Thermoplastic hoses offer a new dimension to hose technology, presenting several advantages over their rubber counterparts. Made from a combination of thermoplastic materials, these hoses are designed to withstand demanding conditions with enhanced performance characteristics. Unlike rubber hoses, which can degrade over time due to factors like heat, abrasion, and chemicals, thermoplastic hoses provide superior durability and resilience.
Exceptional Durability
Introduction to Durability in Hydraulic Hoses
Durability is a critical factor in the performance and longevity of hydraulic hoses. In industrial settings, hoses are exposed to extreme conditions, including high pressures, fluctuating temperatures, and various chemical environments. The ability of a hose to withstand these challenges directly impacts the efficiency of hydraulic systems and the safety of operations. Durable hoses help prevent failures, reduce maintenance, and ensure consistent performance, making them essential components in any hydraulic system.
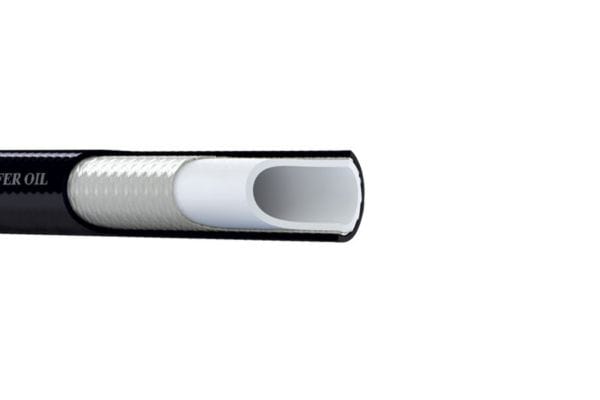
Thermoplastic vs. Rubber
When comparing thermoplastic hoses to traditional rubber hoses, the difference in durability is striking. Thermoplastic hoses are engineered to resist a range of stresses more effectively than their rubber counterparts. For instance, thermoplastic materials are inherently more resistant to abrasion, which is crucial for hoses that encounter rough surfaces or are subject to frequent movement. Additionally, these hoses excel in resisting chemical degradation, making them ideal for applications where exposure to corrosive substances is common.
Another significant advantage of thermoplastic hoses is their performance under extreme temperatures. While rubber hoses can become brittle and lose flexibility in cold environments or soften and swell in high heat, thermoplastic hoses maintain their integrity across a broader temperature range. This ensures reliable operation in both freezing and high-temperature conditions, reducing the risk of hose failure due to thermal stress.
Maintenance Implications
The enhanced durability of thermoplastic hoses translates into significant maintenance benefits. Since these hoses are more resistant to abrasion, chemicals, and temperature extremes, they experience less wear and tear compared to rubber hoses. This reduced degradation leads to fewer hose replacements and less frequent repairs, which translates into lower maintenance costs and minimized downtime.
In practical terms, the longevity of thermoplastic hoses means that maintenance teams can focus on other aspects of system upkeep rather than constantly addressing hose issues. The reduced need for replacements and repairs also contributes to the overall efficiency of hydraulic systems, as the risk of unexpected hose failures and related downtime is minimized. This durability not only supports smoother operations but also enhances the safety and reliability of industrial processes.
Lightweight and Flexible
Importance of Hose Weight and Flexibility
The weight and flexibility of hydraulic hoses are crucial factors in their overall performance and usability. In many industrial applications, hoses are required to navigate tight spaces, move frequently, or be handled manually. Heavier hoses can be cumbersome and difficult to manage, leading to increased labor and potential safety hazards during installation and maintenance. Similarly, hoses that lack flexibility can be challenging to route and position, which may require additional fittings or modifications to the system.
The ability of a hose to bend and flex without compromising its structural integrity is essential for maintaining the efficiency of hydraulic systems. Flexibility allows hoses to accommodate dynamic movements and alignments, reducing the risk of damage and ensuring smooth fluid transfer. Therefore, selecting hoses that offer both lightweight and flexible characteristics can significantly enhance the ease of handling, installation, and long-term performance.
Advantages of Lightweight Thermoplastic Hoses
Thermoplastic hoses are renowned for their lightweight nature, a distinct advantage over traditional rubber hoses. The reduced weight of thermoplastic hoses makes them easier to handle, transport, and install, which can be particularly beneficial in environments where manual handling is required. This advantage is not only about ease of use but also about improving overall operational efficiency.
Compared to rubber hoses, which can be relatively heavy and less manageable, thermoplastic hoses provide a more user-friendly alternative. The lighter weight reduces the physical strain on workers and equipment, making it easier to maneuver hoses into position. Additionally, the reduced weight can lead to lower shipping costs and easier storage, further contributing to the cost-effectiveness of thermoplastic hoses.
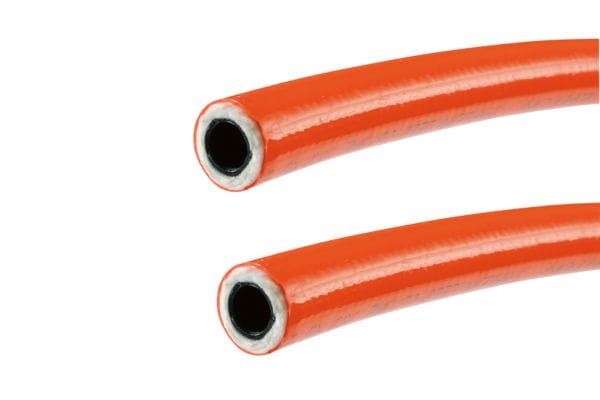
Increased Flexibility
One of the standout features of thermoplastic hydraulic hoses is their increased flexibility. Unlike rubber hoses, which may stiffen over time or become less flexible in colder temperatures, thermoplastic hoses maintain their pliability across a wide range of conditions. This enhanced flexibility allows thermoplastic hoses to be bent and maneuvered easily without kinking or collapsing, which is essential for complex hydraulic systems where precise routing is required.
The ability to navigate tight spaces and fit into challenging configurations without sacrificing performance is a significant benefit. This flexibility also reduces the need for additional fittings or adapters, which can simplify system design and installation. Moreover, the resilience of thermoplastic hoses to bending and twisting ensures consistent fluid flow and minimizes the risk of pressure drops or leaks.
Impact on System Design
In complex or space-constrained hydraulic systems, the use of lightweight and flexible thermoplastic hoses can provide substantial design benefits. Their ability to be routed easily through tight spaces and around obstacles allows for more efficient use of available space, potentially reducing the overall size and complexity of the hydraulic system. This can lead to a more streamlined and compact design, which is especially valuable in applications where space is at a premium.
Furthermore, the flexibility of thermoplastic hoses can simplify the design process by reducing the need for excessive fittings or custom configurations. This can lead to lower installation costs and faster setup times. The ease of handling and installation also contributes to a more efficient workflow, allowing for quicker system assembly and reduced labor costs.
Resistance to Environmental Factors
Environmental Challenges for Hydraulic Hoses
Hydraulic hoses operate in diverse environments, each presenting unique challenges that can affect their performance and longevity. Common environmental factors that impact hose durability include UV exposure, ozone, moisture, and extreme temperatures. UV rays can degrade materials, causing them to become brittle and crack over time. Ozone, a reactive gas present in the atmosphere, can deteriorate rubber compounds, leading to weakened hoses. Moisture, particularly in the form of water or chemicals, can cause corrosion or swelling, compromising the hose’s integrity. Additionally, extreme temperatures, both high and low, can affect the flexibility and strength of the hose material, leading to potential failures.
Thermoplastic Hoses’ Resistance
Thermoplastic hoses are engineered to resist these environmental challenges more effectively than traditional rubber hoses. The materials used in thermoplastic hoses are inherently more resistant to UV radiation and ozone, which helps prevent degradation and extends the hose’s usable life. These hoses are also designed to resist moisture absorption, reducing the risk of corrosion and swelling. Their performance in extreme temperatures is another critical advantage; thermoplastic hoses maintain their flexibility and strength in both high and low temperatures, ensuring reliable operation across a wide range of conditions.
The advanced material composition of thermoplastic hoses allows them to perform consistently even when exposed to harsh environmental factors. For example, their resistance to UV and ozone means they are less likely to suffer from surface cracking and brittleness, which can lead to hose failure. Their moisture resistance ensures that they remain functional and reliable, even in wet or corrosive environments.
Applications in Harsh Environments
Thermoplastic hoses excel in a variety of challenging conditions, demonstrating their adaptability and resilience. They are commonly used in industries such as agriculture, construction, and mining, where hoses are frequently exposed to harsh weather conditions and abrasive environments. In agricultural settings, for instance, these hoses are used in irrigation systems where they face UV exposure and moisture. In construction and mining, thermoplastic hoses are subjected to dust, mud, and extreme temperatures, making their resistance to environmental factors particularly valuable.
One notable application is in offshore drilling operations, where hoses must endure saltwater exposure, high pressure, and extreme temperatures. Thermoplastic hoses are favored in these environments for their ability to withstand corrosive saltwater and maintain performance under pressure and temperature fluctuations. Similarly, in the automotive industry, where hoses face exposure to engine heat, oil, and chemicals, thermoplastic options provide durability and reliability that can enhance vehicle performance and safety.
Longevity and Performance
The resistance of thermoplastic hoses to environmental factors significantly contributes to their longevity and overall performance. By withstanding UV radiation, ozone, moisture, and temperature extremes, these hoses experience less degradation over time compared to rubber hoses. This resistance helps prevent issues such as cracking, swelling, and weakening, which are common in less durable hose materials.
The result is a longer lifespan for thermoplastic hoses, reducing the frequency of replacements and maintenance. This extended durability not only enhances the reliability of hydraulic systems but also provides cost savings over the long term. The improved performance in challenging conditions ensures that hydraulic systems remain operational and efficient, even in demanding environments.
Enhanced Safety Features
Safety Considerations in Hydraulic Systems
Safety is paramount in hydraulic systems due to the high pressures and potentially hazardous fluids involved. Leaks or failures in hydraulic hoses can lead to significant operational risks, including equipment damage, system downtime, and even personal injury. Ensuring that hoses are reliable and robust is critical for maintaining the integrity of hydraulic systems and protecting personnel and machinery.
Hose safety encompasses several factors, including pressure tolerance, material integrity, and resistance to environmental stressors. A hose must be able to withstand internal pressures without bursting, resist external wear and tear, and maintain its functionality in various environmental conditions. Proper hose selection and maintenance are essential to minimize risks and ensure safe operation.
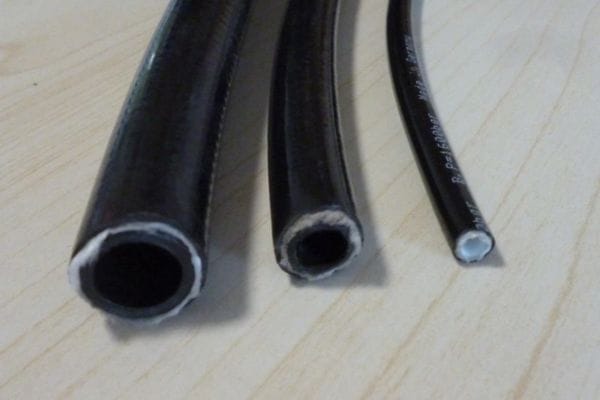
Thermoplastic Hoses and Safety
Thermoplastic hoses are designed with several safety features that enhance their performance and reduce the risk of failures. One of the key safety aspects of thermoplastic hoses is their burst resistance. These hoses are constructed to handle high pressures, and their material composition allows them to withstand and operate effectively under extreme conditions without bursting. This burst resistance is crucial for preventing catastrophic failures that could lead to leaks or hazardous situations.
Additionally, thermoplastic hoses are designed to have a reduced risk of leaks compared to traditional hoses. The smooth inner surface of these hoses minimizes turbulence and friction, which helps prevent the formation of weak spots and reduces the likelihood of leaks. Their resistance to abrasion and chemicals also contributes to maintaining the hose’s integrity over time, further lowering the risk of leaks.
Comparison with Rubber Hoses
When compared to traditional rubber hoses, thermoplastic hoses offer several safety advantages. Rubber hoses, while flexible and initially durable, can degrade over time due to exposure to UV rays, ozone, and extreme temperatures. This degradation can weaken the hose material, increasing the risk of leaks and bursts. In contrast, thermoplastic hoses are less susceptible to such environmental factors, which means they maintain their safety features for a longer period.
Furthermore, the construction of thermoplastic hoses often includes features such as reinforced layers and improved bonding techniques, which enhance their overall strength and resistance to failure. These design improvements make thermoplastic hoses a safer choice, particularly in high-pressure and high-risk applications.
Regulatory Standards and Compliance
Thermoplastic hoses are designed to meet or exceed various safety standards and regulations, ensuring that they provide reliable and compliant performance. These hoses are often subjected to rigorous testing and certification processes to verify their ability to withstand pressure, resist environmental stresses, and maintain safety under operational conditions.
For example, many thermoplastic hoses comply with standards such as SAE (Society of Automotive Engineers) or ISO (International Organization for Standardization), which specify performance criteria for hydraulic hoses. Compliance with these standards indicates that the hoses have been tested for safety and reliability, providing an additional layer of assurance for users.
In addition to meeting industry standards, thermoplastic hoses may also adhere to specific regulatory requirements for various applications, such as those related to environmental protection or safety in hazardous environments. This adherence to regulations ensures that thermoplastic hoses not only perform effectively but also contribute to a safer working environment.
Cost-Effectiveness
Cost Factors in Hydraulic Hose Selection
When selecting hydraulic hoses, several cost factors need to be considered to determine the most economical choice for a given application. The initial cost of the hose is an obvious factor, but it is crucial to also evaluate long-term costs associated with maintenance, replacements, and operational efficiency.
Initial Cost: This is the upfront expenditure for purchasing the hose. While thermoplastic hoses may have a higher initial cost compared to some rubber hoses, it is essential to look beyond this figure to understand the complete financial picture.
Maintenance Costs: Hydraulic hoses require regular inspection and maintenance to ensure they are functioning correctly and to prevent unexpected failures. Hoses that are more resistant to wear, environmental factors, and pressure fluctuations typically incur lower maintenance costs over their lifespan.
Replacement Costs: Frequent hose replacements can be costly, both in terms of the price of new hoses and the labor involved in installation. Hoses that are prone to wear and tear will need to be replaced more often, increasing overall costs.
Long-Term Cost Benefits of Thermoplastic Hoses
Thermoplastic hoses offer significant long-term cost benefits due to their durability and reduced maintenance needs.
Durability: The exceptional durability of thermoplastic hoses means they are less likely to suffer from issues such as abrasion, chemical degradation, and temperature-related wear. This enhanced longevity results in fewer replacements over time, translating into direct cost savings.
Reduced Maintenance: Thermoplastic hoses typically require less maintenance compared to rubber hoses due to their resistance to environmental factors and their robust construction. This reduction in maintenance needs lowers labor costs and minimizes downtime, leading to further cost savings.
Fewer Replacements: The longer service life of thermoplastic hoses means that replacements are less frequent. Fewer replacements not only reduce the cost of new hoses but also minimize the labor costs associated with changing hoses and the associated downtime for system repairs.
Conclusion
In conclusion, thermoplastic hoses offer numerous advantages that make them a superior choice for various industrial applications. Their combination of durability, flexibility, environmental resistance, safety, and cost-effectiveness provides a compelling case for their adoption. For those looking to enhance their hydraulic systems, exploring thermoplastic hoses could prove to be a valuable decision.
FAQ
What are thermoplastic hoses?
Thermoplastic hoses are hoses made from thermoplastic materials, designed to handle high pressures and various environmental conditions in hydraulic systems. They are an alternative to traditional rubber hoses.
What are the key benefits of thermoplastic hoses?
The main benefits include exceptional durability, lightweight and flexibility, resistance to environmental factors, enhanced safety features, and cost-effectiveness.
How do thermoplastic hoses compare to rubber hoses in terms of durability?
Thermoplastic hoses generally offer superior durability compared to rubber hoses, resisting abrasion, chemicals, and extreme temperatures more effectively.
Are thermoplastic hoses suitable for harsh environments?
Yes, thermoplastic hoses are designed to withstand harsh conditions, including UV exposure, ozone, moisture, and extreme temperatures, making them ideal for challenging environments.
Do thermoplastic hoses offer safety advantages?
Yes, they have enhanced safety features such as burst resistance and reduced risk of leaks, contributing to safer hydraulic system operations.
Are thermoplastic hoses cost-effective?
Despite a higher initial cost, thermoplastic hoses are cost-effective in the long run due to their durability, reduced maintenance, and fewer replacements, offering significant long-term savings.