Every ball valve is a symphony of precision-engineered parts working in harmony. The ball itself, usually made of stainless steel or brass, serves as the central element, enabling or blocking flow. The handle or actuator provides the mechanism for rotation, while the stem connects the handle to the ball. Seats and seals ensure a leak-proof operation, even under high pressure.
How Does Ball Valve Flow Direction Work?
Explanation of the Flow Path in a Ball Valve
The brilliance of a ball valve lies in its simplicity. At the heart of this design is a ball with a precision-machined hole, or bore, that dictates the flow of fluids or gases. When the handle aligns the bore with the pipeline, the flow is seamless and unrestricted. Turn the handle 90 degrees, and the bore shifts perpendicular to the pipeline, stopping the flow entirely. This mechanism not only offers instant on-off control but also minimizes pressure drop, making ball valves a top choice for efficient fluid management in residential, commercial, and industrial systems.

Understanding the Role of the Ball and Stem
The ball and stem work in tandem to achieve precise flow control. The ball serves as the gatekeeper, with its bore allowing or halting the flow depending on its alignment. The stem connects the external handle to the internal ball, transmitting the rotational force needed to open or close the valve. Equipped with seals and bearings, the stem ensures smooth, leak-proof operation, even under high pressure or frequent use. Together, these components form the backbone of the valve’s functionality, enabling accuracy, reliability, and long-term performance.
Types of Ball Valves and Their Flow Direction
One-Piece, Two-Piece, and Three-Piece Ball Valves
Ball valves come in various configurations, each tailored to specific needs. One-piece valves are compact and cost-effective, ideal for basic applications, though their flow direction cannot be disassembled for maintenance. Two-piece valves strike a balance between accessibility and durability, with detachable components for cleaning or repairs. Three-piece valves, however, shine in demanding environments—they allow for complete disassembly without removing the valve from the pipeline, ensuring seamless flow direction control and extended lifespan.
Full Port vs. Reduced Port Ball Valves
The distinction between full port and reduced port ball valves lies in their bore size. Full port valves offer an unrestricted flow path that matches the diameter of the pipeline, minimizing pressure drops and turbulence. Reduced port valves, on the other hand, have a smaller bore, making them lighter and more economical while maintaining effective flow control. Choosing the right type depends on the system’s need for efficiency versus cost.
Multi-Port Ball Valves: T-Port and L-Port Flow Patterns
When systems demand more than simple on-off control, multi-port ball valves come into play. T-port valves can direct flow to multiple outlets simultaneously or isolate one pathway, offering flexibility in complex systems. L-port valves, meanwhile, allow switching between two flow paths, ensuring precise control in dual-direction applications. Understanding these unique flow patterns is crucial for selecting the right valve for your system’s needs.
Identifying Ball Valve Flow Direction
Common Flow Direction Markings and Symbols
Manufacturers often simplify identifying ball valve flow direction with markings and symbols. Arrows engraved on the valve body indicate the correct flow path, while some valves include the words “IN” and “OUT” for clarity. These visual cues eliminate guesswork during installation, ensuring the valve operates as intended. Understanding these markings is key to preventing errors that could disrupt the system’s performance.
What to Do If the Valve Has No Markings
When a ball valve lacks flow direction indicators, careful inspection becomes essential. Begin by examining the bore of the valve; in many cases, the handle alignment provides clues—parallel positioning typically signifies an open flow path. For multi-port valves, consulting the manufacturer’s manual is vital to understanding flow patterns. In the absence of documentation, a quick flow test with low-pressure fluid can confirm the correct direction, ensuring a smooth and accurate setup.
Factors That Influence Flow Direction in Ball Valves
Valve Design and Manufacturing Variations
Not all ball valves are created equal. Design elements such as the position of the ball bore, the type of seals used, and the valve’s overall configuration can significantly impact flow direction. For example, some valves are bi-directional, allowing flow in either direction, while others are uni-directional, designed for a specific flow path. Manufacturing tolerances and material choices further influence how the valve performs under various conditions, making it essential to select a valve that aligns with your system’s requirements.
System Pressure and Temperature Considerations
The operational environment also dictates flow direction in ball valves. High-pressure systems demand robust seals and precise flow alignment to prevent leaks or failures. Similarly, extreme temperatures can affect the valve’s materials, causing expansion, contraction, or seal degradation. Selecting a ball valve engineered for the specific pressure and temperature ranges of your application ensures consistent performance and safe operation, no matter the conditions.
How to Determine the Correct Flow Direction for Installation
Reading Manufacturer Specifications
Manufacturer specifications are your primary guide to ensuring correct valve installation. These documents detail crucial aspects such as the valve’s intended flow direction, pressure limitations, and compatible applications. Often, they include diagrams or flow charts indicating the proper orientation of the ball bore. Ignoring these instructions risks improper installation, which could lead to leaks, system inefficiency, or even equipment damage. Before starting any installation, thoroughly review the provided documentation to confirm you understand the valve’s design and functionality. Additionally, keeping these specifications accessible for future reference can save time and prevent mistakes during maintenance or replacement.
Visual Inspection Techniques
When documentation isn’t available, a visual inspection can provide essential insights. Most ball valves feature external markings like arrows, “IN” and “OUT” labels, or other symbols that indicate flow direction. For two-way valves, the handle position is often a reliable indicator—when the handle is parallel to the pipe, the valve is open, aligning the flow with the bore. Multi-port valves, such as T-port or L-port configurations, require extra attention to confirm the ball’s internal alignment matches the desired flow path. Spending a few moments to observe and verify these details ensures proper installation and prevents system interruptions.
Testing for Proper Flow Direction
In cases where markings are absent or unclear, testing becomes a critical step. Using a low-pressure fluid, manually operate the valve to observe the flow pattern. Start with the valve in an open position and gradually turn the handle, noting how the flow changes. This hands-on method can also identify any resistance or irregularities in the mechanism, signaling potential issues that need to be addressed. For more complex systems, using specialized equipment like flow meters can provide precise confirmation of the valve’s performance. Testing may take extra time, but it guarantees accuracy and avoids costly errors.
Common Mistakes to Avoid
Installing Without Checking Flow Direction
One of the most frequent errors in ball valve installation is neglecting to verify the flow direction before securing the valve in place. This oversight may seem minor but can lead to significant consequences, including restricted flow, increased wear on the valve components, and even system malfunctions. For example, a uni-directional ball valve, designed to operate in a specific flow path, will not function correctly if installed backward. This can result in leakage or pressure imbalances that compromise system efficiency. To avoid this, always double-check the valve’s markings or refer to the manufacturer’s documentation before starting the installation process. Even a quick inspection of handle alignment or visible flow indicators can prevent costly errors.
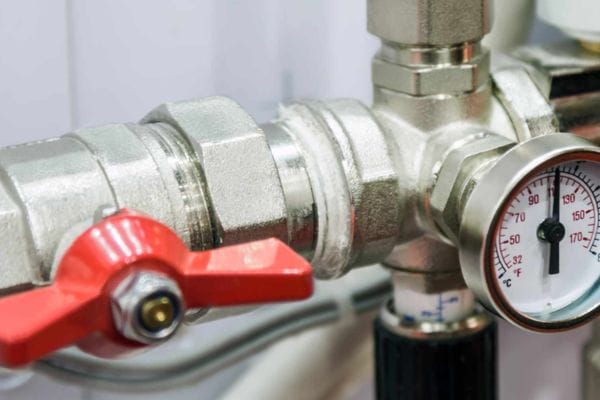
Ignoring Manufacturer Guidelines
Manufacturer guidelines exist for a reason: they are tailored to the specific design and functionality of the valve. Failing to adhere to these instructions can lead to improper installation, reduced valve lifespan, or safety hazards. For instance, some valves may require precise torque settings for the stem or specific sealing materials to match system conditions like high pressure or temperature extremes. Overlooking such details might void the warranty and result in unexpected failures. Additionally, neglecting the recommended cleaning or preparation steps—such as flushing out debris from the pipeline—can introduce contaminants that damage the valve over time.
By disregarding these guidelines, you also miss out on critical information about flow direction, operational limitations, and maintenance protocols. Before proceeding with installation, take the time to familiarize yourself with the valve’s specifications. This small investment in preparation ensures the valve operates as intended and eliminates potential risks.
Best Practices for Setting Up Ball Valves
Pre-Installation Checklist
A thorough pre-installation checklist is critical to ensuring the successful integration of a ball valve into any system. Start by inspecting the valve for visible defects such as cracks, uneven surfaces, or damaged seals. Confirm that the valve’s materials and pressure ratings align with the application’s requirements, particularly in high-pressure or high-temperature environments. Next, clean the pipeline to remove debris, dirt, or residues that could compromise the valve’s performance. It’s also essential to review the manufacturer’s specifications and verify details such as flow direction markings, torque requirements for bolts, and gasket compatibility. This upfront diligence prevents unnecessary delays and costly mistakes during installation.
Ensuring Correct Orientation During Installation
Proper orientation is fundamental for a ball valve to operate efficiently. Begin by aligning the valve with the pipeline, ensuring that flow direction indicators (e.g., arrows or “IN” and “OUT” labels) correspond to the intended fluid path. For valves without clear markings, reference the bore position or consult the manufacturer’s manual. Tighten the bolts evenly in a crisscross pattern to prevent misalignment or leaks, ensuring a secure but not over-tightened fit.
For multi-port valves, pay extra attention to the alignment of the ball’s bore, especially if switching between multiple flow paths is required. During installation, periodically test the valve’s operation by turning the handle to confirm that it moves freely and aligns correctly with the ports. This step ensures the valve’s functionality before the system is pressurized, avoiding the need for costly adjustments later.
Troubleshooting Flow Direction Issues
How to Spot Incorrect Flow Direction in Action
Incorrect flow direction in a ball valve can lead to immediate and noticeable problems within a system. Common signs include reduced flow rate, unusual pressure fluctuations, or visible leaks around the valve. You might also notice that the system struggles to maintain consistent performance, such as pumps overworking or equipment downstream failing to function as expected. In some cases, the handle may feel unusually stiff or misaligned, indicating improper installation. For multi-port valves, incorrect flow direction may result in fluid traveling to unintended outlets, disrupting operations. Observing these warning signs early can prevent more significant issues down the line.
Step-by-Step Guide to Correcting Installation Errors
Turn Off the System and Depressurize: Begin by shutting down the system and relieving any pressure in the pipeline to ensure safe handling of the valve.
Inspect the Valve Orientation: Examine the valve for markings, such as arrows or port labels, to verify if it aligns with the intended flow direction. If no markings are present, use a low-pressure flow test or consult the manufacturer’s guide to confirm the correct orientation.
Remove the Valve: Loosen the bolts or fittings and carefully remove the valve from the pipeline. Be cautious to avoid damaging seals or threads during this process.
Reposition the Valve: Align the valve properly with the flow direction, ensuring that any markings match the system’s requirements. For multi-port valves, check the ball’s internal orientation against the desired flow path.
Reinstall and Test: Reattach the valve securely, tightening bolts in a crisscross pattern to prevent leaks. Gradually reintroduce pressure and test the system to confirm that the valve operates correctly and that flow follows the intended path.
Document and Monitor: Record the changes made for future reference and observe the system over time to ensure the problem is fully resolved.
Conclusion
Proper flow direction is the backbone of any well-functioning system that uses ball valves. Misalignment can lead to reduced efficiency, leaks, or even catastrophic system failures, causing unnecessary costs and operational delays. By understanding how ball valves work and carefully considering their flow direction during installation, you ensure smooth, reliable operation and maximize the valve’s lifespan.
FAQ
What is ball valve flow direction?
Ball valve flow direction refers to the path that fluid or gas takes through the valve, controlled by the alignment of the valve’s ball bore.
How do I identify the flow direction on a ball valve?
Look for markings like arrows, “IN” and “OUT” labels, or other symbols on the valve body. These indicate the correct flow direction.
What happens if the flow direction is wrong?
Incorrect flow direction can cause reduced flow, leaks, system inefficiency, and potential damage to the valve or pipeline.
Can a ball valve be installed in any direction?
Some ball valves are uni-directional, meaning they only work in one direction. Always check the valve markings and manufacturer specifications for proper installation.
How do I troubleshoot flow direction issues in a ball valve?
Inspect for visible markings or use a low-pressure test to check the flow direction. Misaligned valves may cause pressure fluctuations or leaks.
Are there different types of ball valves for different flow directions?
Yes, there are uni-directional and bi-directional ball valves, as well as multi-port valves with T-port or L-port configurations, each suited for specific flow requirements.