You need to replace a hose, but the specifications seem like a foreign language. Using the wrong component could mean catastrophic failure, dangerous fluid leaks, and extended, costly downtime for your equipment.
This M-Z glossary decodes essential hydraulic hose terminology. It clearly defines concepts from matched systems and MSHA ratings to working pressure, ensuring you have the precise information needed for safe and reliable hose selection.
Matched System to MSHA?
An assembly fails, but the hose supplier blames the fitting supplier, and vice versa. Using components from different manufacturers creates a liability gray area, leaving you with a failed system and no clear recourse.
A “matched system” is the use of hose and fittings from the same manufacturer, ensuring tested compatibility. MSHA is a critical safety rating for flame resistance, required for hoses used in underground mining operations.
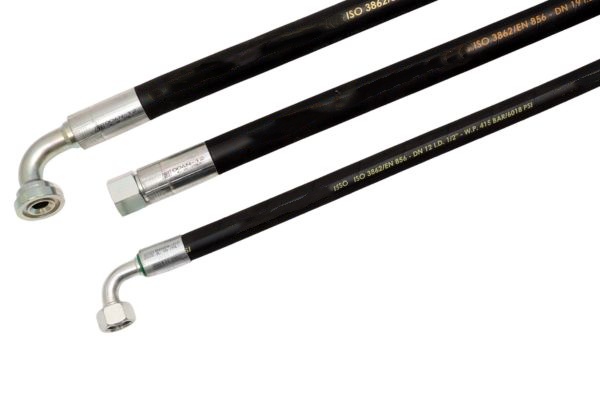
Ensuring Compatibility and Safety
Matched System: This is one of the most important concepts for hydraulic safety and reliability. A matched system means the hose and the fittings (couplings) have been designed, tested, and validated to work together by a single manufacturer. The manufacturer performs extensive impulse testing and burst testing on that specific combination to guarantee that a proper crimp will meet or exceed published performance standards. Mixing a hose from one brand with a fitting from another introduces unknown variables. The “bite” of the fitting’s stem and the compression of the ferrule may not be optimal for that specific hose’s construction, leading to a drastically weakened assembly that is prone to blow-offs. For this reason, we and most other reputable manufacturers will only guarantee the performance of our hose assemblies when our own fittings are used.
Maximum Working Pressure (MWP): This is the highest pressure that a hose assembly is rated for in continuous service. This is the single most important pressure rating to consider when selecting a hose and should never be exceeded in operation. It is determined by taking the hose’s minimum burst pressure and dividing it by the required safety factor (typically 4:1).
Metric: While dash sizes are based on inches, a significant portion of the global hydraulics market, particularly in Europe and Asia, uses metric measurements (millimeters) and standards, such as DIN and certain EN/ISO specifications for fittings and ports.
MSHA (Mine Safety and Health Administration): This US government agency sets mandatory safety standards for equipment used in underground mining. Hoses with an MSHA rating have a cover that has passed a stringent flame resistance test (CFR 30, Part 18.65), ensuring it will self-extinguish within a set time after an ignition source is removed. This is critical for preventing fires in enclosed, hazardous environments.
Nipple to OD?
A custom hose clamp doesn’t fit the new hose, even though the inner diameter is correct. The outer diameter was not considered during selection, causing delays and forcing a redesign of the mounting hardware.
The nipple is the internal part of a fitting that goes inside the hose. The OD, or Outer Diameter, is the total measurement across the outside of the hose, a critical dimension for clamping and routing.
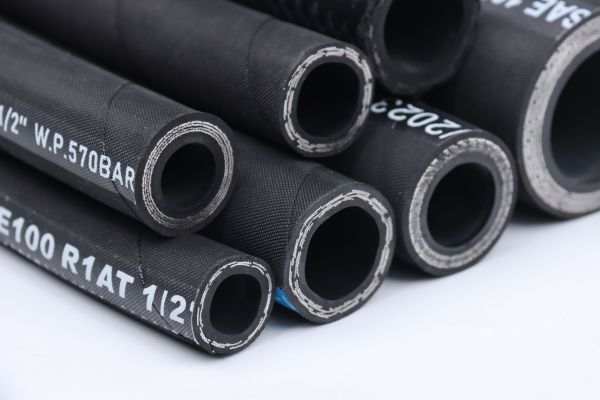
Critical Dimensions and Materials
Nipple: Also known as the stem or insert, the nipple is the portion of a hose fitting that is inserted directly into the hose’s inner tube. It typically has serrations or barbs that bite into the tube material to help create a seal and provide holding power once the ferrule is crimped. The nipple’s design is precisely engineered to work with the hose’s inner diameter and tube thickness.
NBR (Nitrile Butadiene Rubber): Often referred to simply as Nitrile, this is one of the most common synthetic elastomers used for the inner tube of hydraulic hoses. Its primary advantage is excellent resistance to standard petroleum-based hydraulic fluids, oils, and greases. It is a cost-effective and reliable choice for the majority of standard hydraulic applications. However, it has poor compatibility with certain synthetic fluids like phosphate esters or water-glycol mixtures.
Nominal Size: This is a general term used to describe the hose’s size, which almost always refers to the Inner Diameter (ID). It is often used interchangeably with “Dash Size.”
OD (Outer Diameter): This is the measurement of the hose from one side of its outer cover to the other. While the ID dictates flow, the OD is a critical dimension for selecting the correct clamps, protective sleeves, and spiral guards. It can also be an indicator of the hose’s construction; for a given ID, a hose with a larger OD typically has more or thicker reinforcement layers and thus a higher pressure rating.
Elastomer | Common Name | Best For | Not Good For |
NBR | Nitrile | Petroleum-based oils, air | Phosphate esters, weather/ozone |
CR | Neoprene | Weather/ozone, some refrigerants | Many synthetic fluids, solvents |
EPDM | EPDM | Water-based fluids, phosphate esters | Petroleum-based oils, gasoline |
Ozone Resistance to Push-on Hose?
A hose that sits exposed on a piece of farm equipment develops deep surface cracks and fails. It was not rated for ozone and UV exposure, causing the rubber cover to become brittle and disintegrate.
Ozone resistance measures a cover’s ability to withstand environmental cracking. A push-on hose is a low-pressure solution that uses special barbed fittings that do not require crimping or clamps for assembly.
Environmental Factors and Specialized Hoses
Ozone Resistance: Ozone is a gas present in the atmosphere that aggressively attacks the polymer chains in rubber, causing a specific type of degradation known as ozone cracking. This is especially prevalent on hoses that are under tension or bent. A hose cover with poor ozone resistance will become brittle and develop deep cracks when exposed to the environment, compromising its ability to protect the reinforcement. Manufacturers add special anti-ozonant chemicals to their cover compounds to improve this resistance.
Petroleum-Based Fluid: This is the most common category of hydraulic fluid, derived from refined crude oil. Standard hydraulic hoses with NBR (Nitrile) inner tubes are designed primarily for use with these fluids.
Pin-Pricking: This is the process of creating very small perforations in the hose’s outer cover. It is mandatory for hoses used to convey gaseous media (like compressed air or nitrogen) at pressures above 250 PSI. Gas can slowly permeate through the inner tube and become trapped under the cover. Without a path to escape, this trapped gas will form large blisters, causing the cover to separate from the reinforcement and leading to failure. Pin-pricking allows this trapped gas to safely vent to the atmosphere.
Push-on Hose: Also known by trade names like Push-Lok, this is a type of low-pressure hose (typically under 300 PSI) designed for quick and easy field assembly. It uses specially designed fittings with aggressive, deep barbs. The hose is simply pushed onto the fitting by hand, and the barbs grip the inner tube so tightly that no external ferrule or clamp is required. It is ideal for shop air lines, coolant lines, and other low-pressure fluid transfer applications.
Reinforcement to Routing?
A hose on a machine with constant flexing fails repeatedly in the same spot. It was built with a spiral-wire hose, which is too stiff; a more flexible braid hose was the correct choice.
Reinforcement is the internal strength layer of a hose. Routing is the physical path a hose follows during installation, a critical factor in preventing abrasion, kinking, and premature failure.
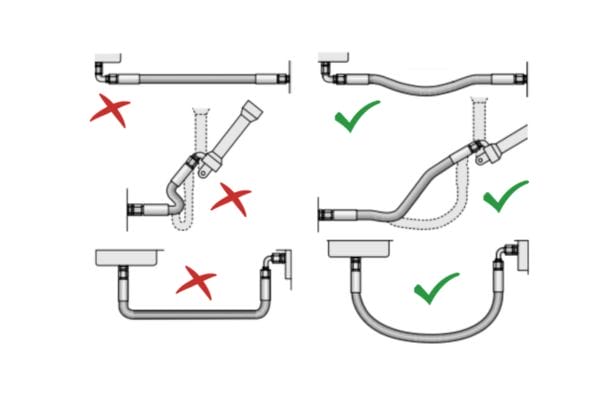
Strength Layers and Installation Practices
Reinforcement: This is the heart of a hydraulic hose’s strength. It is the layer sandwiched between the inner tube and the outer cover that contains the pressure. There are two primary types:
- Braid: Wires or textiles are interwoven around the tube. This construction is highly flexible and ideal for low to medium pressures and applications requiring tight routing (e.g., SAE 100R1, 100R2).
- Spiral: Wires are laid down in parallel layers, with each layer wrapped in an opposite helical direction. This construction is much stronger, offers superior impulse life, and is used for high and very-high-pressure applications (e.g., SAE 100R13, 100R15). The trade-off is that spiral hoses are significantly stiffer and have a larger bend radius.
Reusable Fitting: This is a mechanical fitting, usually with a threaded socket and nipple, that can be assembled onto a hose with hand tools and can be disassembled and reused on a new hose. While once common, they have largely been replaced by permanently crimped fittings, which offer far greater reliability and safety in modern high-pressure systems.
Routing: Proper routing is as important as selecting the correct hose. During installation, the hose’s path must be planned to avoid common failure modes. Hoses should be routed to avoid sharp bends, twisting, pulling, kinking, and abrasion against machine parts or other hoses. Using clamps, brackets, and protective sleeves is essential for a long-lasting, reliable installation.
Reinforcement Type | Key Advantage | Best Application | Example |
Braid | Flexibility | General purpose, tight routing | Forklift hydraulics, mobile equipment |
Spiral | Strength & Impulse Life | High pressure, heavy impulse | Excavators, hydrostatic drives |
SAE to Swage?
A hose is specified as “100R2,” but the meaning is unclear. This code represents a specific SAE standard that defines the hose’s construction, pressure rating, and intended application, making it a critical piece of information.
SAE is the standards body that defines most hydraulic hoses. Skive is the removal of the hose cover before crimping, a practice now largely obsolete due to modern no-skive designs. Swage is another term for crimping.
Standards and Assembly Methods
SAE (Society of Automotive Engineers): This US-based organization develops and publishes the “J517” standards that define the vast majority of hydraulic hoses used globally. These standards, such as SAE 100R1, 100R2, or 100R15, provide a universal specification for hose construction, dimensions, pressure rating, and performance. Specifying an SAE standard ensures a certain level of interchangeability and performance, regardless of the manufacturer.
Safety Factor: This is the ratio between a hose’s minimum burst pressure and its maximum working pressure. For dynamic hydraulic applications, the industry-mandated safety factor is 4:1. This means a hose with a 10,000 PSI burst pressure will have a maximum working pressure of 2,500 PSI. This margin provides safety against pressure spikes and gradual fatigue over the hose’s life.
Skive: This refers to the process of removing a portion of the hose’s outer cover (and sometimes the inner tube) before attaching a fitting. While many older hose systems required this, modern “no-skive” hose and fitting technology has made it largely unnecessary. No-skive systems are faster to assemble and have the added benefit of leaving the cover intact under the ferrule, which protects the wire reinforcement from corrosion.
Spiral Reinforcement: As described earlier, this is a construction method where layers of high-tensile steel wire are helically wrapped in parallel to provide strength for very high-pressure applications.
Swage: This is a verb that is synonymous with crimping. To swage a fitting is to use a machine to compress the ferrule and permanently attach it to the hose.
Temperature Range to Working Pressure?
A hose becomes rigid and cracks in a cold-weather application. The selected hose was not rated for the low ambient temperatures, causing the rubber compounds to lose their flexibility and fail prematurely.
Temperature range defines a hose’s operational limits. Working pressure is the maximum continuous pressure a hose is designed to handle safely, the most important specification for any hydraulic application.
Operating Limits and Final Definitions
Temperature Range: Every hose datasheet specifies a temperature range, for example, -40°F to +212°F (-40°C to +100°C). This defines the limits for both the fluid inside the hose (fluid temperature) and the environment outside (ambient temperature). Operating above the maximum temperature will accelerate aging, make the rubber brittle, and can cause the inner tube to harden and crack. Operating below the minimum temperature can cause the hose to become stiff and lose its flexibility, also leading to cracking under flexion. Some fluids or applications may require a de-rating of the maximum temperature.
Thermoplastic Hose: This is a category of hose that uses plastic materials (like nylon, polyester, or polyurethane) instead of rubber. They are known for being lightweight, having excellent chemical resistance, and extremely low volumetric expansion. Standards like SAE 100R7 and 100R8 cover thermoplastic hoses, which are often used in high-pressure hydraulic tools and material handling equipment.
Twist: Twisting a hose along its longitudinal axis during installation is a critical error that drastically reduces its service life. A twisted hose has its reinforcement wires in a state of constant stress. Under pressure, these forces will try to un-twist the hose, which can loosen fittings and cause the wire layers to fatigue and break. The layline should always be used as a guide to ensure it runs straight and is not spiraled after installation.
Vulcanization: This is the chemical process, typically involving heat and pressure, that cures raw rubber into a strong, stable, and elastic material suitable for use in a hose.
Working Pressure (Maximum): This is the ultimate operational guide. It is the highest pressure a hose should see in service and forms the basis for safe and reliable system design. It is what remains after applying a 4:1 safety factor to the hose’s minimum burst pressure.
Conclusion
Mastering this M-Z vocabulary completes your understanding of hydraulic hoses. This knowledge empowers you to select, install, and maintain fluid power systems with maximum safety, efficiency, and reliability.