Common ball valve failures, if left unaddressed, can disrupt operations and lead to inefficiencies, safety hazards, and even system downtime. Therefore, recognizing the early signs of valve failure and understanding how to troubleshoot and resolve these issues is key to extending valve life and ensuring the smooth operation of the entire system.
Ball Valve Getting Stuck or Jammed
Overview of Sticking or Jamming Issues
A ball valve that becomes stuck or jammed is a serious problem that can hinder the performance of an entire fluid control system. Ball valves are designed to be simple and reliable, using a rotating ball with a hole to either allow or block fluid flow. However, if the ball becomes obstructed or difficult to move, it can prevent the valve from performing its basic function of regulating flow. This can lead to system inefficiencies, flow disruptions, and even safety hazards, especially if the valve cannot be opened or closed when required.
When a ball valve is stuck, the ball inside the valve body is unable to rotate freely due to physical obstruction or damage. This results in the inability to fully open or close the valve, which can impede fluid flow or cause leaks. Jammed valves can be caused by a variety of factors, including dirt or debris inside the valve, corrosion of internal components, or improper installation of the valve and actuator. Depending on the cause, the issue can range from a minor inconvenience to a significant problem that requires immediate attention.
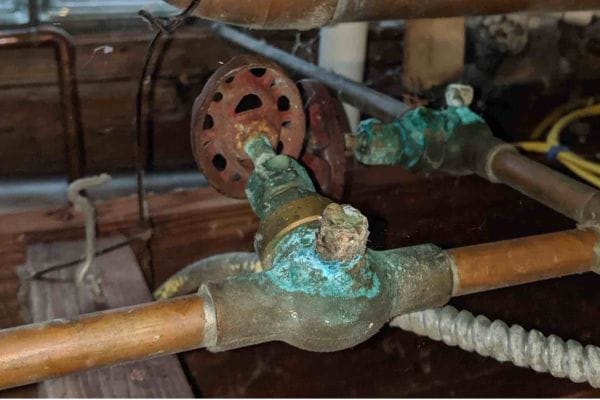
Causes of Valve Sticking
Several factors can lead to ball valve sticking or jamming, including:
Dirt and Debris: One of the most common causes of a stuck ball valve is the accumulation of dirt, rust, or other debris inside the valve body. This foreign material can obstruct the movement of the ball, causing it to jam. In high-pressure systems or where fluids contain particulates, debris can accumulate over time, particularly if the valve is not regularly maintained or cleaned.
Corrosion: Corrosion of the valve’s internal parts, such as the ball, seat, or stem, can result in increased friction and cause the valve to seize. Corrosion typically occurs due to exposure to harsh chemicals, moisture, or extreme temperatures, and it can cause the surfaces to become rough or uneven, making it difficult for the ball to rotate smoothly.
Incorrect Installation: Improper installation can also contribute to a stuck valve. If the valve is misaligned, the stem or actuator may not engage properly with the ball, causing friction or causing the ball to become misaligned within the body. Similarly, incorrect torque on the valve’s end connections or improper mounting of the actuator can contribute to this issue.
Lack of Lubrication: If the ball or stem lacks sufficient lubrication, the moving parts may stick due to friction. Lubrication is essential for smooth operation, and without it, the valve components may seize up, preventing the ball from rotating freely.
Wear and Tear: Over time, repeated usage can cause the valve’s components—especially the ball and the actuator—to wear down. This wear can lead to increased friction or mechanical failure, resulting in the ball becoming jammed or the actuator losing its ability to rotate the valve fully.
Temperature and Pressure Variations: Extreme temperature or pressure changes can put stress on the ball valve and its components, causing them to deform. These deformations may cause the ball to jam or the valve to become difficult to operate.
Common Scenarios
There are several common scenarios where ball valves may become stuck or jammed:
Ball Not Rotating Fully: In this case, the ball inside the valve body may not be able to complete a full 90-degree turn, which is necessary for the valve to either open or close. Partial rotation can occur due to the accumulation of dirt, corrosion on the ball or stem, or friction between the ball and valve seat. A valve that doesn’t fully rotate is not effectively controlling fluid flow and may lead to leaks or inadequate shut-off.
Inability to Open or Close the Valve: If the ball valve becomes completely stuck, the actuator (manual or automated) may not be able to turn the valve at all. This can occur when corrosion or debris has completely obstructed the ball or if the actuator is misaligned or malfunctioning. A valve that cannot be opened or closed can lead to system shutdowns or create safety hazards in critical applications.
Troubleshooting and Solutions
When a ball valve is stuck or jammed, troubleshooting should be done methodically to identify and address the underlying cause. Here are some effective solutions:
Cleaning the Valve and Removing Debris: One of the first steps in addressing a stuck valve is to clean the valve thoroughly. Remove any dirt, rust, or debris that may be obstructing the ball’s movement. In some cases, the valve may need to be disassembled to clean out debris, especially if it’s accumulated in hard-to-reach areas. For valves that are exposed to particulate-laden fluids, a filtration system or regular cleaning schedule should be considered to prevent buildup.
Using Lubricants to Free the Ball: If the ball is stuck due to friction or corrosion, applying the appropriate lubricant to the valve stem and ball can help free the mechanism. Use lubricants that are compatible with the valve’s materials and the fluid being controlled. A suitable lubricant can reduce friction and allow the ball to rotate smoothly, resolving minor sticking issues. It’s important to ensure that the lubricant doesn’t cause any adverse reactions with the fluid or the valve’s sealing materials.
Replacing Worn Parts: If cleaning and lubrication don’t resolve the issue, worn parts may need to be replaced. The valve stem, actuator, or even the ball and seats may be damaged due to wear or corrosion. Replacing these components can restore the valve’s functionality and prevent further sticking. When replacing parts, ensure that new components are compatible with the original valve specifications and the intended application.
Re-aligning the Valve and Actuator: In cases where improper installation or misalignment is the cause of the jam, the valve and actuator may need to be realigned. Misalignment can cause excess friction between the ball and valve seat or between the actuator and valve stem. Ensuring that the valve and actuator are correctly installed, with the proper torque on the end connections, can alleviate the sticking issue.
Valve Seat Damage
Overview of Valve Seat Failure
The valve seat plays a crucial role in ensuring that a ball valve performs its primary function—sealing off the fluid flow when the valve is in the closed position. The valve seat is typically a ring-shaped component made from materials that are highly resistant to wear, pressure, and corrosion. It sits directly in contact with the ball when the valve is closed, creating a tight seal that prevents fluid from leaking through the valve body.
When the valve seat becomes damaged or degraded, it fails to maintain this seal, leading to issues such as leaks, improper shut-off, and inefficient fluid control. This not only reduces the effectiveness of the ball valve but can also result in operational disruptions, system inefficiencies, and even safety hazards if fluid leakage occurs in sensitive applications. A damaged valve seat can undermine the valve’s overall integrity and functionality, causing unwanted flow or loss of pressure in the system.
Common Scenarios of Valve Seat Damage
Seat Material Degradation: The valve seat is typically made from soft materials, such as elastomers or PTFE (Polytetrafluoroethylene), to create an effective seal against the ball. However, these materials can degrade over time due to exposure to harsh chemicals, extreme temperatures, or abrasive particles in the fluid stream. As the seat material breaks down, it loses its ability to form a tight seal, resulting in leaks even when the valve is closed.
Excessive Wear from Harsh Fluids or Pressure: In systems that handle high-pressure fluids or abrasive substances, the valve seat can wear down much faster than normal. High-flow velocity, abrasive solids, or high temperatures can erode the seat material, leading to damage or loss of sealing ability. Furthermore, extreme pressure conditions may force the ball into the seat more aggressively, causing it to wear unevenly or crack. In such cases, improper shut-off or persistent leaks become more prevalent, as the damaged seat can no longer support the valve’s sealing function.
Thermal and Chemical Degradation: Over time, valve seats exposed to extreme temperature variations or corrosive chemicals may experience thermal degradation or chemical attack. This can cause the seat material to become brittle or chemically altered, impairing its sealing capabilities. For instance, PTFE seats may become soft or lose their shape when exposed to high temperatures, while elastomeric seals can swell or shrink when exposed to certain chemicals, leading to leaks.
Troubleshooting and Solutions
When valve seat damage occurs, it is essential to perform thorough inspections and take corrective measures to restore the valve’s functionality.
Inspecting the Valve Seat for Wear or Damage: The first step in diagnosing valve seat failure is to visually inspect the seat for signs of wear, cracks, or deformation. This can typically be done by disassembling the valve and removing the ball to gain access to the seat. Look for obvious signs of scoring, gouges, or abrasion, which are indicators of excessive wear. Additionally, check for any signs of material degradation or chemical attack. If the seat has lost its elasticity or shape, it may need to be replaced.
Replacing Worn or Damaged Seats: Once damage is identified, the valve seat should be replaced with a new one. In many cases, the seat is replaceable, and the valve itself can continue to be used after the damaged seat has been replaced. When replacing the seat, make sure to choose a high-quality replacement that matches the original specifications, including size, material, and design. Replacing the valve seat is crucial for restoring the valve’s ability to create a tight seal and prevent further leakage.
Choosing the Correct Material for Valve Seats Based on Application Conditions: One of the key factors in preventing valve seat damage is selecting the right seat material for the specific application. For instance, if the valve will be exposed to high temperatures, materials like metal or high-temperature elastomers should be chosen, as PTFE may degrade in such conditions. If the fluid being handled contains abrasive particles, a more durable material, such as ceramic or hard-coated metal, may be necessary.
Corrosion and Material Degradation in Ball Valves
Overview of Corrosion in Ball Valves
Corrosion is one of the most common and damaging issues that can affect ball valves, especially in systems exposed to harsh chemicals, high humidity, extreme temperatures, or abrasive environments. Corrosion can occur both externally and internally, and its impact on valve performance can be severe, leading to reduced reliability, leaks, compromised flow control, and even complete valve failure. In many industrial applications, corrosion is the primary cause of valve malfunctions, necessitating regular inspections and preventive measures.
The process of corrosion involves the gradual deterioration of material properties due to chemical reactions between the material and its environment. For ball valves, corrosion can degrade the valve body, seats, stem, or internal parts, leading to poor sealing, leaks, or mechanical failure. The rate and extent of corrosion depend on factors such as the fluid being handled, the materials used in the valve, and environmental conditions.
Common Materials Vulnerable to Corrosion
Certain materials used in ball valve construction are more vulnerable to corrosion than others. Common materials susceptible to corrosion include:
Carbon Steel: While cost-effective and widely used, carbon steel is highly susceptible to rust and corrosion when exposed to water or humid environments. Carbon steel valves are generally not recommended for systems involving aggressive chemicals or high moisture content.
Brass: Brass, often used in residential and light industrial applications, is prone to dezincification and corrosion, especially in high-chloride environments. This leads to pitting and weakening of the valve structure.
Cast Iron: Cast iron valves are vulnerable to both internal and external corrosion. Over time, exposure to moisture or corrosive fluids can cause significant degradation of the valve body.
Stainless Steel (Lower Grades): While stainless steel is generally more resistant to corrosion than carbon steel, certain grades (such as 304 stainless steel) may still succumb to pitting, crevice corrosion, or stress corrosion cracking in chloride-rich environments.
Aluminum: Aluminum ball valves are often used in lightweight applications but are highly susceptible to corrosion, particularly when exposed to saltwater or acidic environments.
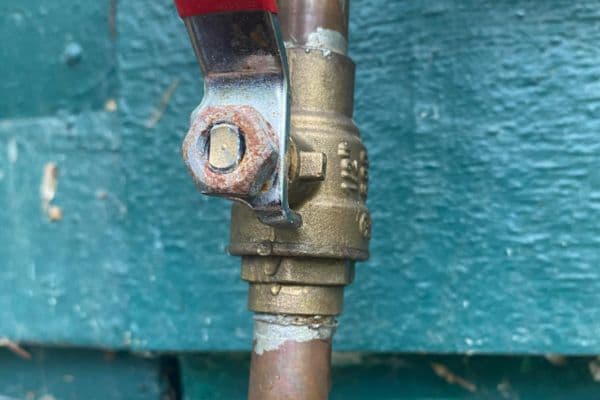
Common Scenarios of Corrosion in Ball Valves
Rust on the External Valve Body: External corrosion, often seen as rust on the outside of a valve body, is common in valves exposed to high humidity or water vapor. Rust typically forms on the surface of metals like steel and iron when they are exposed to moisture and oxygen. Over time, this rust can compromise the integrity of the valve, leading to weakened valve bodies, loss of structural strength, and potential leaks. External corrosion can be exacerbated by poor maintenance or lack of protective coatings.
Internal Corrosion from Exposure to Harsh Chemicals or Water: Internal corrosion occurs when the fluid passing through the valve reacts with the internal surfaces of the valve, leading to material degradation. For example, water or acidic chemicals like hydrochloric acid can cause pitting or surface etching on valve components, particularly in brass or carbon steel valves. Similarly, exposure to chlorine, sulfides, or other reactive chemicals can cause corrosion inside the valve body, leading to leaks or failure of the valve’s sealing mechanism.
Corrosion Under Insulation (CUI): Corrosion under insulation (CUI) is a particular problem in ball valves used in industrial settings, where insulation is applied to valves or piping systems. If the insulation becomes wet or moisture-laden, it can create an environment that promotes internal and external corrosion of the valve components. This often leads to hidden corrosion that may not be immediately apparent during regular inspections, resulting in catastrophic failures if not identified early.
Troubleshooting and Solutions for Corrosion
Identifying Corrosion on the Valve Body and Internal Components: The first step in addressing corrosion is to thoroughly inspect the valve for visible signs of material degradation. Externally, look for rust, pitting, discoloration, or flaking on the valve body. Internally, if the valve can be disassembled, inspect the seats, ball, stem, and other moving parts for signs of pitting, rust, or thinning of the material. Regular, periodic inspections can help identify early signs of corrosion, especially if the valve operates in a corrosive or high-humidity environment.
Cleaning and Removing Corrosion: Once corrosion is identified, the next step is to clean and remove the damaged material. For external corrosion, abrasive methods such as wire brushing or sandblasting can be used to remove rust and other surface corrosion. This can restore the surface of the valve body and allow for further inspection. For internal corrosion, a combination of chemical cleaning agents, abrasives, and mechanical cleaning methods may be required to remove corrosion from the valve ball and seats.
Replacing Corroded Components or Entire Valve: In cases where corrosion has severely degraded the valve body, seats, or other critical components, replacement may be necessary. Valve seats and internal components can be replaced if the rest of the valve body is still in good condition. However, if the valve body itself is significantly corroded, the entire valve should be replaced to ensure reliable performance and avoid future leaks or failures.
Overheating or Overpressure Failure in Ball Valves
Overview of Overheating/Overpressure Issues
Ball valves are essential components in fluid control systems, regulating the flow of liquids or gases in a variety of industrial applications. However, when exposed to excessive temperatures or pressures beyond their design limits, ball valves can experience significant operational failures.
Effects of Excessive Heat or Pressure on Ball Valve Performance:
Overheating: Excessive heat can cause the materials of the valve to expand, soften, or degrade. In many cases, sealing materials such as elastomers or PTFE can break down at high temperatures, leading to leaks or loss of sealing integrity. Furthermore, excessive thermal expansion can cause the ball to seize within the valve, leading to difficulty in operation or valve jamming.
Overpressure: Similarly, overpressure can cause distortion or damage to the valve components. The valve body, seats, and seals can all be compromised under excessive pressure. Overpressure conditions may lead to failure of the ball valve’s sealing mechanism, leaks, or even catastrophic valve body rupture in extreme cases. If the internal pressure exceeds the valve’s rated capacity, the valve may not close properly, leading to dangerous fluid leakage.
Common Scenarios of Overheating or Overpressure Failure
Valve Failure Due to Exceeding Temperature Ratings: Every ball valve is rated for a specific maximum operating temperature. Exposing the valve to temperatures beyond this limit can cause various types of damage, such as distortion of the valve body, failure of the seals, or weakening of the valve’s material strength. For instance, many standard valve seats and seals made from materials like PTFE or elastomers begin to degrade at temperatures above 180-200°C, resulting in leaks or valve failure.
Overpressure Causing Valve Distortion or Leaks: Ball valves are designed to withstand certain pressure limits based on their material strength, size, and construction. Exposing the valve to pressures that exceed its rated capacity can cause deformation of the valve body or the ball itself. This can lead to misalignment between the ball and valve seat, resulting in improper sealing, pressure loss, or leakage.
In cases of extreme overpressure, the valve body may crack or rupture, resulting in hazardous fluid leaks, especially in applications dealing with high-pressure gas or corrosive substances. Overpressure can also damage internal components such as the valve stem, actuator, or sealing rings, leading to valve failure and significant downtime for repair or replacement.
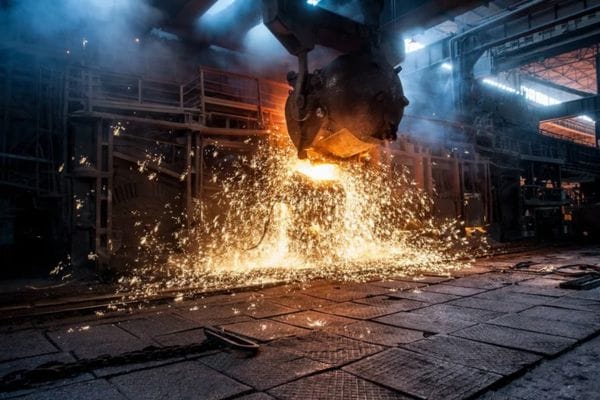
Troubleshooting and Solutions
When a ball valve experiences issues due to overheating or overpressure, prompt identification of the root cause is critical to preventing further damage and ensuring the safety and performance of the system. Here are several steps to troubleshoot and address these issues:
Checking Temperature and Pressure Gauges Regularly: One of the most effective ways to prevent overheating or overpressure failure is through regular monitoring of system parameters. Operators should continuously check temperature and pressure gauges to ensure that the system is within the safe operating limits. If temperatures or pressures approach or exceed the valve’s rated specifications, the system should be shut down immediately to prevent damage. Regular monitoring also allows for the early detection of abnormal conditions, helping prevent failures of ball valves before they occur.
Replacing Damaged Components Due to Overheating or Pressure Damage: If overheating or overpressure has caused significant damage to the ball valve, it may be necessary to replace certain components to restore the valve’s function. Common components that may need replacement include valve seats, seals, O-rings, and even the valve body if it has been structurally compromised. Inspecting the ball, stem, and actuator for signs of deformation or wear is also essential, as these parts may have been affected by excessive heat or pressure.
Installing Pressure Relief Systems or Pressure Regulators: To prevent overpressure, installing pressure relief systems or regulators is an effective strategy. These systems help maintain the pressure within safe operating limits by automatically venting excess pressure from the system. Pressure relief valves (PRVs) and pressure regulators can be used to control the pressure downstream of the ball valve, ensuring that the valve is never exposed to pressures beyond its rated capacity.
Actuator or Operator Failures in Ball Valves
Overview of Actuator Issues
Actuators are critical components that provide the force needed to operate ball valves, allowing them to open or close based on system demands. Actuators can be powered in several ways: manually, pneumatically, or electrically.
Manual Actuators: These are operated by hand and typically used in smaller valves or in situations where automated control is unnecessary. They rely on a handwheel or lever to turn the valve.
Pneumatic Actuators: These use compressed air to operate the valve. Pneumatic actuators are commonly used in industrial systems that require fast and efficient valve movement.
Electric Actuators: Electric actuators are powered by electricity and provide precise control over the valve position, making them ideal for systems requiring accurate flow regulation and remote control.
Hydraulic Actuators: These actuators use hydraulic fluid to move the valve and are generally used in high-pressure applications where greater force is required.
Common Scenarios of Actuator Failure
Actuator Not Responding to Commands: A common issue with actuators is that the valve does not respond to control signals, whether from a manual input or an automated system. This may occur due to mechanical failure within the actuator, issues with power supply, or control signal interruptions. For example, in electric actuators, a failure in the electrical system (such as a blown fuse or faulty wiring) can prevent the actuator from receiving or executing the command to move the valve.
Pneumatic Actuators Losing Air Pressure: Pneumatic actuators rely on compressed air to function. If the air pressure is lost or insufficient, the actuator will fail to operate the valve. This can be caused by leaks in the air supply system, failure of the compressor, or damage to the actuator itself. Pneumatic actuators can also suffer from issues like air hose blockages or contamination, which can prevent the actuator from receiving or releasing the air needed to move the valve.
Electric Actuators Having Power Issues: Electric actuators can fail if they lose power or if the power supply is unstable. This may occur due to issues like power outages, electrical surges, or faulty connections. For example, a malfunctioning power supply, such as a broken transformer or loose wiring, can cause the actuator to stop functioning. Additionally, electric actuators that use motors can also experience mechanical failures, such as gear slippage or motor burnout, leading to a loss of valve movement.
Overloading or Mechanical Failure: Actuators can also fail due to overloading or mechanical wear. Overloading occurs when the actuator is asked to perform beyond its rated capacity, such as trying to move a valve that is too large or heavy for the actuator’s specifications. This can cause mechanical components to fail, including gears, motors, or pistons, which may render the actuator inoperable.
Troubleshooting and Solutions
Diagnosing actuator failures requires a systematic approach to identify the root cause and perform the necessary repairs. Below are some steps for troubleshooting and solutions:
Diagnosing Actuator Failures: The first step in troubleshooting is to determine the type of actuator and its failure mode. For pneumatic actuators, check the air pressure and verify that there are no leaks in the system. If the actuator is not responding, inspect the compressor and verify that it is supplying adequate air pressure. For electric actuators, check the power supply and ensure that there is no interruption in the electrical circuit. For manual actuators, ensure that the valve is not seized or obstructed and that the handle is intact.
Checking Air, Power, or Mechanical Connections: For pneumatic actuators, inspect the air supply lines for leaks, blockages, or damage. Verify that the compressor is working correctly and that the air pressure meets the required specifications for actuator operation. If there is no power to an electric actuator, check the electrical connections, fuses, and circuit breakers. Ensure that the wiring is intact and the actuator’s motor is functioning properly. Mechanical connections, including gears or couplings, should be inspected for wear or damage that may affect actuator performance.
Replacing Faulty Actuators or Operator Components: If the actuator or operator components are found to be damaged beyond repair, replacement may be necessary. In the case of pneumatic actuators, this could involve replacing the actuator itself, the air compressor, or damaged valves in the air supply line. For electric actuators, faulty motors, controllers, or wiring may need to be replaced. In cases where the actuator is part of a larger control system, replacement of control boards or feedback sensors may be required.
Performing Manual Overrides in Case of Actuator Failure: In situations where an actuator fails and immediate action is required, performing a manual override can ensure that the valve continues to function. Many electric and pneumatic actuators are equipped with manual override mechanisms, which allow operators to turn the valve by hand or using an alternative power source. This is especially useful for emergencies when automated control is not possible.
Conclusion
Whether through scheduled maintenance, addressing minor issues before they escalate, or choosing higher-quality valves, taking proactive steps now can prevent future failures. Don’t wait until problems arise—invest in the long-term health of your systems by adopting the practices discussed in this article.
FAQ
What causes a ball valve to leak?
Leaks in ball valves can occur due to worn seals, damaged O-rings, improper installation, or issues with the valve stem. External leaks often happen around the stem or seals, while internal leaks may occur through the valve body or between the ball and seat.
Why do ball valves get stuck or jammed?
Ball valves may become stuck due to dirt or debris buildup, corrosion, or improper installation. A ball that doesn’t rotate fully or a valve that won’t open or close can be a sign of these issues.
What is valve seat damage and how does it affect the valve?
Valve seat damage occurs when the sealing surface between the ball and valve body wears down or degrades. This can lead to leaks or improper shutoff, compromising the valve’s ability to control fluid flow.
How can corrosion affect ball valves?
Corrosion, whether external or internal, can degrade the valve material, leading to rust, leaks, and eventual failure. Common causes include exposure to chemicals, moisture, or extreme temperatures, especially in steel or brass valves.
What happens when a ball valve is exposed to overheating or overpressure?
Overheating and overpressure can distort or damage the valve, leading to leaks, cracking, or complete failure. It’s important to monitor temperature and pressure levels to prevent these issues.
How can actuator failure impact a ball valve?
Actuator failures prevent the ball valve from responding to control signals, leading to an inability to open or close the valve. Common causes include power issues (for electric actuators) or air pressure loss (for pneumatic actuators).