You’re in the field, fighting to connect a hydraulic implement to your tractor. The fittings are stubborn, covered in grime, and refuse to latch, bringing your entire operation to a frustrating standstill.
For a reliable and efficient farm, you need a strategic selection of couplers. The core must-haves are the ISO 7241-A poppet for universal compatibility, the modern ISO 16028 flat-face for cleanliness, a connect-under-pressure type for problem-solving, and high-flow models for performance.
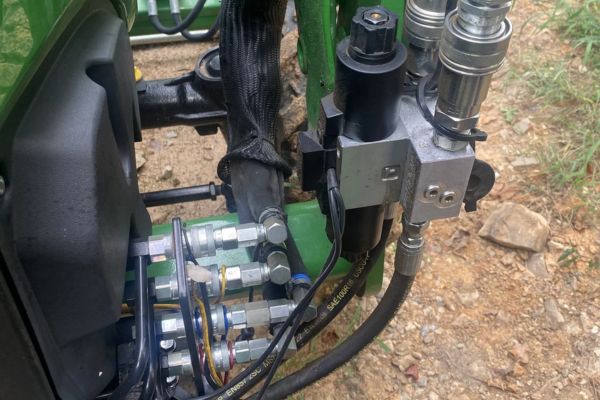
Is the ISO 7241-A Poppet Your Most Essential Ag Coupler?
You need a dependable coupler that connects to nearly any tractor or implement, regardless of brand. Using a non-standard fitting isolates your equipment, making it impossible to borrow or rent machinery in a pinch.
The ISO 7241-A poppet valve coupler is the bedrock of agricultural hydraulics. Its globally recognized standard ensures wide interchangeability, while its robust, cost-effective design makes it the foundational coupler for any farm operation.
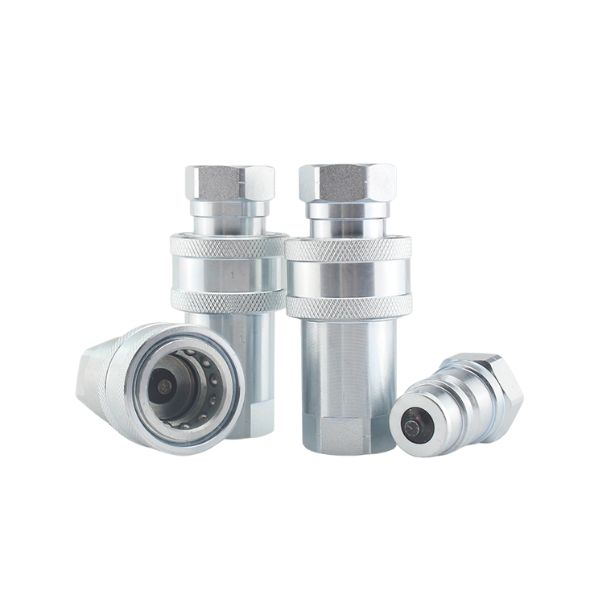
This coupler is, without question, the universal workhorse of the farm. Its design is simple, proven over decades, and built to withstand the demanding conditions of fieldwork. The true key to its dominance is the power of the ISO 7241-A standard. This specification dictates the precise dimensions of the male nipple and female coupler, meaning a fitting from one compliant manufacturer will connect perfectly with another. This interchangeability is the lifeblood of cooperative farming and equipment rental, allowing machinery from different brands and eras to work together seamlessly. As a manufacturer, we produce millions of these couplers, and their simple reliability makes them the first and most important type to stock in any farm workshop.
Mechanism, Role, and Limitations
The ISO 7241-A coupler works using a simple poppet valve. Inside both the male nipple and the female coupler, a spring holds a conical valve, or “poppet,” firmly against its seat, sealing the hydraulic line when disconnected. To connect, the operator manually retracts a sleeve on the female coupler and inserts the male nipple. This action mechanically pushes both poppets off their seats, opening a path for fluid to flow. This robust mechanism is ideal for agriculture due to its durability against physical abuse and its relative tolerance for minor contamination. However, this design has inherent limitations. The small chamber created between the two poppets before they fully open traps fluid, which results in spillage upon disconnection. This same cavity introduces a bubble of air into the system upon connection. While acceptable for basic cylinder functions, this can cause “spongy” hydraulics in more sensitive applications. The open cavity of the disconnected nipple is also a notorious trap for dirt and dust.
Feature | Specification / Description | Agricultural Significance |
Standard | ISO 7241-A | Guarantees interchangeability between different brands of tractors and implements. |
Valve Type | Poppet (conical valve) | Simple, robust, and cost-effective design suitable for rough use. |
Material | Hardened Carbon Steel | Provides excellent durability against physical impact and high pressure. |
Weakness | Spillage & Air Inclusion | Creates minor messes and can affect sensitive hydraulic motor performance. |
Contamination Risk | High | The open cavity in the male nipple easily traps field dust and debris. |
Why Should You Upgrade to Flat-Face Couplers?
Spilled hydraulic oil creates a slippery hazard, contaminates your soil, and cakes your machine in a layer of grime. This dirt inevitably enters the hydraulic system, posing a silent but deadly threat to expensive pumps.
Flat-face couplers, built to the ISO 16028 standard, are designed for near-zero spillage. Their perfectly flush, easy-to-clean mating surfaces are the ultimate defense against fluid loss and catastrophic system contamination on a modern farm.
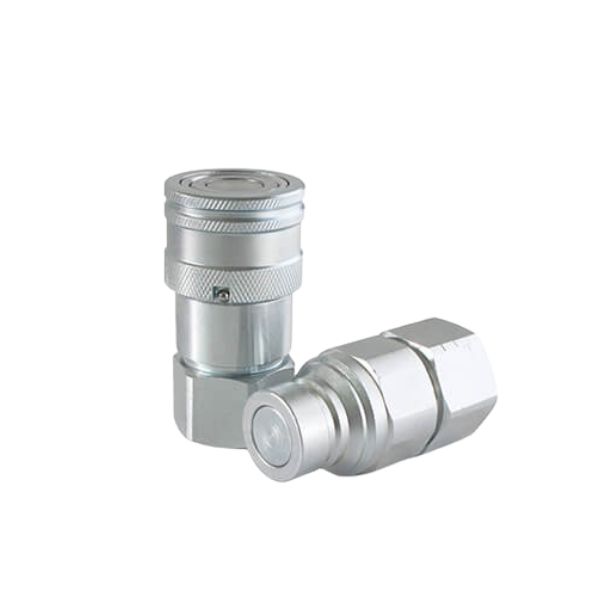
The shift from poppet to flat-face technology is one of the most significant advancements in practical farm hydraulics. We strongly recommend this upgrade to clients operating modern, electronically controlled machinery. The primary motivation is preventing contamination. A single grain of abrasive dust introduced by a dirty poppet coupler can scar the internals of a multi-thousand-dollar hydraulic pump or valve stack. The poppet’s recessed cavity is almost impossible to clean perfectly in a dusty field. In stark contrast, the flush surface of a flat-face coupler can be wiped completely clean with a single swipe of a rag. This simple design change virtually eliminates the primary source of introduced contamination, dramatically extending the life of your entire hydraulic system.
The “Seal Before Flow” Advantage
The brilliance of the flat-face coupler lies in its valve sequence. When you connect the two halves, the flat external faces make contact first, creating a secure seal around the circumference. Only after this initial seal is established do internal pins engage and retract both valves, opening the path for fluid flow. This “seal before flow” design provides several monumental benefits for agriculture. First, spillage is reduced to a mere film of oil, often less than 0.02 mL. This keeps machines clean, protects the environment, and saves money on hydraulic fluid. Second, and most importantly, it prevents contamination. Since the connection is sealed before the system is opened, there is no pathway for dirt to be injected. Third, most ISO 16028 couplers include a locking sleeve. This safety feature prevents accidental disconnection of a line under high pressure—a critical safeguard. Finally, their internal design often provides a higher flow rate with less pressure drop than a poppet of the same size, improving the efficiency of high-demand implements.
How Do You Beat Trapped Pressure When Connecting Implements?
An implement has been sitting in the hot sun all day. The hydraulic fluid inside its hoses has expanded, creating immense trapped pressure that makes connecting it to your tractor physically impossible.
Connect-under-pressure couplers are engineered with a small, internal relief valve. This allows you to effortlessly connect hydraulic lines against high static pressure, solving one of farming’s most common and frustrating hydraulic problems.
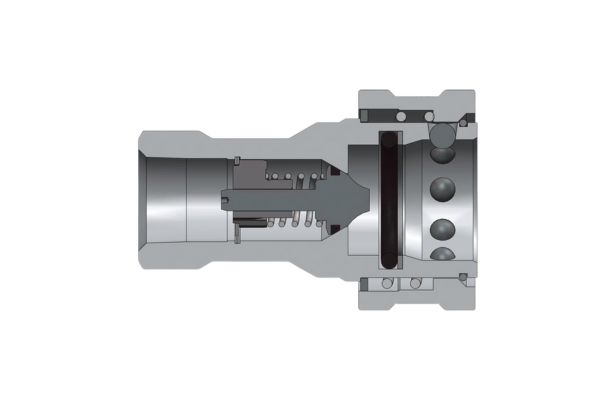
This scenario is all too familiar to anyone who works with farm machinery. Black hydraulic hoses are incredibly effective at absorbing solar energy, and the subsequent thermal expansion of the trapped fluid can spike internal pressure to 3,000 PSI or more. At this level, you cannot overcome the force needed to unseat the main poppet valve. The old-school, dangerous solution was to “crack a fitting” with a wrench, spilling oil and risking a high-pressure injection injury. Connect-under-pressure technology completely eliminates this problem. It is a feature we now recommend as a standard fitment for any implement that is frequently disconnected and left outside, as it transforms a frustrating, time-consuming task into a simple, safe connection.
Science and Solution
These innovative couplers, which can be based on either poppet or flat-face designs, contain a crucial internal modification. The male nipple typically incorporates a secondary, smaller valve pin. When you begin to push the two halves together, this small pin makes contact first and opens a tiny relief passage. This allows the high-pressure trapped fluid in the implement hose to safely bleed back into the lower-pressure tractor circuit. As the pressure rapidly equalizes, the resistance disappears, allowing you to complete the connection and open the main valves with minimal physical effort. This simple yet ingenious solution provides a massive return on investment by saving time, preventing wasted hydraulic fluid, and, most importantly, eliminating an unsafe work practice. For an even more robust solution on heavy-duty implements, some screw-to-connect style couplers can also provide this capability through pure mechanical advantage.
What Are High-Flow Couplers and When Do You Need Them?
Your air seeder fan seems underpowered, or your hydraulic mower motor bogs down under load. Your tractor has enough power, but the implement is being starved of the hydraulic flow it needs to perform.
High-flow quick couplers are designed with larger bodies and streamlined internal valves to minimize flow restriction and pressure drop. They are essential for any implement with a hydraulic motor to ensure it operates at peak power and efficiency.
Think of a standard hydraulic coupler as a single-lane road. For a basic cylinder, that is fine. But for a high-demand hydraulic motor, you need a multi-lane highway. Using a standard coupler on a high-flow circuit is a primary cause of poor implement performance. The restriction creates a significant pressure drop, meaning the pressure at the motor is much lower than the pressure at the tractor. This starves the motor of power, reduces its speed, and generates a massive amount of waste heat, which degrades your hydraulic oil. We advise clients that any implement relying on a continuous-flow hydraulic motor—such as the fans on air seeders and vacuum planters, large mower decks, or hydraulic conveyors—requires a dedicated high-flow circuit with properly sized couplers.
Understanding Pressure Drop’s Impact
Pressure drop is the enemy of hydraulic efficiency. Every fitting, hose, and valve in a circuit creates some restriction to flow. High-flow couplers, typically in 3/4″ or 1″ body sizes, are engineered specifically to minimize this. They feature larger internal pathways and more aerodynamically designed valves that allow a greater volume of oil to pass through with less turbulence and energy loss. Upgrading from a standard 1/2″ coupler to a 3/4″ high-flow model can dramatically reduce pressure drop, delivering more hydraulic horsepower to the implement. This means an air seeder fan spins up to the correct RPM, a hydraulic motor maintains its torque under load, and the entire system runs cooler and more efficiently. It’s not about the tractor’s power; it’s about delivering that power effectively.
Coupler Size | Typical Flow Rate | Performance Class | Ideal Implement Use |
1/2″ Standard | 12 GPM (45 LPM) | Standard Duty | Basic cylinders (lift, tilt, steer), small motors. |
3/4″ High-Flow | 25 GPM (95 LPM) | High Performance | Air seeder fans, hydraulic mowers, vacuum motors. |
1″ High-Flow | 45 GPM (170 LPM) | Extreme Duty | Very large planters, commercial mowers, high-demand circuits. |
Are Multi-Coupler Plates Worth It for Your Farm?
You’re trying to attach a front-end loader or a complex harvester head. Fumbling with four, six, or even more hydraulic hoses (plus electrical lines) is a slow, messy process where crossing lines is a constant risk.
Multi-coupler plates consolidate numerous hydraulic and electrical lines into a single, lever-actuated block. They provide an instant, error-proof method for connecting complex attachments, drastically reducing changeover time and eliminating connection errors.
For certain applications, the multi-coupler is a transformative technology. While the initial investment is higher, the return in time savings and convenience is immense for any implement that is connected and disconnected frequently. A front-end loader is the classic example. A task that involves wrestling with multiple individual couplers, often in an awkward position, becomes a simple, clean, ten-second process of aligning the block and pushing a single lever. This is a premium solution we supply for high-end loader applications and specialized harvesting equipment where speed and reliability are paramount. The system not only saves time but also enforces correct connection every time.
Speed, Safety, and Error-Proofing
The principle behind a multi-coupler is simple: it uses a guide-pin system to perfectly align an entire bank of individual couplers (often flat-face for cleanliness). A large cam-action lever then provides the powerful mechanical advantage needed to push all the couplers together simultaneously and lock them securely in place. The benefits extend far beyond pure speed. Firstly, it is completely error-proof. It is physically impossible to cross-connect hydraulic lines, which could cause an implement to operate backwards or dangerously malfunction. Secondly, it improves cleanliness and safety. The plates often have integrated covers that protect all the coupling faces when disconnected, and the operator spends far less time in the potentially hazardous “crush zone” between the tractor and the implement. While not necessary for a simple drawbar implement, for loaders, grapples, and complex headers that are swapped daily, the efficiency gains make a multi-coupler plate a very wise investment.
How Do You Ensure Total System Reliability and Safety?
You’ve invested in the correct couplers, but they are still failing prematurely. A brand new fitting is already stiff to operate or weeping oil because it has been compromised by grit and poor handling.
True reliability goes beyond the coupler itself. Religious use of **dust caps**, having a small kit of **problem-solver adapters**, and performing regular visual inspections are the final, critical steps to ensure a robust and leak-free hydraulic system.
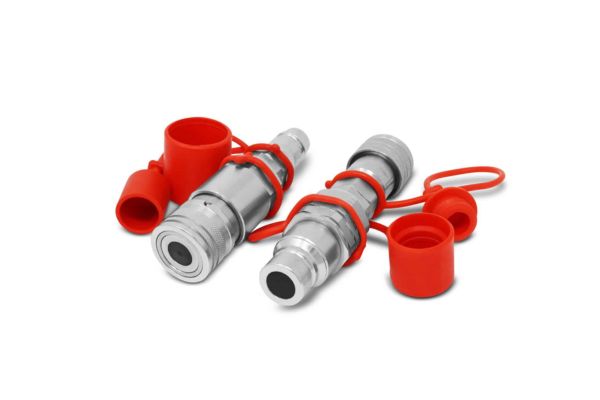
This is a point I cannot stress enough with our customers. The most advanced coupler in the world will fail if it is not protected. Dirt is the number one enemy of any hydraulic system. Couplers live in one of the dirtiest environments on the farm—right in the path of dust, chaff, and mud thrown up by the tires. Treating your couplers with the same care as the rest of your hydraulic system is essential. This means using protective caps and plugs without fail, being prepared for the occasional oddball fitting from an older piece of equipment, and taking thirty seconds to inspect a connection before you make it. This discipline is what separates a system that performs flawlessly for years from one that suffers from chronic leaks and failures.
A Three-Pillar Approach to Reliability
To guarantee long-term performance, focus on these three pillars:
- Protection with Dust Caps: This is non-negotiable. A plastic dust cap costs pennies but protects a precision-machined steel component worth many dollars. It is the single most effective action you can take. The male plug keeps debris out of the nipple, while the female cap keeps the coupler’s sleeve and locking mechanism clean and functioning smoothly.
- Preparedness with Adapters: Every farm eventually acquires an older or non-standard piece of equipment. Having a small “problem-solver” kit with adapters to convert between different thread types (e.g., NPT to BSPP), or even different coupler standards (e.g., an older John Deere poppet nipple to an ISO-A coupler), can save a day of downtime.
- Prevention through Inspection: Before every connection, wipe both halves clean and take a quick look. Is a seal protruding? Is the locking sleeve full of grit? Does the male nipple look scored or damaged? Catching these small issues early prevents larger, more expensive failures and ensures a secure, leak-free connection every time.
Conclusion
Strategically equipping your machinery with the right mix of compatible, clean, and high-performance couplers is a direct investment in your farm’s productivity, reliability, and long-term health. Topa can customize the best hydraulic quick connect for your needs, contact us now for fast shipping!