Grease fitting is a small component in machinery where grease is injected to lubricate parts and reduce friction. When these fittings become clogged, grease cannot flow properly, leading to excessive wear, overheating, and potential failure of machinery.
Common Causes of Clogged Grease Fittings
Grease fittings are vital components in maintaining the smooth operation of machinery by ensuring that moving parts are properly lubricated. However, when these fittings become clogged, it can lead to severe performance issues and even equipment failure. There are several common causes of clogged grease fittings, each of which affects the flow of grease and ultimately impacts machine efficiency.
Grease Quality and Viscosity: Why It Matters
The quality and viscosity of the grease you use play a critical role in ensuring that your machinery stays properly lubricated. Grease with the wrong viscosity can cause flow issues in the system, while low-quality grease can degrade over time. When grease thickens or hardens, it can block grease fittings, preventing grease from flowing to critical parts.
For optimal performance, always ensure that the grease used matches the manufacturer’s specifications for viscosity. High-quality, compatible grease can prevent clogs and ensure that machinery operates smoothly and efficiently.
Environmental Factors
External environmental conditions have a significant impact on grease quality and its ability to flow through fittings. Dust, dirt, moisture, and extreme temperatures can degrade grease, causing it to thicken or harden, ultimately leading to blockages.
Dust and Dirt: These contaminants can enter the grease fitting if seals are damaged or improperly sealed, leading to contamination within the system. This can result in the grease becoming thick or gritty, obstructing the flow.
Moisture: Water ingress into the grease system can break down grease, causing it to become watery or emulsified, which reduces its effectiveness and leads to clogging.
Extreme Temperatures: Very high or low temperatures can change the consistency of grease. In cold conditions, grease can become too thick to flow properly, while high temperatures can cause it to break down faster and form sludge.
Regular maintenance and using grease that is formulated to withstand specific environmental conditions can help mitigate these issues.
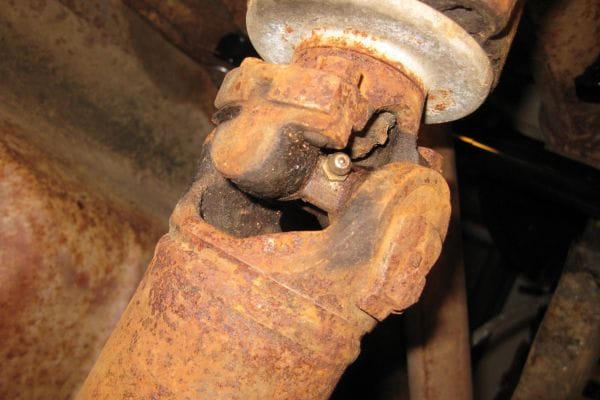
Over-lubrication and Its Impact on Grease Flow
Over-lubricating machinery can be just as damaging as under-lubricating it. When too much grease is applied, it leads to over-pressurization in the lubrication system. Excess grease can force contaminants into the grease fitting, leading to blockages. Additionally, over-lubrication may cause the grease to harden or become difficult to pump through the system, effectively obstructing the flow.
Furthermore, over-pressurization can damage equipment seals, leading to leaks and further contamination of the lubrication system. To prevent over-lubrication, always follow manufacturer recommendations for grease amounts and reapplication frequency.
Poor Lubrication Practices: The Hidden Culprits
Incorrect lubrication practices are often overlooked but are major contributors to clogged grease fittings. These practices include:
Using the Wrong Grease: Using grease that isn’t compatible with the machinery or environment can cause blockages. For example, grease that is too thick may clog the fitting, while grease that’s too thin may fail to provide sufficient lubrication.
Inconsistent Greasing Schedule: Failing to grease machinery on a regular basis, or over-greasing, can both lead to clogged fittings. Without a consistent greasing routine, grease may harden, become contaminated, or not reach the necessary parts, leading to blockages.
Establishing a clear lubrication protocol based on manufacturer guidelines can go a long way in preventing these issues.
Inadequate Maintenance: Failing to Inspect and Clean Grease Fittings
Regular inspection and cleaning are essential for preventing clogs. Over time, dirt, hardened grease, and other debris can accumulate around the grease fitting, blocking grease flow. Without proper maintenance, grease fittings can become difficult to service, resulting in inadequate lubrication and increased wear on equipment.
Make it a habit to inspect grease fittings at regular intervals, ensuring that the fittings are clean and free of debris. Cleaning fittings before lubrication ensures that grease flows freely to where it is needed.
External Contaminants: Dust, Dirt, and Water in Your Grease System
External contaminants are one of the most common causes of clogged grease fittings. Dust, dirt, and water can easily enter the grease system if the fitting seals are compromised or if the system is improperly sealed.
Dust and Dirt: If the environment is dusty or gritty, dirt can enter the grease fitting and mix with the grease, causing it to thicken or form a sludge. This can clog the fitting and reduce lubrication efficiency.
Water: Water ingress is another major concern. Even a small amount of water can cause grease to degrade, making it less effective and prone to clogging.
Regularly inspect seals, replace damaged fittings, and use protective covers to prevent contaminants from entering the system.
Aging and Worn-Out Fittings: Time for a Replacement?
Over time, grease fittings can become worn or damaged, especially if they are frequently exposed to harsh operating conditions. As fittings age, they may corrode, rust, or develop cracks, compromising their ability to properly accept grease.
Corrosion: Corroded fittings can block grease flow and reduce the effectiveness of lubrication, leading to increased wear on equipment.
Seal Failure: Fittings that are no longer sealed properly can allow contaminants like dirt and water into the grease system, leading to clogs and lubrication issues.
If a grease fitting is damaged or corroded beyond repair, it’s crucial to replace it promptly to ensure that grease can flow freely and continue to lubricate the machinery.
Signs Your Grease Fitting is Clogged
Grease fittings are essential for maintaining smooth operation in machinery by ensuring that moving parts remain properly lubricated. When these fittings become clogged, they prevent grease from reaching critical components, leading to various operational issues. Here are some key signs that indicate a clogged hydraulic grease fitting:
Difficulty Greasing: When the Grease Gun Won’t Work
One of the most obvious signs of a clogged hydraulic grease fitting is difficulty when trying to grease the component. If the grease gun doesn’t dispense grease properly or you encounter resistance when applying grease, it likely indicates a blockage or restriction in the fitting. This could be due to hardened grease, debris, or other obstructions inside the fitting.
What to Check: Inspect the grease gun and nozzle to ensure they’re in good condition and that the fitting is aligned properly. If the grease gun is functioning correctly and the fitting is still not accepting grease, it’s time to investigate further for blockages.
Unusual Noises or Vibrations in Your Equipment
A clogged hydraulic grease fitting can prevent proper lubrication of moving parts, leading to increased friction. When parts rub against each other without sufficient grease, they can produce unusual noises such as squeaks, grinding sounds, or vibrations. These noises often signal that the components are under stress, which can lead to accelerated wear and eventual failure.
What to Listen For: Pay attention to any changes in sound or vibrations coming from the machinery. Unusual sounds are a clear indication that the lubrication system is not functioning as it should, often due to a clogged fitting.
Grease Leakage Around the Fitting
If a grease fitting is clogged, it can cause excessive pressure to build up within the lubrication system. This pressure buildup can force grease to leak out from around the fitting, resulting in grease spills or visible leakage. A properly functioning fitting should accept the grease without forcing it out.
What to Look For: Inspect the area around the grease fitting for signs of grease leakage. If you notice grease oozing out from the fitting, it’s a sign that the fitting is not properly accepting grease, likely due to a blockage or damage.
Visible Blockages or Residue Around the Fitting
Clogged hydraulic grease fittings may exhibit visible signs of buildup. If you notice hardened grease, dirt, or residue accumulating around the fitting, it’s an indication that the grease flow has been obstructed. This is often caused by old or contaminated grease, dirt ingress, or lack of regular maintenance.
What to Check: Clean the grease fitting to inspect for hardened or contaminated grease. If you find that grease is not flowing freely, or if you see visible obstructions, it’s time to clear the fitting and restore proper lubrication.
Reduced Equipment Performance and Increased Wear
When grease fittings are clogged, machinery often operates with insufficient lubrication, leading to increased friction between moving parts. This can result in reduced equipment performance, slower operation, or even complete breakdowns due to excessive wear. Over time, a clogged hydraulic grease fitting will cause parts to wear out faster, leading to more frequent repairs and costly downtime.
What to Observe: Monitor the overall performance of the equipment. If the machinery shows signs of reduced speed, efficiency, or responsiveness, combined with higher-than-usual temperatures, it may be due to inadequate lubrication from a clogged hydraulic grease fitting. This can also lead to visible wear on bearings, joints, or other moving parts.
Preventing Clogged Grease Fittings
Clogged hydraulic grease fittings are a common problem that can significantly affect the performance and longevity of machinery. Preventing clogs before they occur requires a proactive approach to maintenance, proper lubrication practices, and selecting the right components for the job.
Establishing a Regular Grease Fitting Maintenance Routine
A consistent maintenance routine is the foundation for preventing clogged hydraulic grease fittings. By making inspection and cleaning a regular part of your equipment maintenance schedule, you ensure that grease fittings remain free from debris and function properly. A maintenance routine can include:
Inspecting fittings for visible damage, cracks, or signs of wear.
Cleaning fittings before lubrication to remove any accumulated dirt or hardened grease.
Checking for proper grease flow to ensure that grease is being distributed evenly and without resistance.
By staying on top of these tasks, you can catch potential issues early and prevent more severe blockages or wear.
Selecting the Right Grease for Your Machinery
Not all grease is created equal, and using the wrong type can contribute to clogging issues. The grease you choose should be carefully selected based on the specific requirements of your machinery. Key factors to consider include:
Viscosity: Choose grease with the correct thickness to match your machine’s operating conditions. Grease that is too thick can clog fittings, while grease that is too thin may not provide sufficient lubrication.
Temperature Resistance: Consider the operating temperature range of your machinery. Grease that isn’t temperature-resistant enough may degrade or thicken over time, causing blockages.
Material Compatibility: Ensure the grease is compatible with the materials used in your equipment, such as seals, bearings, and metal components. Incompatible grease can cause damage to parts or lead to clogging.
Using the correct grease helps ensure consistent lubrication and reduces the risk of clogging due to grease degradation.
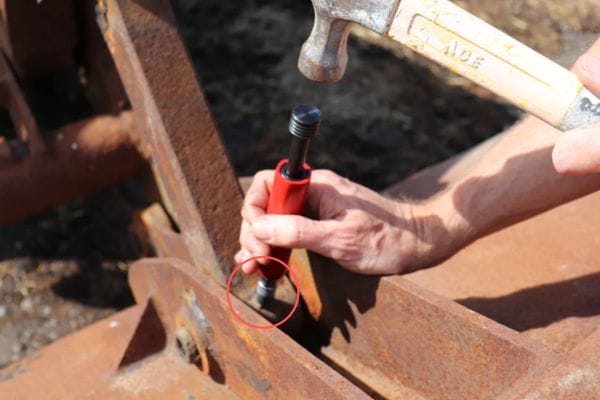
Importance of Grease Fitting Inspection and Cleaning
Routine inspection and cleaning of grease fittings are crucial steps in preventing clogs. Regularly checking fittings for any signs of blockage, damage, or contamination will help you catch issues before they escalate. Here’s why it’s important:
Signs of Damage: Look for cracks or worn-out fittings that may allow contaminants to enter the grease system.
Preventing Contamination: Clean grease fittings before applying new grease to remove any old or contaminated grease, dirt, or debris.
Ensuring Proper Flow: Inspect fittings to ensure they allow grease to flow freely without resistance, ensuring all components are adequately lubricated.
By cleaning the fittings and inspecting for damage, you can keep the grease system running at peak performance and prevent clogs from developing.
Using Automatic Lubrication Systems to Minimize Human Error
Automatic lubrication systems are designed to deliver precise, consistent amounts of grease to each fitting, reducing the chances of clogging caused by human error. These systems help by:
Eliminating Over-greasing: Automatic systems are calibrated to apply the right amount of grease, preventing over-pressurization and the risk of forcing contaminants into the fitting.
Reducing Under-greasing: Automated systems ensure that each part gets lubricated at the correct frequency, preventing parts from running dry and wearing out.
Using the Right Grease: Automatic systems can be set up to use the correct type of grease for different machinery, ensuring compatibility and reducing the risk of clogging.
While automatic lubrication systems are an investment, they can significantly reduce maintenance costs and improve equipment performance over time by ensuring that grease is applied correctly and consistently.
Proper Grease Gun Usage to Avoid Over-pressurization
When using a grease gun, it’s important to apply the right amount of pressure to avoid over-pressurizing the system. Over-pressurization can force contaminants into the grease fitting, cause the grease to leak, or even damage seals and components. To avoid these issues:
Avoid Excessive Force: Apply grease at a steady, controlled pressure. If resistance is encountered, stop and check for possible blockages or damaged fittings before continuing.
Monitor Pressure: Use a grease gun with a pressure gauge to monitor and control the amount of pressure being applied, ensuring that the fitting does not become over-pressurized.
Follow Manufacturer Recommendations: Always adhere to the equipment manufacturer’s specifications for grease application pressure, as applying too much force can cause serious damage.
By using the grease gun correctly and carefully, you can prevent issues such as grease leakage and clogged fittings that result from over-pressurization.
Avoiding Contaminants: Protecting Your Grease System from Dirt and Water
Contaminants like dirt and moisture can quickly degrade the quality of grease, leading to clogs and system failures. To prevent these contaminants from entering the grease system, take the following precautions:
Inspect Seals Regularly: Ensure that the seals on grease fittings are intact and not worn out. Damaged seals allow dirt and water to infiltrate the lubrication system, causing contamination.
Keep the System Clean: Always clean the area around the grease fitting before applying grease to avoid introducing dirt or dust into the system.
Use Protective Covers: Consider using protective covers for grease fittings to shield them from dirt, dust, and moisture, especially when machinery is used in harsh environments.
Step-by-Step Guide
When a grease fitting becomes clogged, it can lead to inadequate lubrication, causing friction, wear, and potential damage to your equipment. Fixing a clogged hydraulic grease fitting requires a systematic approach to safely clear the blockage and restore the proper flow of grease.
Step 1: Identify the Problem and Assess the Damage
Before taking any action, it’s essential to confirm that the grease fitting is indeed clogged. Common signs of a clogged hydraulic grease fitting include:
Difficulty greasing: If you’re having trouble applying grease or the grease gun doesn’t dispense grease properly, the fitting may be obstructed.
Leakage: Excessive pressure buildup due to a clog can cause grease to leak around the fitting.
Unusual equipment behavior: If your equipment is making unusual noises, vibrating, or experiencing reduced performance, it may be a result of inadequate lubrication due to a clogged hydraulic grease fitting.
Once you identify the issue, assess whether the blockage is recent or has been building up over time. This can help you determine how severe the clog might be.
Step 2: Use a Grease Gun to Apply Pressure and Clear the Blockage
The first attempt to fix the clog is to apply pressure using a grease gun. This is a simple and effective method for clearing minor blockages. Here’s how to do it:
Prepare the grease gun: Ensure the grease gun is filled with the correct type of grease for your equipment.
Attach the nozzle to the fitting: Ensure a tight seal between the grease gun and the grease fitting.
Apply steady pressure: Begin pumping grease into the fitting. The force of the grease should help push the blockage out. Be careful not to over-pressurize the fitting, as this can damage seals or cause grease to leak.
Monitor the grease flow: If the grease starts flowing freely, the blockage is cleared. If it doesn’t, proceed to the next step.
Step 3: Apply Heat to Loosen Clogged Grease
If the grease fitting is still clogged after attempting to use the grease gun, the blockage may be caused by hardened grease. Applying heat can soften the grease and make it easier to clear. Here’s how to safely apply heat:
Use a heat gun or torch: Aim the heat at the clogged fitting and surrounding areas. Be cautious with the amount of heat to avoid damaging the fitting or surrounding parts.
Heat the fitting for a few minutes: Gradually warm the fitting and the surrounding area to soften the hardened grease inside.
Test the grease gun again: After applying heat, try pumping grease through the fitting once more. The softened grease should help clear the blockage.
Step 4: Use a Solvent or Grease Removal Tools for Stubborn Blockages
If heat doesn’t work, you may need to use a solvent or specialized tools to break up and remove the blockage. Here’s how to proceed:
Apply a grease solvent: Use a lubricant or solvent specifically designed to dissolve hardened grease. Apply the solvent to the fitting and allow it to penetrate the clog for several minutes.
Use a grease fitting cleaning tool: If the solvent isn’t effective, you can use a grease fitting cleaning tool or a small wire brush to carefully clear the blockage.
Clean out the fitting: Gently scrub and clear the fitting until grease flows freely. Be cautious not to damage the fitting or introduce new contaminants during this process.
Step 5: Inspect the Fitting for Damage and Replace if Necessary
Once the blockage is cleared, it’s time to inspect the grease fitting to ensure it is in good working condition. Here’s what you should look for:
Cracks or damage: If the fitting is cracked, worn out, or corroded, it may need to be replaced. A damaged fitting can cause leaks or further blockages.
Seal integrity: Check that the seal around the fitting is intact to prevent dirt or moisture from entering the lubrication system.
Smooth operation: Ensure that the fitting allows grease to flow smoothly and doesn’t offer resistance.
Conclusion
Proactive care, including timely inspections and routine cleaning of grease fittings, will help prolong the lifespan of your equipment, reduce repair costs, and maintain high performance. By staying on top of your grease fitting maintenance, you’ll avoid costly disruptions and keep your machinery running at its best.
FAQ
What is a grease fitting?
A grease fitting, also known as a Zerk fitting, is a small, threaded metal part that allows for easy injection of grease into machinery components, such as bearings or joints, to ensure smooth operation and prevent wear.
How do I know if my grease fitting is clogged?
Signs of a clogged hydraulic grease fitting include difficulty greasing, leakage around the fitting, unusual equipment noises or vibrations, visible residue or grease buildup around the fitting, and reduced equipment performance.
Can I fix a clogged hydraulic grease fitting myself?
Yes, clogged hydraulic grease fittings can often be fixed with simple tools. You can apply pressure with a grease gun, use heat to loosen hardened grease, or use a solvent or cleaning tool to clear stubborn blockages. If the fitting is damaged, it may need to be replaced.
How often should I inspect my grease fittings?
It’s recommended to inspect your grease fittings regularly as part of your equipment maintenance routine—typically every few weeks or according to the manufacturer’s maintenance schedule.
Can using the wrong grease cause clogs?
Yes, using the wrong type of grease, such as one with incorrect viscosity or incompatible with your equipment, can cause blockages in the fittings. Always choose the grease recommended by the manufacturer.
How can I prevent grease fitting clogs in the future?
To prevent clogs, establish a regular maintenance routine, use the correct grease, keep grease fittings clean and dry, and consider using automatic lubrication systems to ensure proper grease application. Regular inspections and cleaning are key to avoiding blockages.