A leaking ball valve is more than just an inconvenience—it can lead to system inefficiency, wasted resources, and even costly repairs if left unaddressed. The frustration of dealing with continuous drips or pressure losses is compounded by the risk of damage to surrounding equipment or areas, which can escalate maintenance costs and downtime.
Common Causes of Ball Valve Leakage
Ball valves are valued for their durability and ability to provide reliable shutoff control, but leaks can still occur due to several common causes. Understanding these causes is essential for diagnosing issues, preventing future leaks, and extending the valve’s lifespan. Leaks in ball valves typically result from issues with the stem, seats, seals, improper installation, or fluctuations in pressure and temperature.
Stem Leaks
Cause:
Stem leaks are often due to worn or damaged stem O-rings or seals. Over time, seals can lose elasticity due to regular use, exposure to extreme temperatures, or chemical corrosion. Stem seals are responsible for preventing fluid from escaping around the valve’s stem, but when these seals wear out or crack, they no longer create a tight barrier. High-pressure systems or applications with frequent valve actuation tend to increase wear on stem seals, making leaks more likely.
Symptoms:
Signs of a stem leak include fluid leaking around the valve stem, especially during valve actuation or in pressurized systems. If the stem’s O-rings or seals have aged or deteriorated, they may no longer prevent fluid from seeping through, leading to visible leakage.
Impact:
Stem leaks compromise system efficiency by allowing fluid loss, which can reduce pressure in the system. In addition to causing potential contamination, stem leaks may increase the need for regular maintenance, as they often necessitate replacement of the damaged seals. If ignored, stem leaks can result in more significant issues, including increased wear on the valve and surrounding components.
Seat and Seal Wear
Cause:
Ball valves rely on seats and seals to ensure tight shutoff, but these components are vulnerable to wear, especially in applications with abrasive or corrosive fluids, high temperatures, or high pressure. Over time, the valve seats and seals may become worn, eroded, or even slightly deformed, making it difficult for the valve to close securely. Each time the valve is opened or closed, it experiences minor friction, which eventually causes wear on the seat and seals.
Symptoms:
A worn seat or seal often results in leaks at the main sealing points of the valve. The leakage may be present even when the valve is fully closed, as the worn-out seat can no longer maintain a complete seal. For high-temperature or abrasive applications, leaks may appear more quickly as seals degrade faster under stress.
Impact:
Worn seats and seals reduce the valve’s sealing effectiveness, which can lead to leaks and contamination risks in the fluid system. This issue compromises the valve’s ability to control flow, creating inefficiencies in system performance. Moreover, seats and seals that degrade due to constant exposure to chemicals or pressure variations require frequent inspection and replacement, increasing maintenance time and costs.
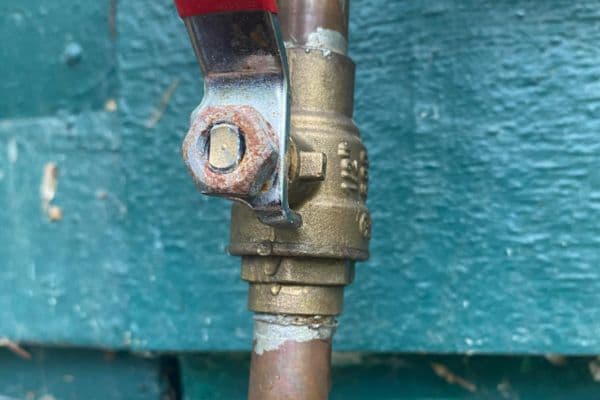
Improper Installation
Cause:
Improper installation practices, such as incorrect alignment, overtightening, or inadequate support, can significantly impact a ball valve’s performance. When a valve is misaligned with the pipeline, it can create uneven pressure distribution on the seals and seats. Overtightening during installation can also damage the valve body and seats, reducing the valve’s ability to seal properly. Additionally, poor support during installation may cause the valve to shift over time, leading to leaks as it experiences vibration and pressure fluctuations.
Symptoms:
Leaks due to improper installation are often seen near the connection points, such as the valve’s flanges or threaded ends. Misalignment causes the valve to strain against the pipe, leading to gaps or cracks in the seals over time. An improperly installed valve may also feel loose or wobbly, as it lacks the necessary support to remain stable under pressure.
Impact:
Incorrect installation practices put extra stress on the valve components, leading to premature wear and potentially damaging the valve permanently. As a result, improperly installed valves may require frequent repairs or complete replacement, driving up maintenance costs. Moreover, if the valve’s alignment is not corrected, leaks will likely recur, impacting system reliability and efficiency.
Pressure Spikes or Temperature Changes
Cause:
Sudden pressure spikes or temperature fluctuations can put excessive stress on a ball valve’s seats and seals. When pressure within the system suddenly increases, it forces the seals to compress beyond their normal capacity, which can cause deformation or cracking. Similarly, drastic temperature changes can cause materials to expand or contract, weakening the seals and reducing their ability to form a tight seal.
Symptoms:
Leaks caused by pressure or temperature changes may be intermittent and occur primarily during high-stress periods, such as when the system experiences high-pressure surges or sudden temperature changes. These leaks may appear as minor drips initially but can worsen over time if the valve remains under continuous stress.
Impact:
Pressure spikes and temperature fluctuations can cause permanent damage to valve components if they occur frequently. This issue shortens the lifespan of the valve, as repeated stress leads to micro-damage that accumulates over time. Such leaks can disrupt system performance and may require expensive replacements or reinforcement of the valve with pressure relief devices. Moreover, systems subject to frequent pressure or temperature changes need robust valves with materials and designs that can withstand such stresses to prevent recurrent leaks.
Inspecting Ball Valve Leaks
Why Inspection Matters
Ball valves are designed for durability and efficient on/off control, but regular wear, environmental factors, and pressure changes can cause leaks. Early detection through regular inspections can prevent small issues from becoming larger problems. A leaking ball valve not only leads to system inefficiencies and fluid loss but can also cause downstream components to experience additional stress, potentially leading to wider system failures. Regular inspections minimize downtime, reduce repair costs, and maintain system safety, especially in high-pressure or high-temperature applications.
Inspection Checklist
A thorough inspection can reveal signs of leakage and help diagnose the underlying cause. Here’s a checklist to follow when inspecting ball valves for potential leaks:
Visual Inspection
Check for Signs of Fluid Leaks: Look for visible fluid around the valve body, stem, and connection points. Areas near the stem are particularly vulnerable to leaks, especially if the O-rings or stem seals are worn.
Examine the Valve Body for Cracks or Corrosion: Over time, exposure to certain chemicals or extreme temperatures can weaken the valve body, causing cracks or corrosion that lead to leaks.
Inspect Connection Points: Check for moisture or fluid around flanges, threaded ends, or welded joints. Even minor leaks at these connection points can worsen over time if not addressed.
Note Any Residue or Discoloration: Discoloration or residue around the valve can be a sign of prolonged leakage or chemical exposure, indicating wear or damage.
Pressure Testing
Why Pressure Testing Is Important: Pressure testing can confirm whether the valve is holding pressure effectively when in the closed position. A leaking valve may show a pressure drop, signaling an internal leak or a worn seat.
How to Perform a Basic Pressure Test:
Close the valve fully and pressurize the system to the standard operating pressure.
Monitor the pressure gauge for a set time (often 15-30 minutes) to check for any pressure drop. A pressure drop indicates a potential leak.
For more accurate results, isolate the section of the system with the valve to test solely for valve leakage.
Check for Back Pressure Leaks: Some systems may require testing in reverse, especially if the valve is used in applications with fluctuating pressure. This can reveal leaks on the downstream side.
Listen for Sounds
Hissing Sounds: In pressurized systems, hissing sounds around the valve often indicate a pressure leak. The sound usually results from gas or fluid escaping through a small gap in the valve’s seal or body.
Other Noises: Popping or creaking noises during valve operation can signal internal wear, particularly if the valve is under high pressure. These sounds may indicate compromised seals or a misaligned ball.
Inspect Seals and O-Rings
Check for Wear and Brittleness: Over time, seals and O-rings can become brittle, cracked, or worn. These components are critical to maintaining a leak-proof seal, so damage to seals or O-rings is a common cause of leaks.
Look for Discoloration: Chemical exposure, extreme temperatures, or pressure spikes can cause discoloration or deterioration of seals and O-rings. If they appear discolored or stiff, they may need replacement.
Examine Seals for Fit: Seals that no longer fit snugly around the stem or seat areas can allow fluid to leak through. Regular inspections can ensure that seals maintain their elasticity and proper fit.
Safety Precautions
Inspecting ball valves, especially in high-pressure systems, requires safety measures to prevent injury and ensure accurate results:
Depressurize the System: Before beginning any inspection, ensure that the system is fully depressurized. Pressurized systems can release fluid suddenly, posing a risk of injury.
Wear Protective Gear: Gloves, safety goggles, and protective clothing are essential, particularly in systems involving chemicals, high-pressure fluids, or extreme temperatures.
Check for Hazardous Materials: If the system handles corrosive or hazardous fluids, make sure you follow all safety protocols for handling such materials, including additional protective equipment or ventilation.
Label Inspection Areas: For large or shared systems, label the section undergoing inspection to avoid accidental activation by other operators.
Fixing a Leaking Ball Valve: Step-by-Step Solutions
Leaks in ball valves can occur in several locations and for different reasons, such as worn seals, improper installation, or pressure spikes. Addressing these leaks requires understanding the leak source and following the correct steps for repair.
Fixing Stem Leaks
Stem leaks are a common issue caused by worn or damaged O-rings or stem seals, which lose elasticity over time or due to exposure to high pressure and temperature fluctuations.
Step 1: Shut Off System Pressure and Drain Any Remaining Fluid
Begin by shutting off the system to release any remaining pressure.
Ensure the valve is fully drained before starting repairs to avoid spillage or accidental pressure release.
Step 2: Remove the Valve Handle and Access the Stem
Detach the valve handle or actuator from the top of the stem.
Once the handle is off, you should have access to the stem, where the O-rings or seals are located.
Step 3: Replace Damaged O-Rings or Stem Seals
Use pliers or a seal puller to remove old O-rings or seals from the stem.
Clean the stem area to remove any residue or debris.
Place new, compatible O-rings or seals around the stem, ensuring they fit snugly to prevent further leaks. Use a light coating of lubricant compatible with the system’s fluid to ease installation and prolong seal life.
Step 4: Reassemble the Valve and Test for Leaks
Reattach the handle and reassemble the valve as per manufacturer instructions.
Restore system pressure and inspect the stem area for any leaks.
If leaks persist, check that the O-rings are properly seated or consider using higher-quality seals for better performance.

Replacing Worn Seats and Seals
Worn seats and seals lead to leaks at the primary sealing points of the valve. This issue usually requires partial dismantling of the valve to replace damaged components.
Step 1: Depressurize and Dismantle the Valve
Depressurize the system and ensure no residual fluid is present before starting the repair.
Dismantle the valve by removing the body bolts or by unscrewing it, depending on the valve design.
Step 2: Remove Old Seats and Seals
Locate the valve’s seats, typically situated around the ball inside the valve body.
Carefully remove the worn seats and seals using a pick or small screwdriver.
Clean the seating areas thoroughly to remove debris, residue, or rust, which could interfere with the new seals.
Step 3: Install New, Compatible Seats and Seals Based on Valve Specifications
Purchase replacement seats and seals that match the valve’s specifications, as incompatible materials can worsen the problem.
Place the new seats into the valve body, ensuring they fit securely around the ball to create an effective seal.
Step 4: Reassemble and Test Under Pressure to Ensure a Complete Seal
Reassemble the valve and apply pressure to the system.
Monitor the valve for leaks by visually inspecting the sealing points.
If the valve still leaks, check the seats again for proper alignment or consider consulting a specialist.
Correcting Installation Issues
Improper installation can cause alignment issues, stress on the valve, and subsequent leaks. Fixing these issues involves realigning and securing the valve correctly within the system.
Step 1: Ensure Valve Alignment Is Correct
Verify that the valve is correctly aligned with the pipeline. Misalignment places undue pressure on the valve seats and connections, causing leaks.
Adjust the position of the valve to ensure it’s aligned parallel to the pipe axis.
Step 2: Check Support and Reposition as Necessary to Eliminate Stress Points
Confirm that the valve is properly supported to prevent shifting due to vibration or pressure changes.
If the valve feels loose, reposition and secure it with appropriate support or clamps to ensure stability.
Step 3: Follow Proper Torque Specifications When Tightening
Over-tightening or under-tightening can lead to connection issues and leaks.
Tighten the valve connections according to the manufacturer’s torque specifications to avoid excess stress on the valve body and seals.
Step 4: Inspect for Any Remaining Leaks After Reinstallation
Once reinstalled, inspect the valve for leaks at all connection points.
Monitor the valve under operating conditions to ensure it remains leak-free and properly seated in the system.
Dealing with Pressure and Temperature-Related Leaks
Leaks can also result from sudden pressure spikes or temperature changes, which stress the valve’s seals and seats. Addressing these leaks requires stabilizing system conditions to protect the valve components.
Step 1: Install Pressure Regulators or Relief Valves to Avoid Spikes
Install pressure regulators to maintain consistent pressure within the system and prevent spikes that could damage valve seals.
For high-pressure applications, relief valves help manage sudden increases, protecting the valve from excessive pressure.
Step 2: Adjust System Temperatures Gradually if Possible
If the system is prone to temperature fluctuations, adjust temperature settings gradually to avoid rapid expansion or contraction that can damage seals.
Use insulation or temperature control mechanisms to stabilize fluid temperatures around the valve.
Step 3: Monitor the Valve During High-Stress Operations to Catch Leaks Early
During high-stress operations, monitor the valve closely for signs of leakage, such as hissing sounds or drips.
Conduct regular inspections in high-pressure or high-temperature systems to catch leaks before they worsen.
When to Replace a Leaking Ball Valve
Deciding when to replace a leaking ball valve instead of repairing it can save time, resources, and prevent further damage to the system. While repairs are often effective for minor leaks, there are cases where replacement is more practical and cost-efficient.
Evaluating Repair Costs vs. Replacement
One of the key factors in deciding whether to replace a ball valve is evaluating the costs of repeated repairs. While minor issues, such as worn O-rings or loose fittings, are generally inexpensive to fix, persistent or recurring leaks can indicate underlying wear that simple repairs cannot address. If you find yourself frequently repairing the valve or if replacement parts (like seals and seats) are wearing out quickly, the costs of repairs may soon surpass the cost of a new valve. Replacing the valve may be a better investment, as a new valve can improve system reliability and reduce ongoing maintenance expenses.
Additionally, consider the downtime caused by ongoing repairs. In high-use systems or critical applications, frequent maintenance interruptions can have operational and financial impacts, making replacement more cost-effective in the long run.
Signs a Valve Should Be Replaced
If a ball valve exhibits any of the following signs, replacement may be necessary to ensure optimal performance and safety:
Persistent Leaks Despite Repairs
If leaks continue to occur even after multiple repairs, the valve’s internal components may be irreparably worn or damaged. Persistent leaks may indicate that the valve is no longer capable of creating a tight seal, often due to seat or stem damage that cannot be permanently fixed. In such cases, replacement is usually the best option.
Visible Corrosion, Cracking, or Severe Wear
Corrosion or cracking on the valve body, stem, or ball is a strong indicator that the valve is nearing the end of its lifespan. Corrosion not only weakens the structural integrity of the valve but can also cause it to fail unexpectedly. Severe wear on seats, seals, or the ball itself compromises the valve’s ability to control fluid flow, making replacement necessary to maintain safe and efficient operations.
Consistently Poor Performance Under Pressure
If the valve struggles to hold pressure or leaks at high-pressure points, it may no longer be fit for the system. Poor performance under pressure can indicate that the valve’s internal components have worn down beyond repair, and continued use could lead to safety risks or system failures. A replacement valve designed for high-pressure tolerance may provide a more reliable solution.
Choosing a Replacement Valve
When replacing a ball valve, it’s crucial to select a valve that meets the specific requirements of your system. Consider the following factors when choosing a new valve:
Materials Compatibility
Select a valve with materials suited to your system’s fluid type and environmental conditions. For example:
Stainless Steel: Excellent for corrosive environments, high temperatures, and abrasive fluids.
Brass: Commonly used for water and low-pressure applications.
PVC or Plastic: Suitable for lightweight and non-corrosive applications, particularly in low-pressure systems.
Ensure that the materials in the replacement valve can withstand the system’s fluid properties to prevent future corrosion or damage.
Pressure and Temperature Tolerance
Match the replacement valve’s pressure and temperature ratings to the system’s operating conditions. For high-pressure applications, a trunnion-mounted ball valve offers added stability, while high-temperature systems may benefit from metal-seated valves. For low-pressure and standard-temperature settings, a floating ball valve may be sufficient.
Valve Size and Flow Requirements
Choose a valve with the appropriate size and flow capacity. For systems needing minimal pressure drop, a full-port valve provides unrestricted flow, while reduced-port valves are more cost-effective for applications where a slight pressure drop is acceptable.
Maintenance Accessibility
In applications where valves are difficult to access, consider a top-entry ball valve that allows for easier maintenance. For systems with frequent inspection needs, selecting a valve with easily replaceable parts can simplify future repairs.
Conclusion
Simple steps like checking for visible leaks, conducting pressure tests, and inspecting seals can go a long way in maintaining valve integrity. Choosing high-quality valves that suit the specific pressure, temperature, and fluid characteristics of your system also reduces the likelihood of leaks and prolongs the valve’s life.
FAQ
What causes a ball valve to leak?
Common causes include worn stem O-rings, degraded seats and seals, improper installation, and pressure or temperature fluctuations.
Can a leaking ball valve be repaired, or does it need to be replaced?
Minor leaks can often be repaired by replacing seals or seats. However, if leaks persist despite repairs, replacement may be more cost-effective.
How do I fix a stem leak on a ball valve?
Shut off the system, remove the valve handle, replace the worn O-rings or stem seals, and reassemble the valve. Test for leaks after reassembly.
Why is my ball valve leaking even when it’s closed?
This may be due to worn seats or seals that no longer form a tight seal when the valve is closed, allowing fluid to seep through.
How can I prevent ball valve leaks?
Regular inspections, timely replacement of seals, and proper installation help prevent leaks. Also, ensure the valve material is compatible with your system’s pressure and temperature.
When should I replace a leaking ball valve?
If a valve shows signs of persistent leaks, visible corrosion, cracking, or poor performance under pressure, replacement is recommended to avoid further issues.