Hydraulic hoses play an essential role in powering critical industrial applications. Whether it’s in heavy machinery for construction, agricultural equipment, or automotive systems, these hoses are responsible for transferring fluids under high pressure, enabling efficient operation and functionality. However, as vital as they are to smooth operations, hydraulic hoses are often overlooked until they fail.
Understanding the Basics of Hydraulic Hoses
Hydraulic hoses are essential components in various industries, serving as flexible tubes that convey hydraulic fluids under high pressure. These hoses are critical for enabling the movement of machinery and equipment in sectors like construction, agriculture, automotive, and manufacturing. To understand their importance, it’s crucial to explore the different types of hydraulic hoses, their functions, and the wide range of applications they support.

Types of Hydraulic Hoses
Hydraulic hoses come in different varieties, each designed to suit specific applications and environmental conditions. One of the most common types is reinforced rubber hoses, which feature multiple layers of braided wire and rubber to withstand high pressure and resist abrasion. These hoses are highly durable and flexible, making them suitable for a broad range of applications.
Another type is thermoplastic hoses, which are lighter and more resistant to chemicals than rubber hoses. They offer excellent flexibility and are ideal for environments where exposure to harsh chemicals or extreme temperatures is common. PTFE hoses, made from polytetrafluoroethylene, are known for their resistance to extreme temperatures and aggressive chemicals. These hoses are often used in high-temperature and high-pressure applications, making them a popular choice in industries such as chemical processing and food production.
Functions of Hydraulic Hoses
The primary function of hydraulic hoses is to transfer fluids—usually oils or water-based liquids—throughout hydraulic systems to generate mechanical force. These hoses are designed to handle extremely high pressures, enabling the movement of parts in machinery such as lifts, cranes, and excavators. The hoses must be flexible enough to move with the machinery while maintaining their structural integrity under pressure. This allows for precise control of hydraulic systems, which is essential for operations ranging from steering in vehicles to lifting heavy loads in industrial equipment.
Common Applications
Hydraulic hoses are used across a broad spectrum of industries, each with its own unique set of demands. In construction, for example, hydraulic hoses are found in excavators, loaders, and other heavy machinery that rely on hydraulics to move and operate efficiently. Agriculture also heavily depends on hydraulic hoses, with equipment like tractors, harvesters, and irrigation systems utilizing hydraulic power for various tasks. The automotive industry employs hydraulic hoses in systems like braking, steering, and power transmission, ensuring smooth and reliable vehicle operations. Additionally, hydraulic hoses are essential in manufacturing for operating machinery that requires precise movements, such as robotic arms and assembly lines.
Average Lifespan of Hydraulic Hoses Last
Typical Lifespan Range
The lifespan of a hydraulic hose can vary greatly depending on the application, environment, and maintenance practices. In general, hydraulic hoses are expected to last anywhere from one to five years. However, this is not a hard-and-fast rule, and the actual lifespan can differ depending on usage conditions. For example, hoses operating in a relatively clean and stable environment may last towards the higher end of this range, while those subjected to harsh conditions, such as extreme temperatures or frequent bending, may degrade more quickly.
Hydraulic hoses in non-continuous applications, such as agricultural equipment that may only be used during certain seasons, can have a longer service life if properly maintained. On the other hand, hoses in industrial or construction environments that operate continuously under high pressures and loads tend to wear out faster. Therefore, understanding the specific conditions in which your hydraulic hoses are used is critical to estimating their longevity accurately.
Variables Affecting Longevity
Environmental Exposure: Hydraulic hoses can be exposed to harsh environments that contribute to wear and tear. External factors such as UV exposure, chemicals, moisture, and extreme temperatures can cause hoses to degrade prematurely. For example, hoses exposed to direct sunlight without protective covers can become brittle due to UV radiation, while hoses used in chemical environments may suffer from corrosion if not made from resistant materials.
Hose Materials: The type of materials used to manufacture the hose significantly impacts its lifespan. Rubber hoses are prone to wear due to friction and environmental factors, whereas hoses made of thermoplastic or PTFE offer better resistance to chemicals and extreme temperatures. Choosing the correct material for the specific application is essential for ensuring a longer lifespan.
Operating Pressures: The internal pressure a hose is subjected to plays a critical role in its longevity. Hoses operating at or near their maximum pressure rating are more likely to suffer from fatigue and burst under the strain. Operating at pressures below the hose’s rated capacity can help extend its life.
Temperatures: Extreme temperatures, both high and low, can have a profound effect on hydraulic hose life. High temperatures can cause the hose material to soften or degrade, leading to failure, while cold temperatures can make hoses brittle and prone to cracking. Hoses designed for specific temperature ranges should be used to ensure longevity in these conditions.
Mechanical Stress: Bending, twisting, and kinking of hoses during operation can shorten their lifespan. Installing hoses with the appropriate bend radius and ensuring that they are routed in a way that minimizes mechanical stress can help prevent premature failure. Additionally, hoses that are regularly moved or flexed should be monitored more closely for signs of wear.
Industry Standards
Industry standards and guidelines exist to help manufacturers and users ensure the reliability and durability of hydraulic hoses. Two of the most widely recognized standards are set by the Society of Automotive Engineers (SAE) and the International Organization for Standardization (ISO).
SAE Standards: SAE sets the benchmark for hydraulic hose performance in terms of pressure ratings, temperature ranges, and material specifications. For instance, SAE J517 is a standard that specifies the dimensions, performance requirements, and testing procedures for hydraulic hoses. These standards help manufacturers produce hoses that meet consistent safety and performance criteria, allowing users to select hoses that match their specific operational needs.
ISO Standards: ISO also provides guidelines for hydraulic hose design and performance. ISO 18752, for example, focuses on high-pressure hydraulic hoses and includes classification criteria for hoses based on their maximum working pressure and temperature range. ISO standards are designed to promote quality and safety in hydraulic applications globally.
Factors That Impact Hydraulic Hose Lifespan
The lifespan of hydraulic hoses is influenced by a combination of factors, ranging from environmental exposure to the way hoses are installed and maintained. By understanding these factors and addressing them proactively, operators can significantly extend the life of their hydraulic hoses, reduce the likelihood of unexpected failures, and ensure optimal performance of hydraulic systems.
Environmental Factors
Environmental conditions play a significant role in the degradation of hydraulic hoses. For example, exposure to heat can cause the hose material to soften, swell, or degrade, especially in applications where hoses are subjected to elevated temperatures. Over time, this can result in the hose becoming brittle and prone to cracking. Conversely, hoses exposed to extreme cold can stiffen, leading to a loss of flexibility and an increased likelihood of failure during operation.
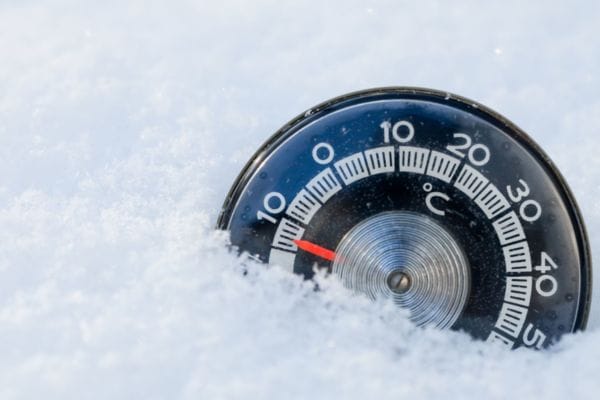
Chemicals are another environmental factor that can severely impact hydraulic hose longevity. In applications where hoses come into contact with corrosive fluids, the hose material can break down more rapidly if it is not specifically designed for chemical resistance. Over time, the interaction between the hose and the chemicals can weaken the hose walls, leading to leaks or bursts.
UV light is another culprit that can damage hoses, particularly in outdoor applications. Prolonged exposure to sunlight can cause hoses to degrade through a process known as photo-oxidation, which weakens the hose material and leads to cracking and fading. This is particularly problematic for hoses made of rubber or other light-sensitive materials.
Lastly, abrasion can occur when hoses rub against surfaces, machinery, or other hoses. Continuous friction can wear away the hose’s outer layer, leaving the inner layers vulnerable to damage. Abrasion can be particularly problematic in confined spaces or high-movement applications where hoses are frequently in motion.
Installation Practices
Importance of Correct Installation Techniques
Proper installation is critical to extending the lifespan of hydraulic hoses. One of the most common installation mistakes is allowing hoses to become twisted or kinked during installation. These stress points can weaken the hose, leading to cracks, leaks, or premature failure. Twisting, in particular, puts undue stress on the hose’s internal structure, reducing its ability to withstand pressure and movement over time.
Avoiding sharp bends is another key installation consideration. Hydraulic hoses are designed with a specific minimum bend radius, which refers to the tightest curve that the hose can be bent without compromising its integrity. When hoses are bent beyond this limit, the internal reinforcement may buckle, leading to reduced flow capacity and potential damage. Ensuring that hoses are installed with gentle curves and that they have enough slack to move with the machinery helps prevent bending stress.
Proper Fitting and Routing of Hoses
Correct fitting is essential for hydraulic hose performance. Improperly fitted hoses can lead to leaks, pressure drops, and even dangerous blowouts. Ensuring that the fittings are appropriate for the hose diameter, pressure rating, and fluid type is crucial for maintaining a secure and reliable connection.
Routing the hose properly can also reduce the risk of premature wear. Hoses should be routed in a way that minimizes contact with sharp edges, abrasive surfaces, and moving parts. Clamps and protective sleeves can be used to secure hoses in place, reducing movement and friction. Additionally, hoses should be routed to avoid excessive tension or stretching, which can weaken the hose over time.
Hose Selection
Ensuring the Right Hose is Chosen for the Specific Application
Selecting the correct hydraulic hose for the application is one of the most important factors in ensuring its longevity. The hose must be chosen based on the system’s pressure requirements, temperature range, and the type of fluid being used. For instance, a hose designed for low-pressure systems will not perform well in high-pressure environments and will fail prematurely.
Temperature compatibility is also essential. Hoses that are not rated for the system’s temperature range can suffer from thermal degradation, reducing their ability to handle pressure. Similarly, the fluid compatibility of the hose material must be considered. Certain hydraulic fluids can be corrosive to some hose materials, leading to internal degradation and leaks. Ensuring that the hose is chemically compatible with the fluid it will carry is key to preventing early failure.
Consequences of Using the Wrong Hose
Using the wrong hose for an application can have disastrous consequences. For example, a hose that is not rated for the system’s operating pressure can burst, leading to equipment damage, fluid spills, and even injury to personnel. Incorrect material selection can lead to chemical reactions between the fluid and hose, causing internal erosion and reducing the hose’s ability to maintain pressure. Over time, the wrong hose selection can lead to increased maintenance costs, unplanned downtime, and a shorter overall system lifespan.
Regular Wear and Tear
How Normal Usage and High-Cycle Operations Contribute to Hose Fatigue Over Time
Over time, normal usage of hydraulic hoses leads to wear and tear, which contributes to hose fatigue. In systems with high-cycle operations, where the hose is constantly moving, flexing, or pressurized, the hose’s internal and external layers gradually weaken. High-frequency movement can cause microcracks to develop in the hose material, which can spread and eventually lead to hose failure.
Continuous vs. Intermittent Use
The frequency of use also affects hose life. Continuous use of hydraulic hoses, particularly in high-pressure environments, can accelerate the aging process due to constant strain on the hose material. Hoses used continuously may need to be replaced more frequently due to the persistent forces acting on them.
On the other hand, intermittent use can give the hose time to “recover” between cycles, which can extend its lifespan. However, hoses that remain idle for long periods can also degrade due to environmental exposure or chemical interactions. Therefore, regardless of whether a hose is used continuously or intermittently, regular inspections.
Warning Signs of Hydraulic Hose Failure
Hydraulic hoses are a critical part of many industrial systems, and their failure can lead to costly downtime, safety hazards, and even complete system shutdowns. Recognizing the early warning signs of hydraulic hose failure is essential for preventing these issues. Whether it’s visual, performance-based, auditory, or tactile indicators, understanding what to look for can help operators determine when it’s time to repair or replace a hose.
Visual Indicators of Wear
Cracks: Cracks are one of the most obvious signs of a deteriorating hydraulic hose. Cracks may appear on the outer cover due to aging, excessive exposure to environmental elements, or the hose’s inability to flex as it once did. Cracks often occur when hoses are exposed to extreme temperatures or UV light for extended periods. These fissures weaken the hose’s structure and make it more vulnerable to leaks and bursts.
Blisters: Blisters on a hydraulic hose can indicate internal damage. This usually happens when the inner layers of the hose start to degrade, allowing fluid to seep between the layers and create bubbles or bulges on the outer surface. Blisters are a serious sign of impending failure and should be addressed immediately, as they often signal that the hose’s internal structure has been compromised.

Cuts and Abrasions: Hydraulic hoses are often subjected to friction, which can lead to cuts and abrasions on the outer layer. If the hose is rubbing against metal parts, machinery, or even other hoses, the outer cover can wear away over time. While small cuts or abrasions might seem harmless initially, they can expose the inner layers of the hose to environmental damage and increase the risk of leaks or ruptures. Addressing this wear early is key to preventing larger failures.
Corrosion or Rust: If the hose’s fittings are corroding or showing signs of rust, it could indicate that moisture is making its way into the hose assembly. Corrosion weakens the connection points and can lead to fluid leakage or complete detachment from the fittings.
Flattening or Deformation: Hoses that appear flattened, kinked, or deformed may have been subjected to improper installation or routing. Such deformation can restrict fluid flow, increase pressure in the system, and weaken the hose structure over time.
Performance Indicators
In addition to visual signs, performance-related issues often indicate that a hydraulic hose is nearing the end of its service life. Here are several key performance indicators that should raise red flags:
Fluid Leakage: One of the most obvious indicators of hose failure is fluid leakage. This can happen when the hose’s walls or fittings become damaged, causing hydraulic fluid to escape. Leaks may start as small drips but can quickly escalate into larger problems if left unchecked. In some cases, a small pinhole leak may be difficult to detect visually but can still reduce system performance.
Pressure Drops: Hydraulic systems rely on precise pressure to function properly. If a hose is compromised, you may notice a sudden or gradual drop in pressure throughout the system. This could indicate that the hose is leaking internally or that its structure has weakened to the point where it can no longer maintain the required pressure. When pressure drops occur, system performance is diminished, which can impact the effectiveness of machinery and processes.
Loss of System Efficiency: A failing hydraulic hose can cause a noticeable decrease in the overall efficiency of the system. This could manifest as slower response times, reduced power output, or inconsistent operation of machinery. If the system seems to be working harder to achieve the same results, or if certain components are underperforming, it may be a sign that one or more hoses are compromised and need to be inspected or replaced.
Auditory and Tactile Indicators
Sometimes, hose failure can be detected through auditory or tactile clues. These signs are often overlooked, but they can provide critical insights into the health of your hydraulic hoses.
Unusual Noises: Hydraulic systems are typically noisy, but certain sounds can indicate trouble. For example, a whistling or hissing noise may suggest that air is being sucked into the system through a small leak or crack in the hose. Similarly, a “popping” or “snapping” sound could indicate that the hose is under too much stress and is starting to fail. These sounds are often precursors to more serious problems, and they should be investigated immediately.
Changes in Hose Flexibility: Over time, hydraulic hoses can lose their flexibility, making them stiffer and harder to manipulate. This change in flexibility can be felt when handling the hose and may be a sign that the hose material has degraded. Excessive stiffness can lead to cracking or kinking during operation, further weakening the hose. If a hose that was once supple and flexible becomes rigid, it’s time to consider replacement.
When to Replace vs. Repair
One of the most important decisions operators face is whether to repair a damaged hose or replace it altogether. In general, it’s better to err on the side of caution when dealing with hydraulic hoses, as the consequences of failure can be severe.
Repair
In some cases, minor issues such as superficial abrasions or small leaks near fittings may be repaired if they are caught early. Temporary repairs, such as patching or re-clamping, may allow the hose to function until a replacement can be installed. However, repairs should never be considered a long-term solution, as they only address the symptoms of a problem rather than the root cause.
Replace
Severe Damage: If a hose has significant cracks, blisters, or deformations, it is no longer safe to use and should be replaced immediately.
Frequent Leaks: If the hose develops multiple leaks, this indicates that the material is degrading and should be replaced rather than patched.
Age: Hydraulic hoses should be replaced after they reach the end of their recommended lifespan, regardless of visible wear. Even if a hose appears to be in good condition, materials can weaken over time, making failure more likely.
Performance Issues: Persistent performance problems such as pressure drops, fluid leaks, or system inefficiencies should prompt a full inspection and possible replacement of the affected hoses.
Conclusion
Don’t wait for your hydraulic hoses to fail before addressing potential issues. Proactively maintaining your hydraulic hoses can save time, reduce costs, and prevent dangerous equipment malfunctions. Regularly scheduled inspections can help you identify visual, performance-based, and even subtle auditory signs that a hose may be nearing the end of its life. By taking a proactive approach, you can replace hoses before they become a liability, ensuring your hydraulic systems continue to operate smoothly and efficiently.
FAQ
How long do hydraulic hoses typically last?
Hydraulic hoses usually last between one to five years, depending on usage, environmental factors, and maintenance.
What are the signs that a hydraulic hose needs to be replaced?
Common signs include cracks, leaks, blisters, reduced flexibility, and pressure drops in the system.
Can hydraulic hoses be repaired, or should they always be replaced?
Minor issues like small leaks can sometimes be repaired temporarily, but it is generally safer to replace damaged hoses to prevent future failures.
What factors can shorten the lifespan of a hydraulic hose?
Exposure to extreme temperatures, chemicals, UV light, improper installation, and continuous high-pressure usage can all reduce hose lifespan.
How often should hydraulic hoses be inspected?
Hydraulic hoses should be inspected regularly, with more frequent checks in harsh environments or high-use applications—ideally every few months.
What should I do if I notice a leak in a hydraulic hose?
If you notice a leak, shut down the system immediately and inspect the hose. Replace the hose if it shows significant damage or wear.