Do AN Fittings Need Sealant?
Introduction
AN fittings are specialized connectors used extensively in hydraulic systems to ensure secure and leak-free connections. These fittings, known for their durability and precision, play a critical role in various industries, including automotive, aerospace, and industrial hydraulics. Proper sealing in hydraulic systems is paramount to prevent leaks, which can lead to system inefficiencies, safety hazards, and costly downtime. This article aims to address a common question among industry professionals: Do AN fittings need sealant?
The Role of Sealant in Hydraulic Fittings
Sealants play a crucial role in hydraulic systems by addressing two primary needs: preventing leaks and enhancing connection strength. Leaks in hydraulic systems can cause significant issues, including loss of pressure, reduced efficiency, potential damage to equipment, and safety hazards. By using sealants, connections are fortified against the risk of leakage, ensuring the system operates smoothly and efficiently. Additionally, sealants can improve the overall strength of the connections, providing extra security in high-pressure environments and preventing fittings from loosening due to vibrations or thermal expansion.
Types of Sealants
There are several types of sealants used in hydraulic systems, each serving specific purposes:
Thread Sealant (Liquid and Tape): Liquid thread sealants are applied directly to the threads before assembly, creating a tight seal as they cure. Teflon tape, a common thread sealant, is wrapped around the threads to fill any gaps and create a seal when the fitting is tightened.
O-rings and Gaskets: These are pre-formed seals made from materials such as rubber, silicone, or metal. They are placed between mating surfaces to prevent leaks. O-rings are commonly used in static and dynamic sealing applications, while gaskets are typically used in static applications.
How Sealants Work
Sealants function through two main mechanisms:
Chemical Bonding: Certain liquid sealants cure through a chemical reaction, forming a solid, durable bond that fills any gaps between threads or surfaces. This chemical bond provides a robust seal that resists pressure, temperature changes, and chemical exposure.
Physical Barrier: Sealants like Teflon tape and O-rings create a physical barrier that blocks the passage of fluids. Teflon tape fills the space between threads, while O-rings and gaskets compress to fill gaps, preventing fluid from escaping.
Do AN Fittings Need Sealant?
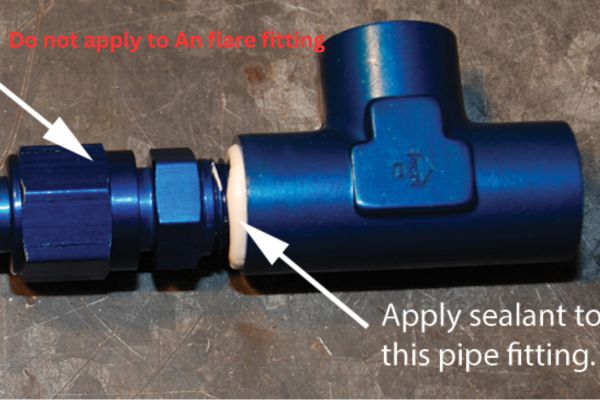
AN fittings are engineered with a unique seal design that typically eliminates the need for additional sealants. The sealing mechanism in AN fittings relies on two main features:
Flare and Cone Interface: AN fittings utilize a 37-degree flare at the end of the tubing that mates with a corresponding cone-shaped seat within the fitting. When tightened, the flare and cone interface creates a secure, leak-proof metal-to-metal seal. This design ensures that the seal is maintained under high pressure without the need for extra sealants.
Metal-to-Metal Seal: The precision-engineered metal surfaces of AN fittings are designed to mate perfectly, forming a tight seal that is both robust and reliable. This metal-to-metal contact eliminates the gaps and spaces that could otherwise lead to leaks, making sealants unnecessary in most cases.
Factors to Consider
Application-Specific Requirements
When deciding whether AN fittings need sealant, it’s crucial to consider the specific requirements of the application, including:
High-Pressure vs. Low-Pressure Systems: In high-pressure hydraulic systems, the integrity of the seal is paramount. AN fittings are designed to handle high pressures without additional sealant, relying on their metal-to-metal seal. In low-pressure systems, the need for sealant might be less critical, but the robust design of AN fittings still generally negates the necessity for sealant.
Temperature Extremes: Hydraulic systems operating under extreme temperatures require reliable seals that can withstand thermal expansion and contraction. AN fittings’ metal-to-metal seals are effective across a wide range of temperatures, making them suitable for use without sealants in both hot and cold environments.
Material Compatibility
The materials used for AN fittings and their compatibility with the hydraulic fluid and the system’s environment are also important factors:
Aluminum, Steel, Stainless Steel AN Fittings: The choice of material for AN fittings can affect their performance in different environments. Aluminum fittings are lightweight and corrosion-resistant, making them ideal for applications where weight is a concern. Steel fittings offer high strength and are suitable for high-pressure applications, while stainless steel fittings provide excellent corrosion resistance in harsh environments.
Chemical Resistance and Reactivity: It’s important to ensure that the material of the AN fittings is compatible with the hydraulic fluid and any other chemicals in the system. Incompatible materials can lead to corrosion, leaks, and system failure. Sealants, if used, should also be compatible with both the fittings and the fluid to avoid chemical reactions that could compromise the seal.
Installation Best Practices
Proper installation techniques are critical to ensuring the reliability of AN fittings without the need for sealants:
Proper Torque Specifications: Applying the correct torque during installation is essential to achieve a secure metal-to-metal seal. Over-tightening or under-tightening can lead to leaks and fitting failure. Manufacturer guidelines should be followed to ensure the correct torque is applied.
Avoiding Over-Tightening: Over-tightening AN fittings can damage the sealing surfaces, compromising the integrity of the metal-to-metal seal. It’s important to follow best practices, such as using a torque wrench and adhering to specified torque values, to avoid over-tightening.
By considering these factors—application-specific requirements, material compatibility, and installation best practices—professionals can ensure that AN fittings perform reliably without the need for additional sealants.
Alternatives to Sealant
Using AN Fittings Without Sealant
AN fittings are designed to provide a reliable seal without the need for additional sealants. Here are some scenarios where the sealant is unnecessary and the associated benefits and potential drawbacks:
Scenarios Where Sealant is Unnecessary:
Standard Hydraulic Systems: In typical hydraulic applications where AN fittings are properly installed and maintained, the metal-to-metal seal provided by the flare and cone interface is usually sufficient to prevent leaks.
High-Pressure Applications: AN fittings are specifically designed to handle high-pressure environments, making them suitable for use without sealant in systems where maintaining pressure integrity is crucial.
Temperature-Variable Environments: The precision engineering of AN fittings ensures that they can maintain a reliable seal even under temperature fluctuations, eliminating the need for additional sealant.
Benefits and Potential Drawbacks
Benefits:
Leak Prevention: The metal-to-metal seal of AN fittings is highly effective at preventing leaks without the need for sealant, reducing maintenance and downtime.
Durability: AN fittings are less likely to degrade or fail over time compared to seals reliant on chemical sealants, which can wear out or become ineffective.
Simplified Maintenance: Without the need for sealant, installation, and maintenance become simpler and cleaner, avoiding the mess and potential for contamination that sealants can cause.
Potential Drawbacks:
Initial Installation Precision: Achieving a leak-free seal with AN fittings requires precise installation. Any damage to the sealing surfaces or improper torque can lead to leaks.
Potential for Misapplication: In some cases, users might mistakenly apply sealant, thinking it will enhance the seal, which can cause issues such as contamination or improper fitting seating.
Ensuring a Proper Seal Without Sealant
To ensure a reliable seal using AN fittings without the need for sealant, it’s important to focus on proper installation practices:
Importance of Clean and Undamaged Threads:
Clean Threads: Before installation, make sure that all threads are clean and free from debris, dirt, or old sealant residue. Contaminants can prevent proper seating of the flare and cone, leading to leaks.
Undamaged Threads: Inspect the threads for any damage, such as nicks, burrs, or deformities. Damaged threads can compromise the integrity of the seal. If threads are damaged, it’s best to replace the fitting or tubing end.
Correct Installation Techniques:
Proper Torque Application: Use a torque wrench to apply the correct amount of torque as specified by the manufacturer. Over-tightening or under-tightening can cause leaks or damage the fitting.
Aligning Fittings Properly: Ensure that the tubing and fitting are properly aligned before tightening. Misalignment can prevent the flare and cone from seating correctly, leading to an incomplete seal.
Avoid Over-Tightening: Over-tightening can deform the sealing surfaces, leading to leaks. Follow manufacturer guidelines and use a torque wrench to avoid this common mistake.
How to Use Sealant for AN Fittings
While AN fittings are designed to create a reliable seal without additional sealants, there are instances where using a sealant might be considered. If you choose to use sealant, it’s crucial to apply it correctly to ensure the integrity of the fitting. Here is a detailed guide on how to use sealant for AN fittings:
Choose the Right Sealant
Thread Sealant: Use a thread sealant that is compatible with the materials of your fittings and the fluids in your system. Liquid thread sealants are often preferred for their ease of use and reliability.
Teflon Tape: If you opt for Teflon tape, make sure it is designed for hydraulic systems and compatible with the materials and fluids used.
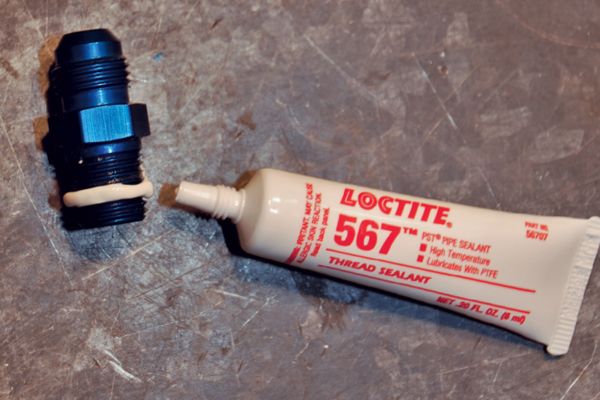
Prepare the Fittings
Clean the Threads: Ensure the threads of both the fitting and the tubing are clean and free from any debris, dirt, or old sealant. Use a brush or cloth to remove any contaminants.
Inspect for Damage: Check the threads for any signs of damage, such as nicks, burrs, or deformities. Damaged threads should be replaced to ensure a proper seal.
Applying Liquid Thread Sealant
Apply Evenly: Apply a small amount of liquid thread sealant to the male threads of the AN fitting. Spread it evenly around the threads, avoiding excess sealant that could contaminate the system.
Avoid the First Thread: Leave the first thread or two free of sealant to ensure that excess sealant does not enter the hydraulic system.
Allow to Cure: Follow the manufacturer’s instructions regarding curing time. Some sealants require a certain amount of time to set before the system can be pressurized.
Applying Teflon Tape
Wrap the Tape: Begin wrapping the Teflon tape around the male threads, starting from the second thread. Wrap in the direction of the threads (usually clockwise) to ensure the tape doesn’t unravel when the fitting is tightened.
Ensure Coverage: Wrap the tape around the threads 2-3 times, ensuring it covers the threads completely but does not create a bulky layer.
Press and Smooth: Press the tape into the threads to smooth it out and ensure it adheres well.
Assembling the Fittings
Align Properly: Align the fitting and the tubing correctly before starting to tighten. Proper alignment is crucial to avoid cross-threading and ensure a good seal.
Tighten to Specification: Use a torque wrench to tighten the fitting to the manufacturer’s specified torque. Over-tightening can damage the fitting and compromise the seal, while under-tightening can lead to leaks.
Check for Leaks: After assembly, pressurize the system and check for leaks. If leaks are detected, re-tighten the fittings slightly and recheck. If leaks persist, disassemble, reapply sealant, and reassemble.
Tips and Best Practices
Follow Manufacturer Instructions: Always follow the sealant manufacturer’s instructions for application and curing. Different products have specific requirements.
Avoid Overuse: Use only the necessary amount of sealant. Excessive use can lead to contamination and other issues.
Regular Inspection: Regularly inspect fittings for signs of leaks or wear. Reapply sealant as needed during routine maintenance.
Avoid These Mistakes When Using Sealant with AN Fittings
While applying sealant to AN fittings can be beneficial in certain situations, it’s crucial to avoid common mistakes that can compromise the integrity of the fitting and the hydraulic system. Here are key mistakes to avoid:
Using Sealant When Not Needed
Unnecessary Application: AN fittings are designed to create a reliable metal-to-metal seal without additional sealants. Applying sealant when it’s not required can lead to contamination and improper sealing.
Manufacturer Guidelines: Always refer to the manufacturer’s recommendations. Many AN fitting producers advise against using sealants on their products.
Over-Tightening the Fittings
Damage to Sealing Surfaces: Over-tightening can deform the sealing surfaces of the flare and cone, leading to leaks and potential fitting failure.
Proper Torque: Use a torque wrench to apply the correct amount of torque as specified by the manufacturer to avoid over-tightening.
Applying Too Much Sealant
Excess Sealant: Using too much liquid sealant or wrapping too many layers of Teflon tape can cause the sealant to squeeze into the hydraulic system, leading to contamination and blockages.
Even Application: Apply a thin, even layer of liquid sealant or 2-3 wraps of Teflon tape to ensure proper sealing without excess material.
Incorrect Sealant Selection
Compatibility Issues: Not all sealants are suitable for use with hydraulic systems or compatible with the materials of the fittings and the hydraulic fluid.
Right Product: Choose a sealant specifically designed for hydraulic systems and ensure it is compatible with the materials and fluids involved.
Not Allowing Sealant to Cure
Premature Pressurization: Some liquid thread sealants require a curing period to form a proper bond. Pressurizing the system before the sealant has cured can result in leaks.
Curing Time: Follow the manufacturer’s instructions regarding the required curing time before pressurizing the system.
Incorrect Tape Wrapping
Wrong Direction: Wrapping Teflon tape in the wrong direction can cause it to unravel when the fitting is tightened.
Proper Technique: Wrap the tape in the direction of the threads (usually clockwise) to ensure it stays in place during assembly.
Conclusion
In summary, AN fittings are meticulously designed to create a reliable metal-to-metal seal, which typically negates the need for additional sealants. However, understanding when and how to use sealant correctly can be beneficial in specific scenarios. Following best practices, such as ensuring clean and undamaged threads, applying the correct torque, and choosing the right sealant, can enhance the reliability and efficiency of hydraulic systems.
FAQ
AN fittings typically do not require sealant because they are designed to create a reliable metal-to-metal seal. However, in some cases, a thread sealant can be used if recommended by the manufacturer.
If sealant is necessary, use a compatible liquid thread sealant or Teflon tape designed for hydraulic systems. Ensure it is suitable for the materials and fluids in your application.
Yes, over-tightening can damage the sealing surfaces, leading to leaks. Always use a torque wrench and follow the manufacturer’s specified torque values to avoid over-tightening.
Check for proper alignment, ensure the threads are clean and undamaged, and verify that the fitting is tightened to the correct torque. If leaks persist, disassemble, clean, and reapply sealant if necessary, then reassemble correctly.
Wrap Teflon tape around the male threads 2-3 times, starting from the second thread, and wrap in the direction of the threads (usually clockwise) to ensure it stays in place during tightening.
Using excessive sealant can lead to contamination and improper sealing. Apply a thin, even layer of liquid sealant or a moderate amount of Teflon tape to achieve a proper seal without excess material.