Fittings are crucial components in hydraulic and pneumatic systems, ensuring the secure and leak-free connection of various components. They maintain system integrity under varying pressures, temperatures, and operational conditions. JIC, BSP, thrust-wire, and face seal fittings each serve specific purposes in different applications. Understanding their unique features and appropriate use cases is essential for optimizing system performance.
Overview of Fitting Types
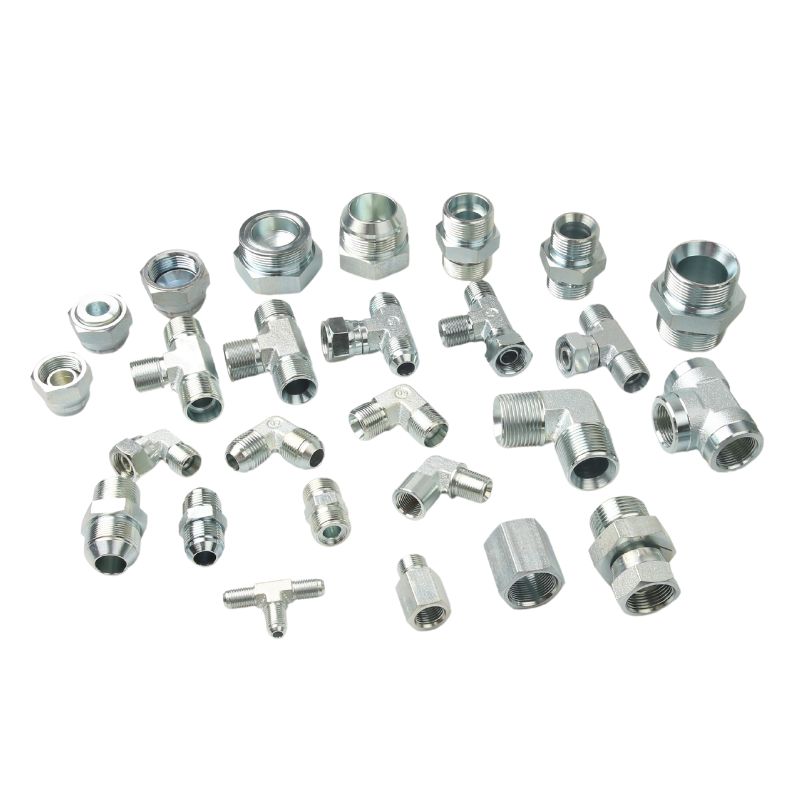
A. JIC Fittings
Definition and History: JIC fittings are standardized fittings commonly used in hydraulic systems. They feature a 37-degree flare seating surface, which helps create a metal-to-metal seal.
Common Applications: Widely used in industries like automotive, aerospace, and industrial hydraulics due to their reliability and ease of installation.
Advantages: JIC fittings are versatile, compatible with various systems, and known for their widespread use and availability, making them a go-to option for many professionals.
B. BSP Fittings
Definition and Background: BSP (British Standard Pipe) fittings are commonly used in the UK and other countries following British standards. They are available in two thread types: BSPT (tapered) and BSPP (parallel).
Types of BSP Threads:
BSPT (British Standard Pipe Tapered): Tapered threads that seal by thread interference.
BSPP (British Standard Pipe Parallel): Parallel threads that usually require an O-ring or gasket for sealing.
Common Applications: These fittings are often used in plumbing and hydraulic systems, particularly in regions where British standards are prevalent.
C. Thrust-Wire Fittings
Introduction: Thrust-wire fittings are designed to withstand high-vibration environments. They incorporate a wire or ring that helps maintain the integrity of the connection under stress.
Applications: Ideal for applications where fittings are exposed to frequent vibrations or movement, such as in heavy machinery and industrial equipment.
Benefits: The unique design of thrust-wire fittings enhances sealing, reduces the risk of leaks, and improves the durability of connections in demanding conditions.
D. Face Seal Fitting
Explanation: Face seal hydraulic fittings utilize a flat sealing surface and a seal (often an O-ring) to create a secure, leak-proof connection. These fittings are known for their high-pressure sealing capabilities.
Common Applications: Commonly used in hydraulic systems that operate under high pressure, such as in aerospace, defense, and high-performance industrial applications.
Key Benefits: Face seal hydraulic fittings are highly effective in preventing leaks, are easy to maintain, and offer a reliable solution for high-pressure environments.
When to Use JIC Fittings
A. Industry Applications
JIC (Joint Industry Council) fittings are widely recognized and utilized across multiple industries that demand robust, reliable, and versatile hydraulic connections. Their design, characterized by a 37-degree flare seating surface, provides a strong seal that can withstand significant pressure, making them a preferred choice in environments where performance and safety are paramount.
Automotive Industry:
- Hydraulic Systems: In the automotive industry, JIC fittings are commonly used in hydraulic systems, including those found in power steering, braking systems, and hydraulic lifts. Their ability to securely handle high pressures makes them suitable for these critical applications where any leakage could lead to system failure or safety hazards.
- Fuel Lines: JIC fittings are also employed in fuel lines due to their compatibility with various types of fluids, including gasoline, diesel, and hydraulic oils. The flare design ensures that connections remain tight, even under the vibration and movement typical in automotive environments.
Agriculture Industry:
- Heavy Machinery: In agriculture, heavy machinery such as tractors, harvesters, and irrigation systems often use hydraulic systems that require dependable connections. JIC fittings are used in these machines due to their durability and ability to handle the high pressures and rugged conditions typically encountered in agricultural environments.
- Versatility Across Equipment: The compatibility of JIC fittings with a wide range of equipment and fluid types means they are a versatile option for agricultural applications, where different types of machinery may need to be interconnected within a single system.

B. Key Considerations for Use
When selecting JIC fittings, several critical factors must be taken into account to ensure optimal performance and longevity of the hydraulic system. These considerations help in choosing the right fitting for the specific application, preventing issues such as leaks, system failures, or unnecessary maintenance.
Pressure Rating:
High-Pressure Tolerance: JIC fittings are designed to withstand high pressures, which makes them suitable for demanding hydraulic applications. However, it is essential to verify that the specific JIC fitting selected meets or exceeds the pressure requirements of the system. Overlooking pressure ratings can lead to fitting failure, resulting in costly downtime and repairs.
Operating Temperature:
Temperature Range: The operating temperature of the system is another critical consideration. JIC fittings are typically made from materials such as stainless steel, carbon steel, or brass, which have different thermal properties. It is important to choose a material that can handle the temperature extremes the system will encounter. For instance, stainless steel JIC fittings are often used in applications involving high temperatures or corrosive environments.
Fluid Compatibility:
Chemical Resistance: The type of fluid being conveyed through the system can significantly impact the performance and longevity of the JIC fitting. Some fluids may be corrosive or chemically reactive with certain fitting materials. Therefore, ensuring fluid compatibility with the fitting material is crucial. For example, if the hydraulic fluid is aggressive or prone to causing corrosion, stainless steel JIC fittings would be a better choice over carbon steel.
System Flexibility:
Dynamic Applications: JIC fittings are ideal for systems that require flexibility and movement, as their design allows for some degree of movement without compromising the seal. This makes them particularly useful in applications where hoses or tubes are subject to movement, vibration, or expansion and contraction due to temperature changes.
C. Regional Standards and Compatibility
One of the significant advantages of JIC fittings is their broad compatibility with other fitting types and adherence to widely recognized standards, making them a versatile option in global applications.
Compatibility with AN (Army-Navy) Fittings:
Interchangeability: JIC fittings share the same 37-degree flare seating angle as AN fittings, which are commonly used in military and aerospace applications. This similarity allows for interchangeability between JIC and AN fittings, making JIC fittings a convenient choice for systems that may already use AN fittings or where compatibility with AN fittings is required. This interchangeability extends the utility of JIC fittings in various industries, from military applications to civilian aerospace and automotive sectors.
North American and SAE Standards:
Recognition in North America: JIC fittings are standardized under SAE J514, which means they are widely recognized and used in North America. This standardization ensures that JIC fittings meet specific performance criteria, making them a reliable choice for engineers and technicians working in regions that adhere to SAE standards.
Global Reach: While JIC fittings are most commonly used in North America, their compatibility with other standards and fitting types, such as those found in European or Asian markets, makes them a viable option for global applications. This global compatibility ensures that JIC fittings can be used in systems that cross regional boundaries, simplifying supply chains and reducing the need for multiple fitting types in a single system.
When to Use BSP Fittings
A. Global Applications
BSP (British Standard Pipe) fittings are integral to hydraulic and pneumatic systems in regions where British and European standards prevail. These fittings are the default choice in many industries across the UK, Europe, Australia, and other regions influenced by British engineering standards. They are particularly prevalent in sectors such as oil and gas, marine, construction, and manufacturing.
In the oil and gas industry, BSP fittings are often used in both upstream and downstream applications, where reliable and leak-proof connections are critical. Marine applications also benefit from BSP fittings due to their robustness and compatibility with other standardized components. In the construction industry, where equipment and machinery often need to meet specific regulatory standards, BSP fittings provide a reliable option that aligns with local and regional regulations.
B. Choosing Between BSPT and BSPP
One of the key decisions when using BSP fittings is choosing between BSPT (British Standard Pipe Tapered) and BSPP (British Standard Pipe Parallel) threads. The distinction between these two thread types is crucial as it determines the fitting’s sealing method and suitability for different applications.
- BSPT (Tapered Threads): BSPT fittings have tapered threads, meaning the thread diameter decreases or increases along the length of the fitting. This tapering effect allows for a tight, self-sealing connection as the threads are screwed together, which compresses the threads and creates a seal. BSPT threads are typically used in applications where a tight seal is required without the need for additional sealants. This makes BSPT ideal for high-pressure systems where reliability and ease of installation are important. However, care must be taken to ensure that the taper angle matches correctly with the corresponding female part, as mismatched tapers can lead to leaks.
- BSPP (Parallel Threads): BSPP fittings, on the other hand, have parallel threads, meaning the thread diameter remains consistent along the length of the fitting. BSPP threads do not create a seal by themselves and thus require the use of an O-ring, washer, or another sealing mechanism to ensure a leak-proof connection. BSPP fittings are preferred in applications where consistent thread engagement is necessary, and where the use of an O-ring provides additional sealing security. This makes BSPP fittings particularly suitable for hydraulic systems where fluid compatibility and pressure containment are critical.
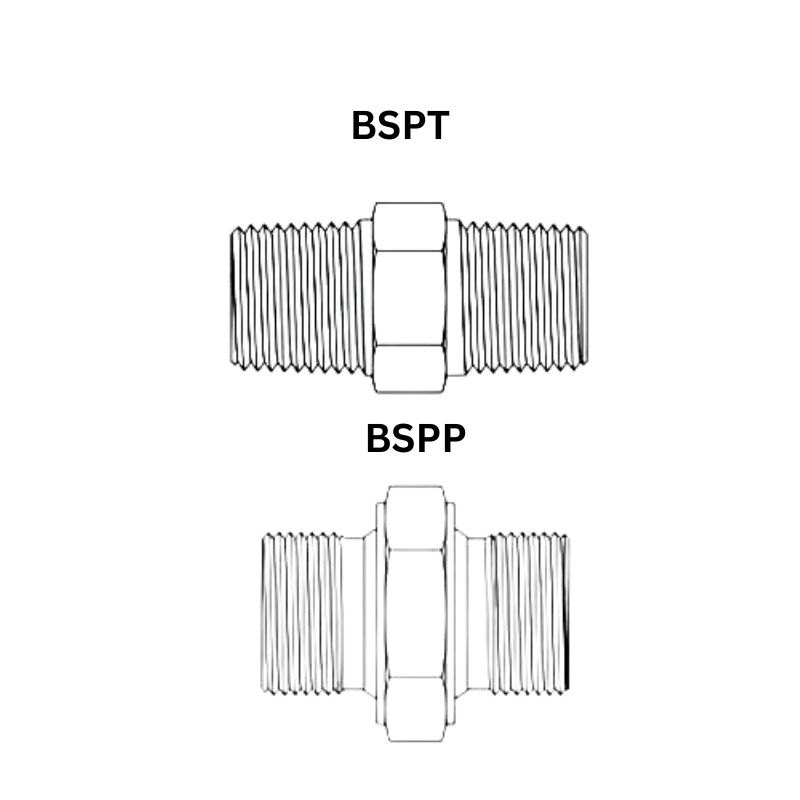
Choosing between BSPT and BSPP depends on the specific requirements of the system, including pressure levels, the need for additional sealing components, and the type of fluid being transported. In some cases, industry standards or regulations may dictate the preferred thread type, further influencing the decision.
BSP Adaptor Pressure Ratings
Nominal Bore Diameter | Design Working Pressure | Proof Pressure | Over Pressure | ||||
Inch | mm | PSI | BAR | PSI | BAR | PSI | BAR |
1/8 | 5 | 5,145 | 350 | 7,718 | 525 | 20,580 | 1,400 |
1/4 | 6.3 | 6,500 | 450 | 9,750 | 675 | 22,000 | 1,520 |
3/8 | 10 | 5,500 | 380 | 8,250 | 570 | 19,000 | 1,310 |
1/2 | 12.5 | 4,500 | 310 | 6,750 | 465 | 16,000 | 1,100 |
5/9 | 14.25 | 4,200 | 289 | 6,375 | 434 | 14,170 | 964 |
5/8 | 16 | 4,000 | 280 | 6,000 | 420 | 12,350 | 850 |
3/4 | 19 | 3,500 | 240 | 5,250 | 360 | 11,000 | 750 |
1 | 25 | 2,500 | 170 | 4,500 | 310 | 9,750 | 675 |
1-1/4 | 32 | 2,500 | 170 | 3,750 | 255 | 7,700 | 530 |
1-1/2 | 37.5 | 2,000 | 136 | 3,000 | 204 | 5,940 | 404 |
2 | 50 | 1,250 | 84 | 3,000 | 204 | 5,940 | 404 |
2-1/2 | 62.5 | 1,250 | 84 | 1,860 | 126 | 3,596 | 245 |
3 | 75 | 1,120 | 76 | 1,680 | 114 | 3,170 | 216 |
C. Key Considerations for Use
When selecting BSP fittings for a particular application, several factors need to be considered to ensure optimal performance and longevity:
- Sealing Method: The choice between BSPT and BSPP threads will largely dictate the sealing method. BSPT provides a self-sealing mechanism through thread compression, while BSPP requires an O-ring or washer to achieve a seal. The specific sealing needs of the system should guide the selection process.
- Thread Type and Compatibility: It’s crucial to ensure that the male and female threads are compatible, both in terms of type (BSPT vs. BSPP) and thread pitch. Incompatible threads can lead to improper sealing, leaks, and potential system failures.
- Environmental Conditions: The environmental conditions where the fittings will be used should also be considered. For example, in marine applications, corrosion resistance is a key factor, so selecting fittings made from materials that can withstand saltwater exposure is essential. Similarly, in high-temperature environments, the material’s thermal expansion properties and the fitting’s ability to maintain a seal under varying temperatures should be evaluated.
- System Requirements: The specific requirements of the hydraulic or pneumatic system, including pressure ratings, fluid type, and flow rate, must be assessed. BSP fittings are versatile, but ensuring that the chosen fitting meets the system’s pressure and flow requirements is critical to avoid performance issues.
- Installation and Maintenance: Consideration should also be given to the ease of installation and maintenance. BSP fittings, particularly BSPP, often require precise installation to ensure a proper seal and regular maintenance checks should be scheduled to inspect the integrity of the seals and threads.
When to Use Thrust-Wire Fittings
A. What Are Thrust-Wire Fittings?
Thrust-wire fittings are specialized hydraulic fittings designed to enhance the sealing capability and overall reliability of connections in systems subjected to high vibration and pressure. The key feature of these fittings is the incorporation of a thrust-wire—typically a thin, robust wire embedded within the fitting. This wire acts as an additional sealing mechanism, providing extra stability to the connection by compensating for the movement and stress that occurs in high-vibration environments. Thrust-wire fittings are particularly valuable in applications where standard fittings may loosen or fail due to intense operational conditions.
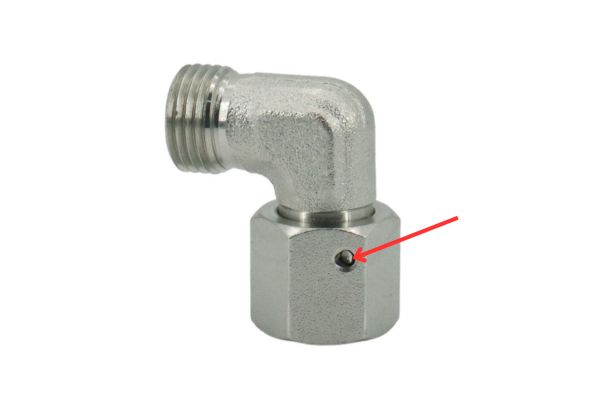
B. High-Vibration and High-Pressure Applications
Thrust-wire fittings are particularly well-suited for environments characterized by high vibration and pressure, such as those found in heavy machinery, mining, and construction equipment. These industries often involve equipment that operates under extreme conditions, where components are subjected to constant movement, pressure fluctuations, and mechanical shocks.
In such settings, standard fittings might not be sufficient to maintain a secure connection over time, as the constant vibration can cause threads to loosen and seals to degrade, leading to leaks and potential system failures. Thrust-wire fittings address this challenge by providing a more robust connection that remains secure even when exposed to significant vibrational forces. The thrust-wire helps maintain the integrity of the seal, ensuring that the connection remains leak-proof and reliable throughout the equipment’s operation.
For example, in mining operations where hydraulic systems are critical for the functioning of drilling equipment, thrust-wire fittings can prevent downtime caused by fitting failures. Similarly, in construction machinery, where equipment is often subjected to rough handling and varying pressures, these fittings ensure that the hydraulic systems continue to operate efficiently without the risk of leaks or other failures.
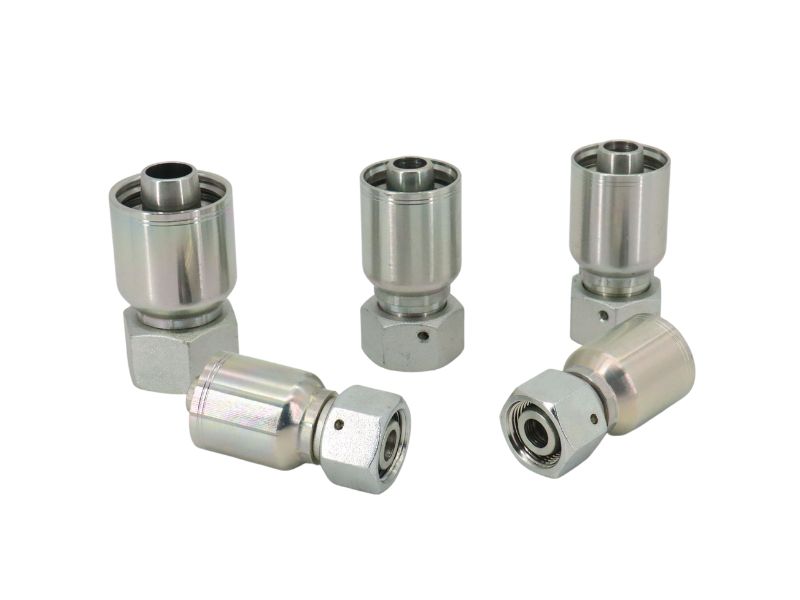
C. Durability and Reliability
The inclusion of a thrust-wire in these fittings significantly enhances their durability and reliability, making them a preferred choice in applications that demand long-lasting and fail-safe performance. The thrust-wire acts as a secondary sealing mechanism, which not only helps maintain a tight connection but also compensates for any wear or deformation that might occur over time due to constant stress and vibration.
This added durability is particularly important in systems where maintenance is challenging or infrequent, as it reduces the likelihood of leaks and system failures that could lead to costly repairs or downtime. For instance, in remote mining operations or heavy machinery used in construction projects, the ability to rely on the continuous performance of hydraulic systems is crucial. Thrust-wire fittings provide that assurance by offering a more resilient connection that can withstand the harshest operational conditions.
When to Use Face Seal Hydraulic Fittings
A. High-Pressure Systems
Face seal hydraulic fittings, often referred to as O-ring face seal (ORFS) fittings, are specifically designed for use in high-pressure hydraulic systems where the integrity of the connection is of utmost importance. These fittings are engineered to create a tight, reliable seal that can withstand the intense pressures commonly found in industries like aerospace, automotive manufacturing, and industrial hydraulics.
The robust design of face seal hydraulic fittings, combined with the use of an O-ring, makes them ideally suited for these applications, where the fittings must consistently perform under demanding conditions.
B. Preventing Leaks
One of the primary advantages of face seal hydraulic fittings is their exceptional ability to prevent leaks, even in high-pressure environments. The key to this leak prevention lies in the O-ring that is seated in a groove on the face of the fitting. When the fitting is tightened, the O-ring is compressed against the mating surface, creating a secure, leak-proof seal.
This O-ring provides a secondary sealing mechanism, which is particularly valuable in applications where vibration, pressure fluctuations, or thermal expansion could otherwise compromise the integrity of the connection. The O-ring’s ability to adapt to minor imperfections on the mating surfaces also enhances the fitting’s ability to maintain a seal over time, reducing the risk of leaks due to wear or deformation.
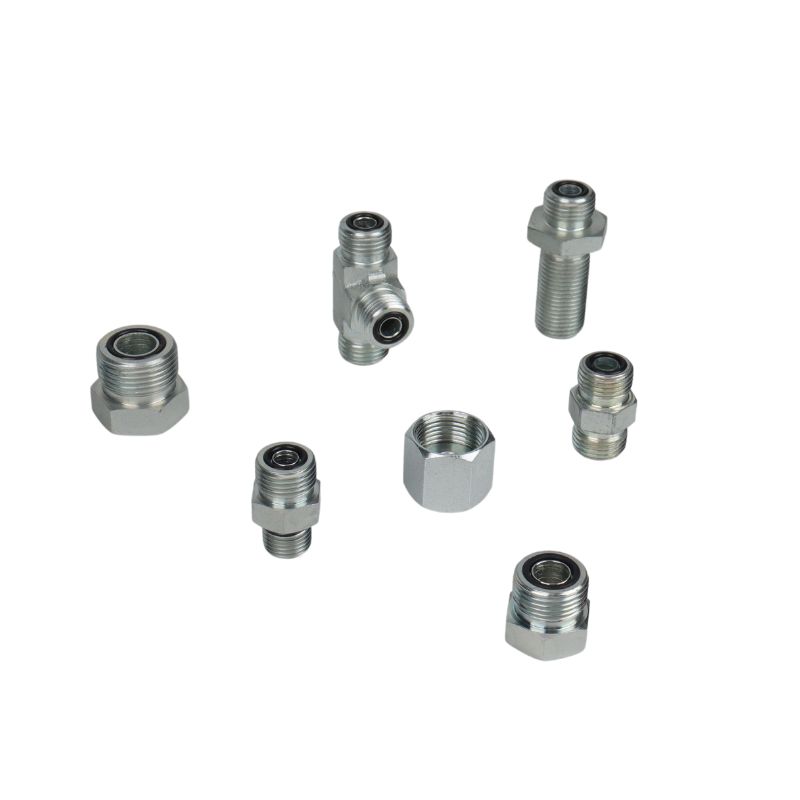
C. Installation
To fully realize the benefits of face seal hydraulic fittings, proper installation and regular maintenance are essential. The effectiveness of the O-ring seal, and therefore the overall performance of the fitting, depends heavily on the quality of the installation process.
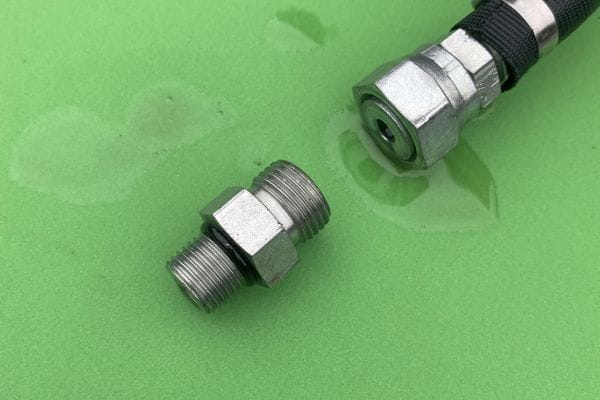
Installation Best Practices:
- Surface Preparation: Ensure that the mating surfaces are clean, smooth, and free of any debris or contaminants that could interfere with the O-ring’s ability to form a seal. Surface imperfections, such as scratches or dents, can compromise the seal and lead to leaks.
- O-ring Inspection: Before installation, inspect the O-ring for any signs of damage, such as cuts, cracks, or flattening. A damaged O-ring should be replaced immediately to ensure a proper seal.
- Lubrication: Apply a light coat of compatible lubricant to the O-ring before installation. This helps to reduce friction during assembly, preventing damage to the O-ring and ensuring smooth, even compression.
- Proper Torque: Use a torque wrench to tighten the fitting to the manufacturer’s specified torque values. Over-tightening or under-tightening can both lead to sealing issues. Over-tightening can crush the O-ring, while under-tightening may not compress the O-ring sufficiently to form a proper seal.
- Alignment: Ensure that the fittings are properly aligned before tightening. Misalignment can cause uneven compression of the O-ring, leading to leaks.
Conclusion
As we’ve discussed, each fitting type has its own set of strengths and is best suited for certain conditions. Whether you’re dealing with high-pressure systems, environments with significant vibration, or systems that require compatibility with specific regional standards, understanding the unique characteristics of JIC, BSP, thrust-wire, and face seal hydraulic fittings will help you make informed decisions.
FAQ
What are JIC fittings used for?
JIC fittings are commonly used in hydraulic systems across various industries, including automotive, aerospace, and agriculture. They are known for their versatility and ability to handle high-pressure environments.
What is the difference between BSPT and BSPP fittings?
BSPT fittings have tapered threads that create a tight seal without the need for additional sealants. BSPP fittings have parallel threads and typically require an O-ring or washer to ensure a leak-proof connection.
When should I use thrust-wire fittings?
Thrust-wire fittings are ideal for applications subjected to high vibration and pressure, such as in heavy machinery, mining, and construction equipment. They provide enhanced durability and leak prevention under extreme conditions.
What are face seal hydraulic fittings and where are they used?
Face seal hydraulic fittings, or O-ring face seal (ORFS) fittings, are designed for high-pressure hydraulic systems. They use an O-ring to create a secure, leak-proof seal, making them suitable for aerospace, automotive, and industrial hydraulic systems.
How do I properly install face seal hydraulic fittings?
To install face seal hydraulic fittings properly, ensure the mating surfaces are clean and smooth, inspect and lubricate the O-ring, use a torque wrench to tighten to specified values, and ensure proper alignment.
What should I consider when selecting hydraulic fittings for my system?
When selecting hydraulic fittings, consider factors such as pressure rating, temperature, fluid compatibility, and the specific requirements of your system.