A common question often arises: Can you safely combine different hose and fitting brands within the same system? This inquiry usually stems from practical considerations like availability, cost, or convenience. Yet, despite the potential benefits, mixing brands comes with notable risks. Mismatched components can result in leaks, reduced performance, increased wear, and even complete system failure.
Why Matching Components is Crucial
In hydraulic systems, the compatibility of hoses and fittings is not just a matter of convenience; it’s essential for maintaining system integrity, safety, and performance. Mismatching components can result in severe consequences, including leaks, equipment damage, and safety hazards.
Compatibility Concerns
1. Manufacturing Specifications and Design Parameters
Hoses and fittings are designed with specific parameters, such as diameter, pressure rating, and connection types, which are tailored to work with components from the same manufacturer. Each manufacturer follows its own set of specifications to ensure the components are optimized for performance, safety, and durability. When components from different brands are mixed, there is a risk of incompatibility in these parameters. For instance, a hose designed to operate at a specific pressure might not perform effectively with a fitting with a different pressure rating, potentially leading to underperformance or failure.
2. Differences in Manufacturing Tolerances
Hydraulic components are made with precise tolerances, which dictate how tightly they fit together and how well they perform under pressure. Even small variations in manufacturing tolerances can impact the effectiveness of the seal between the hose and fitting. Different manufacturers may have slight variations in their design, even for components labeled with the same specifications. These differences can result in poor sealing, increased wear, or the inability to maintain adequate pressure, thereby increasing the risk of leaks and malfunctions.
Impact on System Safety
1. Potential Safety Risks
Mismatched components can pose significant safety risks in hydraulic systems, where fluid is often under high pressure. A poor connection between the hose and fitting can lead to leaks, resulting in fluid spraying out at high velocities. This not only presents a physical hazard to workers but can also cause damage to nearby machinery or products. In the worst-case scenario, a complete disconnection under pressure can lead to catastrophic failures, risking serious injury or extensive equipment damage. Therefore, ensuring that components are designed to work seamlessly together is crucial for maintaining a safe working environment.
2. Loss of Pressure Integrity
Hydraulic systems rely on maintaining consistent pressure to function effectively. If components are not properly matched, there can be a significant loss of pressure due to inadequate sealing or mismatched flow rates. This pressure drop can affect the entire system’s performance, making it less efficient and unreliable. Even a minor drop in pressure can have costly consequences in industries where precision and consistency are critical.
Loss of Performance
1. Reduced Efficiency
Hydraulic systems are designed for optimal performance, but mismatched components can lead to inefficiencies. For example, a fitting with a lower flow capacity paired with a high-capacity hose can create a bottleneck, reducing the system’s overall performance. This inefficiency may increase energy consumption, operational costs, and the likelihood of overheating, which can further degrade system components.
2. Increased Wear and Tear
Mismatched hoses and fittings can accelerate wear and tear on system components. If components are not properly aligned or sealed, increased friction and pressure fluctuations can occur, leading to faster degradation. Over time, this can result in more frequent maintenance requirements, increased downtime, and ultimately higher costs for repairs or replacements.
3. Decreased Reliability and Durability
Reliability is a key factor in hydraulic systems, especially in critical applications like heavy machinery, construction, or industrial manufacturing. When hoses and fittings are mismatched, system reliability decreases as the potential for leaks, pressure loss, and component failures rises. This not only impacts productivity but can also affect the longevity of the equipment, leading to higher operational costs over time.
Common Challenges of Mixing Hoses and Fittings
Combining hoses and fittings from different manufacturers might seem like a cost-effective or convenient solution. However, this approach brings several challenges that can compromise the performance, safety, and reliability of hydraulic systems. Here, we’ll discuss some of the most common challenges encountered when mixing components: variations in pressure ratings, material differences, and thread and coupling mismatches.
Pressure Rating Variations
1. Mismatch in Pressure Capacity
One of the most critical aspects of hydraulic components is their pressure rating, which specifies the maximum pressure they can safely handle. Different manufacturers may use varying design parameters, leading to significant differences in pressure capacity. For example, a hose designed to withstand high pressure may not be compatible with a fitting that has a lower pressure rating. This discrepancy can create a weak point in the system, increasing the risk of leaks or even catastrophic failure.
2. Impact on System Performance
When components with mismatched pressure ratings are combined, the system may not perform as expected. The fitting could become the limiting factor, restricting the system’s overall pressure capacity and reducing efficiency. This bottleneck can also cause pressure fluctuations, leading to inconsistent system performance, reduced productivity, and potentially more frequent maintenance requirements.
3. Safety Hazards
Operating a hydraulic system with components that have different pressure ratings can be hazardous. If the system exceeds the lower pressure capacity of one component, it can result in sudden failure, creating a risk of fluid ejection under high pressure. This not only poses safety risks to personnel but can also damage other equipment, leading to costly downtime and repairs.
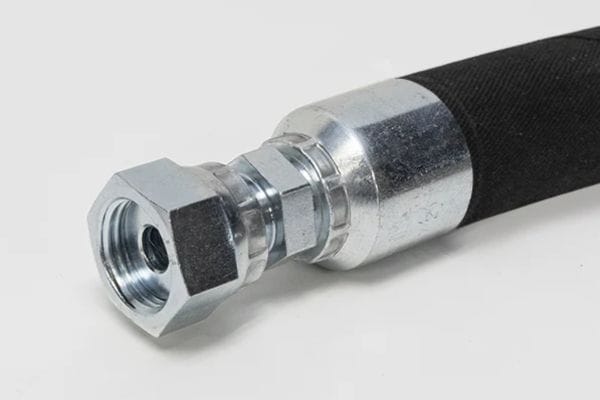
Material Differences
1. Potential Chemical Reactions
The materials used in hoses and fittings are often chosen based on the fluids they will transport and the environmental conditions they will encounter. When mixing components from different brands, there is a risk of using incompatible materials, which can cause chemical reactions. For example, a hose made from one type of rubber may react adversely with a fitting made from a different metal alloy, leading to material degradation. This chemical incompatibility can compromise the seal between the hose and fitting, increasing the likelihood of leaks.
2. Corrosion Risks
Even if the materials are chemically compatible with the hydraulic fluid, mixing different metals can create galvanic corrosion. This type of corrosion occurs when dissimilar metals come into contact with each other in the presence of an electrolyte, such as water or hydraulic fluid. For instance, combining a steel fitting with an aluminum hose end can lead to accelerated corrosion, weakening the joint and potentially causing leaks or failures over time.
3. Decreased Component Longevity
Material differences can also affect the overall durability and lifespan of hydraulic components. Incompatible materials may wear at different rates, creating uneven stresses and accelerating component failure. This can result in higher maintenance costs and the need for more frequent replacements, negating any initial cost savings from using mixed brands.
Thread and Coupling Issues
1. Importance of Thread Matching
Threads play a crucial role in securing hydraulic connections, ensuring that hoses and fittings remain tightly coupled under pressure. Different manufacturers may use slightly different thread designs or dimensions, even within the same thread type category. This can lead to poor fits, which compromise the connection’s ability to maintain pressure and resist vibrations. In hydraulic systems, even minor differences in thread design can result in inadequate sealing, leading to leaks.
2. Secure Connections for Safety
A secure, leak-free connection is essential for hydraulic system safety. When threads do not match properly, there is an increased risk of the hose detaching from the fitting, especially under high pressure. This can be extremely dangerous, as hydraulic fluid can spray at high velocity, potentially injuring personnel and damaging surrounding equipment.
3. Cross-Threading Risks
Attempting to force mismatched threads together can result in cross-threading, which damages the threads and prevents a secure seal. Cross-threading not only weakens the connection but also makes future repairs more difficult, as damaged threads may require re-tapping or replacement. This further increases maintenance costs and downtime.
Industry Standards for Hose and Fitting Compatibility
In the hydraulic industry, standards play a vital role in ensuring the safety, performance, and reliability of hoses and fittings. Adhering to these standards helps maintain system integrity, provides consistency across different components, and minimizes the risks associated with mismatched parts.
Overview of Relevant Standards
1. ISO Standards
The International Organization for Standardization (ISO) sets globally recognized standards for hydraulic hoses and fittings. These standards specify performance criteria, such as pressure ratings, temperature resistance, dimensional tolerances, and compatibility with various fluids. Some key ISO standards include:
ISO 18752: Focuses on performance-based specifications for hydraulic hoses, categorizing them based on pressure ranges and temperature limits.
ISO 12151: Covers various types of hydraulic hose fittings, detailing their design, dimensions, and performance requirements.
2. SAE Standards
The Society of Automotive Engineers (SAE) provides another set of widely accepted standards for hydraulic components. These are commonly used in the North American market and ensure that hoses and fittings meet specific performance and compatibility criteria. Notable SAE standards include:
SAE J517: Provides guidelines for hydraulic hoses, detailing requirements for materials, pressure capacity, and dimensional tolerances.
SAE J516: Focuses on hydraulic hose fittings, specifying design, dimensions, and materials to ensure compatibility and durability.
3. Other Relevant Standards
DIN Standards (Deutsches Institut für Normung): Widely used in Europe, DIN standards cover both hydraulic hoses and fittings, providing detailed specifications for dimensions, pressure ratings, and materials.
BSI Standards (British Standards Institution): These standards also contribute to the global framework for ensuring the compatibility and safety of hydraulic components.
Role of Standards in Ensuring Safety
1. Consistency Across Components
Adhering to industry standards helps ensure that hydraulic components are consistent in terms of performance, dimensions, and pressure ratings. This consistency is vital for maintaining secure connections and preventing leaks. By following established standards, manufacturers can produce hoses and fittings that are more likely to work together seamlessly, even if sourced from different brands.
2. Minimizing Risks
Compliance with industry standards reduces the likelihood of mismatched components, which can lead to serious safety hazards. For example, using a fitting that does not meet the appropriate pressure standard can result in leaks, system failures, or catastrophic disconnections under high pressure. By ensuring that all components meet the same standards, operators can enhance the overall safety of hydraulic systems and reduce the risk of unexpected failures.
3. Improved Durability and Reliability
Standardized components tend to be more reliable and durable, as they are designed to withstand specific pressures, temperatures, and chemical exposures. This not only improves system performance but also extends the lifespan of hydraulic components, reducing the need for frequent replacements and minimizing downtime.
Certification Labels
1. Identifying Certified Components
Most certified hydraulic components come with visible labels or markings that indicate compliance with specific standards. For instance, a hose that meets ISO 18752 requirements will have a label displaying its pressure range, temperature capacity, and ISO classification. Similarly, fittings will be marked with their applicable standards (e.g., SAE J516), making it easier for users to identify compatible parts.
2. Verifying Compatibility
When selecting hydraulic hoses and fittings, look for these certification labels to ensure that the components meet the necessary standards for your application. Certified components are usually tested rigorously to ensure they can perform safely under specified conditions. This verification process adds an extra layer of confidence in the reliability and compatibility of the parts.
Risks of Mixing Different Brands in Hydraulic Systems
Mixing hoses and fittings from different manufacturers in hydraulic systems can introduce various risks that impact safety, legal standing, and operational efficiency. While combining different brands may seem convenient or cost-effective, the potential downsides often outweigh the benefits.
Safety Risks
1. Potential for Disconnection
One of the most serious risks when using mismatched components in hydraulic systems is disconnection. Hoses and fittings from different brands may have slightly different thread designs, sealing surfaces, or coupling mechanisms. These differences can compromise the integrity of the connection, leading to unexpected disconnections under pressure. In high-pressure hydraulic systems, a sudden disconnection can be catastrophic, causing fluid to be expelled at high velocity, which poses a significant risk to personnel and equipment.
2. Leaks and Fluid Spills
Hydraulic systems operate under high pressure, and even minor mismatches between hoses and fittings can lead to inadequate sealing. This results in leaks, which not only reduce system efficiency but also create safety hazards. Hydraulic fluid leaks can cause slippery surfaces, increasing the risk of falls and injuries. Additionally, certain hydraulic fluids are flammable or toxic, posing environmental risks and health hazards to workers. Over time, persistent leaks can lead to costly fluid loss and potential damage to other components within the system.
3. Pressure Failures and Equipment Damage
Mismatched components often have varying pressure ratings, leading to weak points in the hydraulic system. If a fitting with a lower pressure capacity is combined with a hose designed for higher pressure, the fitting can fail, resulting in sudden depressurization and potential equipment damage. This pressure imbalance not only reduces the system’s efficiency but also increases the likelihood of damage to pumps, valves, and other critical components. In extreme cases, a complete system failure can occur, resulting in significant repair costs and potential safety incidents.
Legal and Warranty Concerns
1. Void Warranties
Most manufacturers provide warranties for their hydraulic components under the condition that they are used as specified, which typically includes using matching parts from the same brand. When components from different brands are combined, there is a strong possibility of voiding the warranties. Manufacturers are unlikely to honor warranties for components that fail due to mismatched parts, as this goes against their specified usage guidelines. This means that any damage, repairs, or replacements resulting from the use of mismatched components will likely be at the user’s expense.
2. Potential Legal Liabilities
In cases where hydraulic system failure causes injury or property damage, legal liability can be a serious concern. If it is found that mismatched components contributed to the failure, the operator or owner of the equipment could be held liable for negligence. Moreover, insurance claims might be denied if it is determined that non-compliance with manufacturer guidelines—such as using mismatched components—was the primary cause of the incident. Therefore, it’s crucial to understand the legal implications of mixing components, especially in industries where safety standards are strictly regulated.
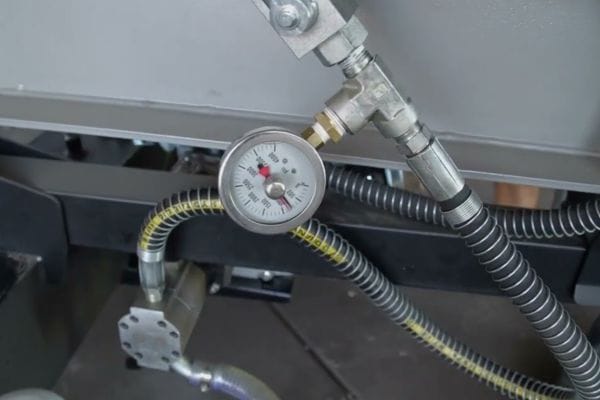
Operational Downtime
1. Increased Maintenance and Repairs
Hydraulic systems rely on consistent pressure and secure connections to function efficiently. Mismatched components are more prone to failure, leading to increased maintenance and repair needs. This not only raises operational costs but also contributes to unplanned downtime, which can have a significant impact on productivity. Every hour of downtime can be costly, especially in industries like construction, manufacturing, and logistics, where hydraulic systems are critical to daily operations.
2. Unplanned Downtime and Production Loss
The use of mismatched components increases the likelihood of sudden equipment failure. When a hydraulic system goes down unexpectedly, it can halt production lines, delay projects, and disrupt overall workflow. The cost of unplanned downtime extends beyond just repair expenses; it includes labor costs, lost productivity, and potential penalties for missed deadlines. In industries where precision and consistency are crucial, even a brief disruption can lead to significant financial losses.
3. Reduced Equipment Lifespan
Frequent pressure imbalances, leaks, and disconnections caused by mismatched components can accelerate wear and tear on the system. Over time, this results in a reduced lifespan for pumps, valves, seals, and other critical parts. As these components wear out faster, the overall reliability of the system diminishes, leading to more frequent breakdowns and higher replacement costs. The cumulative impact of using incompatible components can undermine the long-term viability of hydraulic equipment, making it less cost-effective and less efficient.
Best Practices for Ensuring Compatibility
When mixing hoses and fittings from different manufacturers becomes necessary, it’s vital to follow best practices to ensure system safety, performance, and reliability. While using components from the same brand is generally the safest approach, there are ways to minimize risks when combining different brands. This section outlines the key steps for ensuring compatibility, from consulting experts to testing and using adaptors effectively.
Consulting Manufacturers and Experts
1. Seek Professional Guidance
The first step in ensuring compatibility between hoses and fittings from different brands is to consult with manufacturers or industry experts. Manufacturers have a deep understanding of their product specifications, pressure ratings, and material properties. By sharing details about the hydraulic system—such as fluid type, pressure levels, and operational conditions—manufacturers can offer specific recommendations for compatible components. This expert guidance can prevent potential mismatches and help identify suitable alternatives.
2. Consult Hydraulic System Specialists
Hydraulic system specialists, including engineers and technicians, can provide valuable insights on component compatibility. They can assess the system requirements and recommend the best combination of hoses and fittings based on factors like pressure ratings, material compatibility, and performance needs. Experts can also offer solutions to address any specific challenges, such as chemical resistance or extreme temperature conditions, ensuring that the components work well together under various circumstances.
3. Review Product Specifications and Certifications
Before mixing components, review the technical specifications provided by each manufacturer. Look for information on pressure ratings, temperature limits, material composition, and certification labels to ensure compatibility. Verifying that the components meet the same industry standards (e.g., ISO, SAE) can help confirm that they are likely to perform well together in the same system.
Testing and Verification
1. Conduct Initial Compatibility Testing
Once components have been selected, the next step is to conduct compatibility testing in a controlled environment. This helps identify any potential issues, such as pressure drops, leaks, or improper sealing before the components are installed in the main hydraulic system. Begin by testing the combined components at low pressure to ensure that the seals and connections are secure, then gradually increase the pressure to the system’s operating levels.
2. Perform Stress Testing
In addition to initial compatibility tests, stress testing is crucial to verify that the mixed components can withstand the system’s maximum pressure and flow rates. Stress tests should simulate real-world conditions, including pressure surges, temperature fluctuations, and vibration exposure. Monitor the system for signs of leaks, pressure imbalances, or unusual noises, as these can indicate compatibility issues. Conducting stress tests can ensure that the mixed components will perform reliably under normal operating conditions.
3. Implement a Regular Maintenance Routine
After installing mixed components, establish a regular maintenance routine to monitor system performance. This includes checking for leaks, pressure consistency, and any signs of wear at the connection points. Early detection of issues can prevent serious failures and extend the lifespan of the hydraulic components.
Use of Adaptors and Connectors
1. When to Use Adaptors
Adaptors can be a useful solution for bridging compatibility gaps when combining hoses and fittings from different manufacturers. For example, if the threads or coupling types do not match, adaptors can help create a secure connection. Adaptors are also helpful when connecting components with different pressure ratings, as long as the overall system pressure remains within safe limits. However, adaptors should only be used when necessary, as they can introduce additional connection points that may be prone to leaks.
2. Choosing the Right Adaptors
When selecting adaptors, ensure that they are made from compatible materials and are designed to handle the same pressure and temperature ranges as the main components. Adaptors should also meet relevant industry standards, such as ISO or SAE, to ensure that they can perform reliably within the hydraulic system. Avoid using generic or unverified adaptors, as they may not provide the necessary performance or safety required for hydraulic applications.
3. Proper Installation of Adaptors
The effectiveness of adaptors depends largely on proper installation. Make sure to follow the manufacturer’s guidelines for tightening, sealing, and connecting adaptors to the hoses and fittings. Use the recommended tools and techniques to ensure a secure fit. Over-tightening can damage the threads, while under-tightening can result in leaks. Additionally, apply appropriate thread sealants to prevent leaks at the adaptor connections, especially in high-pressure systems.
Conclusion
Matching components from the same manufacturer remains the safest and most effective approach for hydraulic systems, as it ensures seamless integration and minimizes risks. However, if mixing brands is unavoidable, it’s crucial to consult with manufacturers or hydraulic experts to verify compatibility. Conducting thorough testing in a controlled environment, using appropriate adaptors, and implementing regular maintenance can help mitigate the risks.
FAQ
Can I safely mix different brands of hydraulic hoses and fittings?
Mixing brands can be risky due to differences in design, pressure ratings, and materials. Always consult experts and conduct thorough testing.
What are the main risks of using mismatched hydraulic components?
Potential risks include leaks, disconnections, pressure failures, and reduced system performance.
Will mixing components void the warranty?
Yes, using mismatched parts often voids the manufacturer’s warranty, making you liable for any damage or failures.
How can I ensure compatibility when mixing brands?
Consult manufacturers, review specifications, and test components together in a controlled environment.
Are adaptors safe to use for bridging compatibility gaps?
Yes, if used correctly and with compatible materials. Follow installation guidelines to prevent leaks.
Why is it important to follow industry standards like ISO or SAE?
Adhering to these standards ensures the safety, reliability, and consistent performance of hydraulic systems.