One crucial aspect that often goes unnoticed in hydraulic hose maintenance is the bend radius. The hydraulic hose bend radius refers to the smallest possible curve the hose can safely accommodate without being damaged or compromising its integrity. Adhering to the correct bend radius is essential because even a slight deviation can result in significant wear and tear, leading to hose failure, fluid leaks, and a potential halt in operations.
Understanding Hydraulic Hose Bend Radius
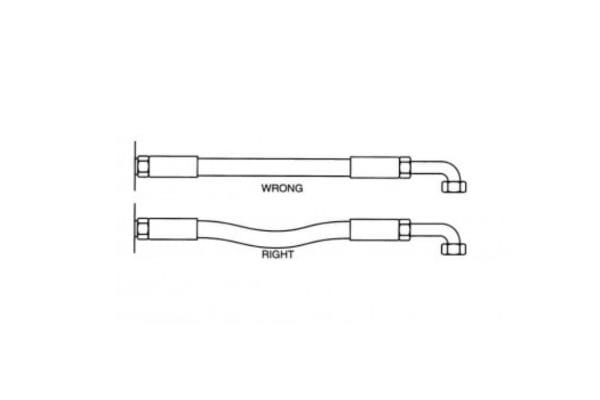
What is Bend Radius?
The bend radius of a hydraulic hose is a fundamental concept that refers to the minimum radius a hose can be bent without compromising its structural integrity or performance. In technical terms, bend radius is the smallest arc that a hose can curve around without kinking, collapsing, or incurring damage to its inner layers, which could ultimately lead to hose failure.
The importance of maintaining the correct bend radius lies in the physics of fluid dynamics and hose material behavior. Hydraulic hoses are designed to withstand high pressure while remaining flexible, but excessive bending puts stress on the hose’s internal structure. This stress can lead to a breakdown of the reinforcement layers or cause permanent deformation of the hose, resulting in reduced flow capacity or, worse, catastrophic failure.
Importance of Minimum Bend Radius
The minimum bend radius is the smallest permissible radius that a hose can be bent around during installation or operation without negatively impacting its performance. Staying within this limit is crucial for the longevity and reliability of hydraulic hoses. Bending a hose too tightly can weaken the hose’s internal components, such as the inner tube and reinforcement layers, leading to leaks, cracks, or even rupture. Moreover, tight bends can create flow restrictions, reducing the efficiency of the system and increasing pressure loss. This can place additional strain on pumps and other components, potentially shortening their lifespan.
Maintaining the minimum bend radius ensures that the hose operates within its designed limits, preventing excessive stress and promoting optimal flow conditions. Ignoring these guidelines can lead to frequent maintenance, unplanned downtime, and increased operating costs.
How the Bend Radius is Calculated
The bend radius of a hydraulic hose is calculated based on the diameter of the hose and the specifications set by the hose manufacturer. The typical formula for calculating the bend radius is:
Minimum Bend Radius=Factor×Outside Diameter of Hose
The factor is provided by the hose manufacturer and varies based on the hose construction and material. For example, a braided hose may have a different bend radius factor compared to a spiral hose due to differences in flexibility and reinforcement structure.
Manufacturers will specify the minimum bend radius for each hose model, and this value must be adhered to during installation and operation to ensure the hose remains functional and safe.
How Bend Radius Varies with Hose Type and Size
The allowable bend radius can vary significantly depending on the hose material, type, and size. Different hoses are constructed for specific applications, and their design plays a critical role in determining their flexibility and minimum bend radius.
Hose Materials and Constructions:
Hydraulic hoses are typically made from rubber, thermoplastic, or PTFE (Polytetrafluoroethylene). Rubber hoses tend to have a moderate bend radius, offering a balance between flexibility and durability. Thermoplastic hoses are generally more flexible, resulting in a tighter bend radius, while PTFE hoses, which are more rigid, require a larger bend radius to prevent kinking and damage.
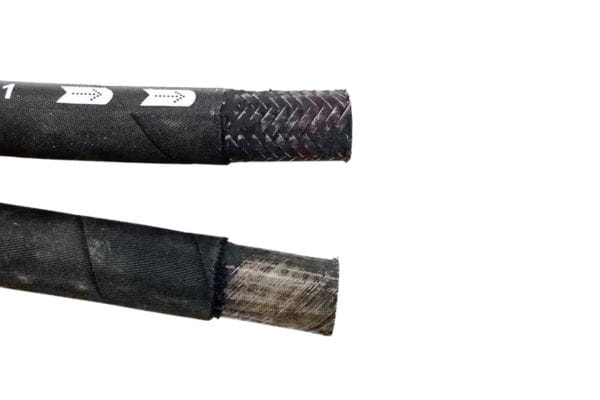
Braided vs. Spiral Hoses:
The construction of the hose also impacts its flexibility. Braided hoses, reinforced with wire or textile braids, are typically more flexible than spiral hoses, which are reinforced with multiple layers of steel wire spirals. Spiral hoses are often used in high-pressure applications but require a larger bend radius due to their rigidity. Braided hoses, on the other hand, can be bent more tightly, making them suitable for applications with space constraints.
Examples of How Size and Type Influence Allowable Bend Radius
Small Diameter Hoses: Smaller diameter hoses generally allow for a tighter bend radius. For example, a 1/4-inch braided hose might have a minimum bend radius of just a few inches, making it suitable for installations in confined spaces.
Large Diameter Hoses: Conversely, larger diameter hoses require a greater bend radius. For example, a 2-inch spiral hose used in high-pressure applications might have a minimum bend radius of several feet. Attempting to bend a large hose too tightly can cause severe internal damage or even complete failure.
Importance of Adhering to Minimum Bend Radius
Impact of Ignoring Minimum Bend Radius
Premature Hose Wear and Tear
When hydraulic hoses are bent beyond their recommended minimum radius, it places excessive stress on the hose’s internal layers. This strain can cause the hose’s reinforcement materials (such as wire braids or spirals) to weaken, stretch, or even break over time. The result is a significant reduction in the hose’s ability to maintain its integrity under pressure, leading to premature wear. Additionally, continuous over-bending can cause the outer cover of the hose to crack, exposing the inner layers to environmental elements that can accelerate deterioration.
In industrial environments where hydraulic hoses are subjected to frequent movement and pressure fluctuations, ignoring the minimum bend radius leads to faster hose degradation, requiring more frequent replacements and unplanned downtime for repairs.
Increased Risk of Fluid Leaks, Pressure Loss, and Efficiency Reduction
Bending hydraulic hoses too tightly can cause the inner tube to collapse or distort, leading to kinks or restrictions within the hose. These obstructions can severely impact the flow of hydraulic fluid, resulting in increased pressure loss within the system. Pressure loss reduces the overall efficiency of the hydraulic system, as the pump must work harder to maintain the desired pressure levels. Over time, this added stress on the system can lead to further equipment failures and higher energy consumption.
Moreover, extreme bending increases the likelihood of fluid leaks at critical connection points or along the hose itself. Leaking hydraulic fluid not only reduces system performance but also introduces the risk of contamination, slip hazards, and environmental damage, particularly in sensitive industries such as food processing, healthcare, or aerospace.
Potential Safety Hazards Due to Hose Failures
Perhaps the most concerning consequence of ignoring the minimum bend radius is the risk of catastrophic hose failure. Hydraulic systems operate under high pressure, and a compromised hose can lead to violent ruptures, spraying high-pressure fluids into the surrounding area. This presents a significant safety hazard to nearby personnel, potentially causing injuries such as burns, bruises, or cuts from the sudden release of pressure.
In more severe cases, hose failures can result in the malfunction of critical machinery or equipment, leading to accidents or damage to expensive components. Safety is paramount in industries that rely on hydraulic systems, and adhering to bend radius guidelines is a simple but effective way to mitigate these risks.
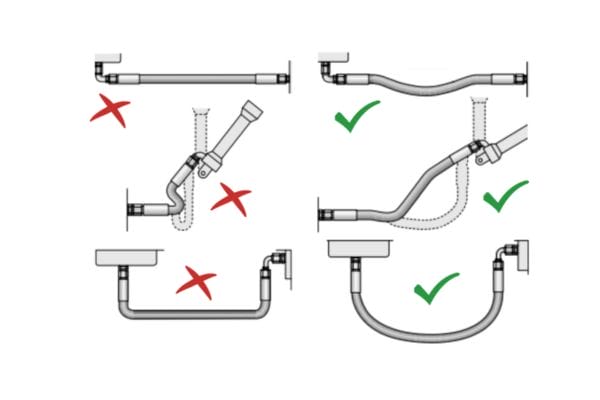
Benefits of Maintaining Proper Bend Radius
Improved Longevity of Hoses
Ensuring that hydraulic hoses are installed and operated within their specified minimum bend radius promotes longer hose life. By avoiding excessive bending, the internal components of the hose are protected from undue stress and wear, allowing the hose to perform effectively over a more extended period. This longevity not only reduces the frequency of hose replacements but also minimizes disruptions to operations, contributing to greater system uptime and productivity.
Enhanced System Performance and Efficiency
Hydraulic systems function most efficiently when the flow of hydraulic fluid is uninterrupted and maintained at the desired pressure levels. By adhering to the minimum bend radius, hoses are kept free of obstructions that could restrict fluid flow, ensuring that the system operates at peak performance. Efficient flow within the system means that the pump and other components do not have to compensate for pressure losses or other inefficiencies, resulting in lower energy consumption and less strain on the system as a whole.
Furthermore, maintaining proper bend radius prevents fluid leaks and pressure drops, which can significantly reduce the performance of the system. With well-maintained hoses, machinery operates smoothly, and the risk of unexpected breakdowns is minimized.
Reduced Maintenance and Replacement Costs
Properly installed hoses that adhere to the minimum bend radius experience less wear and tear, meaning fewer breakdowns and less frequent maintenance. This reduction in maintenance needs translates to cost savings in both parts and labor. Regular hose replacements and repairs can be costly, especially in large industrial systems that require specialized hoses and fittings. By reducing the rate of hose failure, companies can lower their overall operating expenses and allocate resources more efficiently.
Factors Influencing Hydraulic Hose Bend Radius
The flexibility and bend radius of hydraulic hoses are influenced by several key factors, including pressure ratings, hose reinforcement, construction materials, environmental conditions, and flow rates.
Pressure Ratings and Hose Reinforcement
How Pressure Affects Flexibility and Bend Radius
Pressure is one of the primary factors that affect the flexibility and bend radius of hydraulic hoses. Hoses are designed to withstand certain levels of internal pressure, measured in psi (pounds per square inch). As pressure increases, the internal forces acting on the hose walls grow, reducing the hose’s overall flexibility. High-pressure hoses tend to be stiffer and have a larger minimum bend radius, while low-pressure hoses are more flexible and can accommodate tighter bends.
When a hydraulic hose is subjected to high pressure, bending it too sharply can cause stress on the hose’s internal reinforcement layers, leading to kinks, cracks, or rupture. This is why high-pressure hoses generally require a larger bend radius. In contrast, hoses that operate under lower pressures are more forgiving and can bend more easily without compromising their structural integrity.
The Role of Reinforcement (Braided vs. Spiral Hoses)
Hydraulic hoses are typically reinforced with layers of braided or spiral wire to provide additional strength and resistance to internal pressure. The type of reinforcement plays a significant role in determining the allowable bend radius.
Braided Hoses: These hoses are reinforced with wire or textile braids, which allow for greater flexibility. Braided hoses can handle moderate to high pressure while maintaining a relatively tight bend radius. This makes them suitable for applications where space is limited and frequent bending is required.
Spiral Hoses: Spiral-reinforced hoses, on the other hand, consist of multiple layers of steel wire spirals, making them more rigid and capable of withstanding extremely high pressure. However, this added strength comes at the cost of flexibility, meaning spiral hoses require a larger minimum bend radius. They are commonly used in heavy-duty applications, such as construction or mining, where high-pressure conditions demand reinforced durability.
Hose Construction Materials
Impact of Different Hose Materials on Bend Radius
The materials used to construct hydraulic hoses also significantly affect their flexibility and bend radius. Different materials have varying levels of elasticity, resistance to stress, and durability, all of which play into how tightly the hose can be bent.
Rubber Hoses: Rubber is the most common material used in hydraulic hoses. It offers a good balance between flexibility and durability, allowing for moderate bend radii. Rubber hoses are suitable for a wide range of applications and can handle various pressure levels without compromising their bend radius too much.
Thermoplastic Hoses: Thermoplastic hoses are lighter and more flexible than rubber hoses, which allows them to bend more easily and achieve tighter radii. These hoses are often used in applications where space constraints are a significant concern, and flexibility is paramount. However, thermoplastic hoses are generally less durable than rubber, especially in abrasive environments.
PTFE (Polytetrafluoroethylene) Hoses: PTFE hoses are known for their resistance to high temperatures, chemicals, and abrasion. However, they tend to be more rigid than rubber or thermoplastic hoses, which means they require a larger bend radius. PTFE hoses are commonly used in environments where chemical resistance is critical, but flexibility is less of a concern.
Environmental Conditions
How Temperature, Chemicals, and UV Radiation Affect Hose Flexibility
Environmental conditions such as temperature, chemical exposure, and UV radiation can also influence the bend radius of hydraulic hoses.
Temperature: Extreme temperatures, whether hot or cold, can affect the flexibility of a hose. High temperatures tend to make hoses softer and more flexible, which could potentially allow for tighter bends. However, this increased flexibility can also weaken the hose structure over time. Cold temperatures, on the other hand, make hoses more rigid, increasing the minimum bend radius and making the hose more susceptible to cracking if bent too sharply.
Chemical Exposure: Exposure to certain chemicals can cause hoses to degrade over time, leading to reduced flexibility. In particular, chemicals that affect the hose’s outer cover or reinforcement layers can make the hose more brittle and prone to cracking when bent. Hoses used in chemically harsh environments must be selected carefully to ensure compatibility and resistance.
UV Radiation: Prolonged exposure to UV radiation can degrade the outer cover of the hose, making it more rigid and prone to cracking when bent. UV resistance is a key consideration for hoses used in outdoor applications, where sun exposure is constant.
Flow Rates and Hose Bend Radius
The Relationship Between Flow Rate and Bend Radius
The flow rate of hydraulic fluid through a hose can also impact the bend radius. When a hose is bent too tightly, it can create restrictions that affect the fluid’s flow dynamics. As the hose is bent beyond its minimum radius, the internal diameter of the hose may become constricted, leading to a reduction in flow rate.
Potential Effects on Fluid Dynamics: Reduced flow rates can increase pressure within the system, potentially leading to pressure spikes or surges that may damage equipment. Additionally, improper bend radius can cause turbulent flow, which increases energy loss and reduces system efficiency.
Maintaining the correct bend radius ensures that the flow rate remains consistent and that the fluid moves smoothly through the system. This helps to avoid pressure losses and ensures that the hydraulic system operates efficiently.
Common Hydraulic Hose Failures Due to Incorrect Bend Radius
Maintaining the correct bend radius in hydraulic hoses is essential for preventing various types of failures that can negatively impact system performance and safety. When the bend radius is disregarded, it can lead to serious issues such as kinking, external abrasion, and internal damage to the hose walls.
Kinking and Hose Collapse
How Incorrect Bend Radius Leads to Kinking and Flow Obstruction
One of the most common failures associated with an improper bend radius is kinking. Kinking occurs when a hose is bent too tightly, causing the hose to fold or crimp in a way that disrupts the flow of hydraulic fluid. When a hose kinks, the inner tube of the hose collapses partially or entirely, creating a blockage or significant restriction in the flow path.
This flow obstruction leads to several operational problems:
Reduced Flow Rate: A kinked hose can dramatically reduce the hydraulic fluid’s flow rate, compromising the performance of the entire system. In hydraulic systems, the fluid must flow efficiently to maintain pressure, and any restriction can reduce the system’s ability to perform at optimal levels.
Increased Pressure: With the flow obstructed, pressure can build up at the point of the kink, placing additional strain on the hose and fittings. This excess pressure can lead to hose rupture, especially in high-pressure systems, causing leaks or a complete failure of the hydraulic line.
Permanent Deformation: In some cases, the hose may experience permanent deformation at the point of the kink, weakening the hose structure and making it more susceptible to future failures, even if the hose is straightened out afterward.
Kinking is especially dangerous because it often leads to a domino effect within the system, resulting in more severe issues like hose rupture or equipment malfunction.
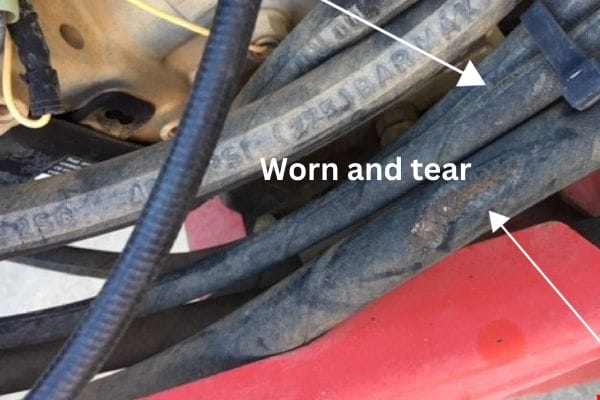
Abrasion and External Damage
Hose Damage Caused by External Abrasion When Bent Beyond Its Limits
Another frequent consequence of incorrect bend radius is external abrasion and damage. When a hydraulic hose is bent too sharply, it may come into contact with other components of the system, such as machinery, other hoses, or sharp edges within the installation environment. Continuous rubbing or chafing against these surfaces can wear down the outer cover of the hose, exposing the reinforcement layers beneath.
This abrasion leads to several key issues:
Compromised Outer Cover: The outer cover of the hose is designed to protect the internal layers from environmental factors and physical damage. When the cover is worn away due to constant rubbing, the hose becomes more vulnerable to external forces like heat, chemicals, and mechanical impacts. This can further degrade the hose’s integrity.
Reinforcement Exposure: If the outer layer is sufficiently damaged, the hose’s reinforcement layers can become exposed. Once these layers are compromised, the hose is much more likely to fail under pressure. Exposure to the elements can also lead to corrosion or weakening of the reinforcement, particularly in environments with harsh chemicals or moisture.
Shortened Hose Lifespan: Continuous external abrasion significantly reduces the overall lifespan of the hose. Even if the hose does not fail immediately, the constant wear and tear will eventually lead to failure, requiring premature replacement.
Preventing abrasion-related failures requires proper installation practices that ensure the hose is not bent too tightly and is routed in a way that avoids contact with other surfaces.
Internal Damage
Internal Weakening of the Hose Walls Due to Excessive Bending
The internal layers of a hydraulic hose are equally at risk when the bend radius is exceeded. Repeated or extreme bending causes fatigue within the hose’s internal structure, which can lead to fractures and cracks over time. This internal damage is often more insidious than external damage because it is not immediately visible, yet it can have equally catastrophic consequences.
Fatigue: Excessive bending puts stress on the hose’s inner tube, which is responsible for containing and directing the flow of hydraulic fluid. Over time, this stress leads to material fatigue, weakening the hose’s ability to contain high-pressure fluids. Fatigue-induced damage often manifests as small cracks or splits in the inner tube, which can progressively worsen with continued use.
Fractures: In extreme cases, internal fractures can develop within the hose. These fractures occur when the material is overstressed to the point of breaking. Once fractures appear, the hose becomes highly susceptible to leaks and failure under pressure. Fractures can also spread, causing entire sections of the hose to lose their structural integrity.
Internal damage is particularly dangerous because it can lead to sudden and unexpected hose failure. In high-pressure applications, even a small fracture can quickly turn into a rupture, resulting in the loss of hydraulic fluid, system failure, and potential safety hazards for workers.
Conclusion
To protect hydraulic systems and extend the life of hoses, best practices for hose maintenance and system design should always be followed. These practices include proper installation techniques, regular inspections for signs of wear, and selecting hoses that are suitable for the environmental and operational conditions. Taking the time to ensure that hoses are installed with the correct bend radius will significantly reduce the likelihood of failures and help maintain the overall efficiency of the system.
FAQ
What is a hydraulic hose bend radius?
The bend radius is the smallest curve a hose can form without causing damage. Adhering to the minimum bend radius prevents kinking, flow obstruction, and hose failure.
Why is maintaining the minimum bend radius important?
Maintaining the correct bend radius prevents premature wear, leaks, and safety hazards, ensuring the hose performs efficiently and lasts longer.
What happens if the bend radius is too small?
If the bend radius is too small, the hose may kink, leading to flow restrictions, pressure buildup, and potential hose rupture.
How is the bend radius calculated?
The minimum bend radius is determined by the hose diameter and construction. Hose manufacturers provide specific bend radius guidelines for each hose type.
Does hose material affect the bend radius?
Yes, different materials (rubber, thermoplastic, PTFE) have varying flexibility, which impacts the allowable bend radius. More rigid materials require a larger bend radius.
How can I avoid exceeding the bend radius?
Ensure proper hose installation and use accessories like clamps or bend restrictors to maintain the correct bend radius and prevent damage. Regular inspections are also key to preventing issues.