Aluminum fitting surface treatment is process used to enhance the surface properties of aluminum components. The right treatment ensures that aluminum fittings can withstand harsh environments, resist wear and tear, and maintain a high quality finish throughout their service life.
Anodizing Aluminum
What Is Anodizing and How Does It Work?
Explaining the anodizing process
Anodizing is an electrochemical process that involves immersing aluminum in an acid bath and applying an electric current. The result? A durable, corrosion-resistant oxide layer forms on the surface of the aluminum. Unlike paint or coatings that sit on top of the material, the anodized layer becomes an integral part of the aluminum itself, making it much stronger and longer-lasting.
This process works by causing the surface of the aluminum to react with oxygen in the electrolytic bath. During the anodizing process, the aluminum atoms at the surface bond with oxygen ions to form aluminum oxide (Al2O3), which is much harder than the original metal.
How anodizing creates a thicker, protective oxide layer
The anodizing process not only increases the thickness of the aluminum’s natural oxide layer but also enhances its protective qualities. The aluminum oxide layer can range from a few microns to over 100 microns in thickness, depending on the specific needs and desired finish.
This thickened oxide layer provides superior protection against environmental elements, such as water, air, and chemicals. The oxide acts as a barrier that prevents corrosion by resisting the intrusion of elements that would normally damage or degrade the aluminum surface.
The science behind anodizing: chemical reactions and the aluminum surface
The anodizing process relies on an electrolytic reaction. When the aluminum is submerged in an acid bath (usually sulfuric acid) and an electric current is applied, the aluminum reacts with the oxygen ions from the bath, forming aluminum oxide. This oxide is tightly bonded to the metal’s surface, making it highly durable and resistant to abrasion. Unlike traditional coatings, the anodized layer is chemically bonded, meaning it won’t peel or chip.
The formation of the oxide layer is controlled, and the result is an exceptionally tough, resistant surface that is capable of handling both physical wear and harsh environmental conditions. This makes anodized aluminum ideal for demanding industrial applications.
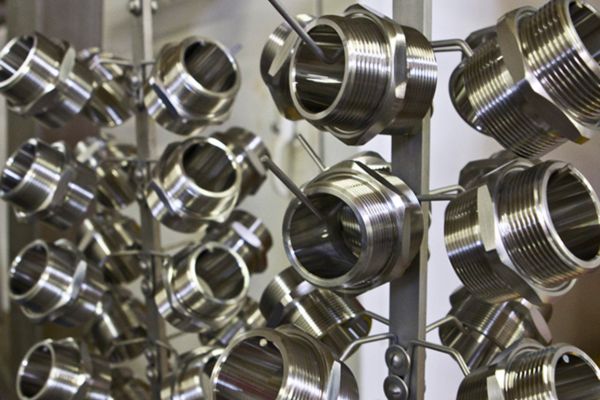
The Benefits of Anodized Aluminum
Enhanced corrosion resistance
One of the primary benefits of anodizing aluminum is its enhanced resistance to corrosion. The thickened oxide layer acts as a protective shield, preventing moisture, chemicals, and salts from penetrating the surface of the aluminum. This is especially valuable in outdoor and industrial settings where aluminum fittings are exposed to harsh weather conditions, pollution, and corrosive environments like coastal areas or chemical processing facilities.
Because the anodized layer is part of the aluminum itself, it won’t chip or peel off like paint, making anodizing the ideal choice for long-term corrosion protection.
Improved wear resistance
Anodizing also significantly improves the wear resistance of aluminum. The aluminum oxide layer is incredibly hard—much harder than the base metal itself. This makes anodized aluminum highly resistant to scratches, dents, and abrasions, making it perfect for applications where the material will endure frequent handling, friction, or exposure to wear and tear.
For example, anodized aluminum is often used in aerospace and automotive applications where parts are exposed to high levels of mechanical stress and environmental conditions.
Aesthetic enhancements
Anodizing aluminum isn’t just about function; it can also enhance the material’s visual appeal. The anodizing process can create a range of finishes, from a subtle matte or satin look to more vibrant, colored surfaces. By incorporating dyes into the anodizing process, aluminum can be anodized in a range of colors, including black, bronze, gold, blue, and more.
The coloring process is deeply integrated into the oxide layer, meaning the colors are permanent and resistant to fading. This is why anodized aluminum is often used in consumer goods like electronics, kitchenware, and architectural features, where both aesthetic appeal and performance are important.
Hard anodizing vs. Decorative anodizing
While both hard anodizing and decorative anodizing create an oxide layer on the aluminum’s surface, there are distinct differences between the two.
Hard anodizing is a thicker, more robust form of anodizing. It is often used when the goal is to improve the aluminum’s mechanical properties, such as increasing its hardness and wear resistance. This type of anodizing is ideal for industrial applications where the aluminum parts will be subject to heavy use, like in the aerospace or automotive sectors.
Decorative anodizing is thinner and typically used for aesthetic purposes. It enhances the appearance of the aluminum, making it more attractive, while still offering some level of corrosion resistance. This type is commonly used for products like furniture, electronics, and architectural finishes.
Understanding the difference between these two types of anodizing is crucial in selecting the right treatment for your aluminum fittings, as the required level of durability or appearance will dictate the type of anodizing process.
Powder Coating Aluminum
What Is Powder Coating for Aluminum Fittings?
Powder coating is a dry finishing process that involves applying a fine powder to the surface of aluminum fittings. The powder, made from a mixture of resin, pigment, and additives, is electrostatically charged and sprayed onto the aluminum surface. Once applied, the powder-coated fittings are heated in an oven, causing the powder to melt, fuse, and form a tough, durable coating.
Unlike traditional liquid paints, which contain solvents and need to be applied in multiple layers, powder coating is more efficient, produces a thicker, more consistent finish, and doesn’t release harmful fumes. The result is a highly protective, smooth finish that is both aesthetically pleasing and long-lasting.
Advantages of Powder Coating Over Other Aluminum Finishes
Superior Durability and Wear Resistance
Powder coating creates a hard, protective layer that is highly resistant to scratches, chips, and abrasions. This makes it ideal for aluminum fittings that will be exposed to heavy use or harsh environments. The tough finish can withstand impacts better than most other types of finishes, such as paints, which tend to chip and peel over time.
Excellent Corrosion Protection
One of the standout benefits of powder coating is its superior resistance to corrosion. The thick coating forms a barrier between the aluminum and environmental elements such as water, chemicals, and UV rays, making it much less likely to corrode compared to untreated or anodized aluminum. This makes powder coating an excellent option for outdoor, marine, or industrial applications where aluminum fittings are exposed to the elements.
Environmentally Friendly
Powder coating is a more eco-friendly finish compared to other methods. It contains no solvents or harmful chemicals, making it safer for both the environment and the workers applying it. Additionally, any excess powder that doesn’t adhere to the aluminum can be collected and reused, reducing waste.
The Power of Aluminum Plating
How Aluminum Plating Enhances Corrosion Resistance
Aluminum plating is an excellent method for improving the corrosion resistance of aluminum fittings. The plating process involves applying a thin layer of another metal (typically nickel, chrome, or zinc) to the surface of the aluminum. This layer forms a barrier that shields the aluminum from environmental factors like moisture, chemicals, and extreme temperatures—elements that can cause oxidation and corrosion.
Aluminum itself is naturally resistant to corrosion due to the formation of a thin oxide layer on its surface. However, in some harsh environments or industrial applications, this natural protection may not be enough. By adding a metal plating, such as nickel or chrome, the aluminum fittings receive an additional layer of protection, making them even more resistant to rust and corrosion. This is especially important in industries where the components will be exposed to chemicals, saltwater, or other corrosive agents.
For example, nickel-plated aluminum has excellent corrosion resistance, making it ideal for components that must withstand humid or salty environments, such as in marine or automotive applications. Additionally, the plating helps to protect the base material from wear and tear, ensuring the aluminum parts last longer and perform more efficiently.
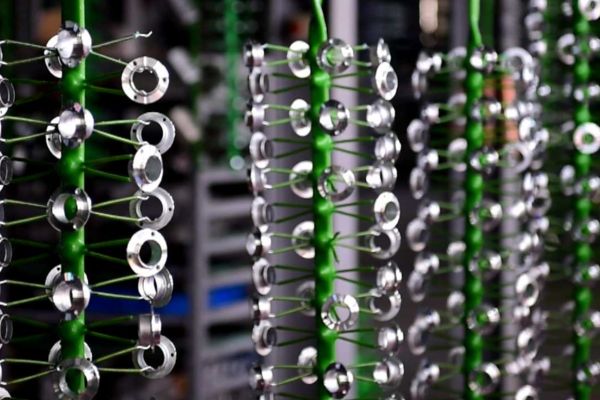
Types of Aluminum Plating
There are several different methods of aluminum plating, each offering specific advantages depending on the intended application and performance needs of the aluminum fittings.
Electroplating
Electroplating is the most common method of plating aluminum and involves using an electric current to deposit a thin layer of metal (often nickel, chrome, or gold) onto the aluminum surface. The process involves immersing the aluminum in a solution containing metal ions and passing an electrical current through the solution, causing the metal to adhere to the surface of the aluminum. Electroplating is used for a variety of applications where improved corrosion resistance and aesthetic appeal are desired.
Hot-Dip Galvanizing
Hot-dip galvanizing involves dipping aluminum components into a molten bath of zinc, which forms a protective coating. While this method is more commonly used for steel, it can be applied to aluminum fittings to offer superior protection against corrosion. The zinc coating bonds with the aluminum, creating a long-lasting barrier that resists rust and wear.
Electroless Plating
Electroless plating is a method that doesn’t require an electrical current to apply the metal coating. Instead, the plating solution contains chemicals that induce a chemical reaction, allowing the metal to deposit onto the aluminum surface. This process is often used to apply nickel, copper, or other metals to aluminum.
Chrome Plating
Chrome plating involves depositing a thin layer of chromium onto the aluminum surface. This not only improves corrosion resistance but also enhances the aesthetic appeal of the aluminum, giving it a mirror-like finish. Chrome plating is often used for high-end applications where both durability and appearance are important.
Aluminum Polishing
The Process of Polishing Aluminum Fittings
Polishing aluminum is a process that smooths the metal’s surface to a high-gloss finish. This involves several steps, each aimed at removing imperfections, scratches, and oxidization from the aluminum surface. The goal is to achieve a shiny, mirror-like surface that not only looks visually appealing but also has enhanced performance characteristics.
Preparation: Cleaning the Surface
Before polishing begins, the aluminum surface must be thoroughly cleaned to remove any dirt, oil, or contaminants. A clean surface ensures that the polishing compounds can work effectively. This cleaning is typically done using mild detergents or specific cleaning solutions designed for metal surfaces.
Sanding: Smoothing Out Imperfections
The next step is sanding. Aluminum parts are typically sanded with a series of progressively finer abrasive papers or pads. This process helps to remove any rough spots, scratches, or oxidation from the metal. Coarse grits are used first to smooth out the surface, followed by finer grits to refine the finish and remove any remaining imperfections.
Polishing: Using Abrasive Compounds
Once the sanding is complete, polishing compounds are applied to the aluminum surface. These compounds contain fine abrasives that help to further smooth the surface and enhance its shine. Typically, a rotary polisher or buffing wheel is used in this stage to achieve a smooth and reflective finish. The polishing compound is spread onto the wheel, and the aluminum part is buffed to a high gloss. The type of polish used depends on the desired level of shine, with some compounds designed for achieving mirror-like finishes and others intended for satin or matte finishes.
Finishing Touch: Sealing the Surface
To preserve the polished finish and protect the surface, a sealing or protective layer may be applied. This could be a clear protective coating or an anodized layer to prevent tarnishing or oxidation. This step is especially important if the aluminum will be exposed to harsh environments, as it can help maintain the reflective surface for longer.
Chemical Film for Aluminum
What Is Chemical Film and How Is It Applied?
Chemical film, also known as chromate conversion coating or Alodine, is a thin protective layer applied to aluminum fittings to enhance their resistance to corrosion. This coating is created through a chemical reaction in which the aluminum surface is treated with a solution containing chromates or other chemicals. Unlike anodizing, which involves an electrolytic process, chemical film creates a more uniform coating without altering the aluminum’s surface thickness. The coating bonds chemically with the aluminum to form a thin, protective layer.
The Application Process:
Cleaning: The aluminum surface must first be thoroughly cleaned to remove any dirt, oil, or oxidation. This is typically done with an acid solution or detergent designed for aluminum.
Chemical Bath: The cleaned aluminum is then submerged in a chemical bath containing a chromate solution. During this process, the chromates react with the surface of the aluminum, forming a protective layer. This coating is very thin, often just a few microns thick.
Rinsing and Drying: After the aluminum is coated, it is rinsed and dried to ensure the coating is stable and free of excess chemicals.
Sealing (Optional): In some cases, the chemical film can be further sealed with an additional coating to enhance its protective qualities, although the film itself is usually sufficient for most applications.
Chemical film coatings are available in various colors, typically shades of gold, yellow, or clear, providing a range of aesthetic options depending on the application.
Advantages of Chemical Film for Aluminum Fittings
Superior Corrosion Protection
The primary benefit of a chemical film coating is its ability to provide excellent corrosion resistance. By creating a protective barrier on the surface of the aluminum, the coating prevents moisture, salt, and other corrosive agents from attacking the metal. This makes it ideal for aluminum fittings exposed to harsh environments, such as marine, automotive, and industrial applications. The thin, effective coating offers protection without compromising the dimensional tolerances of the aluminum.
Lightweight and Thin Coating
Unlike other protective coatings that add bulk or thickness to the aluminum, the chemical film layer is incredibly thin, which helps maintain the original weight and size of the part. This is particularly important in industries like aerospace or automotive, where minimizing weight is crucial to performance.
Enhanced Paint Adhesion
One of the advantages of chemical film is its ability to improve the adhesion of paint and other coatings. The chemical film provides a rougher surface for paints to adhere to, ensuring that the painted finish lasts longer and performs better. This makes it a popular choice for aluminum parts that will be painted, such as in the aerospace and construction industries.
Electrical Conductivity
Chemical film coatings are often used in applications where electrical conductivity is still required. Unlike anodizing, which insulates the aluminum surface, the thin chemical film layer does not significantly affect the electrical conductivity of the metal. This makes it suitable for components in electrical systems, including connectors, circuit boards, and more.
Mechanical Finishes
What Are Mechanical Finishes for Aluminum Fittings?
Mechanical finishes for aluminum fittings involve using physical methods to alter the surface texture and appearance of the metal. Unlike chemical treatments like anodizing or plating, mechanical finishes typically involve abrasive techniques or tools that physically modify the surface, such as sanding, brushing, or blasting. These methods can be used to achieve various textures and effects, from a smooth matte finish to a more rugged, industrial look.
Mechanical finishing is an essential process in industries where aesthetics, performance, and durability are important. These finishes improve the functionality of the aluminum by enhancing its resistance to wear and corrosion, while also offering specific design features that align with the product’s intended use.
Some of the key mechanical finishing techniques used for aluminum fittings include brushing, sanding, bead blasting, and polishing, each offering distinct benefits based on the desired outcome.
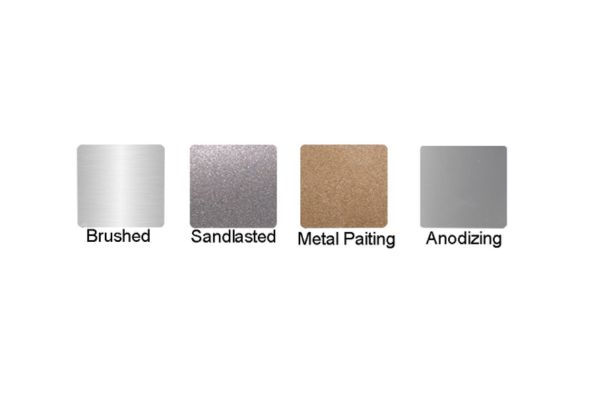
Common Types of Mechanical Finishes
Brushed Finish
A brushed finish is achieved by using a fine abrasive to create parallel, uniform scratches on the surface of the aluminum. The result is a smooth, matte texture with a slight sheen, often referred to as a satin finish. Brushed finishes are widely used in both functional and decorative applications, giving the aluminum an industrial look without being too reflective.
Advantages of Brushed Finish:
Aesthetic appeal: Offers a sleek, modern look while hiding fingerprints and scratches.
Scratch resistance: The texture helps to mask surface imperfections, making it a popular choice for items that undergo regular use, such as appliances, furniture, and automotive parts.
Non-reflective: The brushed surface does not create glare, making it ideal for parts used in bright environments.
Sandblasted Finish
Sandblasting, or bead blasting, involves propelling small abrasive particles (often silica sand or glass beads) against the surface of the aluminum at high velocity. This creates a uniform, matte, slightly textured finish. Sandblasting is often used when a more rustic or industrial look is desired, as it creates a rougher, less polished texture compared to other finishes.
Advantages of Sandblasted Finish:
Textural enhancement: Ideal for creating a matte or satin finish with a distinct texture.
Enhanced grip: Sandblasted aluminum has a rougher surface that provides a better grip, making it useful for items like handrails, tool handles, or any part requiring friction or traction.
Durability: The surface is more resistant to corrosion and oxidation due to the rough texture that helps to hold protective coatings better.
Polished Finish
Polishing aluminum fittings involves smoothing the surface to a high gloss. This is often done using buffing wheels and polishing compounds. The result is a shiny, mirror-like finish that can significantly improve the aesthetic appeal of aluminum parts. Polishing can be done either by hand or with machinery and is commonly used for high-end products or where a reflective surface is required.
Advantages of Polished Finish:
Reflective appearance: Provides a mirror-like shine that is visually striking.
Smooth texture: Reduces the risk of corrosion and improves surface cleanliness by creating a smooth, non-porous layer.
Aesthetic appeal: Polished aluminum is often used in luxury goods, automotive parts, and consumer electronics to create a high-end look.
Shot Peening
Shot peening is a process where tiny spherical media (often steel or ceramic) are blasted at the aluminum surface to induce compressive stresses. This process doesn’t just alter the texture but strengthens the material by improving its fatigue resistance. It’s often used in aerospace, automotive, and industrial applications where the aluminum parts need to resist high stress and cyclic loading.
Advantages of Shot Peening:
Increased strength: The compressive stress improves the material’s fatigue resistance, making it more durable in high-stress environments.
Resistance to cracking: Helps to reduce the likelihood of cracking or surface failure under stress.
Improved lifespan: Ideal for aluminum fittings that will undergo repeated stress or mechanical loading, such as engine parts or components in high-performance machines.
Conclusion
Ultimately, investing in the right surface finishing for aluminum fittings ensures that your components not only perform better but also last longer, offering significant cost savings over time. Whether you are in aerospace, automotive, construction, or any other industry, selecting the right surface treatment can give you the durability, aesthetics, and protection your aluminum fittings need to thrive in even the most demanding conditions.
FAQ
What is aluminum anodizing?
Anodizing is an electrochemical process that creates a protective oxide layer on the surface of aluminum. This increases corrosion resistance, wear durability, and allows for a range of aesthetic finishes.
How does powder coating differ from anodizing?
While both processes protect aluminum, powder coating involves applying a dry powder that is cured to form a thick, colorful finish, offering better impact resistance. Anodizing, on the other hand, forms a durable oxide layer that enhances corrosion resistance and can provide various aesthetic effects but doesn’t add thickness like powder coating.
Why is aluminum plating used?
Aluminum plating, typically done through electroplating or thermal spraying, provides an additional layer of aluminum over another metal to increase corrosion resistance, improve wear resistance, and give a smooth, reflective surface.
Can aluminum plating be used for decorative purposes?
Yes, aluminum plating is often used for decorative purposes, especially in automotive, electronics, and consumer products. The shiny finish provides aesthetic appeal while also offering protection against corrosion.
Is anodizing aluminum a permanent finish?
Yes, anodizing is a permanent finish because the oxide layer forms as part of the aluminum itself, making it resistant to chipping, peeling, or fading over time.
Which aluminum surface treatment is best for marine applications?
For marine applications, aluminum anodizing or aluminum plating are ideal because they offer superior corrosion resistance in salty, humid environments, extending the lifespan of aluminum fittings.