In hydraulic systems, grease fittings are typically used to keep pistons, valves, and joints properly lubricated, reducing friction and the risk of overheating. The grease helps protect the system’s components from corrosion and wear, ensuring a longer lifespan and maintaining the overall efficiency of the system.
What is a Grease Fitting?
A grease fitting, also known as a Zerk fitting or grease nipple, is a small but vital component in mechanical and hydraulic systems that allows for the injection of lubricants into machinery. These fittings are essential for ensuring that moving parts, such as bearings, joints, and other mechanical elements, are properly lubricated to reduce friction, wear, and corrosion. They act as a conduit for grease, making it easier to maintain the lubrication of hard-to-reach areas, ultimately extending the lifespan and efficiency of equipment.
Types of Grease Fittings
- Standard Grease Fittings: These are the most common type and are typically used in general machinery, automotive applications, and light-duty systems. They are simple, reliable, and often threaded to fit the lubrication points on machines.
- Heavy-Duty Grease Fittings: Designed for use in industrial, construction, or agricultural machinery, heavy-duty fittings are built to withstand more demanding environments. They are often made from tougher materials to handle high-pressure conditions and the presence of harsh contaminants like dirt or moisture.
- Quick-Connect Grease Fittings: These fittings feature a design that allows for easy and fast connection to a grease gun, facilitating quick lubrication without the need for threading or screwing in the fitting. This type is particularly useful in applications where time is critical, such as in high-production environments.
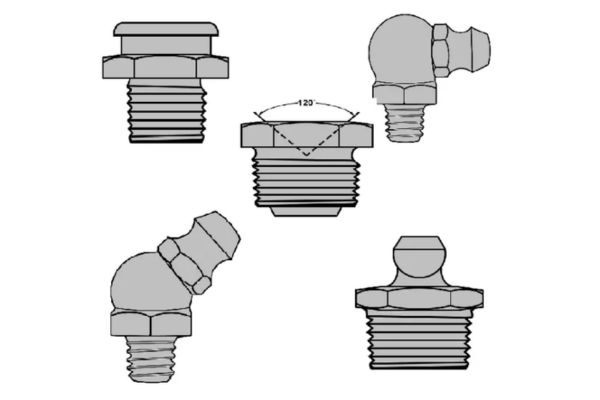
Key Components of a Grease Fitting
A grease fitting typically consists of three main components:
- Body: The main structure of the grease fitting, usually made of steel or brass, which holds the fitting in place. The body is threaded to allow the fitting to be securely attached to the machine or equipment.
- Fitting: The nipple-like part that accepts the grease gun’s nozzle. It allows the grease to be injected directly into the component it’s lubricating. The fitting can be ball-shaped, making it easy for a grease gun to connect and deliver lubrication.
- Grease Port: The small opening where the grease is injected into the system. Over time, this port may become clogged with hardened grease or debris, which is why regular maintenance is crucial.
Common Applications
Grease fittings are widely used across many industries, ensuring the smooth operation of a variety of systems:
- Automotive: In vehicles, grease fittings are used to lubricate suspension parts, steering components, and wheel bearings. Regular maintenance of these fittings helps to reduce wear and avoid expensive repairs.
- Industrial Machinery: Heavy machines, such as presses, conveyors, and pumps, rely on grease fittings to maintain smooth operation and avoid damage due to friction. These fittings are used in bearings, gears, and other moving parts.
- Hydraulic Systems: In hydraulic systems, grease fittings are employed in valves, cylinders, and piston joints to ensure that the hydraulic components stay properly lubricated and operate efficiently, especially in high-pressure environments.
Why Grease Fittings Need to Be Replaced
Grease fittings, though small, are critical to maintaining the smooth operation of hydraulic systems and machinery. However, like all mechanical components, they can wear out over time due to a variety of factors. The continuous exposure to grease, environmental stressors, and the demands of the equipment can take a toll on these fittings.
Wear and Tear
Grease fittings are regularly exposed to high-pressure grease injection, particularly in systems that require frequent lubrication. Over time, this constant exposure can cause wear on the internal components of the fitting, including the ball valve inside the fitting that controls the flow of grease. The internal ball valve can wear down, losing its ability to form a proper seal and allowing grease to leak out.
Moreover, the continuous pressure and repeated lubrication cycles can also lead to physical degradation of the fitting body. As the fitting becomes more worn, the threads may become damaged, leading to a loss of integrity when installing a new fitting or grease gun. This wear can eventually make the fitting less effective at delivering grease into the system, which can result in insufficient lubrication and cause friction, overheating, and even catastrophic failure in more severe cases.
Blockage or Clogging
One of the most common issues that necessitates the replacement of grease fittings is blockage or clogging. Over time, grease can harden or accumulate inside the fitting or the surrounding piping, especially if the lubrication is contaminated with dirt, debris, or moisture. The grease port can become obstructed, making it difficult or impossible to properly inject lubricant into the system.
When a grease fitting becomes blocked, lubrication efficiency suffers. Without adequate grease flow, moving parts in machinery and hydraulic systems can experience increased friction, leading to excessive wear, overheating, and eventual failure of critical components. Furthermore, the grease that does manage to make it through the fitting may not reach all the necessary lubrication points, leaving certain areas under-lubricated and vulnerable to damage. In such cases, replacement of the grease fitting is the only way to restore full lubrication and protect the equipment.
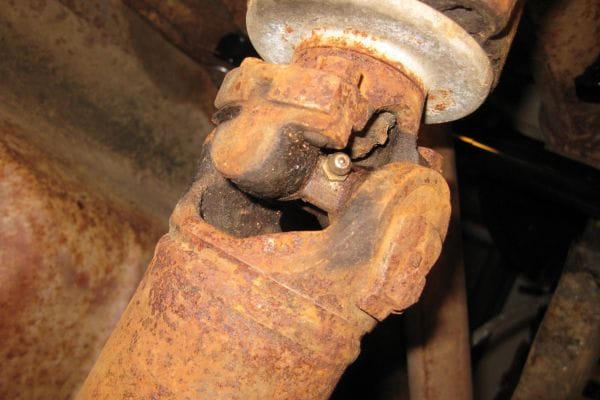
Corrosion
Grease fittings are often exposed to harsh environmental conditions, particularly in outdoor or industrial environments where moisture, dust, salt, and other corrosive substances are prevalent. When exposed to moisture, particularly in humid or wet environments, the steel body of the fitting can begin to corrode, weakening the structure and causing it to fail. Saltwater, commonly found in marine or coastal environments, can accelerate corrosion, as salt acts as a catalyst for the breakdown of metals.
Corrosion can have several negative effects on grease fittings:
- The fitting may become difficult to connect with a grease gun, leading to improper lubrication.
- The internal mechanism of the fitting, including the ball valve, can become stuck, rendering it unusable.
- Rust and other corrosion products can enter the lubrication system, contaminating the grease and potentially causing more damage to sensitive components inside the system.
Once corrosion sets in, it is often more cost-effective to replace the fitting entirely rather than attempting repairs. Preventative maintenance, such as the use of corrosion-resistant fittings or protective covers, can help mitigate these issues, but eventually, all fittings will need to be replaced due to wear from environmental exposure.
Damage to Seals and Threads
Frequent use of grease fittings can also cause damage to their seals and threads. The seals inside a grease fitting ensure that grease is injected properly and that there is no leakage. Over time, these seals can degrade due to repeated grease injections and the mechanical forces applied during installation and use. As seals wear down, they may no longer provide a secure seal, leading to grease leaks. This not only reduces lubrication efficiency but can also cause contamination of the surrounding environment or machinery.
How Often Should Grease Fittings Be Replaced?
Manufacturer Recommendations and General Guidelines
Most manufacturers of machinery, hydraulic systems, and grease fittings will provide specific recommendations regarding the lifespan of grease fittings. These guidelines typically outline the expected maintenance intervals based on the type of machinery and the operating conditions under which it will be used. For example, equipment used in heavy-duty applications, such as mining or construction, may require more frequent grease fitting replacements than equipment used in light-duty or low-intensity applications.
Manufacturer recommendations typically include:
- Routine inspection schedules: How often to check grease fittings for wear, damage, or blockage.
- Replacement intervals: A suggested timeframe (e.g., every 12–18 months) for replacing grease fittings, depending on system usage and type.
- Lubricant recommendations: The type of grease that should be used to prevent clogging, corrosion, or degradation of the fittings.
However, these recommendations are just a starting point. It’s important to assess your system’s actual operating conditions and use them to refine your maintenance schedule.
Factors Affecting Replacement Frequency
Several factors can influence how often grease fittings need to be replaced, including:
Operating Conditions (Temperature, Pressure, Exposure to Contaminants)
Operating conditions play a crucial role in the longevity of grease fittings. Extreme temperature variations, both high and low, can degrade the materials of the fitting and its seals, leading to premature failure. High-pressure systems put added strain on grease fittings, causing more rapid wear due to the constant stress and volume of grease being pumped through the fitting.
Additionally, environments with high levels of contaminants—such as dirt, moisture, salt, or chemicals—accelerate the wear and corrosion of grease fittings. In these harsh conditions, fittings are more likely to degrade, clog, or fail. For instance:
- High-pressure systems require more durable fittings and might necessitate more frequent replacement.
- Outdoor or marine environments where fittings are exposed to saltwater or humidity may require more frequent inspection and replacement due to corrosion.
Frequency and Type of Grease Used
The type of grease used and how frequently the lubrication is applied also impact the replacement schedule for grease fittings. If high-quality, non-contaminated grease is used regularly, fittings will likely last longer. However, low-quality grease, or grease mixed with dirt or debris, can clog fittings or cause them to corrode more quickly.
Systems that require frequent lubrication (e.g., daily, weekly) are subject to higher wear, requiring grease fittings to be replaced more often. On the other hand, equipment that receives less frequent lubrication may have fittings that last longer, provided they are not exposed to extreme conditions.
Equipment Type and Usage Intensity (Light, Medium, Heavy-Duty)
The type of equipment and the intensity of its use significantly influence the frequency of grease fitting replacement. Equipment used in light-duty applications, such as small agricultural machines or light trucks, may only need grease fitting replacement every few years.
For heavy-duty applications, such as mining equipment, construction machinery, or large industrial machines, grease fittings are subjected to much higher stress and more extreme conditions. These applications often require more frequent replacement to maintain optimal performance. In these cases, fittings should be inspected and replaced based on specific manufacturer guidelines and observed wear patterns.
Signs That Indicate Grease Fitting Replacement
Even with a set replacement schedule, it’s important to recognize the signs that a grease fitting may need to be replaced before its scheduled time. Below are the key indicators that grease fittings are no longer functioning optimally:
Leaking or Oozing Grease
One of the first and most noticeable signs that a grease fitting needs to be replaced is grease leakage. If grease begins to ooze around the fitting, it suggests that the seal is compromised, or the fitting itself is cracked or worn. Leakage can lead to grease loss, which means your equipment isn’t being properly lubricated, and can also create a mess, attracting dirt and contaminants.
If you notice that grease is consistently leaking from a fitting during routine inspections or after lubrication, it is time to replace it.
Difficulty in Grease Application
If you experience difficulty when trying to grease the fitting—such as resistance while applying grease or the inability to inject grease properly—it may be a sign that the fitting is clogged or the internal mechanism has become damaged. This could be caused by a blockage or corrosion inside the fitting that prevents grease from flowing smoothly.
Difficulties in grease application also indicate that the lubrication points are not being properly serviced, which can lead to increased friction and accelerated wear in the equipment.
Visible Cracks or Damage
Inspect grease fittings regularly for visible signs of physical damage. Cracks, deformation, or other damage to the fitting body, threads, or nozzle are clear indicators that the fitting needs replacement. Cracks may result from excessive wear, corrosion, or impact, and they compromise the fitting’s integrity, leading to leaks or even complete failure.
It’s especially important to replace any fitting that shows damage that could lead to a broken connection or unsafe operation of your machinery.
Increased Friction or Equipment Malfunction
If equipment is operating with insufficient lubrication, the friction between moving parts increases, which can lead to overheating, premature wear, and eventual breakdowns. This is often a result of a failing or blocked grease fitting that isn’t delivering adequate lubrication. When friction increases or if you begin to notice equipment malfunctions, it’s time to check the grease fittings. Regular replacement and maintenance can prevent such issues from escalating into more serious, costly problems.
The Grease Fitting Replacement Process
Replacing grease fittings is an essential part of hydraulic and mechanical system maintenance, ensuring that the equipment continues to operate efficiently and reliably. The process involves removing worn or damaged fittings and installing new ones, along with proper lubrication to ensure smooth operation.
Step-by-Step Guide to Replacement
Tools and Equipment Needed
Before you begin the replacement process, make sure you have the necessary tools and equipment. Here’s a list of items you will need:
- Grease Fitting Tool (Zerk Fitting Tool): This tool is specifically designed for removing and installing grease fittings. It helps grip and remove the old fitting without damaging the surrounding area.
- Wrenches: Adjustable wrenches or a socket wrench may be required to remove or install the fitting if it’s tightly secured.
- Clean Cloth or Rag: To clean the area around the fitting and remove excess grease or debris.
- Replacement Grease Fitting: Ensure you have the correct size and type of grease fitting for your equipment (standard, heavy-duty, quick-connect, etc.).
- Grease Gun: To apply the grease after the new fitting is installed.
- Thread Sealing Compound (optional): Some installations may require thread sealant to prevent leaks, though many grease fittings have built-in seals.
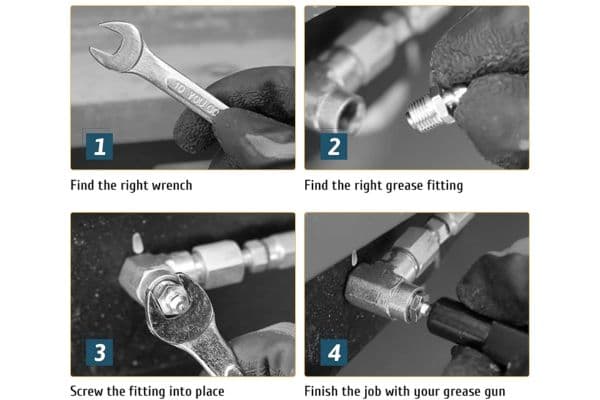
Removing the Old Fitting
The first step in replacing a grease fitting is removing the old, worn, or damaged fitting. This step requires care to avoid damaging the surrounding equipment and to prevent contamination of the system.
- Precautionary Measures: Before beginning, always shut off the equipment and relieve any system pressure. If the equipment is under pressure or if hydraulic systems are involved, failure to do so could lead to grease leakage or potential injury.
- Clean the Area: Use a clean cloth to wipe away any grease or dirt around the fitting. This is crucial to avoid contaminants entering the system when the fitting is removed.
- Loosen the Old Fitting: Use the grease fitting tool or a wrench to loosen and remove the old fitting. Be sure to rotate the fitting counterclockwise to unscrew it. If the fitting is stuck or hard to remove, apply a small amount of penetrating oil to loosen the threads. Allow it to sit for a few minutes before attempting removal again.
- Avoid Contamination: During this process, ensure that no dirt, debris, or moisture gets inside the open hole. Contamination could lead to blockages or damage to the lubrication system. Cover the hole with a clean cloth or tape to protect it temporarily until the new fitting is installed.
Installing the New Fitting
Once the old fitting is removed, it’s time to install the new one. Proper installation is critical to ensure a secure connection and optimal performance of the new grease fitting.
- Check the Fitting Type: Make sure that the replacement fitting matches the type and size of the original fitting (e.g., standard, heavy-duty, or quick-connect). Mismatched fittings could result in improper lubrication or even damage to the system.
- Insert the New Fitting: Thread the new fitting into the hole carefully by hand, ensuring it’s aligned properly. You can use a small amount of thread sealant on the threads to prevent any potential leakage, though many modern grease fittings come pre-sealed.
- Tighten the Fitting: Once the fitting is hand-tight, use a wrench or grease fitting tool to tighten it further. Be sure to tighten it to the manufacturer’s recommended torque specifications. Over-tightening the fitting can damage the threads or the fitting itself, while under-tightening may lead to leaks or a loose connection.
Greasing the Fitting Properly
After the new fitting is securely installed, the next step is to grease it properly to ensure lubrication flows smoothly into the system.
- Connect the Grease Gun: Attach the nozzle of the grease gun to the grease fitting. Make sure the connection is firm to avoid leaks when applying the grease.
- Apply Grease: Pump grease into the fitting until you see it begin to emerge from the component it’s meant to lubricate. This ensures that grease is flowing through the fitting and is reaching the intended areas. You may need to pump several times to fully lubricate the part, depending on the size of the system.
- Check for Leaks: After greasing, check around the fitting for any signs of leaks. If the fitting is leaking grease, it may not have been installed properly or there could be an issue with the fitting itself. If leakage occurs, remove the fitting, check for debris or damage, and reinstall.
Tips for Proper Maintenance After Installation
To ensure the grease fitting continues to perform efficiently, it’s important to follow some best practices for post-installation care:
- Cleanliness: Always keep grease fittings and surrounding areas clean to prevent dirt and contaminants from entering the lubrication system. Regularly wipe off excess grease to prevent buildup.
- Correct Torque: Avoid over-tightening or under-tightening the fitting. Use a torque wrench to ensure the correct torque specifications are followed. Over-tightening can damage the fitting, while under-tightening may lead to leakage or loosening over time.
- Avoid Over-Greasing: Over-greasing can lead to grease leakage or damage to seals. Apply grease only as necessary to maintain proper lubrication, following the equipment manufacturer’s recommended grease volumes and intervals.
Common Mistakes to Avoid During Replacement
While replacing grease fittings is a straightforward process, there are a few common mistakes that should be avoided to ensure the job is done correctly:
- Using Incorrect Fittings: Always double-check the type and size of the grease fitting to make sure it’s the right match for your equipment. Using an incorrect fitting can lead to poor lubrication and possible damage.
- Not Cleaning the Area: Failing to clean the surrounding area before removing the old fitting can introduce contaminants into the system, resulting in blockages or damage.
- Over-Tightening the Fitting: It’s tempting to tighten the fitting as much as possible to ensure a good seal, but over-tightening can damage the threads, break the fitting, or cause undue stress on the equipment. Follow manufacturer specifications for torque settings.
- Ignoring Leaks: If you notice grease leaks after installation, don’t ignore them. Leaks are a sign that the fitting was not installed correctly, or there is a defect in the fitting. Immediate attention is necessary to prevent further damage.
Conclusion
Regular inspections, proper lubrication practices, and a proactive approach to replacement will not only prevent costly issues but also ensure that your equipment performs at its best for years to come.
If you need any grease fittings, just contact Topa!
FAQ
What is a grease fitting?
A grease fitting, also known as a Zerk fitting or grease nipple, is a small metal fitting used to deliver lubricating grease into machinery parts, such as bearings and joints, to reduce friction and wear.
How do I know when to replace a grease fitting?
You should replace a grease fitting if you notice signs such as leaking grease, difficulty applying grease, visible cracks or damage, or increased friction in the equipment indicating poor lubrication.
How often should grease fittings be replaced?
The replacement frequency depends on operating conditions, equipment type, and grease usage. On average, grease fittings should be inspected every 6–12 months, with replacement recommended when damage or wear is noticed.
Can I replace a grease fitting myself?
Yes, replacing a grease fitting is a simple process that requires basic tools such as a grease fitting tool, wrenches, and a new fitting. However, make sure to follow the correct installation steps and torque specifications to ensure a proper seal.
What happens if a grease fitting is not replaced on time?
If a grease fitting is not replaced when needed, it can lead to improper lubrication, increased friction, overheating, and eventual equipment failure, which can result in costly downtime and repairs.
Are there different types of grease fittings?
Yes, there are several types of grease fittings, including standard, heavy-duty, and quick-connect fittings. The choice depends on the application, equipment type, and operating conditions.