Your toughest hydraulic jobs demand a fitting that won’t fail under extreme pressure. But choosing the right high-pressure fitting can be confusing and risky.
77 Series fittings are robust, one-piece, steel crimp fittings designed for high-pressure four and six-wire spiral hydraulic hoses. They provide an extremely reliable, factory-quality connection for demanding applications in construction, mining, and heavy industry.
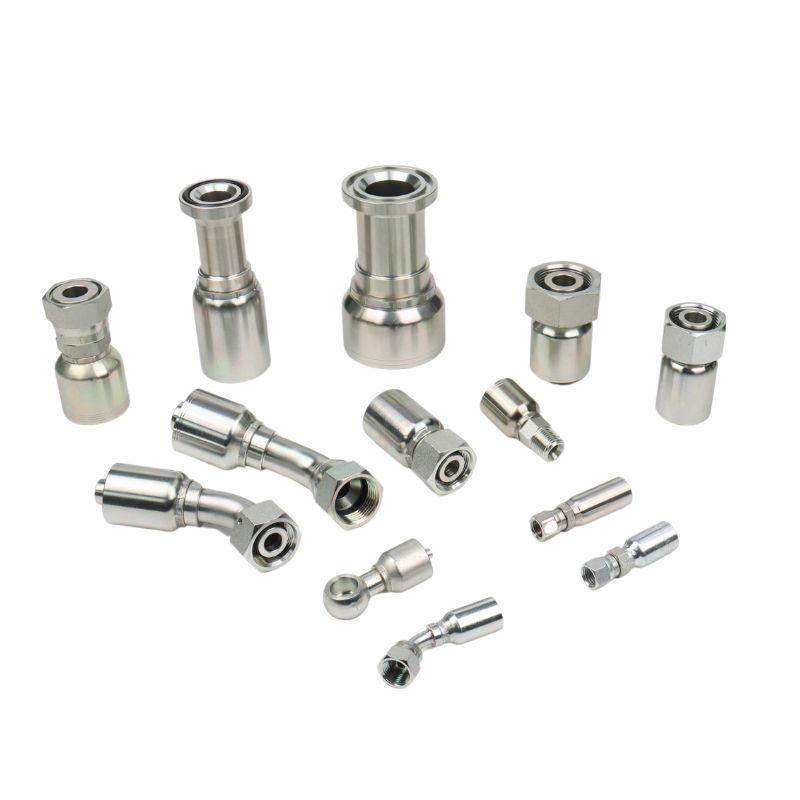
What Exactly Defines a “77 Series” Hydraulic Fitting?
You see the “77 Series” part number but what does it mean? Not knowing the specifics can lead to costly mismatches with your hoses and applications.
A 77 Series fitting is a high-pressure, non-skive hydraulic fitting, typically made from a single piece of steel. It’s designed specifically for the extreme demands of four and six-wire spiral hoses, ensuring a strong, durable, and leak-free crimped connection.
The name “77 Series” has become an industry term for a specific type of heavy-duty fitting. When you encounter it, you should immediately think of high-pressure, high-demand applications. It’s not a fitting for general-purpose use; it’s a specialist piece of engineering. Several key design features set it apart from the more common fittings used on standard two-wire hoses. Understanding these features is key to understanding its purpose and its value.
The Non-Skive Advantage
The most important feature is that these are “non-skive” fittings. In the past, to assemble a fitting on a high-pressure spiral hose, you had to first “skive” or shave off the outer rubber cover of the hose to expose the wire reinforcement. This was a time-consuming, messy, and inconsistent process. A 77 Series fitting is designed with an aggressive inner profile on its ferrule (the outer collar) that is engineered to bite through the outer cover and grip the wire reinforcement directly. This dramatically simplifies and speeds up the assembly process, reduces the chance of human error, and protects the wire reinforcement from being damaged by the skiving tool.
One-Piece Steel Construction
Unlike some other fitting designs that use a separate ferrule and nipple (the part that goes inside the hose), 77 Series fittings are typically a robust, single-piece design. This integrated construction provides immense strength and integrity. There are fewer potential leak paths, and the fitting is inherently stronger and more resistant to the immense forces created by high-pressure hydraulic impulses. They are made from high-tensile steel and are zinc-plated to resist corrosion, ensuring they can stand up to the harsh environments where they are used.
Which Hydraulic Hoses Are Compatible With 77 Series Fittings?
You have a high-pressure hose, but will a 77 Series fitting work? Using the wrong hose can lead to immediate and dangerous assembly failure.
77 Series fittings are not for standard two-wire braided hoses. They are specifically engineered to match the dimensions and pressure ratings of heavy-duty four and six-wire spiral hydraulic hoses, such as those meeting EN 856 4SP, 4SH, or SAE 100R13/R15 standards.
This is the most critical point of all. A hydraulic fitting and hose must be a matched set. Using a 77 Series fitting on the wrong hose is like putting racing tires on a farm tractor; the components are not designed for each other and the result will be a catastrophic failure. I see this mistake made by people trying to save money, but it ends up costing far more in the long run. The internal construction of a spiral hose is very different from a braided hose, and the 77 Series fitting is designed to work with that specific construction.
Understanding Spiral Hose Construction
Standard hydraulic hoses use layers of braided wire for reinforcement. High-pressure hoses use a different method where multiple layers of steel wire are spiraled around the inner tube. This spiral construction is better at handling the extremely high pressures and pressure impulses found in heavy equipment. However, the hose wall is thicker and less flexible. The 77 Series fitting is designed with a longer ferrule and specific internal geometry to correctly grip these multiple, non-flexible layers of wire.
Matching the Standards for Safety
You must always match the fitting to the hose standard. The 77 Series is a perfect partner for the most common types of spiral hose used globally.
Hose Series | Hose Description | Compatible Dash Sizes | Notes |
387 | Compact Wire Braid Hose | -20, -24, -32 | Only large sizes compatible with 77 Series |
487 | High-Pressure Wire Braid Hose | -20, -24, -32 | Same as 387, only large sizes are supported |
787 | Compact Spiral Hose | -8 through -32 | Designed for high-pressure spiral applications |
797 | Super Tough Spiral Hose | -8 through -32 | Tough cover for harsh environments |
Using a 77 Series fitting with these approved hoses ensures the assembly can meet the pressure rating of the hose itself. As a supplier, we at Topa always provide clear compatibility charts to ensure our customers get this critical decision right every time.
What Are the Core Benefits of Using 77 Series Fittings?
Is this heavy-duty fitting worth the cost? You need connections that prevent downtime, but the investment must be justified by clear performance advantages.
The primary benefits are extreme reliability and safety under very high dynamic pressures. The non-skive, one-piece design simplifies assembly, reduces errors, and creates a robust connection that resists vibration and impulse shock, ensuring longer service life in critical applications.

When a piece of mining or heavy construction equipment goes down, the costs are enormous. The decision to use a premium fitting like the 77 Series is an investment in uptime and safety. The benefits go beyond just holding pressure; they address the real-world challenges faced by operators and maintenance teams.
Enhanced Safety and Reliability
This is the number one benefit. In applications with pressure spikes reaching 5000 or 6000 PSI, you cannot afford a connection to fail. The robust, one-piece design and the deep, secure bite of the non-skive ferrule create a connection with an extremely high resistance to blow-off. This provides peace of mind for operators and managers, knowing that the hydraulic connections are one of the most secure parts of the system.
Faster and Simpler Assembly
For maintenance teams working in the field, time is money. As I mentioned, the non-skive design eliminates the slow and messy process of shaving the hose cover. This not only makes the assembly process about five times faster but also removes a major source of potential error. A consistent, repeatable assembly process means more reliable results, even when performed under pressure in field conditions. This benefit appeals to both my quality-focused customers in Europe and my price-sensitive customers in Africa, because reduced labor time and fewer bad assemblies save money for everyone.
Superior Impulse Life
These fittings are not just designed for static pressure; they are designed to survive the brutal reality of hydraulic impulse shocks. The long ferrule supports the hose behind the crimp, helping to distribute the stress from bending and vibration. This results in an assembly that can withstand hundreds of thousands of pressure impulse cycles, which is critical for the longevity of hoses on equipment like bulldozers, excavators, and forestry machines.
How Do You Properly Assemble a 77 Series Fitting?
You have the right parts, but the assembly process is critical. One wrong step can compromise the entire hose assembly, creating a hidden weakness.
Proper assembly involves a clean, square cut of the hose, marking the insertion depth, pushing the fitting on until the mark is met, and crimping with the correct die set in a calibrated crimper to the manufacturer-specified diameter.

The strength of a 77 Series fitting is only realized if it is assembled correctly. This is not a process to be rushed. Following a precise, step-by-step method is essential for safety and reliability.
Step 1: Select Components and Cut the Hose
Ensure you have the correct 77 Series fitting for your specific spiral hose type and size. Use a proper abrasive hose saw to cut the hose to length. The cut must be clean and perfectly square (90 degrees). A crooked cut will prevent the hose from bottoming out correctly inside the fitting.
Step 2: Mark Insertion Depth
Many 77 Series fittings (and their equivalents) have a feature on the ferrule that indicates how far to push it onto the hose. If not, you must measure. Push the fitting all the way onto the hose until it stops. Then, using a white or silver paint pen, make a clear mark on the hose right at the back of the fitting’s collar.
Step 3: Lubricate and Insert the Fitting
Remove the fitting. Apply a light amount of hydraulic oil or an appropriate lubricant to the inside of the fitting’s nipple and the inside of the hose. This is crucial for spiral hose, as it helps the nipple slide in without damaging the hose’s inner tube. Push the fitting onto the hose until the back of the collar meets your pen mark.
Step 4: Crimp with Correct Dies
Select the specific die set recommended by the manufacturer for your hose and fitting combination. Place the assembly in the crimper and crimp it. You will need a powerful, robust crimper capable of handling the large diameters and thick steel of these fittings.
Step 5: Verify the Crimp Diameter
This is the final, essential quality check. Use a set of calipers to measure the outside diameter of the crimped ferrule. Compare this measurement to the crimp specifications provided by the fitting manufacturer. It must be within the specified tolerance. If it is too big (under-crimped) or too small (over-crimped), the assembly is unsafe and must be cut off and discarded.
Are There High-Quality Alternatives to Brand-Name 77 Series Fittings?
You need the performance of 77 Series but your budget is tight. Are you forced to pay premium brand prices for this level of quality?
Yes. Reputable manufacturers like us at Topa produce high-quality equivalent fittings that are fully compatible with the same spiral hoses. These alternatives are rigorously tested to meet or exceed international standards, offering the same safety and performance at a more competitive price point.
This is a very common question, especially from smart buyers like Tony who need to balance performance with cost. The original equipment manufacturer (OEM) brand is excellent, but it carries a premium price tag. For many businesses, sourcing a high-quality, fully tested equivalent is a smart financial decision, as long as you choose your supplier carefully. The key is to ensure you are buying a true equivalent, not a cheap, untested copy.
The Value of a Reputable Alternative
When you choose an alternative supplier like Topa, you should demand proof of quality. We provide our customers with full documentation, including material specifications and results from our own rigorous testing protocols. We perform burst tests and, crucially, impulse tests on our assemblies to validate that they perform just as well as the brand-name products. A reputable supplier will be transparent about their quality control and will stand behind their product.
Performance Without the Price Tag
How can we offer this performance at a better price? Our business model is focused on efficiency. By working directly with customers around the world, from the USA to Ghana, we eliminate layers of distribution markups. Our lean manufacturing partnerships and dedicated marketing and service teams mean we can deliver a world-class product without the overhead of a giant global corporation. You are paying for quality engineering, not for a brand name. We provide a complete matched system—our hoses, our fittings, and our crimp specifications—to give our clients total peace of mind.
What Common Mistakes Should You Avoid With 77 Series Fittings?
You’ve built your assembly, but hidden errors can lead to failures. Knowing the common pitfalls is key to ensuring long-term reliability and safety.
The biggest mistakes are using them on the wrong hose type (like 2-wire), under-crimping or over-crimping, failing to push the hose fully into the fitting before crimping, and not using a properly calibrated crimper with the correct die set.
Making any of these mistakes completely negates the safety and reliability you are trying to achieve by choosing a heavy-duty fitting in the first place. An improperly assembled 77 Series fitting is just as dangerous, if not more so, than a standard fitting used correctly.
Mistake 1: Hose and Fitting Mismatch
This is the most fundamental error. I must repeat it: Never use a 77 Series fitting on a 2-wire braided hose (like SAE 100R2). The fitting is not designed to grip the braided reinforcement correctly and will almost certainly fail by blowing off under pressure.
Mistake 2: Incorrect Crimp Diameter
This is the most common assembly error. It’s critical to use calipers and verify every single crimp.
Crimp Error | What It Means | The Dangerous Result |
Under-Crimp | The crimp diameter is too large. | Not enough grip. The hose can blow out of the fitting. |
Over-Crimp | The crimp diameter is too small. | Too much force. The wire reinforcement is crushed and cut. |
Mistake 3: Incomplete Hose Insertion
If you do not push the hose all the way into the fitting until it bottoms out (and your mark lines up), the ferrule will be crimped onto the wrong part of the hose. The teeth of the ferrule are designed to bite into the hose directly over the nipple, creating a unified seal. A partial insertion creates a massive weak point right at the end of the nipple, which will lead to a very early failure.
Conclusion
77 Series fittings offer unmatched reliability for high-pressure spiral hose applications. Choosing a quality-tested, compatible system ensures safety and performance while providing excellent value for your business.
FAQ
What are 77 series crimp fittings used for?
77 series crimp fittings are used to securely connect hoses in high-pressure hydraulic systems, ensuring leak-free and durable connections.
What types of hoses are compatible with 77 series crimp fittings?
The 77 Series is compatible with various hose types, including braided, spiral, and thermoplastic hydraulic hoses.
What materials are 77 series crimp fittings made from?
These fittings are commonly made from carbon steel and stainless steel, with options for plated finishes to enhance corrosion resistance.
How do I choose the right 77 Series Crimp Fitting?
Consider factors like pressure ratings, hose type, and fluid compatibility to match the fitting with your system’s requirements.
What tools are needed to install 77 series crimp fittings?
A hydraulic crimping machine, a die set matching the fitting size, and a hose cutter are essential for proper installation.
Can I use 77 series crimp fittings with any hydraulic fluid?
The fittings are compatible with a wide range of hydraulic fluids, but it’s important to verify that the fitting material matches the fluid type used in your system.