When air mixes with hydraulic fluid, it creates a condition known as aeration, which can result in a decrease in fluid pressure, reduced efficiency, and erratic behavior of hydraulic components. Common symptoms of air contamination include noisy operation, sluggish actuator movements, and increased wear on system parts. If left unaddressed, these issues can lead to significant downtime, costly repairs, and even catastrophic failures.
Understanding Air in Hydraulic Systems
What is Air Entrapment?
Air entrapment in hydraulic systems refers to the unwanted presence of air bubbles within the hydraulic fluid. This condition can occur when air infiltrates the system, disrupting the continuous flow of fluid and leading to various operational inefficiencies. Essentially, the air in the hydraulic lines creates a compressible medium that interferes with the system’s ability to generate consistent pressure. This can manifest as air pockets that impede fluid movement, leading to inconsistent operation and reduced system performance.
Common sources of air in hydraulic systems include leaks in hoses, fittings, or seals, where air can be drawn into the fluid. Additionally, improper filling procedures, such as introducing fluid too quickly or at an angle, can introduce air into the system. Rapid fluid movement, especially in high-speed applications, can also create turbulence, allowing air to mix with the fluid. Furthermore, temperature changes can affect fluid viscosity and pressure, potentially causing cavitation that contributes to air entrainment. Recognizing these sources is vital for maintenance personnel to prevent air contamination from occurring.
Effects of Air on Hydraulic Performance
The presence of air in hydraulic systems can significantly decrease efficiency. When air is trapped within the fluid, it results in less effective force transmission. This is particularly evident in systems that rely on precise movements, such as hydraulic lifts or robotic arms. Operators may notice sluggish response times or erratic behavior in actuators, leading to delays in operations and impacting overall productivity.
Moreover, air contamination can lead to potential damage to hydraulic components. The compressibility of air causes fluctuations in pressure that can strain pumps, valves, and cylinders. Over time, this can result in accelerated wear and tear on these components, leading to premature failures. Additionally, the presence of air increases the likelihood of cavitation—an effect where vapor bubbles collapse, creating shockwaves that can erode metal surfaces and damage seals. This not only compromises the integrity of the hydraulic system but also results in costly repairs and downtime.
Safety is another critical concern when air is present in hydraulic systems. Erratic system behavior due to air can pose serious risks to operators and surrounding personnel. For instance, unexpected movements of machinery can lead to accidents, injuries, or damage to equipment. Furthermore, if air leads to a complete loss of pressure in critical systems, it could result in catastrophic failures that endanger lives and assets. Therefore, maintaining air-free hydraulic fluid is essential not only for performance but also for ensuring a safe working environment.
Identifying Air in Your Hydraulic System
Signs of Air Presence
Detecting air in a hydraulic system is crucial for maintaining optimal performance and preventing damage. Several signs can indicate the presence of air, allowing operators to take timely action.
Unusual Noises: One of the most common indicators of air contamination is the presence of unusual noises within the hydraulic system. Operators may hear whining, gurgling, or bubbling sounds during operation. These noises result from air bubbles collapsing or moving through the hydraulic fluid, disrupting the flow and causing turbulence. A continuous or pronounced noise often suggests significant air entrainment that requires immediate attention.
Erratic Movements of Actuators: Air in the hydraulic lines can cause actuators—such as cylinders and motors—to operate unpredictably. This can manifest as jerky or inconsistent movements, where the actuator fails to respond smoothly to control inputs. For instance, a hydraulic lift may rise or lower unevenly, or a robotic arm may struggle to maintain precision. These erratic behaviors not only affect productivity but can also pose safety risks if equipment malfunctions during operation.
Increased Pressure Fluctuations: Pressure fluctuations are another telltale sign of air in hydraulic systems. When air is present, the hydraulic fluid’s ability to maintain steady pressure is compromised, leading to erratic pressure readings. Operators may notice spikes or drops in pressure on gauges, indicating that the system is struggling to perform as intended. This instability can further exacerbate wear on system components and lead to operational failures.
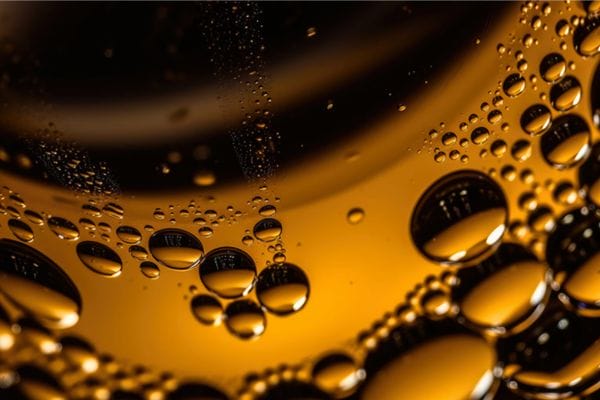
Diagnosing Air Issues
Once signs of air presence are identified, it’s essential to diagnose the issue accurately to implement appropriate solutions.
Visual Inspections: A thorough visual inspection is the first step in diagnosing air issues within a hydraulic system. Operators should check for obvious leaks in hoses, fittings, and seals, as these can be entry points for air. Additionally, examining the fluid reservoir for proper fluid levels and clarity is crucial. If the fluid appears foamy or has a milky consistency, it may indicate the presence of air or contamination. Regular inspections can help detect potential problems before they escalate.
Using Pressure Gauges and Sensors: Pressure gauges and sensors play a vital role in diagnosing air issues. Monitoring pressure readings during operation can help identify irregularities associated with air entrainment. Operators should compare the current pressure readings with the system’s expected operating range. If fluctuations are detected, it may indicate air presence. Installing pressure sensors that provide real-time data can enhance monitoring capabilities and facilitate quicker responses to air-related issues.
Fluid Analysis: Conducting fluid analysis is an advanced method for diagnosing air issues in hydraulic systems. This process involves collecting fluid samples and analyzing them for signs of air entrainment, moisture, or contamination. Laboratory tests can provide insights into the fluid’s condition and reveal the extent of air contamination. By understanding the fluid’s properties, operators can make informed decisions about necessary maintenance and repairs.
Step-by-Step Process to Exhaust Air
System Shut Down and Isolation
Before attempting to exhaust air from a hydraulic system, it is crucial to follow proper shutdown procedures to ensure safety and prevent equipment damage. Begin by turning off the power to the hydraulic system and disconnecting any energy sources. This includes ensuring that all operators are aware of the shutdown and are positioned safely away from moving components. Once the system is powered down, the next step is to isolate it from any external pressure sources. This involves closing isolation valves and ensuring that the hydraulic fluid is contained within the system. Proper isolation helps prevent accidental activation and ensures that the bleeding process can be performed safely and effectively.
After isolating the system, visually inspect it for leaks or signs of damage. Address any issues before proceeding, as leaks can introduce air back into the system during the bleeding process. By taking these precautionary steps, operators can ensure a safer working environment and set the stage for successful air removal.
Opening Bleed Valves
Once the system is shut down and isolated, the next step is to open the bleed valves. Bleed valves are critical components designed specifically for releasing trapped air from hydraulic systems. The location of these valves can vary depending on the system design, but they are commonly found near pumps, actuators, and hydraulic reservoirs.
To identify bleed valves, refer to the system’s manual or schematics for specific locations. Generally, these valves are small, typically equipped with a screw or knob for adjustment. When opening the valves, use the appropriate tools to avoid damaging the components. Loosen the valve slowly to allow air to escape gradually. It’s important to monitor the fluid escaping from the valve; it should be free of air bubbles before closing it. If air bubbles are still present, continue to bleed until the fluid runs clear.
After releasing air, close the bleed valve securely to prevent fluid leaks. Repeat this process for all bleed valves throughout the hydraulic system to ensure thorough air removal. Following this technique not only helps maintain system integrity but also enhances operational efficiency.
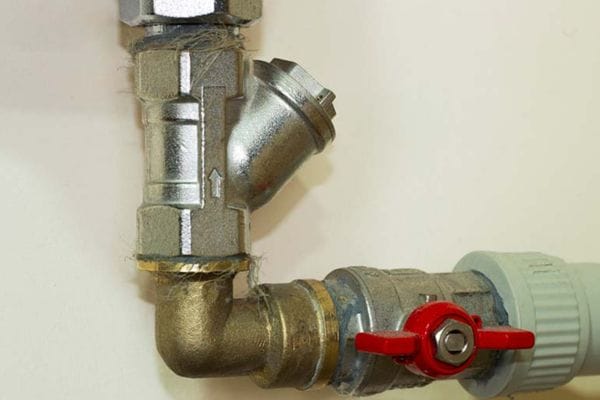
Using a Vacuum Pump
Using a vacuum pump is another effective method for exhausting air from hydraulic systems. This technique involves creating a vacuum environment that helps draw air out of the fluid. Begin by ensuring that the vacuum pump is compatible with your hydraulic system and fluid type. Set up the vacuum pump according to the manufacturer’s instructions, typically involving connecting it to the fluid reservoir or specific bleed points in the system.
Once set up, activate the vacuum pump. As the pump operates, it reduces pressure within the system, encouraging air to escape from the hydraulic fluid. Monitor the vacuum gauge to ensure that adequate vacuum pressure is maintained throughout the process. The duration of operation will depend on the amount of air present; continue until the gauge indicates that air has been sufficiently removed.
One of the advantages of using a vacuum pump is its efficiency in removing air without requiring extensive manual effort. This method can be particularly beneficial for larger or more complex hydraulic systems where manual bleeding may be cumbersome. Additionally, it minimizes the risk of introducing contaminants during the process, making it a preferred choice for many operators.
Manual Bleeding Techniques
Manual bleeding techniques remain a reliable approach for exhausting air, especially in smaller hydraulic systems or when vacuum pumps are not available. This method typically involves a pumping action to expel trapped air from the system. Begin by ensuring that the hydraulic fluid reservoir is filled to the recommended level to prevent running dry during the process.
To manually bleed the system, locate the bleed valves as described earlier. With the valves open, operators should actuate the hydraulic components—such as cylinders or pumps—by engaging the system controls. This action allows the hydraulic fluid to flow and pushes air toward the bleed valves. During this process, it is essential to monitor the fluid levels continuously, as air removal can cause the fluid level to drop rapidly.
As air is expelled, operators will notice a change in the consistency of the fluid exiting the bleed valves; it should become free of bubbles and flow smoothly. Once all visible air is expelled, close the bleed valves securely. After completing this process, test the system by cycling through its operational range to ensure that any remaining air has been adequately removed.
Post-Bleeding Checks
Monitoring System Performance
After completing the air bleeding process, it is crucial to monitor the hydraulic system’s performance to ensure that all air has been successfully removed and that the system is operating as intended.
Checking for Air Bubbles in Fluid: One of the first steps post-bleeding is to visually inspect the hydraulic fluid for any remaining air bubbles. This can be done by observing the fluid in the reservoir or through transparent hoses. If air bubbles are still present, it may indicate that the bleeding process was not entirely effective, and further bleeding may be necessary. Keeping an eye on fluid clarity not only helps detect residual air but also serves as an indicator of fluid quality, ensuring that the hydraulic fluid remains free from contaminants.
Observing System Responsiveness: Next, operators should assess the overall responsiveness of the hydraulic system. This includes monitoring the speed and accuracy of actuator movements and ensuring that the system reacts promptly to input commands. Any sluggishness or delay can signify remaining air in the system or other issues that require further investigation. Conducting operational tests under typical load conditions will provide valuable insights into whether the system is functioning optimally.
Regular Maintenance Tips
To maintain optimal performance and prevent future air issues, implementing a routine maintenance schedule is essential.
Scheduled Bleeding Intervals: Establishing scheduled bleeding intervals based on system usage and environmental conditions can help preemptively address air entrapment. For high-use systems or those operating in challenging environments, more frequent bleeding may be necessary. Conversely, systems with less frequent use might require less regular attention. Documenting these intervals in a maintenance log ensures that bleeding becomes a standard operating procedure, promoting consistent system performance.
Importance of Routine Inspections: Beyond bleeding, conducting routine inspections of the hydraulic system is vital for identifying potential issues before they escalate. Regularly check hoses, fittings, and seals for wear and tear, and monitor fluid levels and quality. Implementing a checklist for these inspections can help ensure that no aspect is overlooked. By being proactive in maintenance, operators can catch leaks or signs of air intrusion early, significantly reducing the risk of system failures.
Conclusion
In addition to the immediate benefits of air removal, maintaining the integrity of hydraulic systems requires ongoing attention. Regular maintenance schedules, fluid analysis, and system audits should be integral parts of any hydraulic management plan. This proactive approach ensures that potential issues are identified and addressed before they escalate into more significant problems, ultimately extending the lifespan of hydraulic equipment and optimizing performance.
FAQ
What causes air to enter a hydraulic system?
Air can enter through leaks in hoses, fittings, or seals, improper filling procedures, or turbulence caused by rapid fluid movement.
How can I tell if my hydraulic system has air in it?
Signs include unusual noises (like whining or gurgling), erratic actuator movements, and increased pressure fluctuations.
What tools do I need to bleed air from a hydraulic system?
Common tools include wrenches, vacuum pumps, and pressure gauges.
How often should I bleed air from my hydraulic system?
This depends on usage; high-use systems may require more frequent bleeding, while others can be checked periodically.
What safety precautions should I take during maintenance?
Always wear appropriate personal protective equipment (PPE) and follow lockout/tagout procedures to ensure safety.
What should I do if air persists after bleeding?
If air issues continue, consider conducting further inspections for leaks or consulting a professional for a thorough assessment.