Imagine this: You’re on a long road trip, and you notice that your brakes feel a bit off. After pulling over to inspect the issue, you discover a small leak in one of your brake lines. With limited tools and resources on hand, you start thinking, “Could I temporarily fix this with a piece of rubber hose until I can get proper repairs?” It seems like a quick and easy solution, but is it safe?
Understanding Brake Lines
What Are Brake Lines?
Brake lines are an integral component of a vehicle’s braking system, responsible for transmitting hydraulic pressure from the master cylinder to the brake calipers or wheel cylinders at each wheel. When you press the brake pedal, the master cylinder forces brake fluid through these lines, creating the necessary pressure to activate the brakes. This process ensures that your vehicle slows down or comes to a complete stop when needed.
Materials Commonly Used in Brake Lines
Brake lines are typically made from materials that can withstand high pressure and resist corrosion over time. The most common materials used include:
Steel: Standard steel brake lines are strong and durable, offering excellent resistance to pressure. However, they can be prone to rust if not properly maintained.
Stainless Steel: Stainless steel brake lines are more resistant to rust and corrosion compared to regular steel. They are often preferred in performance vehicles and in regions where road salt is commonly used.
Nylon-Coated Steel: Some brake lines are made from steel that is coated with a layer of nylon for additional protection against corrosion and physical damage.
These materials are chosen for their ability to handle the demanding environment within a vehicle’s braking system, where both high pressure and temperature variations are constant factors.
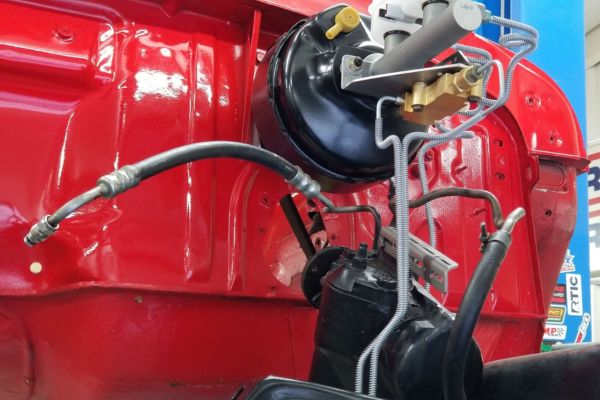
Types of Brake Lines
Rigid Brake Lines:
Material: Typically made from steel or stainless steel.
Usage: These lines are used in areas of the vehicle where they are less likely to be exposed to movement or flexing, such as along the frame or chassis.
Characteristics: Rigid brake lines are known for their durability and ability to withstand high pressures without deforming. They are often custom-bent to fit the specific contours of a vehicle.
Flexible Brake Lines:
Material: Usually made from reinforced rubber or braided stainless steel.
Usage: Flexible brake lines are used in areas where the brake lines need to accommodate movement, such as between the vehicle’s frame and the wheels.
Characteristics: These lines are designed to flex and move with the suspension and steering components. They are essential for maintaining consistent brake pressure while the vehicle is in motion.
Comparison of Metal and Rubber Brake Lines
Metal Brake Lines:
Advantages: High strength, resistance to pressure, and longevity. Metal brake lines provide more consistent and reliable braking performance over time.
Disadvantages: Can be prone to rust if not properly coated or maintained, especially in harsh climates. Rigid lines are less flexible and may be challenging to install in tight spaces.
Rubber Brake Lines:
Advantages: Flexibility allows for easy installation in areas that require movement. They are also less expensive and easier to replace compared to metal lines.
Disadvantages: Rubber lines are more prone to wear, cracking, and swelling over time, especially when exposed to extreme temperatures or corrosive elements. They are also less resistant to high pressure, which can compromise their effectiveness in the braking system.
Rubber Hoses vs Brake Lines
Composition of Rubber Hoses
Inner Tube: The innermost layer, made from a rubber compound that is resistant to the fluid it will carry. This layer ensures that the hose does not degrade from the inside out due to exposure to fluids like water, oil, or other chemicals.
Reinforcement Layer: Surrounding the inner tube, this layer is often made from braided textile fibers, spiral wound wire, or synthetic yarns. The reinforcement layer provides strength and helps the hose withstand moderate pressure. It also gives the hose its characteristic flexibility.
Outer Cover: The exterior layer protects the inner layers from environmental factors such as abrasion, ozone, heat, and oil. The outer cover is often made from a durable rubber compound that resists wear and tear.
Comparison with the Materials Used in Brake Lines
Unlike standard rubber hoses, brake lines are designed to handle much higher pressures and are constructed from materials specifically engineered to resist the extreme conditions within a vehicle’s braking system.
Material Strength: Brake lines are typically made from steel, stainless steel, or reinforced synthetic materials, which provide significantly higher pressure resistance compared to rubber hoses.
Pressure Tolerance: Brake lines can withstand the hydraulic pressure generated in a braking system, which can exceed 1,500 psi. Standard rubber hoses, on the other hand, are generally rated for much lower pressures and would fail under such high demands.
Temperature Resistance: Brake lines are designed to resist the high temperatures generated during braking, whereas rubber hoses may soften, crack, or swell when exposed to excessive heat.
The difference in materials means that rubber hoses simply do not possess the structural integrity or pressure resistance required for use in brake systems.
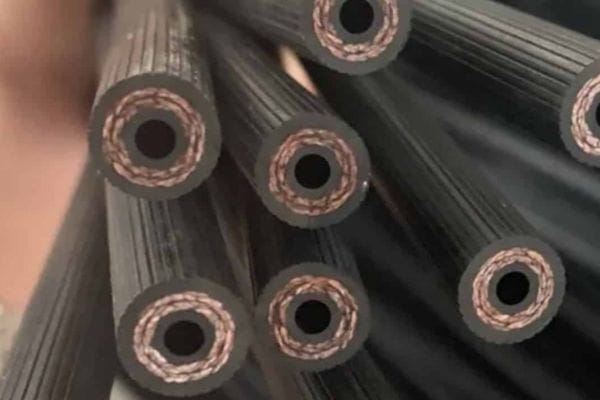
Why Rubber Hoses Are Not Suitable for Brake Lines
Pressure and Temperature Resistance
Brake systems operate under extreme conditions, with hydraulic pressure often reaching over 1,500 psi. Additionally, the heat generated from friction during braking can cause temperatures to rise significantly. Rubber hoses, while flexible and useful in many applications, are not engineered to handle such intense pressure or temperature:
Pressure Resistance: Rubber hoses are typically rated for lower-pressure applications. When exposed to the high pressures within a brake system, they can expand, weaken, or even burst, leading to brake failure.
Temperature Resistance: Rubber hoses can degrade when exposed to the high temperatures generated during braking. The material may soften or become brittle, leading to cracking or splitting, which can cause leaks or total failure.
Durability and Lifespan Concerns
Rubber hoses are generally more prone to wear and tear compared to the materials used in brake lines. Over time, they can suffer from:
Aging: Rubber deteriorates with age, especially when exposed to environmental factors like UV light, ozone, and temperature extremes. This aging process can cause the hose to become brittle and crack, leading to leaks.
Swelling: Exposure to brake fluid, which is often incompatible with standard rubber compounds, can cause the inner layers of a rubber hose to swell. This swelling can reduce the internal diameter of the hose, leading to restricted fluid flow and impaired braking performance.
Wear and Tear: Rubber hoses are more susceptible to physical damage from abrasions, cuts, and punctures. This makes them less reliable in harsh environments where they are exposed to debris and other hazards.
Risk of Leaks, Swelling, and Failure Under Pressure
The combination of lower pressure tolerance, reduced temperature resistance, and decreased durability makes rubber hoses unsuitable for brake line applications. The primary risks include:
Leaks: As rubber hoses degrade or swell, they are more likely to develop leaks, which can cause a loss of brake fluid and a corresponding loss of braking power.
Swelling: Swollen hoses can impede the flow of brake fluid, resulting in delayed or reduced braking response, which is particularly dangerous in emergencies.
Failure Under Pressure: In extreme cases, a rubber hose used in a brake system could burst due to the high pressure, leading to immediate and total brake failure. This poses a significant safety hazard for the driver and others on the road.
Potential Risks of Using Rubber Hoses for Brake Lines
Safety Hazards
Immediate Dangers: Brake Failure and Reduced Braking Efficiency One of the most critical safety hazards of using rubber hoses in place of proper brake lines is the immediate risk of brake failure. When a rubber hose is used in a braking system, it is not equipped to handle the high hydraulic pressure required for effective braking. This can lead to:
Brake Failure: Under intense pressure, a rubber hose may expand or burst, leading to a sudden and complete loss of brake fluid. This results in brake failure, leaving the driver unable to stop the vehicle, which can lead to severe accidents.
Reduced Braking Efficiency: Even if the hose doesn’t fail outright, the expansion of a rubber hose under pressure can cause a delayed response when the brake pedal is pressed. This reduced efficiency can increase stopping distances, making it difficult to avoid collisions, especially in emergencies.
Long-Term Risks: Gradual Degradation and Unexpected Failure Beyond the immediate dangers, rubber hoses used in brake systems pose significant long-term risks due to their tendency to degrade over time:
Gradual Degradation: Rubber is susceptible to environmental factors such as UV light, ozone, and temperature fluctuations. Over time, these elements can cause the rubber to crack, harden, or become brittle, increasing the likelihood of leaks or failure.
Unexpected Failure: The gradual wear and tear on a rubber hose can lead to unexpected failure, often without warning. A small crack or pinhole leak can quickly escalate, causing a sudden loss of brake fluid and, subsequently, brake function. This unpredictability makes rubber hoses a dangerous choice for brake lines, where reliability is paramount.
These safety hazards underscore the importance of using materials specifically designed for brake lines, which are engineered to withstand the demands of the braking system and ensure consistent, reliable performance.
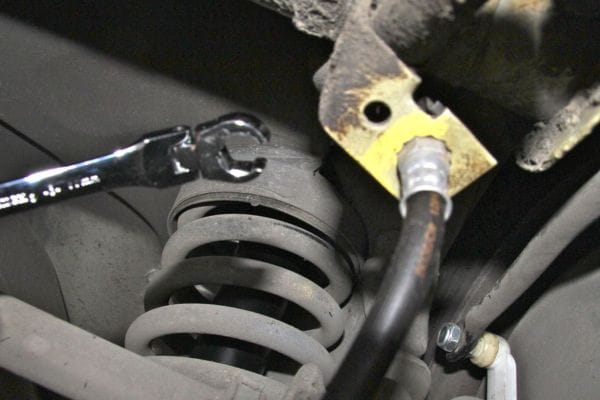
Legal and Regulatory Implications
Legal Requirements for Brake Line Repairs in Various Regions
Brake line repairs are subject to strict legal and regulatory standards in many regions, reflecting the critical role brake systems play in vehicle safety. These regulations typically mandate:
Approved Materials: Only materials that meet specific standards for pressure and temperature resistance are legally allowed for use in brake line repairs. Rubber hoses, not meeting these stringent criteria, are often prohibited.
Professional Installation: In many jurisdictions, brake line repairs must be performed by certified professionals to ensure compliance with safety regulations. Using improper materials like rubber hoses could result in legal penalties or vehicle inspection failures.
Insurance and Liability Issues Associated with Improper Repairs
Using a rubber hose for brake line repairs not only violates legal standards but can also lead to significant insurance and liability issues:
Insurance Coverage: If an accident occurs due to brake failure linked to the use of a rubber hose, insurance companies may refuse to cover the damages. Policies often require that vehicle repairs are performed to industry standards, and the use of non-compliant materials could void coverage.
Proper Materials and Methods for Brake Line Repairs
Approved Brake Line Materials
When it comes to brake line repairs, using the correct materials is crucial for ensuring safety and reliability. The most commonly approved materials for brake lines include:
Steel Brake Lines:
Composition: Standard steel brake lines are made from mild steel, often coated to prevent corrosion.
Use Case: These are typically found in most vehicles and provide a balance between strength, durability, and cost-effectiveness.
Stainless Steel Brake Lines:
Composition: Made from high-grade stainless steel, these lines offer superior corrosion resistance.
Use Case: Ideal for performance vehicles or in regions with harsh climates where road salt and moisture are prevalent. They are often used in aftermarket upgrades due to their durability.
Copper-Nickel (Cupronickel) Brake Lines:
Composition: A blend of copper and nickel, these brake lines are known for their excellent corrosion resistance and ease of installation.
Use Case: Commonly used in European vehicles, Cupronickel lines are flexible and resistant to rust, making them a popular choice for brake line replacements.
Braided Stainless Steel Hoses:
Composition: These flexible hoses consist of an inner Teflon (PTFE) or rubber core, wrapped in a braided stainless steel exterior.
Use Case: Often used in high-performance applications, these hoses provide flexibility while maintaining high pressure resistance. They also improve brake pedal feel by reducing the expansion that occurs in rubber hoses.
Benefits of Using Stainless Steel and Other Durable Materials
Corrosion Resistance: Stainless steel and Cupronickel brake lines offer superior resistance to corrosion, which is a major factor in the longevity and reliability of brake lines. This is particularly important in regions where vehicles are exposed to road salt or moisture.
Durability: Materials like stainless steel and braided steel hoses are more durable than standard rubber hoses, resisting wear and tear over time. This durability ensures that the brake lines maintain their integrity and continue to function effectively under high pressure and temperature conditions.
Enhanced Performance: Using high-quality materials like braided stainless steel hoses can improve brake performance by minimizing line expansion, which leads to a firmer brake pedal feel and more responsive braking.
Techniques for Safe Brake Line Repairs
Proper brake line repair or replacement is a precise task that requires attention to detail and adherence to safety standards. Here is a step-by-step guide:
Preparation:
Safety First: Ensure the vehicle is on a stable, level surface and is securely supported with jack stands.
Gather Materials and Tools: Have the necessary brake line material, fittings, and tools (wrenches, flaring tool, brake fluid, etc.) ready before beginning the repair.
Removing the Damaged Brake Line:
Locate the Damaged Section: Identify the portion of the brake line that needs to be replaced.
Drain the Brake Fluid: Carefully drain the brake fluid from the system to avoid spills and contamination.
Disconnect the Brake Line: Use the appropriate wrenches to disconnect the damaged brake line from the brake system. Be careful not to damage the fittings or surrounding components.
Cutting and Bending the New Brake Line:
Measure the Replacement Line: Measure the length of the old brake line to ensure the new line is cut to the correct size.
Cut the Brake Line: Use a brake line cutter to make a clean, precise cut.
Bend the Line: Using a brake line bending tool, carefully shape the new line to match the contours of the vehicle’s chassis. Avoid kinks or sharp bends that could impede fluid flow.
Flaring the Ends:
Prepare the Ends: Ensure the ends of the brake line are smooth and free from burrs.
Use a Flaring Tool: Create the necessary flares (single or double flare, depending on the vehicle’s specifications) on the ends of the brake line to ensure a secure connection with the fittings.
Installing the New Brake Line:
Connect the Brake Line: Attach the new brake line to the brake system using the appropriate fittings. Tighten securely but avoid over-tightening, which can damage the fittings.
Bleed the Brake System: After installation, bleed the brake system to remove any air that may have entered during the repair process. This step is crucial to restoring full braking performance.
Final Inspection and Testing:
Check for Leaks: Inspect all connections and joints for leaks. Tighten as necessary.
Test the Brakes: Carefully test the brake pedal for firmness and response. Conduct a low-speed test drive in a safe area to ensure the brakes are functioning properly.
Conclusion
In conclusion, rubber hoses are unsuitable for brake lines due to their inability to withstand the high pressures and temperatures required for safe braking. Their tendency to degrade over time poses significant safety risks, including potential brake failure. It’s essential to use proper materials like stainless steel or approved brake line materials and to follow safe repair practices to ensure the reliability of your braking system. Always consult a professional for brake line repairs and regular maintenance.
FAQ
Can I use a rubber hose for a temporary brake line repair?
No, rubber hoses are not suitable for brake line repairs due to their inability to handle high pressure and temperature.
Why are rubber hoses unsafe for brake lines?
Rubber hoses lack the necessary pressure and temperature resistance, leading to potential brake failure.
What materials are approved for brake line repairs?
Approved materials include steel, stainless steel, and copper-nickel (Cupronickel) brake lines.
What are the risks of using a rubber hose for brake lines?
The risks include brake fluid leaks, reduced braking efficiency, and sudden brake failure.
Is it legal to use rubber hoses for brake lines?
No, using rubber hoses for brake lines is generally not compliant with legal and safety standards.
Should I perform brake line repairs myself?
It’s recommended to consult a professional for brake line repairs to ensure safety and compliance with regulations.