failures.
Pressure and Temperature Requirements
Overview of Pressure Limits Specified in ISO 8434-6
ISO 8434-6 specifies pressure limits for 60° cone connectors based on the diameter of the tubing or hose. These limits are critical for ensuring that the connectors can safely handle the expected operational pressures without failure. The standard outlines specific values, which are determined by factors such as material strength and design specifications. Adhering to these pressure limits is essential to prevent leaks and system failures, ensuring the safety and reliability of hydraulic systems.
Temperature Tolerance and Its Importance
Temperature tolerance is another critical aspect outlined in ISO 8434-6. The connectors are designed to operate within specific temperature ranges, typically defined in the standard. High temperatures can lead to material degradation, while low temperatures may affect sealing capabilities. Understanding the temperature tolerance is vital for selecting the right connectors for applications that experience extreme thermal conditions.
Implications for System Design and Selection
When designing hydraulic systems, it is essential to consider both pressure and temperature requirements. Select connectors that not only meet the pressure ratings specified in ISO 8434-6 but also operate effectively within the required temperature ranges. This consideration helps ensure that the system will perform reliably under expected operating conditions, thereby reducing the risk of failures and enhancing overall system performance. Proper selection and adherence to these specifications can lead to safer, more efficient hydraulic systems, ultimately benefiting end-users and operators.
Conclusion
For those interested in integrating 60° cone connectors into their systems or seeking further information, we encourage you to reach out. Our team is ready to assist with tailored solutions and competitive quotes to meet your hydraulic needs. Contact us today to ensure you have the best connectors for your fluid power applications!
FAQ
What are 60° cone connectors used for?
They are primarily used in hydraulic systems for reliable fluid transfer, offering excellent sealing and high-pressure capabilities.
How do 60° cone connectors differ from 24° cone connectors?
The main difference is the cone angle; 60° connectors provide better sealing and are more suitable for high-pressure applications.
Can 60° cone connectors be used without O-rings?
Yes, they can be used with or without O-ring seals, depending on the application requirements.
What materials are commonly used for 60° cone connectors?
They are typically made from stainless steel or carbon steel, ensuring durability and resistance to corrosion.
How should I maintain 60° cone connectors?
Regularly inspect for wear, keep them clean, and replace O-rings or seals to prevent leaks.
What are the pressure limits for 60° cone connectors?
Pressure limits vary based on size and application; consult ISO 8434-6 for specific ratings related to your connectors.