Reliable hydraulic fittings are essential to prevent leaks, corrosion, and performance failures, which can result in costly downtime, equipment damage, and safety hazards. Poor-quality fittings can lead to common issues such as leakage, system contamination, reduced efficiency, and premature wear. In harsh environments, inadequate fittings may corrode, weakening the system and reducing its lifespan. Therefore, rigorous testing of hydraulic fittings is crucial to ensure they meet high-quality standards, ensuring system safety, reliability, and optimal performance.
Dimensional Accuracy and Measurement
Why Dimensional Accuracy is Crucial for Hydraulic Fittings
Dimensional accuracy is one of the most important factors in ensuring the proper functionality and safety of hydraulic fittings. Since hydraulic systems operate under high pressure and extreme conditions, even slight deviations in the size or shape of a fitting can lead to significant problems. Here’s why maintaining precise dimensional accuracy in hydraulic fittings is so critical:
Proper Sealing and Leak Prevention: Hydraulic fittings must be precisely manufactured to ensure a perfect fit when connected. Any variation in dimensions—such as incorrect thread sizes or improperly machined surfaces—can cause poor seals. This leads to hydraulic fluid leaks, which compromise system performance, efficiency, and safety.
Ensuring Compatibility: Hydraulic fittings are part of a larger system, where multiple components must fit together with precision. If a fitting is not dimensionally accurate, it may not be compatible with other parts like hoses, connectors, or valves. This incompatibility can result in malfunctions or even complete system failure.
Stress Distribution: Hydraulic fittings are designed to handle high-pressure environments. If a fitting has irregular dimensions, stress may not be evenly distributed, which can lead to weak points that are prone to cracking or deformation. This can cause premature wear and tear on the fitting and reduce the overall lifespan of the hydraulic system.
Common Tools for Hydraulic Fitting Dimensional Measurement
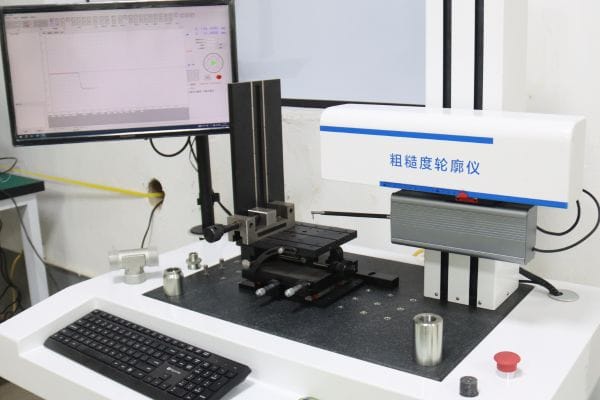
To achieve the precise dimensional accuracy required in hydraulic fittings, manufacturers use a variety of measurement tools and techniques. These tools allow meticulous inspection of the size, shape, and tolerance of each fitting. Here are some of the most common tools used in hydraulic fitting dimensional measurement:
Calipers (Vernier, Dial, and Digital) Calipers are one of the most commonly used tools for measuring the external and internal dimensions of hydraulic fittings. They are highly accurate and can measure things like the outer diameter of fittings, the inside diameter of hoses, and thread depth. Digital calipers provide precise, easy-to-read measurements, making them ideal for production environments.
Micrometers Micrometers are used for measuring the thickness or outside diameter of small components with a high degree of accuracy. They are particularly useful when inspecting the precise dimensions of threaded sections or checking the tolerance of small fittings.
Thread Gauges Hydraulic fittings often feature threaded connections that must be perfectly matched to ensure a leak-proof seal. Thread gauges are specialized tools used to measure the pitch and depth of threads, ensuring that they conform to industry specifications. Both go/no-go gauges and screw pitch gauges are used to check the precision of threaded fittings.
CMM (Coordinate Measuring Machines) A CMM is a sophisticated tool used in hydraulic fitting quality test for precise measurement of 3D shapes. These machines use a probe to measure the fitting’s dimensions in three dimensions, providing high-accuracy data on the geometry of complex fittings. CMMs are ideal for inspecting multiple dimensions and ensuring that a fitting meets exact specifications.
Height Gauges Height gauges are used to measure the vertical dimensions of a fitting. These are especially useful for checking the height or depth of features on the fitting, such as grooves, faces, or internal cavities, ensuring they are within tolerance.
Microscopic Inspection Tools For measuring extremely small features or checking surface finishes, microscopic inspection tools can be used. These tools are often employed when a very high level of precision is required, such as in the measurement of fine threads or small diameter holes.
Go/No-Go Gauges Go/No-Go gauges are a fast and efficient way to check whether a hydraulic fitting is within acceptable tolerance limits. These gauges are designed to fit into a fitting’s measurement points—if the “go” part of the gauge fits and the “no-go” part does not, the fitting passes the test.
Laser Scanning and 3D Laser Profilers Advanced technology such as laser scanning systems can be used to obtain high-precision, non-contact measurements of hydraulic fittings. 3D laser profilers create a digital map of a fitting’s dimensions and surface profile, providing detailed data on the shape, surface texture, and any imperfections.
Optical Projectors An optical projector, also known as a profile projector, uses light and magnification to project an image of the fitting onto a screen. This image can be measured with calibrated rulers or micrometers to assess dimensional accuracy and detect any flaws that could impact the fitting’s functionality.
Depth Micrometers Depth micrometers are used to measure the depth of grooves, slots, or internal cavities within a hydraulic fitting. These measurements are critical to ensuring that features such as internal threads or sealing surfaces meet precise specifications for safe, effective operation.
Corrosion Resistance Test: Protecting Against the Elements
How Corrosion Resistance Testing Prevents Premature Fitting Failures
Corrosion resistance testing is a critical aspect of quality control for hydraulic fittings. Hydraulic systems often operate in harsh environments, where fittings are exposed to moisture, chemicals, salt, and extreme temperatures—conditions that can accelerate the corrosion process. If a hydraulic fitting is not properly tested for its resistance to corrosion, it can lead to premature failure, potentially compromising the entire hydraulic system. Here’s how corrosion resistance testing prevents such failures:
Prevents Material Degradation: Corrosion can weaken the structural integrity of hydraulic fittings, leading to cracks, pitting, and eventually catastrophic failure. By testing fittings for their ability to resist corrosion, manufacturers ensure that the materials used will withstand the harsh operating conditions they may encounter throughout their service life.
Ensures Long-Term Durability: Corrosion resistance testing helps manufacturers select the right materials and coatings for hydraulic fittings, ensuring they have the durability to last even in challenging environments. By simulating long-term exposure to corrosive elements, such as saltwater or industrial chemicals, manufacturers can predict the lifespan of the fittings and guarantee their performance.
Maintains Performance in Critical Environments: Hydraulic systems in industries such as oil and gas, marine, and construction are exposed to harsh, corrosive environments. Without effective corrosion resistance, fittings could deteriorate rapidly, leading to leaks, failures, and loss of pressure in the system. Testing helps identify any weaknesses in materials or coatings that could compromise the fitting’s ability to maintain a seal or handle pressure.
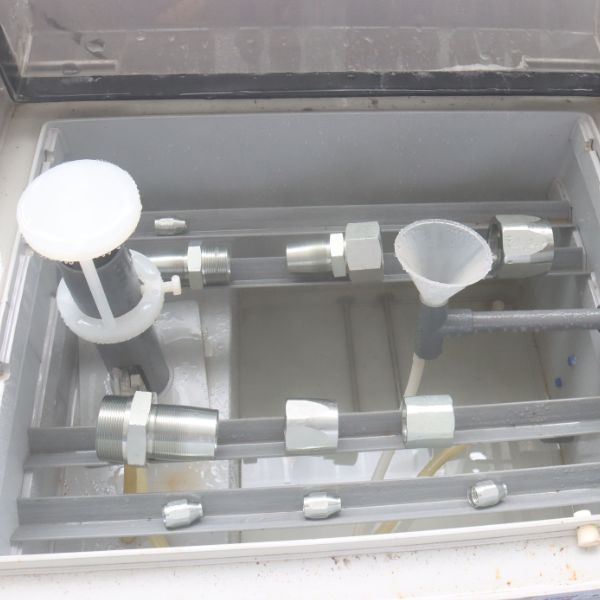
Salt Spray Testing and Its Role in Corrosion Resistance
One of the most widely used methods for evaluating corrosion resistance in hydraulic fittings is salt spray testing, also known as the salt spray test. This method simulates the corrosive effects of saltwater environments and helps manufacturers determine how well their fittings will perform when exposed to saline conditions. Here’s how salt spray testing plays a critical role in assessing corrosion resistance:
Simulating Harsh Environments: Salt spray testing exposes hydraulic fittings to a fine mist of salt water in a controlled chamber. This simulates long-term exposure to marine environments, coastal climates, or industrial settings where fittings might come into contact with salt, chemicals, or moisture. The test accelerates the natural corrosion process, allowing manufacturers to observe the material’s resistance to corrosion in a matter of days or weeks.
Assessing Coatings and Surface Treatments: Hydraulic fittings are often coated or treated to enhance their corrosion resistance. Salt spray testing helps manufacturers assess the effectiveness of these coatings or treatments. The test reveals any areas where the coating may have failed or where the base material is starting to corrode, providing valuable insights into the longevity and effectiveness of the protective layers.
Measuring Corrosion Rates: The test measures the rate at which corrosion appears on the surface of the fitting, typically through the formation of rust or discoloration. By calculating this rate, manufacturers can determine the expected lifespan of the fittings when exposed to real-world corrosive conditions. This allows them to make informed decisions about material selection and design to enhance durability.
Identifying Vulnerable Areas: During salt spray testing, manufacturers can identify specific areas on the hydraulic fitting that are more prone to corrosion. This might include threaded sections, welds, or areas where protective coatings may have been applied inconsistently. Identifying these vulnerable areas early allows for design improvements to strengthen those parts and enhance the overall durability of the fitting.
Pressure Testing: Verifying Pressure Ratings and Safety
How Pressure Testing Confirms the Safety and Functionality of Hydraulic Fittings
Pressure testing is a critical step in the quality assurance process for hydraulic fittings, as it ensures that these components can withstand the high-pressure environments they are designed for without failure. Hydraulic fittings must be able to maintain a secure seal and retain their integrity under extreme pressure conditions. Here’s how pressure testing helps verify the safety and functionality of hydraulic fittings:
Ensures Leak-Free Operation: One of the primary functions of hydraulic fittings is to create a secure, leak-free connection between components in a hydraulic system. Pressure testing checks whether the fittings can handle the system’s pressure without any leaks. By testing fittings at their rated pressure or beyond, manufacturers can confirm that they meet the required sealing standards and will perform safely in the field.
Validates Pressure Ratings: Each hydraulic fitting is designed with a specific pressure rating, indicating the maximum pressure it can safely handle. Pressure testing verifies that the fitting can withstand its rated pressure without deforming, cracking, or failing. This ensures that the hydraulic system operates within safe parameters and minimizes the risk of system failure due to over-pressurization.
Prevents Catastrophic Failures: Pressure testing simulates real-world operating conditions, helping to identify any potential weaknesses in the fitting before it is installed in a hydraulic system. A failure during pressure testing can reveal design flaws or material weaknesses that may not have been apparent during other tests. By catching these issues early, manufacturers can prevent catastrophic failures, such as blowouts or ruptures, that could lead to equipment damage, system failure, or even injury.
Ensures System Integrity: Hydraulic systems often operate under fluctuating pressures and can experience pressure spikes or surges. Pressure testing ensures that the fittings can maintain their integrity even under these dynamic conditions. By testing fittings to their maximum rated pressure, manufacturers can confirm that they will function reliably and safely under varying pressure conditions during real-world operations.
Methods for Performing Hydraulic Fitting Pressure Testing
There are several methods for conducting pressure testing on hydraulic fittings, each suited for different types of fittings, materials, and application environments. The method chosen depends on factors such as the type of fitting, its size, the operating pressure, and the industry standards required. Below are some of the most common methods used for hydraulic fitting pressure testing:
Hydrostatic Pressure Testing
Hydrostatic testing involves filling the hydraulic system or fitting with a liquid (usually water or oil) and gradually increasing the pressure until it reaches the specified test pressure. This method is particularly effective for checking for leaks, structural weaknesses, and material deformation. Because liquids are incompressible, any leaks or ruptures will be immediately visible, making it easier to identify potential issues. Hydrostatic testing is widely used for testing high-pressure fittings and pipelines in industries such as oil and gas, aerospace, and manufacturing.
Advantages: Accurate, easy to detect leaks, and effective for high-pressure testing.
Disadvantages: Requires the use of liquid, which may not be suitable for all environments or systems.
Pneumatic Pressure Testing
Pneumatic pressure testing uses compressed air or another gas to test hydraulic fittings. This method is generally used when the fitting cannot be filled with a liquid or where the use of liquids would pose a safety risk. Pneumatic testing is faster and easier to set up compared to hydrostatic testing, but it is more dangerous due to the compressibility of gases. Therefore, safety precautions, such as the use of protective shields or enclosures, are essential during pneumatic testing.
Advantages: Faster setup, suitable for gas-based systems, and no need for liquid.
Disadvantages: Higher safety risks, less effective in detecting small leaks compared to hydrostatic testing.
Burst Testing
Burst testing is a more extreme form of pressure testing, where the hydraulic fitting is pressurized until it fails (or “bursts”). This test is used to determine the maximum pressure a fitting can handle before it ruptures, giving manufacturers insight into its ultimate strength. While this test is typically performed on a small sample of fittings for quality assurance purposes, it provides valuable data on the material’s failure point and helps define the upper pressure limits for the product.
Advantages: Determines the maximum strength and pressure limits of the fitting.
Disadvantages: Destructive; the fitting is ruined, and this test is usually done only on samples.
Pressure Cycling (Fatigue) Testing
In pressure cycling or fatigue testing, the hydraulic fitting is subjected to repeated pressure fluctuations or cycles to simulate real-world operating conditions. This test is essential for evaluating the durability of hydraulic fittings under fluctuating pressure conditions, as fittings may experience pressure spikes or drops during normal operation. The test helps identify issues related to material fatigue, deformation, and long-term performance.
Advantages: Simulates real-world conditions, ideal for evaluating long-term performance.
Disadvantages: Time-consuming and requires specialized equipment to cycle pressures accurately.
Leak Testing
Leak testing focuses on identifying any signs of leakage under pressure. In this method, the hydraulic fitting is pressurized, and various leak detection tools (such as dye, ultrasonic sensors, or bubble tests) are used to spot leaks at the seals or threaded connections. Leak testing is essential for verifying the integrity of the fitting’s seals and ensuring that the hydraulic system will not suffer from fluid loss during operation.
Advantages: Non-destructive, quick, and ideal for detecting minor leaks.
Disadvantages: Does not assess the overall strength of the fitting; more focused on sealing effectiveness.
Hardness Testing: Ensuring Material Strength
The Importance of Hardness Testing in Hydraulic Fitting Quality Control
Hardness testing is a critical part of the quality control process for hydraulic fittings, as it provides insight into the material’s ability to resist deformation, wear, and surface damage under stress. Hydraulic fittings are exposed to high pressures, vibrations, and harsh operating environments, making it essential to ensure that the materials used can withstand these conditions without losing their integrity. Here’s why hardness testing plays a pivotal role in hydraulic fitting quality control:
Ensures Material Suitability: Hydraulic fittings are made from a variety of metals, including stainless steel, brass, and carbon steel. Each material has its own set of mechanical properties that influence its performance in different applications. Hardness testing helps verify that the material chosen for the fittings has the appropriate hardness level for the intended use, ensuring that it can withstand operational pressures and forces without premature failure.
Detects Inconsistent Material Quality: During manufacturing, material inconsistencies can occur, such as variations in alloy composition or heat treatment processes. These inconsistencies can affect the hardness of the final product and, by extension, its performance. Regular hardness testing helps identify weak points in the material, allowing manufacturers to detect and correct problems before the fittings are used in hydraulic systems.
Improves Component Performance: The hardness of a material is directly correlated with its ability to resist wear and tear. Fittings with inadequate hardness may experience surface damage or deformation over time, leading to system inefficiency and failure. By conducting hardness tests, manufacturers can ensure that fittings will maintain their integrity and perform reliably throughout their lifespan.
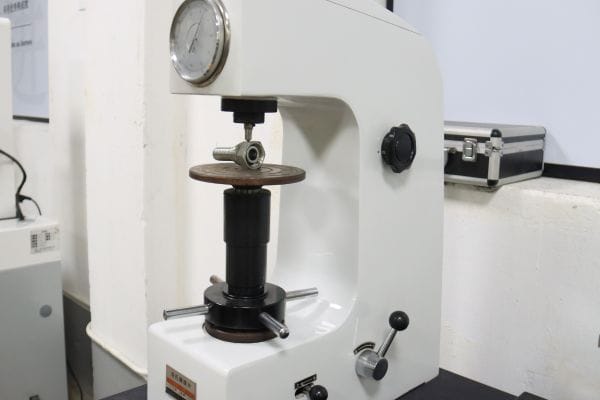
How Hardness Testing Affects Hydraulic Fitting Durability
Hardness testing is directly linked to the durability and longevity of hydraulic fittings. The material hardness determines how well a fitting can withstand the rigors of high-pressure environments, heavy loads, and abrasive conditions. Here’s how hardness testing influences the overall durability of hydraulic fittings:
Wear Resistance: The harder the material, the more resistant it is to wear and surface damage. In hydraulic systems, fittings often experience friction and constant pressure, which can cause softer materials to degrade more quickly. Hardness testing ensures that the material has sufficient hardness to resist wear from repeated cycles of pressure and contact, helping the fitting maintain its performance over time.
Resistance to Surface Damage: Hydraulic fittings, especially those with threaded sections or sealing surfaces, must maintain smooth, precise surfaces to prevent leaks and ensure proper sealing. A material that is too soft may experience surface damage, such as scratching or indentation, which can affect the fitting’s ability to form a tight, leak-proof seal. Hardness testing ensures that the fitting’s surface will remain intact even after prolonged use.
Impact Resistance: Hydraulic systems are exposed to high-pressure forces that can cause components to experience sudden impacts or vibrations. Harder materials are more capable of withstanding these stresses without deforming or breaking, which is essential for maintaining the long-term integrity of the fitting. By ensuring the material hardness meets the required standards, manufacturers can ensure that their fittings will perform reliably even under the most demanding conditions.
Fatigue Resistance: Hydraulic systems are often subject to repeated stress cycles, which can lead to fatigue failure if the material is not properly hardened. Fatigue failure occurs when a material weakens over time due to repetitive loading and unloading. Hardness testing helps to ensure that the material has the necessary resistance to fatigue, extending the life of the hydraulic fitting and preventing premature failure.
Conclusion
In conclusion, investing in hydraulic fitting testing is a proactive approach to guaranteeing the safety, functionality, and efficiency of hydraulic systems, contributing to their long-term success and reliability. Proper testing ensures that fittings can withstand extreme conditions, prevent leaks, and avoid system contamination, ultimately maintaining the integrity and safety of the hydraulic systems they support.
FAQ
What is hydraulic fitting testing?
Hydraulic fitting testing involves evaluating the quality and performance of hydraulic fittings to ensure they meet industry standards. It includes tests for dimensional accuracy, pressure tolerance, corrosion resistance, and material strength.
Why is hydraulic fitting testing important?
Testing ensures that hydraulic fittings are safe, reliable, and durable. It helps prevent leaks, corrosion, and performance failures, which can lead to system inefficiencies or safety hazards.
What are the common testing methods for hydraulic fittings?
Common testing methods include pressure testing, hardness testing, corrosion resistance testing, dimensional measurement, leak testing, and fatigue/burst testing.
How does pressure testing work for hydraulic fittings?
Pressure testing involves subjecting the hydraulic fitting to high pressure to ensure it can withstand the rated pressure without leaking or failing.
What is the role of corrosion resistance testing in hydraulic fitting quality?
Corrosion resistance testing ensures that hydraulic fittings can resist environmental factors like moisture, chemicals, and temperature variations, which helps prolong the lifespan of the fitting and prevent failures due to corrosion.
How does hardness testing affect hydraulic fitting durability?
Hardness testing assesses the material strength of hydraulic fittings, ensuring they can resist wear, impact, and pressure. This is vital for the long-term durability and reliability of hydraulic systems.