Compression Fitting vs Solder Fitting: Which Should You Use?
Introduction
When it comes to plumbing and hydraulic systems, the choice of fittings can make a significant difference in the performance and longevity of your installation. Have you ever wondered whether a compression fitting or a solder fitting would be the better option for your project? The right decision could mean the difference between a leak-free, efficient system and one that requires frequent maintenance. In this article, we aim to demystify the debate between compression fittings and solder fittings. By providing a detailed comparison of these two types of fittings, we hope to equip you with the knowledge needed to make an informed decision.
Understanding Solder Fittings
Solder fittings are components used in plumbing and hydraulic systems to join pipes and tubes. The process of soldering involves melting a filler metal (solder) into the joint to create a strong, permanent bond between the metal surfaces. This technique is commonly used in both residential and industrial applications due to its reliability and strength.
Describe the components and materials used:
Solder fittings typically include a fitting body and the solder itself. The fitting body is usually made of copper, brass, or other metals compatible with the soldering process. The solder is a fusible metal alloy, often composed of tin and lead (in older systems) or tin and copper (in modern, lead-free applications). Additional materials used in the soldering process include flux, which is applied to the joint to prevent oxidation and improve the flow of solder, and a heat source, such as a soldering iron or torch, to melt the solder.
Types of Solder Fittings
Soft solder vs hard solder fittings:
Soft solder fittings: These use a lower melting point solder, typically below 450°C (842°F). Soft solder is easier to work with and is commonly used in domestic plumbing for water pipes. The joints created with soft solder are sufficiently strong for most residential applications but are not suitable for high-pressure or high-temperature environments.
Hard solder fittings: These use a higher melting point solder, often above 450°C (842°F). Hard soldering, also known as silver soldering or brazing, creates much stronger joints that can withstand higher pressures and temperatures. This type is often used in industrial applications, HVAC systems, and other settings where durability and strength are critical.
Applications for each type:
Soft solder fittings: Ideal for household plumbing, including potable water systems, and general maintenance tasks where ease of installation and moderate strength are sufficient.
Hard solder fittings: Suitable for high-pressure industrial systems, HVAC applications, and situations requiring superior joint strength and durability.
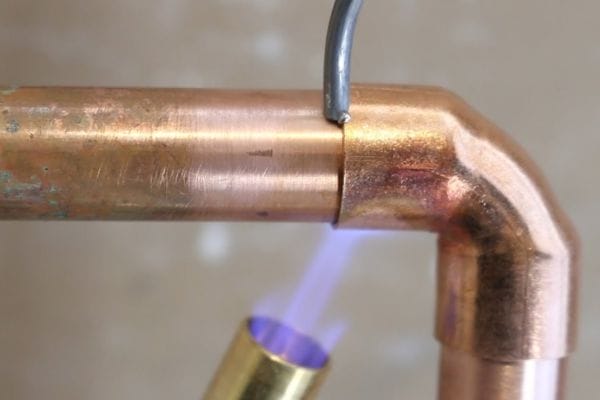
Installation Process
Step-by-step guide on how to install a solder fitting
Preparation:
Clean the pipe ends and fitting with an abrasive cloth to remove any oxidation or debris.
Apply flux to both the outside of the pipe and the inside of the fitting to ensure a clean and strong bond.
Assembling:
Insert the pipe into the fitting, ensuring it is fully seated.
Rotate the fitting slightly to spread the flux evenly.
Heating:
Use a propane torch or soldering iron to evenly heat the fitting and pipe joint.
Heat the joint until the flux begins to bubble and the fitting is hot enough to melt the solder.
Soldering:
Touch the solder to the joint, allowing it to melt and flow into the gap by capillary action.
Continue applying solder until the joint is fully filled and a small bead of solder is visible around the circumference of the joint.
Cooling and Cleaning:
Allow the joint to cool naturally without disturbance.
Wipe away any excess flux with a damp cloth to prevent corrosion.
Advantages of Solder Fittings
Strong and durable joints: Soldered joints are robust and can withstand significant stress and pressure.
Suitable for high-pressure applications: Hard solder fittings, in particular, are ideal for high-pressure environments.
Long-lasting and reliable: Properly soldered joints can last for decades without maintenance, providing long-term reliability.
Disadvantages of Solder Fittings
Requires skill and experience: Soldering is a skilled process that requires practice and precision to achieve strong, leak-free joints.
Time-consuming installation process: Compared to compression fittings, soldering takes more time due to the need for thorough cleaning, flux application, heating, and cooling.
Need for heat, which can pose a safety risk: The use of an open flame or high heat source presents safety risks, including the potential for burns or fire hazards. Proper safety precautions and protective gear are essential.
Comparison of Compression and Solder Fittings
Appearance Characteristics
Compression Fittings:
Compression fittings are composed of three main components: a nut, a ferrule (or ring), and a fitting body. These fittings are typically manufactured from durable materials such as brass or stainless steel, which not only ensures longevity but also provides a robust and sturdy appearance. The nut on the compression fitting features visible threads, which are designed for tightening and securing the connection. Additionally, the surface of the nut may be smooth or knurled to provide a better grip during installation. Compression fittings come in a wide range of sizes and shapes, making them suitable for various pipe dimensions and configurations. The overall look of a compression fitting is quite mechanical, with its polished finish and visible parts, which make it easily identifiable and accessible for maintenance or adjustments.
Solder Fittings:
Solder fittings, on the other hand, consist of the fitting body and the solder material used to join the pipes. These fittings are generally made from copper or brass, known for their excellent conductivity and resistance to corrosion. The appearance of solder fittings is typically smooth and uniform, as the soldering process results in a seamless joint. Solder fittings are available in various sizes to accommodate different pipe diameters, ensuring versatility in their applications. Once installed, a soldered joint is free of visible moving parts, presenting a clean and continuous surface. This seamless appearance not only enhances the aesthetic appeal but also minimizes potential weak points where leaks might occur, providing a sleek and professional finish to any plumbing or hydraulic system.
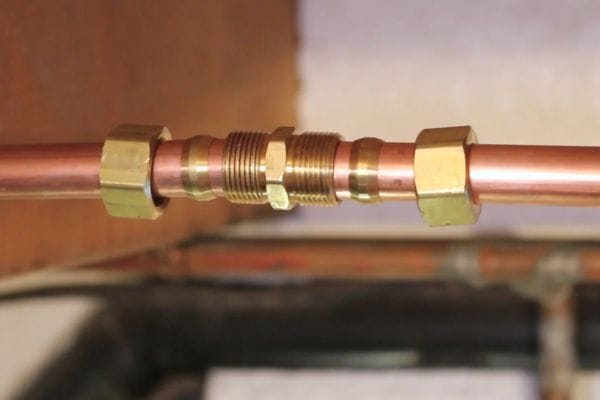
Working Mechanism
Compression Fittings:
Compression fittings create a seal through a straightforward yet effective method. The sealing mechanism involves compressing the ferrule (or ring) between the pipe and the fitting body as the nut is tightened. This compression forces the ferrule to grip the pipe securely, creating a tight, leak-proof seal. The mechanics of this process rely on the precise pressure applied by the nut to compress the ferrule against the pipe surface, ensuring no gaps for leaks. One of the significant advantages of compression fittings is their reusability. They can be easily disassembled and reassembled without damaging the components, allowing for adjustments or repairs.
Solder Fittings:
Solder fittings operate through a different sealing mechanism that involves the application of heat. The joint is sealed by melting solder into the gap between the fitting and the pipe. When heated, the solder flows into the space through capillary action, filling any voids and creating a strong, uniform bond. This process results in a highly durable and permanent connection. The mechanics behind solder fittings ensure that once the solder cools and solidifies, it forms a metallurgical bond that is difficult to disassemble without cutting the pipe. This permanence is advantageous in applications where long-term reliability and strength are crucial, as the soldered joints can withstand significant pressure and stress without leaking or failing.
Applications
Compression Fittings:
Common Uses: Compression fittings are particularly well-suited for scenarios where disassembly and reassembly may be required. They are commonly used in plumbing repairs, as they allow for easy connection and disconnection without the need for soldering or other permanent methods. These fittings are ideal for low to moderate pressure hydraulic systems, providing reliable connections that can be adjusted or replaced as needed.
Flexibility: One of the key advantages of compression fittings is their versatility. They can be used with both metal and plastic pipes, making them a popular choice in residential plumbing and DIY projects. Whether connecting copper pipes in a home water supply system or joining plastic tubing in a garden irrigation setup, compression fittings offer a flexible solution that accommodates various materials and configurations.
Solder Fittings:
Common Uses: Solder fittings excel in applications where a permanent, strong, and durable connection is essential. They are commonly used in high-pressure water supply lines, HVAC systems, and industrial applications where reliability is paramount. The strong bond created by soldering ensures that the joint can withstand significant pressure and stress without leaking or failing.
Durability: Due to their robust nature, solder fittings are preferred in environments where high strength and long-term reliability are critical. They are often found in professional plumbing and industrial settings, where the demand for durable and maintenance-free connections is high. Solder fittings provide a secure and permanent solution, making them ideal for installations that are not expected to be modified or disassembled frequently.
How to Select Between Compression and Solder Fitting
Choosing between compression and solder fittings depends on several factors, including the specific requirements of your project, the materials you’re working with, the environment of the installation, and your level of expertise. Here are some key considerations to help you make an informed decision:
Application Requirements
Compression Fittings:
Flexibility and Adjustability: If your project requires frequent disassembly and reassembly, such as in plumbing repairs or temporary setups, compression fittings are ideal. They allow for easy adjustments and replacements without the need for special tools or skills.
Low to Moderate Pressure Systems: Compression fittings are suitable for low to moderate-pressure systems. If your application falls within this range, compression fittings offer a reliable and convenient solution.
Solder Fittings:
Permanent Installations: For projects requiring permanent, strong, and durable connections, solder fittings are the preferred choice. They provide a robust bond that can withstand high pressure and stress over the long term.
High-Pressure Systems: Solder fittings excel in high-pressure applications, such as water supply lines and industrial systems. If your system needs to handle high pressure, solder fittings offer the necessary strength and reliability.
Material Compatibility
Compression Fittings:
Metal and Plastic Pipes: Compression fittings are versatile and can be used with both metal and plastic pipes. This makes them a popular choice in various residential and DIY projects where different materials might be used.
Solder Fittings:
Metal Pipes Only: Solder fittings are typically used with metal pipes, such as copper and brass. They are not suitable for plastic pipes due to the heat involved in the soldering process.
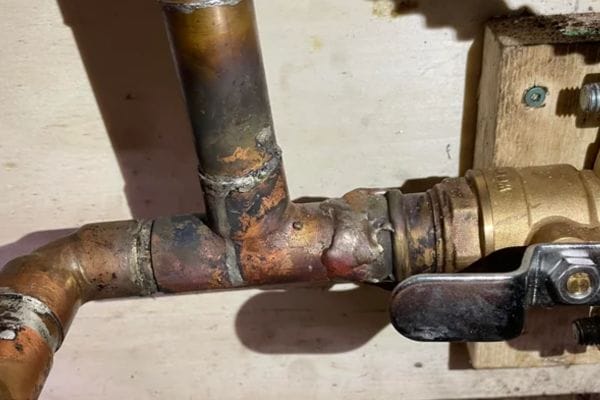
Installation Environment
Compression Fittings:
Ease of Installation: If you’re working in tight spaces or areas where using a torch is impractical or unsafe, compression fittings are easier to install. They require only basic tools, like wrenches, and no special skills or heat.
Safety Considerations: Compression fittings are safer to install in environments where open flames or high heat pose a risk, such as near flammable materials or in confined spaces.
Solder Fittings:
Controlled Environment: If you have a controlled work environment where safety measures can be effectively implemented, solder fittings can be installed with confidence. Ensure proper ventilation and take necessary precautions to handle the heat and potential hazards of soldering.
Cost Considerations
Compression Fittings:
Upfront Costs: Compression fittings may have a higher initial cost due to the components involved (nut, ferrule, fitting body). However, their ease of installation can save on labor costs, especially in DIY projects.
Maintenance Costs: The reusability of compression fittings can reduce long-term maintenance costs, as they can be easily adjusted or replaced without significant expense.
Solder Fittings:
Material Costs: Solder fittings and the necessary materials (solder, flux) are generally affordable. However, the cost of a propane torch or soldering iron should be considered.
Labor Costs: Professional installation of solder fittings can be more expensive due to the skill and time required. However, the durability and longevity of soldered joints can offset these costs over time.
To select the best fitting for your project, assess the specific needs and conditions of your installation. Compression fittings are ideal for flexibility, ease of installation, and low to moderate pressure systems, especially when working with both metal and plastic pipes. Consider the installation environment, your skill level, and cost factors to make an informed decision that ensures the success and reliability of your plumbing or hydraulic system.
Conclusion
To choose the right fitting for your project, consider the specific requirements of your application. Use compression fittings for flexible, low to moderate pressure systems where ease of installation and the ability to make adjustments are important. Opt for solder fittings for permanent, high-pressure installations that demand strong and durable connections. Evaluate the installation environment, your skill level, and cost factors to make an informed decision that ensures the success and reliability of your plumbing or hydraulic system. By understanding the strengths and limitations of each fitting type, you can select the best solution to meet your needs and ensure a reliable, efficient, and long-lasting installation.
FAQ
Compression fittings are commonly used in plumbing repairs, low to moderate pressure hydraulic systems, and DIY projects where disassembly and reassembly may be needed. They are suitable for both metal and plastic pipes.
Solder fittings provide strong, durable, and permanent connections. They are ideal for high-pressure applications, such as water supply lines, HVAC systems, and industrial settings, where reliability and long-term performance are critical.
Yes, one of the main advantages of compression fittings is that they can be easily disassembled and reassembled, making them reusable and adjustable for various applications.
To install solder fittings, you will need a propane torch or soldering iron, flux, solder, and an abrasive cloth. These tools and materials are necessary to clean, heat, and bond the fitting to the pipe.
No, solder fittings are typically used with metal pipes, such as copper or brass. The high heat required for soldering can damage plastic pipes, making solder fittings unsuitable for plastic pipe installations.
Compression fittings are generally easier to install for beginners. They require only basic tools, like wrenches, and no special skills or heat, making them a convenient choice for DIY projects and quick repairs.