The right blade choice directly impacts the quality of the cut, which in turn affects the performance and longevity of the hydraulic system. By selecting the appropriate blade for each type of hose, operators can significantly improve their cutting process, reducing downtime and enhancing the overall safety of the work environment. This post will guide you through the key factors to consider when choosing the right blade, ensuring optimal performance for your hydraulic hose cutting needs.
Understanding Hydraulic Hoses
Types of Hydraulic Hoses
Hydraulic hoses are essential components in hydraulic systems, allowing for the transfer of pressurized fluids to power machinery, industrial equipment, and vehicles. These hoses are constructed from different materials, each tailored to specific applications and environmental conditions.
Rubber Hydraulic Hoses:
Rubber hoses are among the most common and versatile types used in hydraulic systems. They are typically constructed with an inner rubber core, reinforcement layers (usually made of braided steel wire), and an outer rubber cover. Rubber hoses offer flexibility, high-pressure resistance, and good performance in various temperature ranges. They are often used in applications requiring high levels of vibration absorption and movement.
Thermoplastic Hydraulic Hoses:
Thermoplastic hoses consist of a polymer-based core, which is surrounded by layers of synthetic fiber or steel wire reinforcement. Thermoplastic hoses are lighter and more resistant to abrasion compared to rubber hoses. They also offer excellent chemical resistance, making them ideal for applications involving corrosive substances or in environments where weight is a concern, such as mobile equipment.
Teflon (PTFE) Hydraulic Hoses:
Teflon hoses, made from polytetrafluoroethylene (PTFE), are highly resistant to heat, chemicals, and wear. PTFE hoses are commonly used in high-temperature applications or where extreme chemical exposure is expected. Their smooth interior reduces friction and helps maintain fluid flow efficiency. However, they are generally stiffer than rubber or thermoplastic hoses, which can make cutting and handling more challenging.

Variations in Hose Construction
Hydraulic hoses are built to withstand the pressures and conditions of their specific applications. The construction of these hoses varies in complexity and strength based on their reinforcement.
Single-Wire Braided Hoses: These hoses feature a single layer of braided steel wire reinforcement between the inner tube and outer cover. They are flexible, lightweight, and used in lower-pressure applications.
Multi-Wire Braided Hoses: Constructed with multiple layers of steel wire reinforcement, these hoses provide increased strength and durability. They are suitable for high-pressure applications and are common in mobile and industrial machinery.
Spiral-Wound Hoses: These hoses feature spiral-wound steel reinforcement, offering superior strength and resistance to high pressure. Spiral-wound hoses are less flexible than braided hoses but are capable of withstanding the highest pressures and are commonly used in heavy-duty industrial settings.
Challenges in Cutting Hydraulic Hoses
Cutting hydraulic hoses is not a straightforward task due to the complexity of the hose materials and the variety of their reinforcement structures. Each hose material poses unique challenges that require specific tools and techniques for efficient and safe cutting.
Impact of Hose Material and Thickness on Cutting Difficulty:
The thickness and toughness of hydraulic hoses, particularly those reinforced with multiple layers of steel wire or spiral-wound reinforcement, make cutting them difficult. Rubber hoses, while more flexible, can still present challenges because of their thickness and the potential for deformation during cutting. Thermoplastic and PTFE hoses are often more rigid, adding to the difficulty of making clean cuts without specialized blades.
The presence of metal reinforcement layers complicates cutting further. Single-wire and multi-wire braided hoses require more robust cutting tools to slice through the steel without damaging the hose’s inner tube. Spiral-wound hoses, with their increased strength, demand even stronger blades that can penetrate the multiple layers of reinforcement without fraying the edges or compromising the structural integrity of the hose.
Common Problems with Improper Cutting
Selecting the wrong blade or using improper cutting techniques can lead to a variety of issues that negatively impact the performance and safety of hydraulic systems.
Frayed Edges: One of the most common problems with improper hose cutting is frayed edges. Fraying occurs when the blade is not sharp enough or not suited to the hose material, causing uneven cuts. Frayed edges can make it difficult to attach fittings securely and increase the risk of leaks.
Hose Degradation: Cutting with dull or inappropriate blades can damage the internal structure of the hose. This degradation weakens the hose and can lead to premature failure, especially in high-pressure applications.
Leaks: Poor cuts can also lead to improperly seated fittings, which increases the likelihood of fluid leaks. In hydraulic systems, leaks can cause inefficiencies, downtime, and potential hazards for workers.
Types of Blades for Hydraulic Hose Cutting
Cutting hydraulic hoses requires precision, and the choice of blade plays a crucial role in ensuring clean, accurate cuts without damaging the hose’s internal structure. There are several types of blades available for hydraulic hose cutting, each designed to tackle specific materials and conditions.
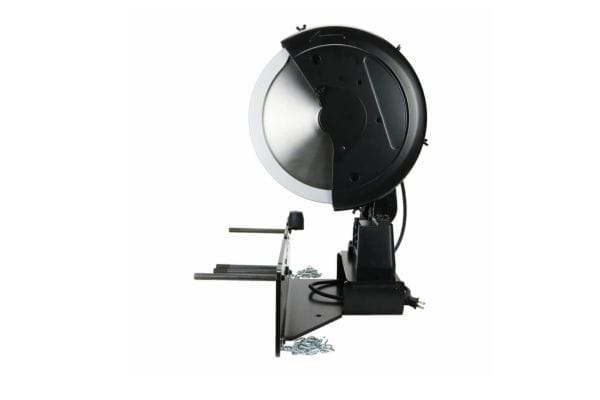
Cold Cutting Blades
Characteristics of Cold Cutting Blades:
Cold cutting blades are constructed from high-strength materials like steel or carbide tips. Unlike blades that generate heat during cutting, cold cutting blades work without causing significant heat buildup, which makes them ideal for applications where thermal damage could degrade the hose material. Steel blades are durable and effective for slicing through a range of materials, while carbide-tipped blades offer enhanced longevity and sharper cutting edges.
Best Uses for Cold Cutting Blades:
Cold cutting blades excel at cutting tough or thick hydraulic hoses, especially those with multiple layers of reinforcement. They are often used in cutting rubber and thermoplastic hoses, as well as hoses with steel-wire or spiral-wound reinforcements. Because these blades don’t produce excess heat, they minimize the risk of hose degradation due to temperature changes during the cutting process.
Pros and Cons:
Precision: Cold cutting blades are known for their precise cuts, making them ideal for high-pressure hydraulic hoses where clean edges are essential to ensuring secure fittings and preventing leaks.
Speed: While cold cutting blades provide precision, they tend to cut more slowly than other blade types, particularly when dealing with heavily reinforced hoses.
Cost: Cold cutting blades, especially carbide-tipped ones, can be more expensive than other blades. However, their durability and the reduction in damage to the hose often justify the initial investment.
Shear Blades
Description of Shear Blades:
Shear blades operate similarly to scissors, with two blades working in tandem to slice through the hose. These blades apply shearing force to cut the hose material, which is particularly effective for softer, more flexible hoses. The scissor-like action ensures that the hose is cut cleanly, with minimal deformation or damage to the internal structure.
Applications in Cutting Softer, Flexible Hoses:
Shear blades are ideal for cutting softer hydraulic hoses, such as those made of rubber or thermoplastic materials. These hoses do not have the same level of reinforcement as their steel-wired counterparts, allowing the shear blades to make clean cuts without exerting excessive force.
Advantages and Disadvantages:
Clean Cuts: Shear blades are excellent for producing smooth, clean cuts, particularly in hoses that do not require a great deal of force to slice through. This reduces the risk of fraying and ensures that the hose can be securely fitted afterward.
Blade Wear: Shear blades can wear down more quickly when used on tougher materials, especially hoses with metal reinforcements. This can lead to uneven cuts if the blades are not maintained properly or replaced regularly.
While shear blades are effective for softer hoses, their tendency to wear down quickly when used on tougher materials makes them less versatile than other blade types.
Toothed Blades
Definition and Types of Toothed Blades:
Toothed blades, such as circular saw blades, are characterized by sharp, jagged teeth that are designed to cut through hard materials quickly. These blades are available in different sizes and tooth configurations, with finer teeth for delicate materials and coarser teeth for tougher, reinforced hoses.
Appropriate Applications for Toothed Blades:
Toothed blades are best suited for cutting hard, reinforced hydraulic hoses, such as those with multiple layers of steel-wire or spiral-wound reinforcement. The rapid cutting action of the teeth allows these blades to slice through the hose material quickly, making them ideal for high-volume cutting environments where speed is a priority.
Pros and Cons:
Quick Cuts: Toothed blades excel in speed, allowing operators to cut through reinforced hoses rapidly, which is beneficial in large-scale operations.
Potential for Fraying: While toothed blades are efficient, they can sometimes cause frayed edges, especially if the teeth are too coarse for the hose material. Frayed edges may affect the ability to secure fittings properly and can increase the risk of leaks.
Overall, toothed blades offer fast cutting speeds but may require additional finishing to smooth out frayed edges, especially when used on softer hose materials.
Abrasive Blades
Introduction to Abrasive Blades:
Abrasive blades are designed to cut through materials using a grinding action rather than slicing. These blades are typically composed of composite materials embedded with abrasive particles, such as silicon carbide or aluminum oxide. When cutting, abrasive blades generate friction, which grinds away the material, producing a smooth edge.
Usage in Cutting Rubber or Softer Materials:
Abrasive blades are primarily used for cutting rubber hydraulic hoses or other softer materials. Their ability to grind away material makes them suitable for applications where a smooth edge is critical, such as when the hose is fitted with high-pressure connectors. Abrasive blades can also handle materials with embedded fibers or light reinforcement.
Advantages of Smooth Edges vs. Drawbacks Of Dust Production:
Smooth Edges: Abrasive blades provide extremely smooth edges, which is a significant advantage when the hose needs to maintain a high level of integrity at the cut ends. This ensures a proper seal when fittings are installed.
Dust Production: One of the drawbacks of using abrasive blades is the production of fine dust particles during the cutting process. This dust can accumulate and pose safety hazards if inhaled or if it contaminates the work area. Additionally, abrasive blades can wear down more quickly than other blade types due to their grinding action.
Factors to Consider When Selecting the Right Blade
Selecting the correct blade for hydraulic hose cutting involves understanding the hose’s material, diameter, and the specific needs of the application. Each factor plays a critical role in determining which blade will yield the best performance, efficiency, and safety.
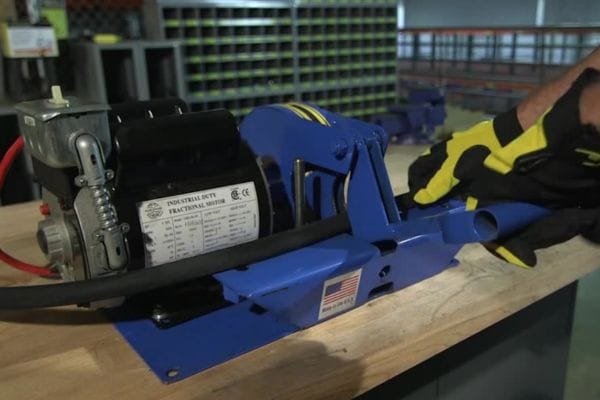
Hose Material and Construction
Material Composition and Blade Choice
Rubber Hoses: Rubber hoses are flexible but tough, often requiring sharp blades to ensure a clean cut without fraying or deformation. Cold cutting blades and toothed blades are generally best suited for rubber hoses, depending on the thickness and reinforcement levels.
Thermoplastic Hoses: Thermoplastic hoses are lighter and more resistant to abrasion compared to rubber hoses. They tend to require shear blades or cold cutting blades that can cleanly slice through the polymer material without causing damage to the hose’s internal structure.
Teflon (PTFE) Hoses: PTFE hoses are highly heat and chemical-resistant but are more rigid than rubber or thermoplastic hoses. Abrasive blades or carbide-tipped cold cutting blades are often needed to handle the rigidity of PTFE while ensuring smooth, clean cuts.
Hose Layering and Blade Requirements:
The construction of hydraulic hoses involves multiple layers, each of which must be taken into account when selecting the appropriate blade. Hydraulic hoses typically consist of:
Inner Tube: The core layer that carries the hydraulic fluid.
Reinforcement Layer: This could be a single or multi-layer braided steel wire or spiral-wound steel, which provides strength and resistance to pressure.
Outer Cover: The protective layer that shields the hose from environmental damage, such as abrasion or weathering.
For Single-Wire Braided Hoses: Cold cutting blades or toothed blades are usually ideal due to their ability to cut through the steel reinforcement while maintaining the integrity of the inner and outer layers.
For Multi-Wire or Spiral-Wound Hoses: Toothed blades are often the best choice because they can quickly cut through heavy steel reinforcements without damaging the inner tube. However, for added precision, cold cutting blades may be preferable.
Hose Diameter and Thickness
Blade Selection Based on Hose Size:
The diameter and thickness of the hydraulic hose are significant factors that influence blade choice. Larger diameter hoses with multiple reinforcement layers require more robust blades, while smaller hoses can often be cut with lighter-duty blades.
Small Diameter Hoses: For hoses with smaller diameters, such as those used in low-pressure or compact hydraulic systems, shear blades or cold cutting blades may suffice. These hoses typically have less reinforcement and require precision over power when cutting.
Large Diameter Hoses: Larger hoses with thick walls and heavy reinforcement, such as spiral-wound hoses, need powerful toothed blades or abrasive blades to slice through the layers effectively. The increased diameter and thickness demand blades that can handle the force required to cut through multiple layers without compromising the hose structure.
By matching the blade to the hose’s size and thickness, operators can ensure efficient cutting and minimize the risk of damaging the hose.
Required Cut Precision
Precision Needs and Blade Selection:
The level of precision required in cutting hydraulic hoses varies depending on the application. High-pressure hoses and hoses used in critical systems often require smooth, precise cuts to ensure that fittings can be securely attached and that the hose remains leak-free.
For High-Precision Cuts: Cold cutting blades are ideal for applications where smooth, clean cuts are necessary, such as in high-pressure hydraulic systems. These blades ensure that the hose ends are free of burrs or frayed edges, which is crucial for forming a proper seal with fittings.
Trade-Offs Between Precision and Speed: While cold cutting blades offer high precision, they are slower than toothed or abrasive blades. In high-volume environments, operators may need to balance the need for precision with the need for speed. Toothed blades, for example, can offer faster cuts, but the edges may require additional finishing to ensure a secure connection.
Understanding the trade-offs between precision and cutting speed allows operators to choose the blade that best fits their application while minimizing rework or finishing efforts.
Cutting Speed and Efficiency
Balancing Speed and Accuracy:
In high-volume cutting environments, speed and efficiency are critical factors. Operators need blades that can handle the workload while maintaining acceptable levels of precision. The right blade can reduce downtime, minimize wear and tear on cutting tools, and increase overall productivity.
Fast-Cutting Blades: Toothed blades are often the go-to choice for fast cuts, especially in environments where hoses need to be cut quickly and in large quantities. These blades excel in speed but may require additional finishing steps to ensure the hose ends are suitable for use.
Maximizing Efficiency: Cold cutting blades, while slower, offer greater durability and produce cleaner cuts, which can reduce the need for rework. By selecting blades that balance speed with accuracy, operators can maximize efficiency without sacrificing quality.
Selecting a blade that balances speed and precision helps maintain productivity while ensuring that each cut meets the necessary standards for hydraulic hose assembly.
Safety Considerations
Safety Precautions by Blade Type:
Safety should always be a top priority when selecting a blade for hydraulic hose cutting. Different blades present unique hazards, and proper safety protocols must be followed to protect operators.
Cold Cutting Blades: These blades generate little heat, reducing the risk of burns or overheating during the cutting process. However, they are sharp and require careful handling to avoid accidents.
Shear Blades: Shear blades operate similarly to scissors and present minimal risk of debris or sparks. However, they still pose a risk of injury if not handled correctly.
Toothed Blades: Toothed blades, particularly those used in saws, can create debris and sharp fragments during the cutting process. Operators should wear protective eyewear and gloves to prevent injuries.
Abrasive Blades: Abrasive blades generate dust and can cause respiratory hazards if proper ventilation and protective masks are not used. Additionally, the friction they produce can create sparks, which can be dangerous in certain environments.
Blades with the Best Safety Profiles:
Cold cutting blades generally offer the best safety profile due to their precision and minimal heat generation. Abrasive blades and toothed blades, while efficient, require stricter safety protocols to mitigate risks such as dust, debris, and sparks.
Conclusion
In summary, each blade type offers distinct advantages and is suited to specific applications. Cold cutting blades excel in precision, shear blades are ideal for softer hoses, toothed blades handle tougher materials effectively, and abrasive blades provide versatility for a range of hose types. The right blade not only improves cutting accuracy but also contributes to overall safety and operational efficiency.
FAQ
What type of blade is best for cutting rubber hydraulic hoses?
Cold cutting blades or toothed blades are generally best for cutting rubber hydraulic hoses. Cold cutting blades provide clean cuts without fraying, while toothed blades are effective for tougher, thicker rubber hoses.
Can shear blades be used for cutting all types of hydraulic hoses?
Shear blades are suitable for cutting softer, flexible hoses. However, they may not be the best choice for hoses with heavy reinforcement or rigid materials, where cold cutting or toothed blades might be more effective.
How does the diameter of the hose affect blade selection?
Larger diameter hoses, especially those with multiple reinforcement layers, require more robust blades like toothed or abrasive blades to handle the thickness. Smaller diameter hoses can often be cut with lighter-duty blades such as shear or cold cutting blades.
What are the advantages of using abrasive blades for hydraulic hose cutting?
Abrasive blades are useful for cutting through tough materials, including rubber and reinforced hoses. They provide smooth edges but can produce dust and may require additional safety measures.
How important is precision in hydraulic hose cutting, and how does it affect blade choice?
Precision is crucial, especially for high-pressure hoses where clean, smooth cuts are necessary to ensure proper sealing with fittings. Cold cutting blades are preferred for precision cuts, while toothed blades might be used in applications where speed is prioritized over precision.
What safety precautions should be taken when using hydraulic hose cutting blades?
Always wear appropriate personal protective equipment (PPE) such as gloves, safety glasses, and masks. Follow the manufacturer’s guidelines for the specific blade type, and ensure proper ventilation when using abrasive blades to avoid dust inhalation.