Grease fittings are typically located at the joints or pivot points where parts move or rotate, which are susceptible to friction. Without these grease fittings, friction and wear would increase significantly, leading to premature breakdowns and frequent repairs.
Understanding Grease Fittings
A. What are Grease Fittings?
Definition and Purpose in Machinery
A grease fitting (also known as a zerk fitting, grease nipple, or lubrication fitting) is a small mechanical component used to inject lubricating grease into various parts of a machine. The fitting is designed to connect to a grease gun, enabling the technician or operator to deliver the appropriate amount of lubricant to components such as bearings, joints, and other moving parts that require regular lubrication to reduce friction and wear.
Grease fittings’ primary purpose is to ensure that machinery operates smoothly by maintaining optimal lubrication levels at critical points. By allowing easy grease injection into hard-to-reach areas, grease fittings help extend the lifespan of mechanical components, reduce wear and tear, prevent overheating, and ensure that the system runs efficiently without causing excessive damage to the equipment.
Types of Grease Fittings
Standard Grease Fitting: The most commonly used type of grease fitting, often referred to as a “Zerk fitting,” features a straight nozzle and can be used in various applications. It is widely used in automotive and industrial machinery.
Angled Grease Fitting: This fitting has a 45° or 90° angle, making it easier to grease components that are difficult to access. It is ideal for tight spaces or when the fitting is mounted in a location that is not easily reached with a straight fitting.
Button Head Grease Fitting: A button-shaped fitting, typically used in situations where space is extremely limited or where it may need to be flush against a surface. These are ideal for industrial and automotive applications where space is a concern.
Rotary Grease Fittings are used in rotating components, such as machinery where parts are continuously turned, such as axles or wheels. The rotating motion ensures that the grease fitting doesn’t obstruct the machinery’s operation.
Straight Grease Fitting: This type has a simple straight design and is used for standard applications where the fitting can be easily accessed. It is the most common and widely recognized style.
Each type of grease fitting has been designed with specific applications and equipment in mind, ensuring the correct flow of lubricant to critical components in the machinery.
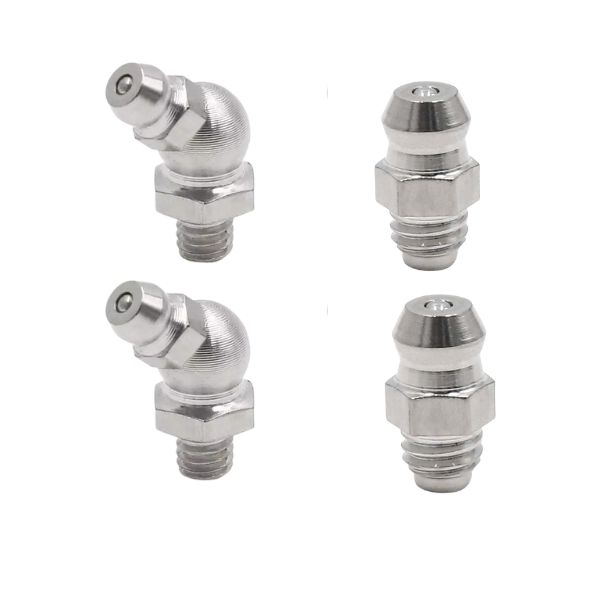
B. Common Materials and Construction
Material Selection for Durability
Grease fittings are typically made from durable metals designed to withstand high pressures and exposure to the harsh conditions they often face in machinery environments. The most common materials used for grease fittings include:
Steel: The most common material for grease fittings, steel offers a good balance of strength and cost-effectiveness. It is capable of handling high-pressure grease flow and is resistant to wear and tear.
Stainless Steel: For more demanding environments, such as those with high humidity, corrosive substances, or high temperatures, stainless steel grease fittings are used. These fittings are highly resistant to rust, corrosion, and wear, making them ideal for heavy-duty and harsh working conditions.
Brass: Brass is sometimes used for grease fittings in low-pressure applications. It is more resistant to corrosion than steel but may not be as durable or pressure-resistant for heavy machinery.
Zinc-Plated Steel: Zinc plating offers additional protection against corrosion, making it suitable for applications where grease fittings are exposed to moisture or outdoor environments.
Aluminum: In applications where weight is a concern, aluminum fittings may be used. However, they are generally not as durable as steel or stainless steel and are better suited for light-duty applications.
Material selection is essential to ensure that the grease fitting can handle the specific pressure requirements and environmental conditions where it will be used. The material must also be resistant to corrosion, wear, and impact damage to ensure a long lifespan.
Why Proper Fitting Choice Matters in Different Machinery Environments
Choosing the right grease fitting depends on several factors, including the type of machinery, the operating environment, and the required lubrication. Proper fitting selection is crucial because an incompatible or inappropriate fitting can lead to:
Premature Failure: Using a fitting that is not suited for the operating pressures or environment may cause it to break, leak, or become clogged, which would ultimately affect the entire lubrication system.
Corrosion: In corrosive environments (e.g., exposure to saltwater or harsh chemicals), using a fitting made from low-grade material such as standard steel might result in rusting, leakage, and premature failure.
Inadequate Lubrication: If a grease fitting is poorly designed or constructed, it might not allow proper grease flow, leading to inadequate lubrication and resulting in increased friction, wear, and potential damage to machinery.
Common Causes of Broken Grease Fittings
A. Over-tightening or Under-tightening
How Incorrect Torque Can Damage Fittings
Grease fittings require precise torque to ensure a secure and effective seal without causing damage. Over-tightening or under-tightening the fitting can cause serious issues:
Over-tightening: When a grease fitting is tightened beyond the recommended torque, it can lead to several problems. The excessive pressure can crack or deform the fitting, potentially making it difficult to attach the grease gun or causing it to break under pressure. Over-tightening can also distort the thread, which might lead to leaks or an inability to properly deliver grease.
Under-tightening: On the other hand, under-tightening a grease fitting can prevent it from creating a proper seal, resulting in grease leakage. Inadequate sealing also compromises the flow of lubrication to the system’s moving parts, which can cause friction and premature wear of components.
Signs of Improper Tightening and Risks Involved
Visible Cracks or Deformation: A fitting that has been over-tightened may show signs of cracks or deformities around the threads or the head.
Leakage: If a fitting is under-tightened, you may notice grease leaking around the fitting during lubrication.
Grease Infiltration Issues: A poorly tightened fitting may fail to deliver adequate lubrication to the necessary components, leading to increased friction and eventual component failure.
The risks involved include reduced equipment lifespan, frequent downtime, and potential damage to both the fitting and the surrounding machinery, leading to costly repairs.
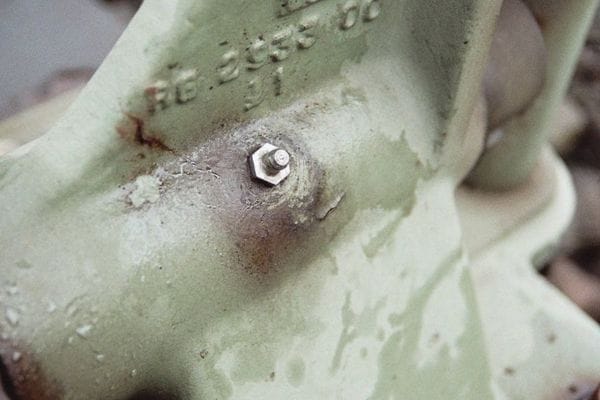
B. Corrosion and Wear
Environmental Factors Leading to Corrosion
Grease fittings are often exposed to harsh environmental conditions, which can lead to corrosion over time. Some of the most common environmental factors contributing to fitting degradation include:
Humidity: In moist or humid environments, moisture can accumulate on the fittings, leading to rust and corrosion, especially in metal fittings that are not corrosion-resistant. This weakens the fitting material and reduces its lifespan.
Chemical Exposure: Chemicals, including acids, salts, or industrial cleaners, can accelerate the corrosion process. These substances can break down the metal, causing pitting and weakening the fitting structure.
Extreme Temperatures: High heat can cause metal to expand, leading to cracks or deformities, while extreme cold can make fittings brittle and more prone to cracking or breaking when force is applied.
How Regular Wear Affects Grease Fittings Over Time
Over time, grease fittings can wear out due to the constant pressure applied by the grease gun, exposure to contaminants, and environmental elements. As a result:
The fitting’s sealing ability can degrade, leading to grease leakage or loss of pressure during lubrication.
The fitting can become clogged with dirt, grease residue, or other debris, obstructing the flow of lubricant.
Wear and tear from constant movement or vibration can loosen or damage the fitting, causing it to fail and require replacement.
Regular inspection and maintenance are essential to detect early signs of wear and prevent more serious problems from developing.
C. Impact Damage
External Factors
Grease fittings are small, often located in tight spaces, and are vulnerable to impact damage. Common sources of impact include:
Tools: Mishandling tools, such as using the wrong size grease gun nozzle or applying excessive force, can cause the fitting to break or become misaligned.
Equipment: In high-impact areas, such as machinery that experiences vibration or machinery that undergoes frequent starts and stops, grease fittings can be subjected to physical forces that lead to cracks or dislodgement.
Rough Handling: During maintenance or repairs, grease fittings may get damaged due to improper handling or accidental impact when moving parts of the system.
Effects of Sudden Pressure Spikes or System Surges
Pressure Surges: In some hydraulic systems, pressure surges can occur when there is a sudden increase in system pressure due to system irregularities or malfunctioning components. These pressure spikes can damage fittings by causing them to dislodge, crack, or become misaligned.
Impact from Vibration: In systems subject to constant vibration or jolts (e.g., on trucks, construction machinery), fittings can be subjected to repeated impacts that weaken the fitting’s structure over time, causing them to break or fail unexpectedly.
D. Inadequate Lubrication
Poor Grease Quality or Improper Grease Application
Grease fittings rely on the proper quality and quantity of grease to lubricate machinery components effectively. Using poor-quality grease or the wrong type of lubricant for the specific application can cause several issues:
Inadequate Lubrication: Using grease that is too thick or too thin can lead to poor lubrication, increasing friction and wear on moving parts.
Contaminated Grease: A grease that contains contaminants like dirt or moisture can clog the grease fitting or cause abrasive wear on components.
Improper Application: Fittings that are not adequately greased may suffer from early signs of wear and tear. Over-greasing, on the other hand, can cause the grease to seep out and lead to contamination or loss of pressure.
How Lack of Maintenance Accelerates Fitting Failure
Without regular maintenance, grease fittings can become clogged, worn, or damaged. Over time, this lack of attention can cause the fitting to fail. For instance:
Clogging: If a fitting isn’t regularly lubricated or maintained, debris can accumulate in the fitting, causing it to become clogged and preventing the proper flow of grease.
Lack of Pressure: As grease degrades or if the lubrication system is neglected, the amount of pressure required to deliver grease through the fitting decreases, leading to inadequate lubrication and increased friction.
Neglecting to maintain grease fittings often accelerates the wear process, causing the fitting to fail prematurely and potentially leading to more severe machinery issues.
E. Poor Installation or Faulty Fittings
Manufacturing Defects in Fittings
Not all broken grease fittings are the result of wear or external factors. Manufacturing defects can contribute to fitting failures. Common defects include:
Incorrect Threading: Fittings with improperly threaded parts may not fit securely, leading to leaks or failures in sealing.
Weak Material: Some fittings may be made with materials that aren’t up to standard or poorly processed, leading to a weakened structure that can break or deform easily.
Defective Seals: Fittings that lack proper seals or gaskets may leak grease, causing inadequate lubrication and eventual breakdown of the fitting.
Mistakes During the Initial Installation Process
During installation, several mistakes can compromise the functionality of grease fittings, such as:
Misalignment: If a grease fitting is not aligned properly with the lubrication point, it may not provide adequate grease flow, leading to lubrication failure.
Sealing Issues: If the fitting’s seal isn’t properly secured, it may leak grease or fail to maintain adequate pressure, causing premature failure of both the fitting and the surrounding components.
Incorrect Size or Type: Installing the wrong size or type of fitting for a specific application can cause it to malfunction, especially if the fitting doesn’t fit properly with the system’s lubrication channels or if it is incompatible with the type of grease used.
Preventative Measures for Avoiding Broken Grease Fittings
A. Correct Installation Practices
Ensuring Proper Fitting Selection for Specific Equipment
The first step in preventing broken grease fittings is ensuring the right type of fitting is selected for each specific application. Different machinery and operating environments have varying lubrication needs, which dictate the fitting type and material:
Type Selection: Choose fittings based on the operational needs of the equipment. For instance, use angled or rotary fittings for hard-to-reach areas, button-head fittings in tight spaces, and straight fittings where they can be easily accessed.
Material Selection: Depending on the environment, you should opt for corrosion-resistant materials like stainless steel or zinc-plated fittings if the equipment is exposed to moisture, chemicals, or extreme temperatures.
Ensuring that fittings are designed to handle the expected pressure and environmental conditions helps reduce the risk of fitting failure.
Step-by-Step Guide on Installing Grease Fittings Correctly
Check Compatibility: Verify that the selected grease fitting matches the equipment and is compatible with the intended grease type.
Clean the Installation Area: Ensure the area where the fitting will be installed is clean and free of debris to prevent contamination that could affect the seal.
Align the Fitting: Ensure the fitting is properly aligned with the lubrication point. This ensures that grease is delivered efficiently without excess force.
Install the Fitting: Thread the fitting into place carefully by hand to avoid cross-threading. Use the appropriate tool to tighten it securely.
Torque Application: Apply the correct torque to avoid over-tightening or under-tightening, both of which can lead to fitting damage or failure.
Inspect for Leaks: Once installed, check the fitting for leaks to ensure that it is sealed correctly.
By following proper installation practices, you can significantly extend the life of the grease fitting and ensure that the lubrication system functions properly.
B. Regular Inspection and Maintenance
Developing a Maintenance Schedule for Checking Grease Fittings
Regular inspection is critical to identifying issues early and preventing broken grease fittings. Develop a comprehensive maintenance schedule that includes:
Routine Inspections: Check grease fittings at least every few weeks or months depending on the machine’s usage. Look for signs of damage, wear, corrosion, or leakage.
Lubrication Monitoring: Ensure that grease is applied at regular intervals. If grease fittings are clogged, damaged, or leaking, address them immediately.
Monitoring Pressure: Ensure that the system’s pressure is within the manufacturer’s recommended levels to avoid stress on the fittings.
Using Diagnostic Tools to Monitor Fitting Conditions
In addition to visual inspection, diagnostic tools can be used to assess the condition of grease fittings:
Grease Pressure Testers: These tools can help determine if the grease is being delivered properly through the fitting and if there are any blockages or pressure anomalies.
Infrared Thermometers: Use infrared thermometers to monitor temperature changes around fittings, as unusual temperature rises could indicate problems with lubrication or a failing fitting.
Ultrasonic Testing: For advanced diagnostics, ultrasonic sensors can detect signs of wear, corrosion, or vibration that might suggest a failing grease fitting.
By regularly inspecting and maintaining grease fittings, you can catch minor issues before they become major problems, reducing downtime and repair costs.
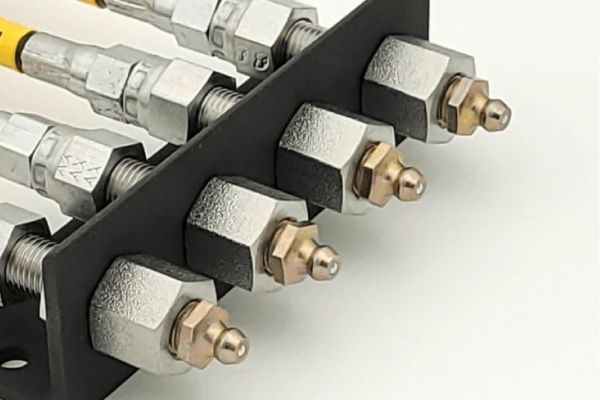
C. Use of Quality Materials
Choosing Corrosion-Resistant and Durable Materials for Fittings
The material used for grease fittings plays a significant role in their durability and resistance to environmental factors. Selecting the appropriate material for fittings can prevent premature failure caused by corrosion, wear, and stress:
Stainless Steel: Ideal for harsh environments, stainless steel is resistant to corrosion from chemicals, moisture, and high temperatures, making it a top choice for heavy-duty machinery.
Zinc-Plated Steel: Provides additional corrosion resistance for environments that may experience rust, but it’s still affordable and effective for less demanding conditions.
Brass: While softer than steel, brass is used in applications where low pressure and light-duty use are required.
Durable Seals and Gaskets: Ensure that fittings come with high-quality seals or gaskets that can withstand heat, pressure, and contaminants.
The Role of High-Quality Grease in Prolonging Fitting Life
Using high-quality grease is just as important as selecting durable fittings. High-quality grease provides better lubrication, reduces friction more effectively, and prevents the buildup of contaminants. Choose grease specifically formulated for the equipment and operating conditions:
Consistency: Choose grease with the correct viscosity for the application. Grease that is too thick may cause clogging, while grease that is too thin may leak or fail to provide proper lubrication.
Additives: High-quality greases contain additives that help protect against oxidation, corrosion, and wear, which extends the life of the grease fitting and the components being lubricated.
D. Proper Torque Application
How to Use Torque Wrenches and Avoid Over-tightening
Torque application is critical when installing grease fittings, as both over-tightening and under-tightening can lead to issues. To avoid damage:
Use a Torque Wrench: Always use a torque wrench to apply the specified torque when installing a grease fitting. This ensures that the fitting is neither too tight nor too loose.
Avoid Over-tightening: Over-tightening a fitting can distort or crack the fitting, causing leaks, excessive stress on components, and possible fitting failure. The torque should be applied according to the manufacturer’s specifications, typically between 10 and 30 foot-pounds.
Proper Re-tightening: For fittings that may need periodic re-tightening, ensure that the torque specification is followed carefully to avoid damaging the fitting or surrounding parts.
Recommended Torque Specifications for Different Fitting Types
Torque specifications vary depending on the fitting type and size. It is essential to follow manufacturer guidelines for each type of fitting to avoid common issues:
Standard Grease Fittings: Typically, these require around 10–20 ft-lbs of torque.
Angled or Button Head Fittings: These fittings might require slightly less torque due to their design but should be tightened to the specifications provided by the manufacturer.
Heavy-Duty Fittings: Larger, heavy-duty fittings for industrial or agricultural machinery may require up to 30 ft-lbs of torque.
Following the correct torque specifications reduces the likelihood of damage and ensures that the fittings maintain their seal and pressure.
E. Environmental Considerations
Preventing Exposure to Harmful Elements Like Water, Salt, and Chemicals
Exposure to environmental factors such as water, salt, chemicals, or extreme temperatures can accelerate the breakdown of grease fittings. To prevent environmental damage:
Protect Fittings from Moisture: Ensure that grease fittings are kept dry and protected from excessive moisture or standing water, which can cause corrosion.
Use Protective Covers or Shields: Install protective covers or shields to shield grease fittings from external elements like dust, dirt, salt, and chemicals. This is particularly important for machinery used in marine environments or outdoors.
Regularly Clean Fittings: Clean grease fittings periodically to remove any accumulated debris, dirt, or grease buildup that might attract moisture or contaminants.
Implementing Protective Covers or Shields
Protective covers or boots can be used to shield grease fittings from damage in harsh environments. These covers protect the fitting from direct exposure to the elements, reducing the risk of corrosion, wear, and contamination. Use covers that are durable and specifically designed for grease fittings to ensure they remain effective over time.
Conclusion
We encourage you to prioritize grease fitting maintenance in your routine equipment care. Ensure that your fittings are in top condition, replace any worn-out or damaged parts, and don’t hesitate to reach out to professionals for assistance when needed.
FAQ
What are grease fittings and why are they important?
Grease fittings, also known as grease nipples, are components used to inject lubricants into machinery to reduce friction and wear. They are crucial for maintaining equipment, ensuring smooth operation, and extending the lifespan of moving parts.
What causes grease fittings to break?
Common causes include over-tightening or under-tightening, corrosion from environmental factors, impact damage, inadequate lubrication, and poor installation.
How can I prevent my grease fittings from breaking?
Preventative measures include using the correct fittings, applying the proper torque, regular inspections, using quality materials, and protecting fittings from environmental damage.
How often should I inspect grease fittings?
It is recommended to inspect grease fittings regularly, at least once a month or every few weeks depending on usage and environmental conditions. Routine checks can catch issues early.
What should I do if a grease fitting is damaged or leaking?
If a grease fitting is damaged or leaking, replace it immediately. Continuing to use a damaged fitting can lead to equipment failure or inefficiency in the lubrication system.
Can I install grease fittings myself?
Yes, as long as the proper installation procedures are followed. Ensure the fitting is aligned, torqued correctly, and compatible with the machinery. If you’re unsure, consulting a professional is a good idea.