The selection of hydraulic components—such as hoses, valves, and pumps—plays a pivotal role in determining system performance. Choosing the right components not only enhances efficiency but also minimizes energy consumption, reduces wear and tear, and improves safety. This article will explore how the proper selection of these components is essential for boosting hydraulic system performance, maintaining system reliability, and ensuring operational safety.
Understanding Hydraulic Systems
Basic Components of a Hydraulic System
Hydraulic systems rely on several core components that work together to generate and transmit power. Each of these components has a unique role, making its selection critical for optimal system performance:
Hydraulic Pumps
Function: Pumps are the driving force of hydraulic systems, converting mechanical energy into hydraulic energy. This process involves drawing hydraulic fluid from a reservoir, pressurizing it, and delivering it into the system to generate the necessary force for tasks like lifting, pressing, or rotating machinery.
Types of Pumps:
Gear Pumps: Known for simplicity and reliability, ideal for low-pressure systems.
Vane Pumps: Offer moderate pressure, suitable for systems that require consistent flow.
Piston Pumps: Capable of handling high pressures, making them suitable for heavy-duty industrial applications.
Impact: The choice of pump affects system pressure, flow rate, and efficiency. An undersized pump can lead to inadequate pressure, while an oversized pump can waste energy and lead to system overheating.
Valves
Function: Valves control the direction, pressure, and flow rate of hydraulic fluid. They ensure that fluid reaches the correct component at the right time and pressure.
Types of Valves:
Directional Control Valves: Manage the flow path of fluid.
Pressure Control Valves: Regulate system pressure, preventing damage from excess pressure.
Flow Control Valves: Adjust the rate of fluid flow, affecting the speed of actuators.
Impact: Valves maintain fluid regulation and safety. Incorrect valve selection can lead to pressure surges, energy losses, and erratic system behavior.
Hoses
Function: Hoses act as flexible conduits that carry hydraulic fluid between components. Their flexibility allows them to adapt to the movement of machinery and changes in system configuration.
Types of Hoses:
Rubber Hoses: Commonly used due to flexibility and vibration absorption.
Thermoplastic Hoses: Offer durability in high-pressure or high-temperature environments.
Stainless Steel Hoses: Ideal for extreme pressure and corrosive environments.
Impact: Hoses must withstand the pressure, temperature, and type of hydraulic fluid used. Inappropriate hose selection can result in leaks, burst failures, or system inefficiencies due to frictional losses.
Fittings
Function: Fittings connect hoses to other components, such as pumps, valves, or actuators. They maintain a secure, leak-proof seal and enable efficient fluid flow across the system.
Types of Fittings:
Threaded Fittings: Commonly used for general hydraulic applications, offering strong sealing capabilities.
O-ring Face Seal (ORFS) Fittings: Ensure leak-proof connections, suitable for high-pressure applications.
Quick-Connect Fittings: Enable rapid attachment or detachment, ideal for systems that require frequent maintenance or changes.
Impact: Proper fitting selection is crucial for maintaining system pressure and preventing leaks. Poorly matched fittings can cause system inefficiencies, leaks, and potential safety hazards.
Actuators
Function: Actuators convert hydraulic energy into mechanical motion, which drives the machinery. They can perform either linear motion (via hydraulic cylinders) or rotational motion (via hydraulic motors).
Types of Actuators:
Hydraulic Cylinders: Provide linear movement for applications like lifting, pressing, or clamping.
Hydraulic Motors: Deliver rotational movement, used in applications like conveyor belts or vehicle drives.
Impact: Actuator selection affects the speed, force, and motion type in hydraulic systems. An undersized actuator can struggle to move loads, while an oversized one can result in slower response times and energy waste.
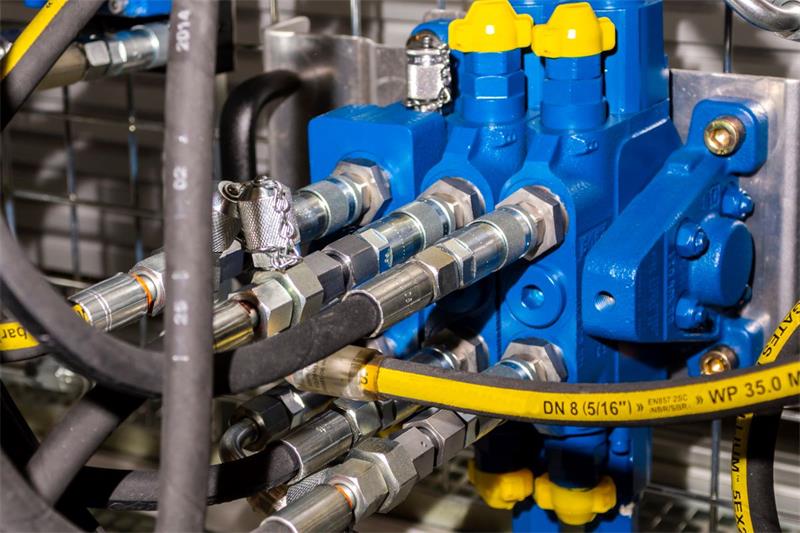
How Hydraulic Systems Work
Hydraulic systems operate based on Pascal’s Law, which asserts that pressure applied to a confined fluid is distributed equally throughout the system. This law forms the foundation of hydraulic power transmission. The working principles can be broken down into three main stages:
Fluid Flow
Pumping Process: The hydraulic pump pressurizes the fluid, drawing it from a reservoir and propelling it through hoses or pipes. The fluid’s movement is facilitated by valves that regulate the direction, ensuring it flows toward the desired component (e.g., actuators).
Flow Paths: The pressurized fluid travels through channels defined by hoses, fittings, and valves, moving toward the actuator. The flow rate is controlled by flow control valves, which influence the speed of the fluid and the actuator.
Pressure Build-Up
Load Adaptation: As the fluid enters the confined space of the system, pressure builds up based on the resistance presented by the load (e.g., weight lifted by a cylinder or the torque required for a motor).
Pressure Regulation: Pressure control valves manage the pressure within safe operating limits. These valves ensure that fluid pressure matches the required system load, preventing damage from pressure surges or sudden drops.
Energy Conversion
Mechanical Movement: The pressurized fluid reaches the actuator, where it converts hydraulic energy into mechanical force. For example:
Cylinders extend or retract to lift or press.
Motors rotate to drive machinery, such as conveyor belts or augers.
Continuous Cycle: The hydraulic fluid returns to the reservoir after passing through the actuator, completing the cycle and allowing for cooling and filtration before the next pressurization phase.
Importance of System Efficiency
Efficiency is defined as the ratio of useful output energy to total input energy. In hydraulic systems, efficiency affects cost, energy use, and overall performance:
Operational Costs
High-efficiency hydraulic systems require less energy to perform the same amount of work, which translates into reduced fuel or electricity costs. Additionally, efficient systems require less maintenance, lowering service costs.
Energy Usage
Efficient systems minimize energy loss through heat, friction, or pressure drops. By using the right components, operators can reduce energy consumption and environmental impact.
Performance
Efficient hydraulic systems deliver faster response times, consistent operation, and longer component life. Consistent system performance reduces downtime, enhances productivity, and increases the reliability of operations.
Key Factors Influencing Hydraulic System Performance
Component Selection
The choice of components plays a critical role in optimizing the overall performance of hydraulic systems. Each component must be chosen based on the system’s specific operational needs:
Pumps
Selecting the right pump (gear, vane, or piston type) directly affects flow rate, pressure, and energy efficiency. A mismatched pump can lead to inefficient energy conversion, resulting in slower response times, increased energy consumption, and system wear.
Hoses
Hoses must be selected for their pressure rating, flexibility, and compatibility with the hydraulic fluid. Improper hose selection can lead to leaks, pressure drops, or burst failures, compromising safety and performance.
Valves
Valves regulate flow, pressure, and direction. Choosing the right valve type (e.g., directional control, pressure relief, or flow control) ensures optimal fluid distribution, reducing energy loss and enhancing system responsiveness.
Fittings
Fittings connect hoses and components, playing a pivotal role in maintaining a leak-proof system. Proper fittings ensure minimal fluid leakage, efficient flow, and the ability to handle system pressures without failure.
The right component selection maximizes performance, minimizes downtime, and extends the service life of hydraulic systems.
System Design Considerations
Effective hydraulic system design should factor in:
Pressure Rating
All components should be rated for the maximum working pressure of the system, including a safety margin to account for pressure spikes. Using under-rated components can lead to safety hazards and premature failure.
Flow Rate
The flow rate affects the speed and responsiveness of actuators. Components must be designed to handle the required flow to avoid slow operation or inconsistent performance.
Temperature
High or fluctuating temperatures can affect hydraulic fluid properties and component integrity. Choosing components designed for the system’s temperature range helps maintain performance and prevent overheating or fluid degradation.
System Environment
Consider the environmental conditions, such as humidity, dust, or corrosive surroundings, when selecting components. For example, components with corrosion-resistant materials are crucial for outdoor or harsh environments to ensure longevity and performance.
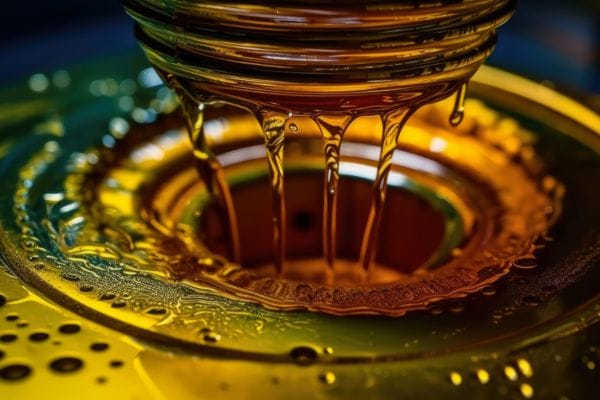
Fluid Quality
Fluid quality has a significant impact on hydraulic system performance:
Contamination
Contaminants like dirt, metal particles, or water can damage components, cause valve malfunction, and degrade fluid properties. Contaminated fluid increases friction and wear, reducing efficiency and risking total system failure.
Importance of Filtration
Effective filtration removes contaminants and ensures clean fluid circulation. Proper filtration systems (strainers, filters, and separators) maintain fluid quality, reducing wear and extending component life.
Maintaining fluid quality through regular filtration checks and timely filter replacement is essential for optimal performance.
Regular Maintenance
Routine maintenance is crucial for sustaining hydraulic system efficiency:
Timely Inspections
Regular inspections help identify issues such as leaks, wear, or pressure fluctuations early. Detecting and addressing problems early prevents unexpected downtime and maintains consistent system performance.
Leak Detection
Monitoring for leaks is vital, as fluid leaks reduce system pressure, leading to inefficient operation and potential safety risks. Inspect hoses, fittings, and seals regularly to prevent leakage.
Component Replacement
Proactive replacement of worn components (e.g., seals, hoses, filters) ensures consistent system operation. Worn or damaged components should be replaced promptly to prevent cascading failures or system inefficiencies.
Hydraulic Hose and Fitting Selection
Material Compatibility
The material of hydraulic hoses and fittings is a critical factor influencing system durability, performance, and fluid compatibility. Different materials offer distinct properties that make them suitable for specific applications:
Rubber Hoses
Properties: Flexible, cost-effective, and capable of absorbing vibrations, making them ideal for general-purpose hydraulic applications.
Compatibility: Rubber hoses are compatible with a wide range of hydraulic fluids, including petroleum-based, water-based, and synthetic fluids.
Durability: While rubber is highly flexible, it can degrade in high temperatures, chemical exposure, or harsh environments, limiting its lifespan in demanding applications.
Thermoplastic Hoses
Properties: Lightweight, durable, and more resistant to abrasions and chemicals than rubber hoses. They also have a smoother inner lining, reducing pressure loss and energy consumption.
Compatibility: Thermoplastic hoses are compatible with various hydraulic fluids, including synthetic oils and bio-based fluids.
Durability: Thermoplastic materials offer enhanced chemical resistance and are more suitable for high-pressure and high-temperature applications. However, they may be less flexible than rubber hoses.
Metal Hoses
Properties: Stainless steel hoses offer superior strength, pressure capacity, and resistance to extreme temperatures and corrosive environments.
Compatibility: They are ideal for use with highly corrosive fluids or in environments with extreme temperatures.
Durability: Metal hoses offer the longest lifespan among materials, but they lack flexibility, making them less suitable for applications requiring frequent movement.
The choice of material should align with the type of hydraulic fluid, environmental conditions, and the required flexibility. Incompatible materials can result in rapid wear, chemical reactions, or leakage.
Pressure Ratings and Safety Margins
Pressure rating is a key consideration in selecting hydraulic hoses and fittings, as improper pressure handling can lead to system failures and safety risks:
Working Pressure
Definition: The maximum pressure that a hose or fitting can withstand during normal operation.
Selection: Hoses and fittings should have a working pressure rating that meets or exceeds the system’s operating pressure. This ensures reliable performance and prevents premature wear or failure.
Burst Pressure
Definition: The maximum pressure a hose or fitting can withstand before it fails. It is usually 4 to 6 times the working pressure.
Selection: Selecting components with a burst pressure significantly higher than the operating pressure is crucial to account for unexpected pressure spikes, preventing catastrophic failures.
Safety Margins
Importance: To ensure safety and compliance, the working pressure of hoses and fittings should include a safety margin, typically 1.5 to 2 times the system’s maximum operating pressure. This margin accounts for pressure fluctuations and potential equipment stress.
By adhering to appropriate pressure ratings and safety margins, operators can prevent leaks, hose ruptures, and system breakdowns.
Temperature Considerations
Temperature variations, both internal and external, can significantly affect the performance and lifespan of hydraulic hoses and fittings:
Impact of High Temperatures
Internal Temperatures: The fluid temperature within the hose can rise due to heat generated by system operations. Prolonged exposure to high temperatures can degrade hose material, causing it to harden, crack, or lose flexibility.
External Temperatures: Hoses and fittings may also be exposed to external heat sources or extreme ambient temperatures. This exposure can weaken the hose material, leading to reduced pressure capacity and potential failure.
High-Temperature-Rated Components
Need: In high-temperature applications, it is essential to use hoses and fittings made from materials specifically designed to withstand elevated temperatures, such as heat-resistant rubber, thermoplastic composites, or stainless steel.
Benefits: High-temperature-rated components maintain flexibility, pressure integrity, and chemical compatibility, ensuring longer service life even under extreme conditions.
Proper consideration of temperature ensures the longevity and safety of hydraulic components, preventing heat-induced failures and maintaining consistent performance.
Sizing and Fit
Selecting the correct size for hoses and fittings is vital for maintaining hydraulic system efficiency and preventing potential issues:
Importance of Proper Sizing
Flow Rate Management: Hoses and fittings must be sized to accommodate the system’s required flow rate without causing excessive pressure loss. Undersized components can create flow restrictions, leading to increased energy consumption and reduced system performance.
System Integrity: Oversized hoses can add unnecessary weight, complicate routing, and increase costs. Proper sizing optimizes energy use, ensuring smooth fluid flow and maintaining system efficiency.
Preventing Leakage and Energy Loss
Sealing Capability: Properly sized fittings ensure a secure and leak-proof connection, reducing the risk of fluid leaks. Even minor leaks can reduce pressure, compromise system performance, and cause safety hazards.
Damage Prevention: Misaligned or incorrectly sized hoses can create additional stress at connection points, leading to wear, fatigue, and potential component failure.
Hydraulic Fluid Selection
Types of Hydraulic Fluids
The type of hydraulic fluid used in a system is fundamental to its performance, durability, and safety. Hydraulic fluids serve as the medium through which power is transmitted, and their specific properties influence system efficiency, component longevity, and operating conditions.
Mineral Oil-Based Fluids
Composition: These fluids are derived from refined crude oil and are the most commonly used type in hydraulic systems.
Properties: Mineral oils offer good lubrication properties, thermal stability, and a wide operating temperature range.
Applications: Widely used in industrial machinery, construction equipment, and agricultural systems due to their affordability and availability.
Limitations: Mineral oil-based fluids are less environmentally friendly and can be hazardous in the event of leaks. Additives may be required to improve anti-wear, anti-corrosion, and anti-foaming properties.
Synthetic Fluids
Composition: These fluids are made from chemically engineered base stocks such as phosphate esters, organophosphate esters, or polyalphaolefins.
Properties: They offer superior lubrication, fire resistance, and extreme temperature tolerance compared to mineral oil-based fluids. Synthetic fluids also resist oxidation, making them suitable for high-temperature environments.
Applications: Ideal for high-performance, heavy-duty applications like aviation, offshore drilling, and industrial manufacturing, where higher temperatures and pressures are common.
Limitations: Synthetic fluids are more expensive than mineral oils and can be incompatible with certain materials, requiring careful selection of system components.
Water-Based Fluids
Composition: These include water-glycol solutions and water-oil emulsions, designed to combine the properties of water and oil for safer applications.
Properties: Water-based fluids are highly fire-resistant and non-toxic, making them safer for use in hazardous environments.
Applications: Used in applications requiring fire resistance, such as steel mills, foundries, and mining operations. They are also suitable for low-pressure systems and environmentally sensitive areas.
Limitations: Water-based fluids have lower lubrication properties than mineral or synthetic fluids, leading to increased wear on components. They may also be prone to freezing and require corrosion inhibitors to protect the system.
The right choice of hydraulic fluid ensures effective power transmission, reduces wear and tear, and aligns with specific operational requirements.
Viscosity Impact
Viscosity refers to the thickness or resistance to the flow of a hydraulic fluid, and it has a major impact on system performance and efficiency:
High Viscosity Fluids
Characteristics: Thicker, slower-flowing fluids.
Effects on Performance: High-viscosity fluids maintain better lubrication and film strength, making them suitable for heavy-duty applications with high loads and low speeds.
Challenges: These fluids can cause increased resistance to flow, leading to higher energy consumption and slower response times. They can also require more power to move, reducing overall system efficiency, especially in colder conditions where the fluid becomes even thicker.
Low Viscosity Fluids
Characteristics: Thinner, faster-flowing fluids.
Effects on Performance: Low-viscosity fluids offer faster response times, better energy efficiency, and lower internal friction, making them ideal for high-speed, high-efficiency applications.
Challenges: Low-viscosity fluids may not provide adequate lubrication under high pressure or heavy load conditions, increasing wear and the risk of component damage. They can also lead to leaks in systems not designed to handle thinner fluids.
Optimal Viscosity Range
Importance: It is crucial to select a fluid with a viscosity within the manufacturer’s recommended range for the specific system. Fluids that are too thick or too thin can lead to suboptimal performance, increased wear, and potential system failure.
Temperature Considerations: Viscosity can change with temperature—fluids thicken at lower temperatures and thin at higher temperatures. Therefore, fluids with high viscosity indexes (VI) that maintain consistent viscosity across a broad temperature range are preferred for stable performance.
Proper viscosity selection ensures efficient power transmission, reduces energy loss, and prolongs component life.
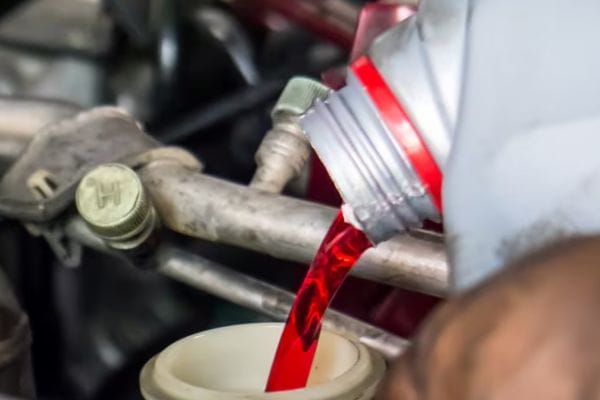
Fluid Compatibility with System Components
Fluid compatibility with system components is crucial for the longevity and safety of hydraulic systems:
Compatibility with Seals
Impact: Hydraulic seals prevent fluid leaks and contamination. Incompatible fluids can cause seals to swell, harden, or degrade, resulting in leakage and potential contamination of the hydraulic system.
Considerations: Ensure that the selected fluid matches the seal materials (e.g., nitrile, Viton, PTFE) to maintain seal integrity. For instance, mineral oil-based fluids are generally compatible with nitrile seals, while synthetic or water-based fluids may require more chemical-resistant seal materials.
Compatibility with Hoses
Impact: Hoses transport hydraulic fluid and must be resistant to the chemical composition of the fluid. Incompatible fluids can weaken the hose material, causing cracks, leaks, or complete failure.
Considerations: Select hoses made from materials that are chemically compatible with the hydraulic fluid. For example, thermoplastic hoses are often more compatible with synthetic fluids, while rubber hoses can work well with mineral oil-based fluids.
Compatibility with Fittings
Impact: Fittings connect hoses to other components and maintain a leak-proof seal. Fluids that are not compatible with fitting materials can lead to corrosion or wear.
Considerations: Fitting materials should resist chemical reactions with the hydraulic fluid. For instance, brass fittings work well with mineral oil-based fluids, while stainless steel fittings are better suited for aggressive synthetic fluids or corrosive environments.
Conclusion
Remember, hydraulic system performance is directly tied to thoughtful and informed component selection. Each decision—whether about fluid type, hose material, or fitting size—impacts the overall effectiveness and longevity of the system. By making informed choices and maintaining regular evaluations, you can ensure that your hydraulic systems operate reliably and efficiently in even the most demanding conditions.
FAQ
What are the main components of a hydraulic system?
The main components are pumps, valves, hoses, fittings, and actuators, each playing a specific role in fluid power transmission.
Why is it important to select the right hydraulic fluid?
The right hydraulic fluid ensures optimal performance, reduces wear, and is compatible with the system’s seals, hoses, and fittings, preventing leaks and damage.
How does hose material affect hydraulic system performance?
Different materials offer varying levels of flexibility, pressure resistance, and compatibility with fluids, impacting durability, efficiency, and safety.
What is the significance of pressure ratings in hydraulic hoses?
Proper pressure ratings ensure that hoses can handle system pressure without bursting, enhancing safety and reliability.
How does temperature impact hydraulic components?
High temperatures can degrade hoses, fluids, and seals, while low temperatures can thicken fluids, reducing system responsiveness.
How often should I perform maintenance on my hydraulic system?
Regular inspections should be performed at least quarterly, with routine maintenance (e.g., fluid checks, hose inspection, and seal replacements) conducted based on usage intensity.