Hydraulic fittings are integral components in hydraulic systems, serving as connectors that keep systems functioning efficiently under various conditions. The right selection of these fittings is critical for ensuring system reliability, safety, and performance. A poor choice can lead to leaks, system failures, and costly maintenance. The durability and performance of a hydraulic system depend heavily on the material used for its fittings, as different materials offer unique properties that can impact the overall operation and lifespan of the system.
Understanding Hydraulic Fittings
A. Definition and Function of Hydraulic Fittings
Hydraulic fittings are components used in hydraulic systems to connect hoses, pipes, and tubes. They play a vital role in ensuring the smooth and efficient flow of hydraulic fluid under pressure. These fittings are designed to create secure and leak-free connections, allowing for flexibility in system design while also supporting the transfer of fluid power. Their primary function is to maintain a tight seal under various pressure and temperature conditions, ensuring the hydraulic system operates safely and efficiently. Without properly functioning fittings, hydraulic systems could experience leaks, pressure drops, or failures, leading to equipment damage and costly downtime.
B. Types of Hydraulic Fittings
Hydraulic fittings come in various types, each designed to fulfill specific functions within a hydraulic system. The main types include connectors, adapters, and couplings:
Connectors:
Connectors are used to join two pieces of hose, pipe, or tubing, allowing for the extension or redirection of hydraulic lines. They often have threads or a push-to-connect design, which makes installation quick and easy. Connectors ensure a stable and secure bond, preventing fluid leaks and pressure loss. Examples include straight, elbow, and tee connectors, each serving different purposes based on the routing needs of the system.
Adapters:
Adapters are used to change the type of connection or transition between different fitting styles or sizes. They are essential when integrating components with different thread types (e.g., converting metric threads to standard threads). Adapters also help connect dissimilar materials, such as adapting between hoses and rigid pipes, providing flexibility in the system design. They are crucial in custom hydraulic setups where compatibility issues may arise due to varying fitting specifications.
Couplings:
Couplings are designed to join or disconnect hydraulic lines quickly and easily, often without the need for tools. Quick-release couplings, for instance, allow for rapid connection and disconnection of hoses, which is valuable in systems that require frequent reconfiguration or maintenance. This type of fitting is especially useful in mobile hydraulic applications and machinery where quick setup and breakdown are critical. Couplings provide secure and leak-proof connections while maintaining the integrity of the hydraulic system during repeated use.
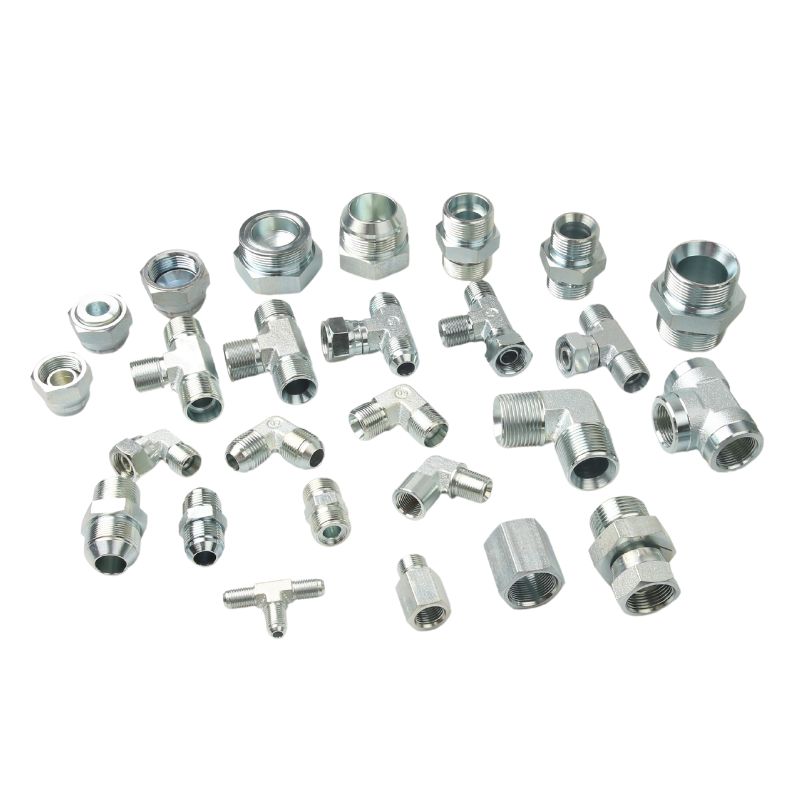
C. Importance of Material Choice in Hydraulic Systems
The choice of material for hydraulic fittings is a critical factor that directly impacts the performance, durability, and safety of a hydraulic system. Different materials offer varying levels of strength, corrosion resistance, and compatibility with hydraulic fluids. The material must be selected based on the operating environment, pressure requirements, and fluid type to prevent degradation and ensure longevity.
Corrosion Resistance: In environments where exposure to moisture, chemicals, or saltwater is common (e.g., marine or chemical processing industries), corrosion-resistant materials like stainless steel are preferred. Using the wrong material in these conditions could lead to rapid wear, leaks, and even system failure.
Strength and Durability: High-pressure systems require materials that can withstand extreme stress without compromising structural integrity. Carbon steel is often used in high-pressure scenarios due to its strength, but stainless steel offers similar strength with the added benefit of corrosion resistance.
Fluid Compatibility: Different hydraulic fluids have varying chemical properties. It’s essential to choose a material that will not react adversely with the fluid used, as incompatible materials can cause contamination, corrosion, or seal failure. Brass, for instance, works well with certain non-corrosive fluids, while stainless steel is more versatile and compatible with a broader range of fluids, including those used in harsh chemical environments.
Stainless Steel Hydraulic Fittings
A. Overview of Stainless Steel as a Material
Stainless steel is an alloy primarily composed of iron, carbon, and a minimum of 10.5% chromium, which provides its characteristic resistance to corrosion. The introduction of chromium forms a protective oxide layer on the surface of the steel, preventing rust and degradation. This unique property makes stainless steel an ideal choice for hydraulic fittings, especially in environments where exposure to moisture, chemicals, and varying temperatures is prevalent.
Stainless steel is also known for its aesthetic appeal, with a shiny, polished finish that is often preferred in visible applications. Its versatility allows for a wide range of forms, from tubing to fittings and valves, making it a favored material in various industrial sectors. The ability to fabricate stainless steel into complex shapes while maintaining its structural integrity adds to its popularity in hydraulic systems.
B. Key Properties of Stainless Steel
Corrosion Resistance: Stainless steel’s most significant advantage is its superior corrosion resistance. The chromium content creates a self-repairing layer of chromium oxide, which protects the underlying metal from environmental factors. This makes stainless steel fittings suitable for use in aggressive environments, including those that involve exposure to chemicals, saltwater, or high humidity. Unlike carbon steel, which can rust and weaken over time, stainless steel maintains its strength and functionality, resulting in lower maintenance costs and increased longevity.
Strength and Durability: Stainless steel is known for its exceptional strength-to-weight ratio. It can withstand high pressures and is less prone to failure under stress compared to many other materials. This strength makes stainless steel fittings ideal for high-pressure hydraulic applications, where safety and reliability are paramount. Additionally, stainless steel exhibits excellent toughness, allowing it to absorb impacts and vibrations without cracking or breaking, which is essential in dynamic operating conditions.
Temperature Resistance: Stainless steel fittings can endure a wide range of temperatures, making them suitable for both high- and low-temperature applications. Certain grades of stainless steel maintain their mechanical properties at elevated temperatures, allowing for reliable performance in environments where thermal stress is a concern. This temperature resistance also extends to cryogenic applications, where maintaining the integrity of hydraulic systems at low temperatures is crucial.
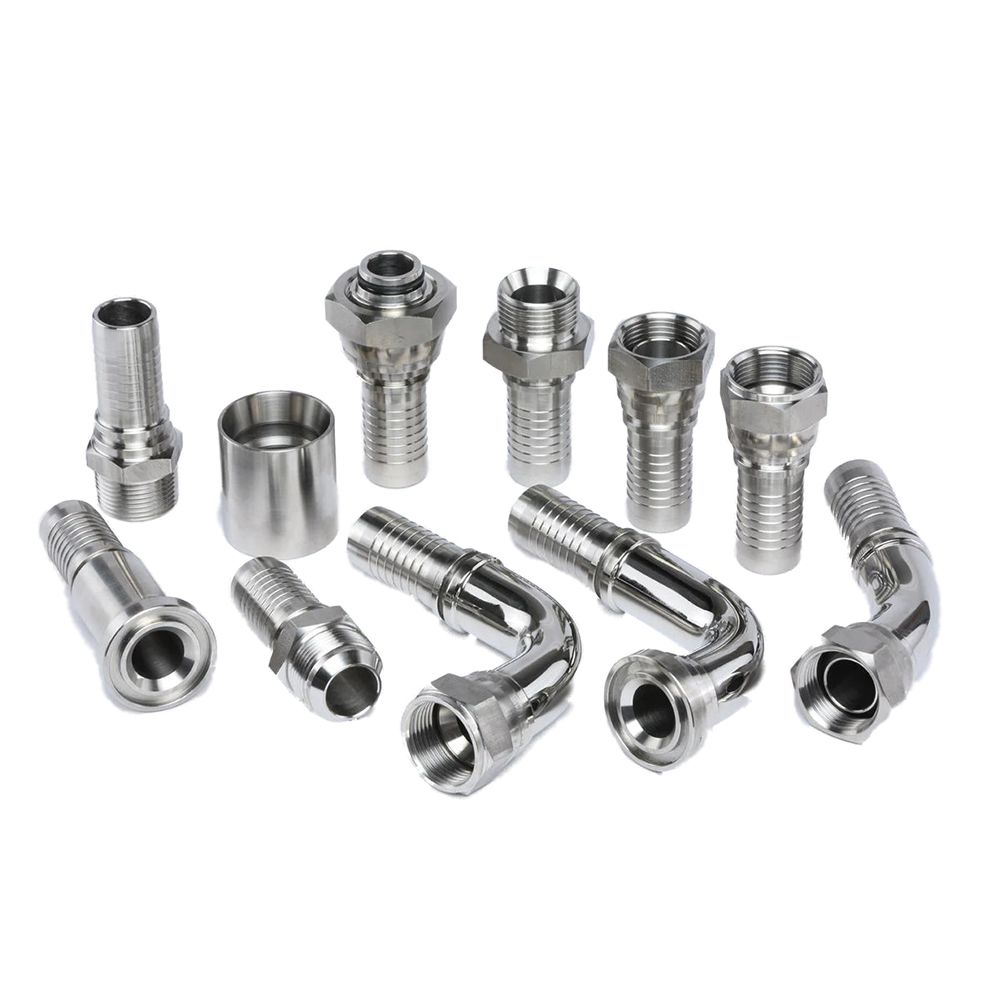
C. Types of Stainless Steel Fittings
304 Stainless Steel: 304 stainless steel is the most commonly used grade for hydraulic fittings due to its balance of corrosion resistance, strength, and cost-effectiveness. It contains approximately 18% chromium and 8% nickel, providing good resistance to oxidation and corrosion in mildly corrosive environments. 304 fittings are ideal for applications that do not involve extreme exposure to chlorides or saline environments.
316 Stainless Steel: 316 stainless steel offers enhanced corrosion resistance compared to 304, primarily due to the addition of molybdenum (around 2-3%). This makes it particularly suited for applications involving salt water, acids, and other aggressive chemicals. 316 fittings are commonly used in marine environments and chemical processing industries, where exposure to harsh conditions is expected. They maintain their strength and integrity, making them a reliable choice for high-performance hydraulic systems.
D. Applications in Various Industries
Chemical Processing: In the chemical processing industry, stainless steel hydraulic fittings are essential due to their resistance to corrosive chemicals and high temperatures. These fittings ensure the safe and efficient transport of fluids in processes such as mixing, heating, and reaction. Their durability reduces the risk of leaks and system failures, which is critical in environments where chemical spills can pose significant risks to health and safety.
Food and Beverage: The food and beverage industry relies on stainless steel fittings to maintain hygiene and prevent contamination. Stainless steel is non-reactive, making it suitable for transporting food and beverages without altering their quality. These fittings are easy to clean and sanitize, ensuring compliance with health and safety regulations. Their corrosion resistance also ensures longevity, reducing the frequency of replacements and maintenance.
Marine Environments: Stainless steel fittings are extensively used in marine applications due to their ability to withstand exposure to saltwater and harsh environmental conditions. The corrosion resistance of 316 stainless steel makes it an ideal choice for shipbuilding, offshore drilling rigs, and underwater equipment. Using stainless steel fittings in these applications helps prevent failures and prolongs the lifespan of hydraulic systems, ensuring reliable operation in challenging maritime conditions.
Comparison with Brass and Carbon Steel Fittings
A. Brass Fittings
1. Properties and Advantages:
Brass is a versatile and widely used material for hydraulic fittings, known for its excellent corrosion resistance, particularly in environments with water exposure. It is an alloy primarily made of copper and zinc, which gives it durability and malleability. Brass fittings are easier to machine and install due to their relatively soft nature, which also makes them suitable for applications where frequent fitting adjustments are needed. Additionally, brass is resistant to rust and offers good thermal and electrical conductivity, making it valuable in hydraulic systems where these properties are beneficial.
2. Limitations:
While brass fittings offer several advantages, they also have limitations. Brass is generally not as strong as stainless steel or carbon steel, which limits its use in high-pressure applications. Its lower tensile strength means it can deform or fail under extreme stress or vibration, making it unsuitable for high-impact environments. Furthermore, brass fittings are not recommended for applications involving corrosive fluids or exposure to saltwater, as these conditions can cause dezincification—a process where zinc is leached out, leading to weakened structural integrity and increased failure risk. Brass fittings are, therefore, best suited for low-pressure, non-corrosive environments.
B. Carbon Steel Fittings
1. Properties and Advantages:
Carbon steel fittings are known for their high strength and durability, making them suitable for demanding applications involving high pressures and temperatures. Carbon steel is composed primarily of iron and carbon, which gives it the toughness needed to handle mechanical stress without deformation. These fittings are often used in industrial and heavy-duty settings where reliability under pressure is critical. Additionally, carbon steel fittings are more affordable compared to stainless steel, providing a cost-effective solution for robust hydraulic systems.
2. Limitations:
Despite its strength, carbon steel has some notable disadvantages. One of the primary limitations is its vulnerability to corrosion, especially in environments with moisture, chemicals, or saltwater exposure. Unlike stainless steel, carbon steel lacks a protective chromium oxide layer, making it prone to rust when exposed to oxygen and water. This limitation often necessitates the use of protective coatings or surface treatments, which add to the maintenance requirements and long-term costs. Carbon steel fittings are also less suitable for environments with extreme temperature fluctuations, as they can become brittle in cold conditions or lose strength at high temperatures.
C. Cost Considerations
Cost is a significant factor when selecting hydraulic fittings, as material choice directly impacts both initial and long-term expenses. Brass fittings are generally affordable and cost-effective for low-pressure and less demanding applications. Their ease of machining and installation further reduces labor costs. However, their lower durability and limitations in high-pressure environments mean they may not be suitable for more complex systems, potentially increasing long-term costs through frequent replacements.
Carbon steel fittings provide a balance between cost and strength, often being less expensive than stainless steel but more robust than brass. This makes them a popular choice in heavy-duty applications where high pressure is involved. However, the added expenses associated with anti-corrosion treatments and ongoing maintenance should be considered when evaluating their overall cost-effectiveness, particularly in corrosive environments.
Stainless steel fittings, while generally more expensive upfront, offer long-term value due to their durability and corrosion resistance. The reduced need for maintenance and the longer lifespan of stainless steel fittings can offset the higher initial investment, especially in applications where environmental exposure and fluid compatibility are critical. In industries where reliability and safety are paramount, stainless steel becomes a cost-effective option despite its higher price tag.
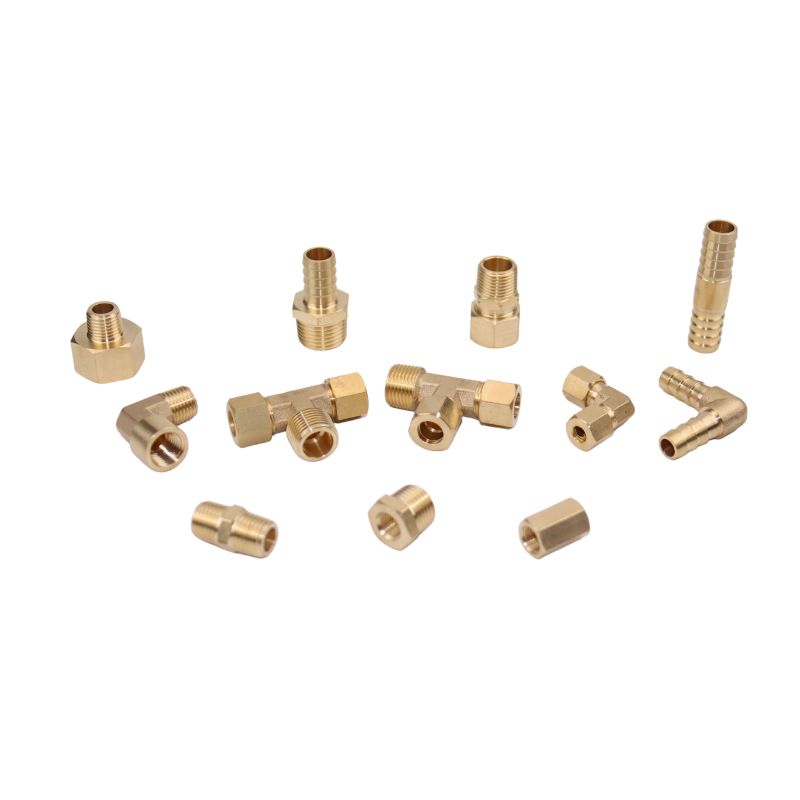
D. Performance in Different Environments
1. Corrosive Environments:
Brass: Brass performs well in moderately corrosive environments, such as those involving freshwater or mild chemicals. However, it is not suitable for highly corrosive environments, such as those with exposure to seawater or acids, as it can suffer from dezincification and corrosion.
Carbon Steel: Carbon steel is not ideal for corrosive environments without protective coatings. If exposed to moisture, chemicals, or saltwater without adequate protection, it will corrode quickly, leading to system failure. In such cases, using carbon steel might increase maintenance requirements and costs.
Stainless Steel: Stainless steel, particularly grades like 316, is highly resistant to corrosion, making it the most suitable option for environments where exposure to harsh chemicals, saltwater, or extreme humidity is expected. Its ability to maintain structural integrity in these conditions significantly reduces the risk of leaks or failures.
2. High-Pressure Systems:
Brass: Brass fittings are not recommended for high-pressure systems due to their lower tensile strength and susceptibility to deformation under extreme pressure. They are better suited for low-pressure applications where the environment is stable.
Carbon Steel: Carbon steel excels in high-pressure applications due to its strength and toughness. It can handle the stress and mechanical forces involved in heavy-duty hydraulic systems, making it a reliable choice in industrial settings where maintaining high pressure is essential.
Stainless Steel: Stainless steel offers similar performance to carbon steel in high-pressure systems but with the added benefit of corrosion resistance. This makes stainless steel fittings the ideal choice for high-pressure systems that also operate in corrosive or harsh environments. They provide both the strength required and the longevity needed to ensure reliable operation.
3. Temperature Variability:
Brass: Brass fittings can handle moderate temperature ranges but are not suitable for extreme fluctuations or very high temperatures. In high-temperature conditions, brass may lose its structural integrity, compromising the safety and reliability of the system.
Carbon Steel: Carbon steel fittings perform well in high-temperature environments but may require specific treatments to enhance their thermal resistance. They can become brittle at low temperatures, limiting their use in systems where temperature variability is significant.
Stainless Steel: Stainless steel’s performance remains stable across a wide range of temperatures, from cryogenic conditions to high heat. Its resistance to both low and high temperatures makes it an excellent choice for hydraulic systems that operate under varying thermal conditions, such as those in the aerospace, marine, or chemical processing industries.
Choosing the Right Fitting for Your Application
Fluid Type
The type of fluid used in a hydraulic system greatly influences the choice of fitting material. Hydraulic systems utilize various fluids such as water-based fluids, synthetic oils, or corrosive chemicals, each with different chemical properties. It is essential to choose a fitting material that is chemically compatible with the fluid to prevent reactions that could lead to corrosion, contamination, or deterioration of the fitting itself.
Water-based Fluids: Stainless steel is often the best choice when using water-based hydraulic fluids due to its excellent resistance to oxidation and corrosion. Brass can also work well in such environments, provided the pressure remains low and the environment is not highly corrosive.
Synthetic Oils: Most metals, including carbon steel, are generally compatible with synthetic oils. However, if there is a risk of exposure to moisture or the presence of other corrosive elements, stainless steel fittings are recommended to provide additional protection and ensure long-term reliability.
Corrosive Chemicals: In systems that transport aggressive chemicals or fluids with corrosive properties (such as acids), 316 stainless steel is often the preferred choice due to its superior resistance to chemical attack. Carbon steel or brass fittings may degrade quickly under such conditions, leading to system failures.
Pressure and Temperature Requirements
The pressure and temperature conditions within a hydraulic system are crucial in determining the appropriate fitting material and type. Different materials perform optimally at varying pressure levels and temperatures, and selecting a fitting that matches these parameters is essential for the safe and efficient operation of the system.
Pressure Requirements:
For high-pressure systems, such as those found in industrial or heavy-duty applications, carbon steel and stainless steel are the best options due to their high tensile strength and durability. Brass fittings are not recommended for high-pressure applications as they may deform or fail under extreme stress.
In low-pressure systems, where the operational environment is less demanding, brass fittings can be suitable and cost-effective, especially if the fluid type and environmental conditions are non-corrosive.
Temperature Requirements:
For systems operating at high temperatures, such as those used in industrial processing or chemical plants, stainless steel fittings are preferred due to their ability to retain structural integrity and resist thermal expansion. Stainless steel’s performance remains stable across a wide temperature range, ensuring system reliability and safety.
In low-temperature or cryogenic applications, stainless steel also excels because it remains ductile and resists brittleness, unlike carbon steel, which can become fragile in extremely cold conditions. This property makes stainless steel fittings an optimal choice for environments with fluctuating or extreme temperatures.
Environmental Conditions
The surrounding environment where the hydraulic system operates plays a significant role in material selection. Environmental factors such as humidity, exposure to chemicals, or saline conditions can affect the longevity and performance of hydraulic fittings.
Corrosive Environments: For applications in environments with high exposure to corrosive elements, such as marine environments or chemical processing facilities, stainless steel fittings, especially 316 grade, provide superior resistance to rust and chemical attack. Carbon steel, while strong, requires additional protective coatings or treatments to withstand such environments, increasing maintenance and costs.
Humid or Moist Conditions: In humid environments or systems exposed to moisture, choosing stainless steel over carbon steel or brass helps ensure the fittings do not corrode over time. Brass can also be used, but it is generally recommended for less critical, low-pressure systems.
Harsh Industrial Settings: In rugged industrial settings where fittings may face mechanical stress, impact, or vibration, carbon steel and stainless steel are appropriate choices due to their robustness. Carbon steel fittings are suitable when corrosion is not a major concern, while stainless steel offers both strength and corrosion resistance, making it ideal for challenging conditions.
Conclusion
As you navigate the selection process for hydraulic fittings, take the time to evaluate your specific operational needs comprehensively. Consider factors such as the type of fluid, operating pressures, temperature ranges, and environmental conditions to ensure you make an informed decision. By making informed choices, you can ensure the longevity and reliability of your hydraulic systems, contributing to greater efficiency and safety in your operations.
FAQ
What is the most corrosion-resistant material for hydraulic fittings?
Stainless steel, particularly 316 grade, offers the highest corrosion resistance, making it ideal for applications involving chemicals, saltwater, or high humidity.
When should I use brass hydraulic fittings?
Brass fittings are best used in low-pressure applications and non-corrosive environments, such as systems involving freshwater or non-reactive fluids.
What is the main advantage of carbon steel fittings?
Carbon steel fittings are highly durable and strong, making them suitable for high-pressure applications and industrial settings where mechanical strength is critical.
Are stainless steel fittings suitable for high-temperature environments?
Yes, stainless steel fittings can withstand a wide range of temperatures, including high temperatures, without losing their structural integrity, making them suitable for both high and low-temperature applications.
How do I choose the right fitting material for my hydraulic system?
Consider factors such as the type of fluid used, operating pressure, temperature requirements, and environmental conditions to select the most compatible and durable material.
Why are stainless steel fittings more expensive than other options?
Stainless steel fittings are more expensive due to their superior properties, including corrosion resistance, durability, and versatility in extreme conditions.