Unlike tapered threads that rely on the thread itself for sealing, parallel threads use an elastomeric seal, making their assembly distinct and requiring specific techniques to achieve a leak-free connection.
Understanding Parallel Thread Fittings
A. Definition and Types of Parallel Thread Fittings
Parallel thread fittings are designed to create secure, leak-free connections in hydraulic systems. Unlike tapered threads, which rely on the shape of the thread itself for sealing, parallel threads achieve a seal through the use of elastomeric seals, such as O-rings or flat gaskets. This design allows for easier assembly and disassembly without compromising the integrity of the connection.
Several types of parallel thread fittings are commonly used:
SAE Straight Threads (SAE J1926 / ISO 11926): These fittings feature a straight thread design and are widely used in hydraulic systems. They provide a strong mechanical connection and are compatible with a variety of sealing methods. The SAE J1926 standard is often used in North America.
ISO 6149: ISO 6149 fittings are standardized international parallel threads used in hydraulic applications. They offer a robust sealing solution and are recognized for their reliability and ease of assembly, making them popular in both industrial and mobile equipment.
JIS B2351: This Japanese Industrial Standard specifies parallel threads for hydraulic fittings, ensuring compatibility and reliability in various applications. JIS B2351 fittings are designed to meet specific performance criteria in Japanese hydraulic systems.
BSPP Flat Face (ISO 1179): The British Standard Pipe Parallel (BSPP) fittings feature flat faces that promote even pressure distribution across the sealing surface. This design reduces the likelihood of leaks and is commonly used in hydraulic and pneumatic systems.
DIN Metric Flat Face (ISO 9974): DIN fittings adhere to German standards and are widely utilized in Europe. The metric flat face design ensures a reliable connection while accommodating a variety of hydraulic applications.
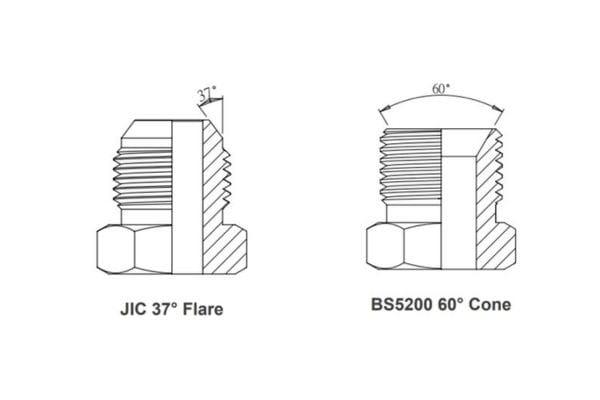
B. How Parallel Threads Differ from Tapered Threads
The primary difference between parallel and tapered threads lies in their sealing mechanism. Tapered threads create a seal through the wedging action of the threads as they tighten, which can lead to distortion over time. This distortion may affect the integrity of the connection, making it more susceptible to leaks after repeated assemblies.
In contrast, parallel threads rely on a separate sealing mechanism, such as an O-ring or gasket, which sits against a flat surface. This design allows for a more consistent and reliable seal, as the sealing surface is not affected by the tightening process. Moreover, parallel threads can be reused multiple times without the risk of thread damage, making them advantageous in maintenance and repair applications.
C. Applications and Benefits of Using Parallel Thread Fittings
Parallel thread fittings are widely used across various industries due to their reliability and ease of use. Common applications include:
Hydraulic Systems: Used in machinery, construction equipment, and automotive systems to create robust connections that withstand high pressure.
Pneumatic Systems: Ideal for air and gas applications where reliable sealing is critical.
Fluid Transfer Systems: Employed in industries such as oil and gas, chemical processing, and food and beverage for safe fluid transport.
The benefits of using parallel thread fittings include:
Ease of Assembly and Disassembly: Their design allows for quick and straightforward connections, reducing downtime during maintenance.
Enhanced Leak Prevention: With a proper sealing method, parallel threads minimize the risk of leaks, which is crucial in maintaining system integrity.
Reuse Potential: Unlike tapered fittings, parallel thread fittings can often be reused without compromising performance, leading to cost savings over time.
Standardization: Many parallel thread fittings adhere to international standards, promoting compatibility across different systems and regions.
Common Mistakes in Parallel Thread Assembly
Parallel thread assembly is critical in ensuring reliable, leak-free connections in hydraulic systems. Attention to detail and adherence to best practices can mitigate the risk of assembly failures. Unfortunately, several common mistakes can compromise the integrity of these assemblies.
A. Ignoring Thread and Surface Inspection
Common Issues (Burrs, Nicks, Scratches): One of the most significant oversights in parallel thread assembly is the failure to thoroughly inspect the threads and sealing surfaces before assembly. Burrs, nicks, and scratches can develop due to wear and tear, or they may occur during handling and transportation. Even minor imperfections on these surfaces can lead to incomplete seals, which ultimately results in leaks.
Technicians must take the time to visually and tactically assess each fitting. If any signs of wear or damage are present, the fitting should be replaced rather than reused. This precaution prevents potential failures that could occur during operation, ensuring the integrity of the hydraulic system.
Importance of Clean Sealing Surfaces: Cleanliness is paramount in achieving successful parallel thread assembly. Contaminants such as dirt, oil, or debris can interfere with the sealing surfaces, preventing a proper fit. A thorough cleaning of the threads and sealing surfaces with a suitable cleaner is essential before assembly. This step not only removes contaminants but also allows for a clearer view of any imperfections that may need attention.
Using a lint-free cloth or specialized cleaning tools can enhance the cleaning process. Ensuring that surfaces are free from contaminants helps create a secure, leak-proof seal that is crucial for the reliable operation of hydraulic systems.
B. Improper O-Ring Handling
Failure to Lubricate O-Rings: Another frequent oversight is the failure to lubricate O-rings before installation. O-rings play a critical role in creating seals between fittings. Proper lubrication is necessary to facilitate a smooth entry into the port, reducing friction and wear during assembly. Without adequate lubrication, O-rings may tear or become deformed, leading to leaks and system failures.
Technicians should always apply a light coat of compatible lubricant to O-rings before installation. This practice not only enhances the sealing capability but also prolongs the life of the O-ring, contributing to the overall durability of the assembly.
Using Incompatible Lubricants: Using lubricants that are not compatible with the O-ring material is another mistake that can lead to significant issues. Certain chemicals can degrade the O-ring material, compromising its sealing ability and potentially causing premature failure.
To avoid this, technicians should always refer to the manufacturer’s recommendations for appropriate lubricants tailored for specific O-ring materials. By using compatible lubricants, the longevity and reliability of the assembly are maintained.

C. Incorrect Tightening Techniques
Over-Tightening and Its Consequences: Over-tightening fittings is a prevalent mistake that can lead to numerous problems. Excessive torque can damage the threads, distort the O-ring, and create leaks, ultimately compromising the integrity of the connection.
Moreover, over-tightening can lead to a phenomenon known as “cold working,” where the material of the fitting becomes distorted and harder. This distortion can complicate future assembly attempts and result in further issues down the line.
Under-Tightening and Its Risks: On the opposite end of the spectrum, under-tightening fittings can create gaps that lead to leaks. A loose connection may be more susceptible to vibration and movement, increasing the risk of failure over time.
Finding the correct balance is crucial. Following specified torque values is essential for ensuring a secure and reliable connection. Technicians should be trained to recognize the importance of applying the right amount of torque for each fitting type.
D. Neglecting Torque Specifications
Importance of Following Manufacturer Guidelines: Each type of fitting is accompanied by specific torque specifications provided by the manufacturer. Neglecting these guidelines can result in improper assembly and compromised system performance. Understanding and adhering to these specifications is vital for achieving the desired seal and ensuring that the fitting can withstand the operational pressures expected in hydraulic systems.
Technicians should consult the manufacturer’s documentation regularly and ensure that they are well informed about the torque values required for the specific fittings they are working with.
Consequences of Improper Torque: Failure to apply the correct torque can lead to both over-tightening and under-tightening, which may result in leaks or premature fitting failure. Over time, repeated instances of improper torque application can lead to a pattern of assembly failures, resulting in costly downtime and repairs.
Regular training and refreshers on torque specifications can enhance technician competency and ensure that each assembly is completed correctly.
E. Inadequate Assembly Inspection
Signs of Poor Assembly: Many assembly failures stem from inadequate inspections following assembly. Common signs of poor assembly include visible O-rings, misaligned fittings, or excessive gaps between sealing surfaces. If any indication that the assembly is not seated properly is detected, technicians should re-evaluate the assembly process to identify and rectify any errors.
Importance of Visual Checks Post-Assembly: Conducting thorough visual inspections after assembly is vital for confirming the integrity of the connection. Technicians should be vigilant in checking for signs of improper fit, such as gaps or misalignment. Ensuring that O-rings are not visible and that fittings are fully seated on the sealing surfaces can help identify potential leaks before the system goes live.
Best Practices for Parallel Thread Assembly
A. Pre-Assembly Checks
Before beginning the assembly of parallel thread fittings, it’s crucial to perform thorough pre-assembly checks to ensure all components are in optimal condition for a successful installation.
Inspecting Threads and Sealing Surfaces:
Visual Inspection: Examine the threads and sealing surfaces for any signs of damage, such as burrs, nicks, or scratches. Even minor imperfections can compromise the seal and lead to leaks. Ensure that both male and female components are clean and free of debris.
Cleaning: Use a suitable cleaning agent to remove any contaminants from the threads and sealing surfaces. A clean connection is essential for achieving a reliable seal.
Check for Wear: Look for any signs of wear that may indicate the need for replacement. For instance, threads that appear flattened or excessively worn may not provide a secure connection.
Preparing Tools and Materials:
Gather Required Tools: Ensure you have all necessary tools on hand, including torque wrenches, screwdrivers, and cleaning supplies. Using the right tools is critical for achieving the proper torque and ensuring a secure fit.
Verify Component Compatibility: Confirm that the fittings and seals you are using are compatible with each other. Mismatched components can lead to assembly issues and potential system failures.
Lubrication: If applicable, prepare the lubricant for O-rings. A light coat of compatible system fluid or designated lubricant helps the O-ring transition smoothly into the port, facilitating a better seal.
B. Assembly Steps
Following a detailed step-by-step assembly process is essential to achieve a secure and leak-free connection.
Step-by-Step Assembly Process:
Step 1: Thread Engagement: Start by gently screwing the male fitting into the female port until it is finger-tight. Avoid using tools at this stage, as it is crucial to ensure that the threads are engaging properly without cross-threading.
Step 2: Lubricate O-Ring: If your fitting has an O-ring, apply a thin layer of lubricant. This step minimizes friction during assembly and helps ensure a proper seal.
Step 3: Finger Tightening: After engaging the threads, continue to tighten the fitting by hand until it is snug but not overly tight. This initial snugness helps align the fitting properly without applying excessive pressure on the O-ring or sealing surface.
Step 4: Torque Application: Using a calibrated torque wrench, apply the specified torque to the fitting. Refer to the manufacturer’s guidelines for the appropriate torque values to avoid over-tightening, which can damage the fitting or cause seal failure.
Importance of Finger-Tightening Before Full Torque:
Alignment: Finger-tightening helps ensure that the fitting is properly aligned before applying torque, reducing the risk of cross-threading and ensuring a better fit.
Preventing Damage: This initial step minimizes the risk of damaging the O-ring or the sealing surfaces by allowing the fitting to seat properly before applying full torque.
Improved Seal Integrity: Proper alignment and snug fit help achieve a more consistent seal, ultimately enhancing the reliability of the connection.
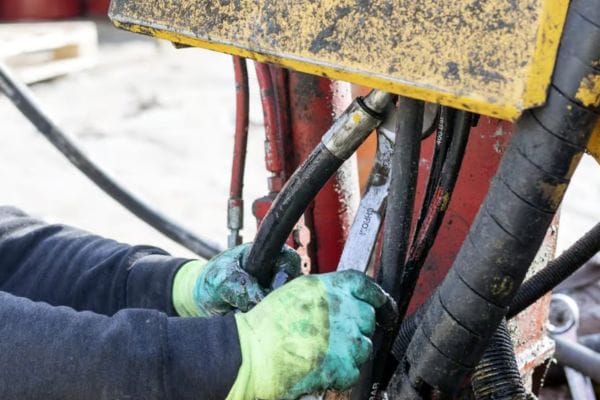
C. Post-Assembly Inspections
After the assembly is complete, conducting thorough post-assembly inspections is crucial for verifying the integrity of the connection.
Checking for O-Ring Visibility:
Visual Inspection: Examine the assembled fitting to ensure that the O-ring is not visible once the fitting is fully seated. A visible O-ring may indicate that the fitting is not properly engaged, which could lead to leaks.
Sealing Surface Check: Ensure that the sealing surface is flush with the fitting, confirming that the O-ring is compressed appropriately to create a secure seal.
Ensuring Complete Seating of Fittings:
Final Tightness Check: Gently attempt to tighten the fitting slightly more to ensure it is fully seated. Be cautious not to exceed the specified torque during this step.
Functional Testing: If possible, conduct a pressure test on the assembly to confirm that there are no leaks under operational conditions. This test helps ensure that the assembly can withstand the pressure of the hydraulic system without failure.
Conclusion
Best practices, including thorough pre-assembly checks, proper O-ring lubrication, adherence to torque values, and diligent post-assembly inspections, help reduce leak risks and improve safety. Continuous education and training are also essential for maintaining assembly quality and equipping technicians with the necessary skills.
FAQ
What are parallel thread fittings?
Parallel thread fittings are connections where the threads are straight and do not taper. They rely on elastomeric seals or O-rings to achieve leak-free connections.
Why is thread inspection important before assembly?
Inspecting threads ensures that there are no burrs, nicks, or scratches that could compromise the seal and lead to leaks during operation.
How should O-rings be prepared before installation?
O-rings should be lubricated with a compatible lubricant to ensure smooth installation and to prevent tearing or deformation.
What are the consequences of over-tightening fittings?
Over-tightening can damage the threads, distort the O-ring, and lead to leaks, as well as make future assemblies more difficult.
Why is it necessary to follow torque specifications?
Following torque specifications helps ensure the fittings are neither too loose nor too tight, which is crucial for maintaining a secure and leak-free connection.
What should I check after assembly to ensure proper installation?
After assembly, inspect for visible O-rings, proper alignment of fittings, and ensure that the fittings are fully seated without excessive gaps.