While ball valves are known for their ability to provide rapid on/off flow control with a simple quarter-turn, needle valves are designed for precision flow regulation, allowing fine adjustments in low-flow applications.
Understanding Needle Valves
Definition
A needle valve is a type of valve used for precise control over fluid flow. Named for its slender, needle-like plunger, it allows for fine adjustments, which is essential in applications where accurate flow control is crucial. The design enables the valve to regulate flow with exceptional precision, especially in low-flow scenarios, making it ideal for tasks like sampling, calibration, and gradual pressure reduction.
Components
Needle valves consist of several key components that work together to control fluid flow finely:
Needle: The main control element, is tapered to fit into the valve seat, allowing fluid to flow around it in adjustable amounts. The needle’s sharp, pointed end allows for precise flow modulation.
Seat: The needle’s tapered tip sits into this seat, forming a tight seal when closed, preventing leakage. The seat is often made from materials that are compatible with the fluid being handled, enhancing durability.
Stem: The stem connects the needle to the handle or actuator, transmitting motion from the handle to the needle for control.
Body: The body houses the other components and provides the structure. Typically, needle valve bodies are made of durable materials like stainless steel, brass, or plastic, depending on the intended environment.
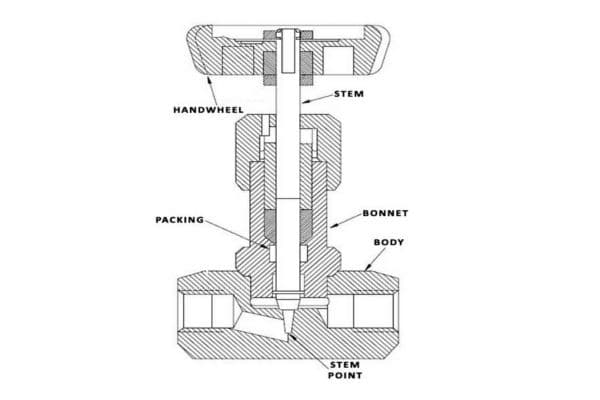
How It Works
Needle valves operate through a simple yet effective flow control mechanism. When the handle is turned, it rotates the stem, which raises or lowers the needle inside the valve body. The more the needle is lifted from the seat, the more fluid can pass around it, gradually increasing the flow. This threaded design enables fine adjustments, allowing operators to set the valve to the exact flow rate needed. As the needle moves closer to the seat, the flow rate decreases until the valve is completely shut off. This gradual control makes needle valves ideal for processes where small flow changes are necessary over time.
Advantages
Needle valves are highly valued for their ability to provide precise flow control. Unlike ball valves, which open and close quickly, needle valves are suited for applications where gradual flow modulation is critical. They are also well-equipped to handle high-pressure systems due to their robust construction, often withstanding pressures of up to several thousand psi. Their fine control allows for smooth, incremental adjustments, making them indispensable in sensitive applications where even minor fluctuations in flow or pressure can impact outcomes. Additionally, needle valves can achieve a tight shutoff, minimizing leakage, which is beneficial in applications involving hazardous or expensive fluids.
Applications
Due to their fine control capabilities, needle valves are common in a range of industries and applications where precise flow regulation is essential:
Laboratories: Needle valves are frequently used in lab settings for processes like sampling, testing, and calibration, where accurate flow rates are vital for experiments.
Pressure Regulation: In high-pressure systems, needle valves provide incremental adjustments to maintain stable pressures, ensuring equipment safety and performance.
Instrumentation: Needle valves are widely used in instrumentation setups, such as flow meters and pressure gauges, to ensure consistent and controlled flow for accurate readings.
Hydraulics and Pneumatics: These valves are utilized to control hydraulic fluid or compressed air in systems where slight changes in pressure or flow need to be finely managed.
Chemical Processing: Needle valves are often employed in the chemical industry for dosing and precise addition of chemicals into a process line, where control over flow is crucial to avoid reactions or contamination.
Needle Valves vs Ball Valves
When choosing between needle valves and ball valves, it’s important to consider the specific needs of your system, such as flow control, pressure handling, and the level of precision required. While both are widely used for regulating the flow of fluids, their designs and functionalities are quite different. Below, we compare needle valves and ball valves across several critical parameters:
Flow Control Mechanism
Needle Valves:
Needle valves are specifically designed for fine, precise flow control. This precision is achieved through the tapered design of the needle, which fits into the valve seat. As the valve stem is rotated, the needle gradually moves into or out of the seat, regulating the flow rate incrementally. This allows operators to adjust the flow in very small amounts, making needle valves ideal for applications where detailed control is critical. The thread design of the needle allows for fine adjustments, making them perfect for controlling flow in systems where the flow rate must be monitored and carefully regulated.
The main strength of needle valves lies in their ability to control low-flow applications with high accuracy, such as in laboratory settings or in applications where very specific fluid volumes need to be controlled. This ability to fine-tune the flow makes needle valves unsuitable for applications requiring high flow rates, as they are designed for slow, controlled changes in flow.
Ball Valves:
In contrast, ball valves operate on a much simpler mechanism. The valve uses a hollow, perforated ball that rotates inside the valve body. When the ball’s hole is aligned with the pipeline, the valve is fully open, allowing fluid to flow freely. When the ball is rotated 90 degrees, the hole is no longer aligned with the flow path, and the valve shuts off the flow. This quarter-turn operation is fast and provides on/off control with a low operating effort.
Ball valves excel in applications that require rapid shut-off or full-flow regulation. Their operation is simple, which makes them ideal for high-flow systems or situations where quick flow shutoff or isolation is needed. However, ball valves are not well-suited for fine flow modulation. They typically perform best when the valve is either fully open or fully closed, and any in-between states can be difficult to manage without specialized designs, such as V-port ball valves.
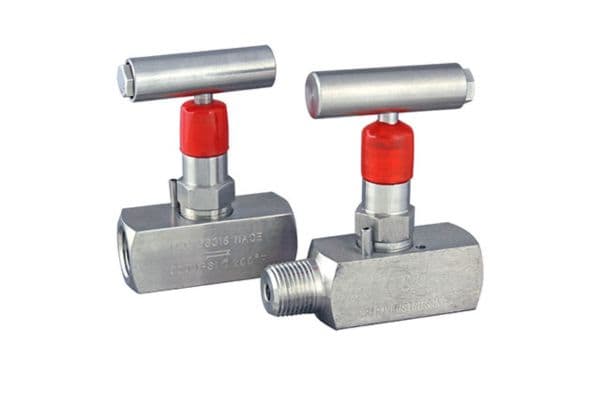
Flow Rate and Pressure Handling
Needle Valves:
Needle valves are designed to handle low flow rates and high-pressure situations. Their precision threading allows them to regulate fluid in systems that require tight control under high-pressure conditions, without introducing significant pressure drops. The fine adjustment mechanism is particularly useful in environments where the fluid flow must be reduced gradually or held steady under variable pressure conditions. However, needle valves tend to have a higher resistance to flow compared to ball valves, which limits their use in high-flow systems.
In terms of pressure handling, needle valves are particularly suited for situations where precise regulation is needed, even at high pressure. This is because their sealing mechanism is designed to withstand significant pressure without leaking. Therefore, needle valves are commonly used in applications like pressure reduction, flow metering, and hydraulic systems where managing flow precisely is critical to the safety and efficiency of the process.
Ball Valves:
Ball valves, on the other hand, are designed for high flow and low pressure drop systems. The design of the ball valve allows fluid to pass through with minimal resistance, making them ideal for applications involving larger flow rates. Because of their quick opening and closing action, ball valves are able to handle fluids in large pipelines or systems that require rapid shutoff, such as in gas distribution or water treatment systems.
When it comes to pressure handling, ball valves generally perform well under moderate to high pressure, but they are more suitable for applications where the flow rates are high and there is not as much need for fine control. Unlike needle valves, ball valves are better for systems that require less regulation of flow and more control over overall flow rate and system isolation.
Precision and Adjustability
Needle Valves:
Needle valves shine when it comes to precision and adjustability. Their design allows for incremental adjustments, giving operators the ability to make very small changes in flow rates. This level of precision is especially useful in applications where consistent, gradual flow is important. Needle valves are commonly used in pressure regulation and metering applications, where the ability to finely control flow can make a significant difference in the system’s performance.
The threaded needle design offers high control over flow, but it also means the operation of the valve is relatively slow, requiring more turns of the handle or actuator to make even minor adjustments. This makes them unsuitable for applications that require fast, frequent changes in flow rate. In systems that demand fine control over flow rate, needle valves are often preferred over other valve types, but their limitations in terms of speed and maximum flow capacity must be considered.
Ball Valves:
Ball valves are less suited for fine adjustments compared to needle valves. While ball valves do provide fast, on/off control, their design doesn’t support the same level of precise, incremental adjustments that needle valves do. Ball valves work best in applications where the primary need is for either full-on or full-off flow regulation, and they are typically used in systems where the flow rate is either fully open or fully closed, such as in pipeline isolation, shutoff valves, or diverting flow.
However, in certain cases, ball valves can be designed with specialized ports (like V-port ball valves) or actuators to achieve a degree of flow modulation, but even then, they can’t match the precision offered by needle valves. Ball valves are ideal for situations where the flow must either be completely allowed or completely stopped, and they are not intended for gradual changes.
Choosing the Right Valve: Needle Valve vs Ball Valve
Application Suitability
When to Choose a Needle Valve
Needle valves are best suited for high-precision control applications where fine adjustments to the flow rate are critical. Their primary advantage lies in their ability to provide incremental flow regulation, which is essential in sensitive systems that require controlled flow under specific conditions. Common applications for needle valves include:
Laboratory Settings: Needle valves are frequently used in research and laboratory environments where precise fluid flow is necessary for experiments, calibration, or testing. In these settings, even small fluctuations in flow can lead to incorrect results, so needle valves are ideal for providing the fine control needed to maintain accuracy.
Instrumentation: For processes requiring precise measurement of flow rates, needle valves are preferred. They are often used in conjunction with flow meters, pressure gauges, or other measurement devices, where precise flow control ensures accurate readings.
Pressure Regulation: In systems where pressure must be carefully controlled, such as in hydraulic or pneumatic systems, needle valves are commonly employed. They allow for gradual pressure adjustments, making them suitable for applications where a stable, controlled pressure is necessary over time.
Needle valves are generally used in applications with low to medium flow rates and high pressure, where the ability to make small, controlled changes in flow is more important than achieving a high flow rate.
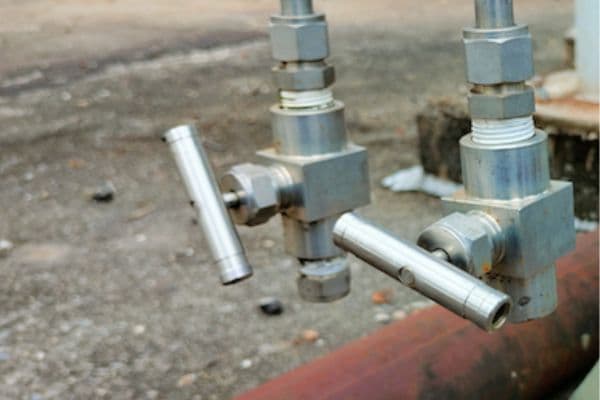
When to Choose a Ball Valve
Ball valves, on the other hand, are designed for on/off flow control and are typically used in systems where a quick shutoff or isolation is needed. The simplicity of the ball valve’s quarter-turn operation makes it suitable for applications where speed and reliability are paramount. Common use cases for ball valves include:
Industrial Pipelines: Ball valves are widely used in industrial pipelines where the main requirement is to control large volumes of fluid. They are often used for isolation purposes, such as turning on or off the flow of water, gas, or other materials through large-diameter pipes.
HVAC Systems: In heating, ventilation, and air conditioning (HVAC) systems, ball valves are used to control the flow of air or water with minimal pressure drop. They are also employed to isolate sections of the system during maintenance or when balancing the system.
Gas and Chemical Handling: Ball valves are ideal for systems where the flow of gases or chemicals needs to be stopped or started quickly. They are often used in shutoff applications, such as in gas distribution systems or in the oil and gas industry.
Ball valves excel in environments that require rapid flow control, such as systems with high flow rates and frequent shutoff demands. Their ability to handle large volumes of fluid with minimal resistance makes them unsuitable for applications that require fine, precise adjustments.
Flow Control Needs
Needle Valves for Precise Flow Regulation
Needle valves are specifically designed for highly controlled, low-flow applications. The key feature that sets them apart from other valve types is their ability to offer very fine adjustments to the flow. This is achieved through the threaded needle design, which allows the operator to make incremental changes in the flow rate. As the needle is adjusted, the opening through which the fluid flows becomes narrower or wider, offering precise control.
Needle valves are commonly used in applications where gradual changes in flow are necessary, such as in laboratories, calibration setups, or instrumentation systems. They are also used to restrict flow in pressure control systems to ensure that the pressure stays within safe and optimal ranges.
Ball Valves for Rapid Flow Control and Isolation
Ball valves, due to their simple quarter-turn operation, are designed for rapid flow control and complete shutoff. Once the valve is opened, it allows fluid to flow unrestricted until it is turned off, at which point the flow stops completely. This makes them ideal for applications requiring quick, full-flow isolation. Ball valves are often used in systems where the flow needs to be either fully on or fully off, with little to no intermediate control.
In large industrial processes or piping systems, ball valves offer a quick response time and minimal flow resistance, making them the ideal choice for high-flow applications like water treatment plants, HVAC systems, or natural gas pipelines. While they cannot match needle valves for precision, they are well-suited for systems where the need for precise flow regulation is secondary to rapid on/off control.
Pressure and Temperature Considerations
Pressure Handling
Needle valves are typically used in high-pressure applications where flow must be controlled precisely. Their design allows for high resistance to pressure fluctuations, and they can handle pressures of several thousand psi in certain configurations. This makes them ideal for hydraulic systems, gas sampling, or fluid systems that operate under high pressure, where controlling the pressure and flow rate is crucial for maintaining the integrity of the system.
While ball valves can handle moderate to high pressures, they are generally not suited for the same extreme pressure control that needle valves can provide. Ball valves can withstand pressures up to a certain point, but their primary function is to allow for full-flow control, which can result in increased pressure drops when used in high-pressure systems.
Temperature Tolerance
Both needle valves and ball valves can be designed to handle a wide range of temperatures, depending on the materials used in their construction. However, needle valves are often chosen for more temperature-sensitive applications due to their ability to provide fine flow regulation at a wide range of temperatures. High-quality needle valves can be constructed with materials that resist temperature fluctuations, ensuring stable performance.
Ball valves are typically better suited for higher temperature ranges and general industrial use, but they are usually employed in systems where temperature control is less of a concern. They can handle hot fluids or gases as long as the flow is either fully open or fully shut, which is ideal for applications where temperature regulation is less complex.
Conclusion
When choosing between a needle valve and a ball valve, it is essential to first consider the nature of the flow (high or low), the required precision, and the pressure and temperature conditions of the system. Needle valves are the go-to choice when fine control and precision are needed, while ball valves are the best option for systems requiring quick and reliable flow shutoff. Always align the valve selection with the system’s operational needs to ensure optimal performance and longevity.
FAQ
What is the main difference between a needle valve and a ball valve?
Needle valves offer precise flow control with fine adjustments, while ball valves provide quick, full-flow shutoff or isolation with a simple quarter-turn mechanism.
Which valve is better for high-pressure systems?
Needle valves are typically better suited for high-pressure systems where fine flow regulation is necessary.
Can ball valves be used for flow regulation?
While ball valves are great for on/off control, they are not suitable for precise flow regulation like needle valves. They are ideal for systems with high flow rates.
Where are needle valves typically used?
Needle valves are commonly used in laboratories, instrumentation systems, and pressure regulation applications where precision is critical.
Are ball valves good for industrial pipelines?
Yes, ball valves are commonly used in industrial pipelines, providing fast and reliable isolation with minimal pressure drop.
Can needle valves handle high flow rates?
Needle valves are generally designed for low-flow applications. For high-flow needs, ball valves are the better choice due to their ability to manage larger volumes.