The performance and longevity of hydraulic systems heavily depend on the quality of the hydraulic fluid used. Hydraulic fluids act as the medium for power transmission, but their role extends far beyond this. They also serve as lubricants, reducing wear and tear on internal components, and they help to manage system heat, preventing overheating. However, the quality of hydraulic fluid can degrade over time due to factors like temperature fluctuations, contamination, and oxidation. This degradation can severely impact the effectiveness of hydraulic fittings, leading to corrosion, leaks, and overall system failure if not properly addressed.
Understanding Hydraulic Fluid Degradation
What is Hydraulic Fluid Degradation?
Hydraulic fluid degradation is the process by which hydraulic fluid loses its essential properties and effectiveness over time. This degradation can lead to a host of problems within hydraulic systems, from reduced efficiency to complete system failures. At its core, hydraulic fluid is responsible for transferring energy, lubricating moving parts, and protecting the system from wear and corrosion. However, due to the extreme conditions under which hydraulic systems operate—such as high temperatures, pressure, and exposure to contaminants—the fluid can break down, leading to serious performance issues.
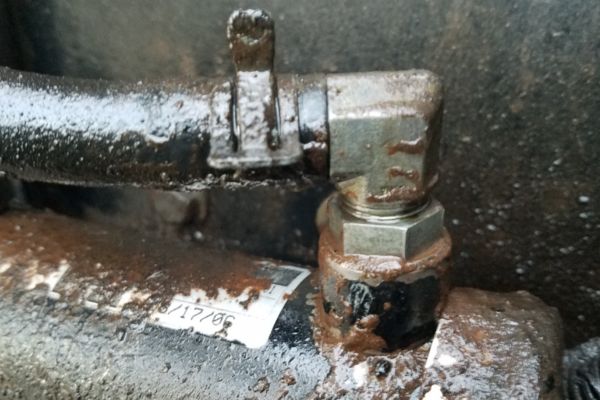
Causes of Fluid Degradation
Several factors contribute to the degradation of hydraulic fluids, each of which can negatively impact the system’s overall performance:
Thermal Breakdown: Hydraulic systems often operate under intense heat, and when hydraulic fluid is exposed to temperatures beyond its tolerance range, its molecular structure begins to break down. This can cause the fluid to lose its ability to lubricate and protect the system. Over time, thermal breakdown results in increased friction and wear on internal components.
Contamination: The presence of contaminants such as water, air, dirt, and metal particles can significantly accelerate the degradation of hydraulic fluid. Water contamination can cause emulsification, which compromises the fluid’s lubricating properties, while dirt and metal particles can lead to abrasive wear within the system. Air contamination, on the other hand, can result in cavitation—small bubbles that collapse under pressure and cause damage to system components.
Oxidation: Oxidation occurs when the hydraulic fluid reacts with oxygen, leading to the formation of acids, sludge, and varnish. This chemical reaction is especially common in systems that operate at high temperatures, as heat accelerates the oxidation process. Oxidized fluids lose their lubricating qualities, become more viscous, and can cause corrosion of metal components, leading to costly damage.
Chemical Reactions: Chemical reactions between hydraulic fluid and the materials in the system, such as seals, hoses, or fittings, can further degrade the fluid. Additives in the fluid can also break down or react with contaminants, changing the fluid’s properties and effectiveness.
Types of Hydraulic Fluids and Their Vulnerabilities
The type of hydraulic fluid used in a system plays a crucial role in determining how quickly degradation may occur. Different fluids are suited to specific operating conditions and environments, and each comes with its vulnerabilities to degradation.
Mineral Oils: Mineral-based hydraulic fluids are the most common type used in industrial applications. They are petroleum-based and typically contain additives that enhance their performance, such as anti-wear agents and oxidation inhibitors. However, mineral oils are particularly susceptible to thermal degradation and oxidation, especially in high-temperature environments. Prolonged exposure to heat can cause these fluids to lose their viscosity, leading to poor lubrication and increased wear on system components.
Synthetic Oils: Synthetic hydraulic fluids are engineered to offer superior performance in extreme conditions. They generally have a higher resistance to thermal breakdown and oxidation compared to mineral oils, making them ideal for applications with high heat and pressure. However, synthetic fluids are not immune to degradation. They can still suffer from contamination issues and may have incompatibilities with certain seals and materials in the hydraulic system, leading to chemical breakdown.
Water-Based Fluids: Water-based hydraulic fluids are often used in applications where fire resistance is critical, such as in mining or steel production. These fluids contain a significant proportion of water, which makes them less flammable. However, their vulnerability to water contamination is their greatest weakness. Water-based fluids are prone to emulsification and microbial growth, which can quickly degrade their performance. Additionally, water promotes corrosion of metal components, further accelerating system wear and tear.
How Different Fluids Degrade Over Time Under Varying Conditions
The rate of degradation for hydraulic fluids depends on the specific operating conditions of the system. In systems that operate under extreme heat and pressure, even the most resilient fluids can degrade rapidly. For example, synthetic fluids may hold up better than mineral oils under these conditions, but over time, repeated exposure to high temperatures will eventually lead to chemical breakdown.
Contaminated environments also significantly accelerate the degradation process. Fluids that are exposed to high levels of dirt, dust, or moisture will degrade faster due to the introduction of foreign particles and substances that interfere with the fluid’s ability to lubricate and protect. Water contamination, in particular, can be a major issue for water-based fluids, as it can quickly lead to corrosion, emulsification, and microbial growth.
Common Warning Signs of Fluid Degradation
Hydraulic fluid degradation often occurs gradually, but there are several warning signs that operators can detect early to prevent system damage and costly repairs. These signs manifest in the form of visual cues, changes in system performance, and even odors that indicate something is wrong. By paying attention to these indicators, maintenance personnel can address issues before they escalate into serious problems.
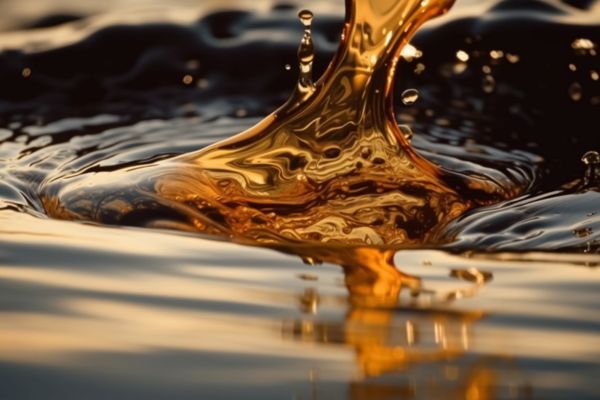
Visual Indicators
One of the most apparent ways to identify fluid degradation is through visual inspection. The appearance of the hydraulic fluid can reveal much about its condition, making regular fluid checks a crucial part of hydraulic system maintenance.
Changes in Fluid Color
Hydraulic fluid typically has a clear or amber appearance when it is in good condition. Over time, as the fluid degrades, it may become darker, taking on a brown or black hue. This darkening is often a sign of oxidation or contamination by dirt, metal particles, or other foreign substances. Discoloration can also indicate thermal breakdown, where the fluid has been exposed to excessive heat, causing its molecular structure to deteriorate.
Appearance of Particles, Foam, or Sediment
Another visual sign of fluid degradation is the presence of visible contaminants, such as dirt, metal shavings, or sediment, in the hydraulic fluid. These particles can clog the system, leading to increased wear on components and reduced efficiency. Additionally, foam or bubbles within the fluid can indicate air contamination, which can cause cavitation and lead to further damage to the system. These visible signs are often the result of prolonged exposure to contaminants or improper sealing of the system.
Unusual Viscosity
Hydraulic fluid should maintain a consistent viscosity to ensure proper lubrication and system performance. Degraded fluid often becomes either too thick or too thin. Thicker fluid may indicate that it has oxidized or absorbed contaminants, while thinner fluid may have lost its ability to provide adequate lubrication, often due to thermal breakdown or dilution with water. In either case, abnormal viscosity can lead to increased friction, wear, and eventual system failure.
Performance-Based Warning Signs
Fluid degradation also manifests in the overall performance of the hydraulic system. These performance issues are often more subtle than visual cues but are just as crucial to identify early on.
Decreased System Efficiency or Sluggish Operation
One of the most common symptoms of degraded hydraulic fluid is a noticeable decline in system efficiency. The machinery may become sluggish, responding more slowly to commands and operating with reduced power. This is often due to the fluid’s inability to effectively transmit power throughout the system, resulting in reduced hydraulic pressure and slower component movement.
Increased Noise or Vibrations in the Hydraulic System
Another warning sign is the presence of unusual noises or vibrations during operation. These can indicate several issues related to fluid degradation, including air contamination, increased friction due to poor lubrication, or cavitation caused by the breakdown of fluid properties. These noises, which may sound like knocking, whistling, or chattering, are a clear indication that the fluid is no longer functioning as intended and is causing abnormal stress on system components.
Excessive Heat Buildup in the System
Hydraulic fluids help to dissipate heat within the system, ensuring that components do not overheat. However, when the fluid degrades, it loses its ability to manage heat effectively. This can lead to excessive heat buildup within the system, which may be observed through higher-than-normal operating temperatures. If left unaddressed, this heat can cause further degradation of the fluid and damage to system components, eventually leading to system failure.
Odor and Smell Changes
In addition to visual and performance-based indicators, the smell of the hydraulic fluid can provide valuable clues about its condition. Changes in odor often signal chemical breakdown or contamination within the fluid.
Presence of Burnt, Rancid, or Chemical Odors
A burnt smell is often associated with thermal breakdown, where the fluid has been exposed to excessive heat for extended periods. This odor suggests that the fluid’s molecular structure has been compromised and that it is no longer providing adequate lubrication or protection to the system.
Rancid odors, on the other hand, can indicate contamination by water or microbial growth, especially in systems using water-based fluids. Microbes can thrive in such environments, leading to foul-smelling, degraded fluid that can cause corrosion and blockages within the system.
Chemical odors often point to oxidation or the breakdown of additives within the fluid. These smells suggest that the fluid’s chemical composition has changed, which can lead to increased wear on seals, gaskets, and other system components.
Impact of Fluid Degradation on Hydraulic Fittings
Hydraulic fluid degradation can have a profound impact on the overall health and performance of hydraulic systems. While the fluid itself is essential for transmitting power and lubricating components, its degradation directly affects the integrity of hydraulic fittings. These fittings are crucial connectors in the system, and when exposed to degraded fluid, they can experience accelerated wear, corrosion, sealing failures, and system leaks. Understanding the specific ways fluid degradation compromises hydraulic fittings is key to preventing system failures and maintaining operational efficiency.
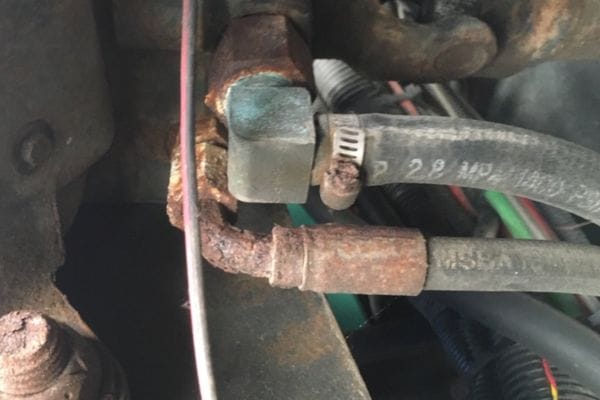
Corrosion and Wear on Fittings
One of the most significant consequences of hydraulic fluid degradation is the accelerated corrosion and wear of metal fittings. Hydraulic fittings are typically made of materials like steel, brass, or stainless steel, which are vulnerable to corrosion when exposed to contaminated or chemically degraded fluid.
How Degraded Fluid Accelerates Corrosion on Metal Fittings
As hydraulic fluid degrades, it often becomes contaminated with water, dirt, metal particles, and other foreign substances. Water contamination, in particular, is a leading cause of corrosion in metal fittings. The presence of water in the fluid can lead to the formation of rust and other corrosive by-products, which weaken the metal over time. Once corrosion begins, it can spread rapidly, compromising the structural integrity of the fittings and making them more susceptible to leaks and failure.
Chemical Reactions Between Degraded Fluids and Hydraulic Fitting Materials
In addition to corrosion caused by water, degraded hydraulic fluids can undergo chemical reactions that adversely affect fittings. For example, the oxidation of hydraulic fluid leads to the formation of acids, which can corrode metal surfaces. These chemical reactions can also attack the protective coatings or finishes on fittings, leaving them vulnerable to further corrosion and degradation. Over time, these reactions reduce the lifespan of the fittings, leading to premature failure and costly repairs.
Sealing Failures
Seals, O-rings, and gaskets play a critical role in maintaining the integrity of hydraulic systems by preventing leaks and ensuring a proper connection between components. However, when hydraulic fluid degrades, it can cause the breakdown of these sealing elements, leading to significant performance issues.
Breakdown of Seals, O-rings, and Gaskets Due to Contamination or Chemical Interactions
Degraded fluid often contains contaminants such as dirt, debris, and chemical by-products that can cause physical damage to seals, O-rings, and gaskets. For example, dirt particles can become trapped in these seals, causing them to wear down and lose their effectiveness. Additionally, chemical interactions between degraded fluid and the materials used in seals (such as rubber or elastomers) can cause the seals to become brittle, swell, or crack. This degradation results in a loss of flexibility and sealing capability, making it difficult for the system to maintain pressure.
Leakage and Its Connection to Fluid Degradation
One of the most immediate consequences of sealing failures is fluid leakage. As seals break down and lose their effectiveness, hydraulic fluid can escape from the system at the points where fittings and other components are connected. Leaks not only reduce the efficiency of the system but also introduce safety hazards, especially in environments where hydraulic systems power heavy machinery or industrial equipment. Over time, fluid leakage can lead to a significant loss of pressure and power, further degrading the performance of the hydraulic system.
Pressure Imbalance and System Leaks
Maintaining consistent pressure is critical for the proper functioning of hydraulic systems. When hydraulic fluid degrades, it can lead to pressure imbalances within the system, increasing the risk of leaks around fittings and other components.
How Degraded Fluid Leads to Pressure Fluctuations
Degraded fluid often exhibits changes in viscosity, contamination with particles, and chemical breakdown, all of which can interfere with the fluid’s ability to maintain consistent pressure. Thicker fluid, for example, may cause blockages or increase friction within the system, leading to pressure spikes. Conversely, thinner fluid may be unable to maintain the necessary pressure levels, resulting in system inefficiencies. These fluctuations can cause excessive stress on hydraulic fittings, increasing the likelihood of leaks and other failures.
Increased Risk of Leaks Around Fittings Due to Pressure Imbalance
Pressure imbalances in the system often manifest as leaks around fittings. When the system is unable to maintain stable pressure, fittings may loosen or become dislodged, creating small gaps where fluid can escape. These leaks further compromise the system’s performance, leading to a vicious cycle of pressure loss and additional fluid degradation. Moreover, pressure fluctuations can accelerate the wear and tear on fittings, increasing the risk of catastrophic failures if left unaddressed.
Preventive Measures to Combat Fluid Degradation
Preventing hydraulic fluid degradation is essential to ensuring the long-term efficiency and reliability of hydraulic systems. By implementing proper storage, handling, and maintenance practices, operators can minimize the risk of fluid degradation and its negative impact on system performance.
Proper Fluid Storage and Handling
One of the first lines of defense against hydraulic fluid degradation is ensuring that fluids are properly stored and handled before they are introduced into the hydraulic system. Poor storage practices can expose hydraulic fluid to contaminants such as dirt, water, and air, all of which can accelerate degradation once the fluid is in use.
Guidelines for Storing Hydraulic Fluids to Prevent Contamination
Hydraulic fluids should always be stored in a clean, dry environment away from potential sources of contamination. The storage area should be free from dust, dirt, and other airborne particles that could contaminate the fluid. Additionally, it is crucial to keep hydraulic fluids away from chemicals or substances that could react with the fluid, leading to degradation even before the fluid is used.
Fluids should be kept in their original containers until they are ready to be used, as these containers are designed to protect the fluid from environmental exposure. When transferring fluid from one container to another, operators should use clean, designated tools to avoid introducing contaminants into the fluid.
Importance of Using Clean, Sealed Containers and Preventing Moisture Exposure
One of the most common sources of contamination in hydraulic fluids is moisture. Water can easily seep into fluid containers that are not properly sealed, leading to emulsification, corrosion, and microbial growth. To prevent moisture contamination, all hydraulic fluid containers should be tightly sealed when not in use. Additionally, operators should avoid storing fluid in open containers or using containers that have been previously exposed to moisture.
Temperature control is another important factor in fluid storage. Hydraulic fluids should be kept in a temperature-stable environment to prevent condensation from forming inside the containers, which could introduce moisture into the fluid. Ideally, fluids should be stored at room temperature and away from direct sunlight or heat sources that could cause thermal degradation.
Regular Fluid Replacement and System Flushing
Even with the best storage and handling practices, hydraulic fluids will eventually degrade over time due to normal system operation. To prevent degraded fluid from causing damage to the hydraulic system, regular fluid replacement and system flushing should be part of routine maintenance.
Best Practices for Replacing Hydraulic Fluids at Recommended Intervals
Hydraulic fluid replacement intervals depend on the type of fluid used, the operating conditions of the system, and manufacturer recommendations. Operators should follow the fluid manufacturer’s guidelines for replacement intervals to ensure that the fluid remains effective in lubricating, cooling, and protecting system components.
When replacing hydraulic fluid, it is important to remove all of the old, degraded fluid from the system to prevent contamination of the new fluid. This ensures that the new fluid will not be compromised by residual contaminants or degraded additives from the old fluid.
Flushing the System to Remove Degraded Fluid and Contaminants
Flushing the hydraulic system is a critical step in removing degraded fluid and any accumulated contaminants. System flushing involves circulating a cleaning agent or fresh hydraulic fluid through the system to dislodge and remove dirt, particles, sludge, and any other contaminants that have built up over time. Flushing is especially important when changing from one type of hydraulic fluid to another, as it prevents chemical incompatibilities between the old and new fluids.
During flushing, operators should ensure that the entire system, including reservoirs, hoses, filters, and fittings, is thoroughly cleaned. After the flushing process is complete, the system should be refilled with fresh hydraulic fluid to restore optimal performance.
Conclusion
In conclusion, taking a proactive approach to hydraulic fluid management is the key to maintaining system efficiency and preventing failures. Regular inspections, adherence to best practices, and seeking expert consultation will help operators stay ahead of potential issues, ensuring that their hydraulic systems continue to perform at their best.
FAQ
What are the signs of hydraulic fluid degradation?
Common signs include fluid discoloration, unusual odors, the presence of particles, and decreased system performance such as sluggish operation or excessive heat buildup.
How often should the hydraulic fluid be replaced?
Hydraulic fluid should be replaced according to the manufacturer’s recommendations, typically every 1,000 to 2,000 hours of operation, or sooner if signs of degradation are present.
What causes hydraulic fluid to degrade?
Hydraulic fluid can degrade due to factors like thermal breakdown, contamination (water, dirt, air), oxidation, and chemical reactions within the system.
How can I prevent hydraulic fluid degradation?
Proper storage, handling, regular fluid replacement, system flushing, and filter maintenance are key practices to prevent fluid degradation.
Can degraded hydraulic fluid damage fittings?
Yes, degraded fluid can cause corrosion, wear, sealing failures, and pressure imbalances, which may lead to damage or failure of hydraulic fittings.
What should I do if I notice signs of hydraulic fluid degradation?
If you detect signs of fluid degradation, inspect the system, replace the fluid, flush the system if necessary, and consider consulting with a hydraulic expert for further guidance.