A persistent fluid leak from a threaded connection can indicate a fundamental mismatch between the fitting type and the application. This can lead to system inefficiency, costly downtime, and significant safety hazards.
The key difference lies in the sealing mechanism. NPT fittings create a seal on the threads themselves using a taper and sealant. In contrast, bite-type fittings create a mechanical seal by forcing a hardened ferrule to cut into the outer surface of a tube, independent of the threads.
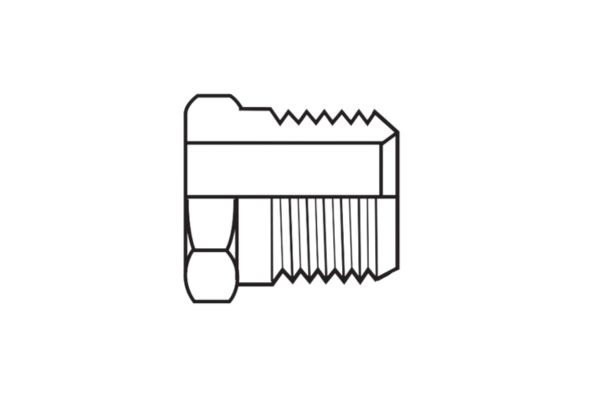
How Does an NPT Fitting Create a Seal?
A pipe joint is weeping fluid, despite having been tightened securely. This creates a mess on the factory floor, wastes valuable fluid, and poses a continuous slip hazard for personnel.
An NPT (National Pipe Taper) fitting seals by forcibly wedging its tapered male threads into matching tapered female threads. This interference fit creates an imperfect metal-to-metal seal that requires a thread sealant to fill the helical leak path.
The NPT thread form is one of the oldest and most widely recognized standards in North America, particularly in plumbing and general industrial piping. Its design principle is straightforward: as the male and female fittings are threaded together, the tapered profile causes them to bind, creating friction and a seal. The threads themselves are intended to deform slightly to conform to one another. However, due to standard manufacturing tolerances, a perfect seal is impossible. A continuous spiral gap always exists at the root and crest of the threads. Therefore, the use of a thread sealant—either PTFE tape or a liquid/paste compound—is not optional; it is a mandatory component of the sealing system. The sealant’s job is to fill this microscopic void and prevent fluid from escaping.
The Mechanics and Limitations of a Tapered Thread Seal
The standard NPT thread has a 1.79° taper relative to the fitting’s centerline. When torque is applied, the flanks of the male and female threads are compressed against each other. This high compressive force is what creates the primary seal, but it also introduces significant stress into the material. The reliance on this wedging action is the source of NPT’s primary weaknesses in demanding applications.
Key Issues with the NPT Sealing Method:
- Galling: The high friction and pressure between the threads, especially with stainless steel, can cause them to seize and gall, destroying the threads upon disassembly.
- Over-Tightening: An installer can easily crack the female port by applying too much torque, as the wedging action creates immense radial force. Under-tightening results in an immediate leak.
- Sealant Dependency: The seal’s integrity is entirely dependent on the correct application of sealant. Too much or too little tape, or applying it in the wrong direction, will result in a leak. Sealants can also be incompatible with certain fluids or degrade over time.
- Positional Orientation: It is difficult to orient shaped fittings like elbows or tees correctly without compromising the seal by backing them off after tightening.
Attribute | Description | Implication for Reliability |
Sealing Principle | Thread deformation and sealant | Prone to leaks from vibration, thermal cycling, and improper installation. |
Torque Sensitivity | High | High risk of port cracking (over-torqued) or leaking (under-torqued). |
Reusability | Poor | Threads deform with each use. Sealant must be reapplied. |
Material Stress | High | Concentrates stress in the port, making it weak against pressure spikes. |
What is the Sealing Mechanism of a Bite-Type Fitting?
A hydraulic system is experiencing leaks at the tube connections, particularly after maintenance or in areas with heavy machine vibration. Standard fittings are failing to provide a dependable, long-term seal.
A bite-type fitting creates a robust mechanical seal using three components: a body, a ferrule, and a nut. As the nut is tightened, it forces the hardened ferrule to progressively “bite” into the tube’s outer wall, creating a positive lock.
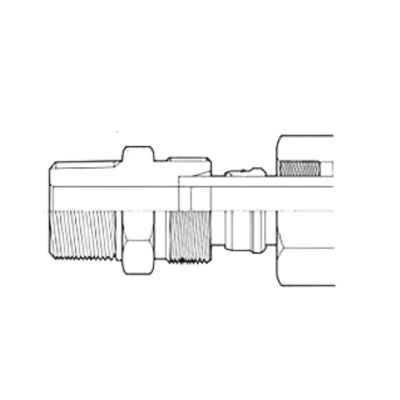
The bite-type fitting (often known by DIN 2353 or ISO 8434-1 standards) is an engineered solution designed specifically for high-pressure hydraulic tubing. Its genius lies in separating the functions of sealing and thread engagement. The threads on the nut and body serve only one purpose: to provide the clamping force needed for the ferrule to do its job. They do not participate in the sealing process at all. This design isolates the seal from the rotational forces of tightening and creates a connection that is far more resistant to the dynamic pressures and mechanical vibrations common in hydraulic systems. The ferrule acts as a circular cutting tool, creating a permanent, visible groove in the tube that provides both a primary seal and immense holding power.
Dissecting the Ferrule’s Action
The ferrule is the heart of the fitting. During initial assembly, as the nut is tightened to a specific torque or number of turns (e.g., 1.25 turns past hand-tight), the tapered inner surface of the fitting body compresses the ferrule. This forces the ferrule’s hardened leading edge to bite into the softer tube metal. This action creates two distinct seals: one between the front face of the ferrule and the fitting body, and another where the ferrule has cut into the tube. This “bite” provides incredible grip, preventing the tube from pulling out under extreme pressure. After the initial assembly, the ferrule is permanently “set” onto the tube. The fitting can then be disassembled and reassembled multiple times for maintenance, and the seal will remain reliable because it is made by the perfectly formed ferrule seating back into the fitting body, not by re-deforming threads. This reusability and reliability are why bite-type fittings are a global standard for hydraulic equipment.
Which Fitting is Better for High-Pressure Hydraulic Systems?
A hydraulic system operates at pressures exceeding 3,000 PSI and is subject to pressure spikes. Using an inadequate fitting risks a dangerous high-pressure leak, which can cause fluid injection injuries and catastrophic equipment failure.
Bite-type fittings are unequivocally superior for high-pressure hydraulic systems. Their engineered mechanical seal is independent of the threads, providing a more robust, reliable, and vibration-resistant connection designed to handle extreme dynamic pressures.
The fundamental design of an NPT fitting makes it unsuitable for modern high-pressure hydraulics. The seal’s reliance on thread deformation and sealant creates a natural weak point. High pressure can force fluid through the spiral leak path, and pressure spikes can further expand the female port, compromising the seal. The wedging action concentrates stress, making the fitting brittle and prone to fatigue cracking. In contrast, the bite-type fitting is designed from the ground up for this environment. The ferrule’s bite creates a seal that is strengthened by internal pressure; the pressure pushes the tube outward, reinforcing the seal against the ferrule. The body of the fitting contains the pressure cleanly, without imparting dangerous radial stresses onto the port or component it is threaded into.
A Technical Pressure-Rating Comparison
Pressure ratings for fittings are determined by extensive testing under both static and dynamic (impulse) conditions. Bite-type fittings consistently outperform NPT across the board. A typical 1/2″ bite-type fitting in steel might be rated for a working pressure of 5,000 PSI (350 bar) or higher, with a 4:1 safety factor. This means it can withstand a burst pressure of 20,000 PSI. Conversely, a 1/2″ NPT fitting’s pressure rating is highly dependent on the material it’s threaded into and the quality of installation, but it is rarely recommended for service above 3,000 PSI in any dynamic system. The key differentiating factor is performance under impulse and vibration. The bite-type’s positive-lock seal remains stable, while the NPT’s thread-based seal can gradually loosen and leak, a phenomenon that is simply unacceptable in mission-critical hydraulic machinery.
Parameter | Bite-Type Fitting | NPT Fitting |
Typical Pressure Rating | Very High (up to 9000+ PSI) | Low to Medium (rarely > 3000 PSI) |
Performance Under Impulse | Excellent (maintains seal) | Poor (can loosen and leak) |
Sealing Mechanism | Mechanical bite on tube | Thread interference and sealant |
Failure Mode | Predictable (tube can yield) | Unpredictable (port can crack) |
Recommended Use | High-Pressure Hydraulics | Low-Pressure Pneumatics, Plumbing |
How Does Vibration Affect NPT and Bite-Type Fittings?
Equipment subject to heavy vibration, such as mobile construction machinery or industrial press lines, is experiencing recurring leaks at its fluid connections. The fittings are loosening over time, requiring constant re-tightening.
Vibration is a primary enemy of NPT fittings, causing the thread connection to loosen and compromising the sealant. Bite-type fittings are inherently vibration-resistant because the ferrule’s bite creates a positive mechanical lock on the tube.
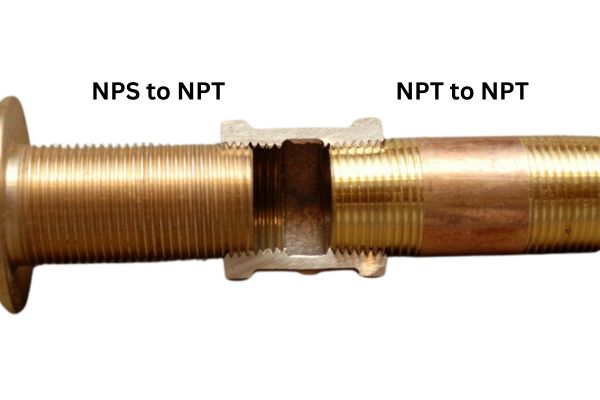
Vibration attacks fittings by creating micromovements. In an NPT connection, these tiny movements can slowly work the wedged threads apart. As the threads loosen, the compression on the sealant is reduced, and a leak path opens. The problem compounds over time, leading to significant leaks and potential fitting failure. Re-tightening provides only a temporary fix, as the root cause—the design’s susceptibility to loosening—is not addressed. For bite-type fittings, the opposite is true. The ferrule’s sharp edge is physically embedded into the tube. This positive lock, held securely by the clamping force of the nut, resists the micromovements caused by vibration. The nut is not under the same kind of wedging stress as an NPT thread, and the seal itself is separate from the threads, so it remains intact even in applications with extreme, continuous vibration.
The Engineering of Vibration Resistance
The resilience of the bite-type fitting comes from how it distributes forces. The clamping force is axial, pulling the ferrule straight into its seat in the body. The ferrule’s bite resists any torsional or axial movement of the tube itself. This creates a preloaded assembly that is stable and rigid. An NPT fitting, however, relies on friction from radial force. Vibration introduces cyclic loading that can overcome this static friction, allowing the threads to “walk” or back off. This is why NPT connections are strictly forbidden in any high-integrity system, such as aerospace, heavy mobile machinery, or high-pressure gas applications. The bite-type design, by creating a permanent, physical alteration to the tube, provides a far more secure and predictable connection that maintains its integrity throughout the service life of the machine, making it the only acceptable choice for equipment that moves, shakes, and operates under dynamic loads.
What Are the Key Differences in Installation and Reusability?
A system was assembled quickly, but now numerous connections are leaking. Maintenance teams are questioning whether the fittings can be reliably disassembled and reassembled without introducing new problems.
Bite-type fittings offer superior reusability and a more predictable installation process. NPT fittings require careful sealant application, have a high risk of installation error, and are not designed for repeated disassembly.
A Step-by-Step Installation Comparison
A direct comparison of the installation workflows reveals the practical advantages of a bite-type system.
Installation Step | Bite-Type Fitting | NPT Fitting |
1. Preparation | Cut tube square, deburr inside and out. Ensure the tube is clean. | Clean male and female threads of all old sealant and debris. |
2. Assembly | Slide the nut and ferrule onto the tube. Insert tube fully into fitting body. | Apply new, appropriate sealant (tape or paste) to male threads only. |
3. Tightening | Tighten the nut to be finger-tight. | Screw fitting in finger-tight. |
4. Final Torque | Use wrenches to tighten the nut to a specified number of turns (e.g., 1.25 turns) or to a specified torque. Creates a permanent bite. | Use a wrench to tighten 2-3 full turns past finger-tight. Stop when oriented correctly. Do not back off. |
5. Reassembly | Disassemble and reassemble freely. Tighten the nut to a specified torque. The seal is reliable. | Not recommended. Threads are deformed. A new seal requires complete cleaning and re-application of sealant. High risk of leaks. |
When is it Appropriate to Choose NPT Fittings?
Given its limitations, are there any applications where an NPT fitting is still a valid choice? An engineer needs to select the most cost-effective fitting for a low-consequence, static application.
NPT fittings remain a suitable and cost-effective choice for non-critical, static, low-pressure applications. These include general plumbing for water, permanent compressed air distribution lines, and industrial fluid transfer systems.
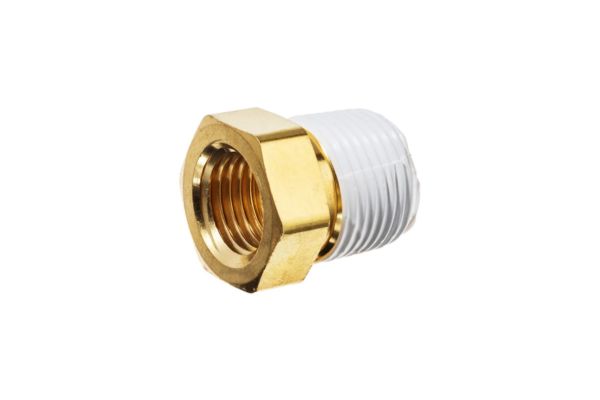
While modern hydraulic systems demand more advanced solutions, it is important to recognize the applications where NPT’s legacy design and low unit cost are advantageous. The key determining factors are pressure and dynamism. In a system that is assembled once and then left alone, with low and stable pressure (generally under 500 PSI), NPT can perform adequately. Its wide availability, especially in North America, and the low cost of individual fittings make it an economical choice for infrastructure like factory airlines or water coolant circuits. The risks associated with NPT (leaks from vibration, cracking from pressure spikes) are minimal in these stable, low-consequence environments. The decision to use NPT should always be a conscious one based on a clear understanding of its limitations.
Cost vs. Risk Analysis
The primary driver for choosing NPT is upfront cost. The fittings themselves are mass-produced and generally cheaper than precision-engineered bite-type fittings. However, a true cost analysis must consider the total cost of ownership, which includes potential risks. For a low-pressure water pipe, the cost of a slow drip is negligible. For a high-pressure hydraulic press, the cost of a leak includes lost hydraulic fluid (which is expensive), cleanup costs, potential environmental fines, machine downtime, and, most critically, extreme safety risks. Therefore, while NPT may save a few dollars per fitting initially, choosing it for inappropriate application transfers that cost higher operational risk and potential maintenance expenses. Bite-type fittings represent a higher initial investment in the component itself, but this investment buys reliability, safety, and lower long-term operating costs in any system where performance truly matters.
Conclusion
NPT fittings are for low-pressure, static plumbing, while bite-type fittings provide the only reliable solution for modern, high-pressure, dynamic hydraulic systems. Choosing correctly ensures system integrity, safety, and long-term performance. If you need to purchase bite type and NPT hydraulic fittings, contact Topa and we can customize the most suitable hydraulic fittings for your needs.