Compression Fitting Leaking: Causes and Solutions
Table of Contents
Introduction
Compression fittings are essential components used in various piping and tubing systems to connect two pipes or tubes. These fittings are widely valued for their ability to create a secure, leak-free seal without the need for welding, soldering, or other complex joining methods. This article aims to shed light on the common causes of leaks in compression fittings and provide practical solutions to address these issues. By exploring the typical reasons for leaks and offering actionable solutions, this article will equip you with the knowledge to maintain and troubleshoot your compression fittings effectively.
What are Compression Fittings?
Compression fittings are mechanical components used to connect two pipes or tubes, ensuring a secure and leak-proof joint. They are commonly used in plumbing, gas lines, hydraulic systems, and various other applications requiring a reliable connection. Compression fittings work by compressing a ferrule (a ring or sleeve) onto the pipe or tube as the fitting is tightened. This compression creates a tight seal between the fitting, the ferrule, and the pipe or tube, preventing leaks. The typical compression fitting consists of three parts: the compression nut, the compression ring (ferrule), and the compression seat. When the nut is tightened, it forces the ferrule against the pipe and the fitting body, creating a seal that is both strong and flexible enough to handle slight misalignments and vibrations in the system.
Types of Compression Fittings
Single Ferrule Fittings
Single ferrule fittings, as the name suggests, utilize one ferrule to create the seal. These fittings are simpler in design and easier to install, making them suitable for applications where ease of use is a priority. The single ferrule compresses directly onto the pipe, forming a seal that is typically sufficient for low to moderate-pressure applications. They are commonly used in residential plumbing and low-pressure industrial systems.
Double Ferrule Fittings
Double ferrule fittings use two ferrules to create the seal: a front ferrule and a back ferrule. The front ferrule creates a seal with the fitting body and the pipe, while the back ferrule grips the pipe, ensuring a secure connection. This design provides a more robust and reliable seal, making double ferrule fittings ideal for high-pressure and high-vibration environments. They are often found in hydraulic systems, chemical processing plants, and other demanding industrial applications.
Common Causes of Compression Fitting Leaking
Improper Installation
Incorrect Tightening
One of the most common causes of leaks in compression fittings is improper tightening. If the fitting is not tightened enough, it can lead to insufficient compression of the ferrule, resulting in a weak seal and potential leaks. Conversely, over-tightening can damage the ferrule or deform the pipe, compromising the integrity of the seal. Achieving the correct level of tightness is crucial, typically following the manufacturer’s guidelines to ensure a secure, leak-proof connection.
Misalignment of the Fitting
Another frequent issue is the misalignment of the fitting during installation. If the pipe and fitting are not properly aligned, the ferrule may not seat correctly, leading to an uneven seal. This misalignment can cause leaks even if the fitting is otherwise correctly tightened. Ensuring that the pipe and fitting are perfectly aligned before tightening is essential to prevent this type of leak.
Wear and Tear
Aging of Materials
Over time, the materials used in compression fittings can degrade, especially if they are exposed to harsh conditions. Aging can cause the ferrules to lose their ability to compress effectively, leading to leaks. Regular inspection and timely replacement of old or worn fittings are necessary to maintain a leak-free system.
Exposure to Harsh Environments
Compression fittings that are exposed to extreme temperatures, corrosive substances, or other harsh environmental conditions can deteriorate faster than those in more benign environments. Corrosion, in particular, can weaken the metal components of the fitting, making them prone to leaks. Using fittings made from materials resistant to the specific environmental conditions they will face can help mitigate this issue.
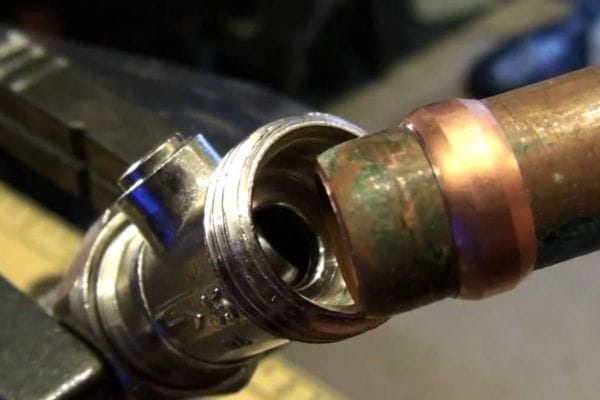
Poor Quality Materials
Substandard Manufacturing
Compression fittings manufactured with substandard materials or poor quality control can be a significant source of leaks. Inferior metals or plastics may not perform as well under pressure, leading to failures in the seal. It is crucial to purchase fittings from reputable manufacturers who adhere to strict quality standards to avoid these problems.
Use of Incompatible Materials
Using fittings made from materials that are incompatible with the pipes or the fluids being transported can also cause leaks. For example, a brass fitting may not be suitable for use with certain chemicals that can cause it to corrode or degrade. Ensuring material compatibility is key to maintaining the integrity of the connection and preventing leaks.
Vibration and Movement
Mechanical Vibrations
In many industrial applications, systems experience significant mechanical vibrations that can loosen compression fittings over time. These vibrations can gradually weaken the seal, leading to leaks. To counteract this, it is important to use fittings designed to withstand vibration or to implement additional support and dampening measures to reduce the impact of vibrations on the fittings.
Frequent Movements Leading to Loosening
Systems that involve frequent movement or adjustments can also cause compression fittings to loosen. Each movement can incrementally reduce the tightness of the fitting, eventually leading to leaks. Regular checks and re-tightening, as needed, can help maintain a secure seal in systems subject to frequent movement.
Incorrect Size or Type
Mismatched Fittings
Using compression fittings that do not match the size or specifications of the pipes they are intended to connect can result in leaks. A fitting that is too large or too small will not create an effective seal. It is essential to ensure that the fittings are the correct size and type for the pipes being used.
Use of Wrong Type for Specific Applications
Different applications may require specific types of compression fittings. Using a fitting designed for low-pressure applications in a high-pressure system, for example, can lead to failure and leaks. Understanding the requirements of your application and selecting the appropriate type of fitting is crucial to prevent leaks and ensure the longevity of the system.
Identifying a Compression Fitting Leak
Visual Inspection
Signs of Leaks
The first step in identifying a compression fitting leak is a thorough visual inspection. Look for visible signs such as moisture, water stains, or residue around the fitting. Even a small amount of liquid can indicate a potential leak. Also, check for any signs of corrosion or rust, which can be a byproduct of leaking fluid.
Areas to Check on the Fitting
Focus your inspection on the key areas where leaks are most likely to occur. These include the junctions where the fitting connects to the pipe and around the compression nut. Pay special attention to any areas where the fitting looks distorted or improperly aligned. The ferrule area should also be scrutinized, as this is where the seal is formed.
Functional Testing
Pressure Testing
Pressure testing is an effective way to detect leaks that are not immediately visible. This involves applying a specified pressure to the system and monitoring it over time. If the pressure drops, it could indicate a leak in the fitting. Pressure gauges can help determine if the system maintains the correct pressure or if there is a slow loss that needs addressing.
Fluid Flow Testing
Another method to identify leaks is fluid flow testing. This involves observing the flow of fluid through the system and checking for any discrepancies. A leak can cause a drop in fluid flow or an unexpected fluctuation. By measuring the flow rate at various points in the system, you can pinpoint the location of a leak.
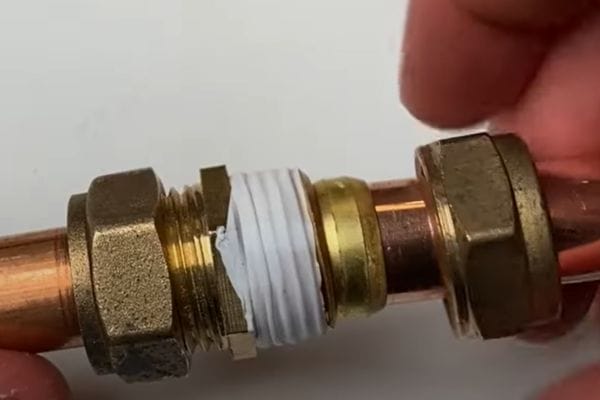
Common Indicators
Drips or Puddles
One of the most obvious indicators of a leak is the presence of drips or puddles around the fitting. Even small drips can accumulate over time, leading to larger puddles and more significant problems. Regularly checking for these signs, especially in areas prone to leaks, can help you catch and fix issues early.
Decreased System Performance
A decrease in system performance can also signal a leak in a compression fitting. This might manifest as reduced pressure in a hydraulic system, lower flow rates in plumbing, or diminished efficiency in a gas line. If you notice that your system is not performing as well as it should, a leak could be the culprit. Identifying and repairing leaks promptly can help restore optimal performance and prevent further damage.
By conducting thorough visual inspections, employing functional testing methods, and being aware of common indicators, you can effectively identify and address leaks in compression fittings. Early detection is crucial for maintaining the integrity and efficiency of your piping systems.
Solutions to Fix Compression Fitting Leaks
Regular Maintenance and Inspection
Scheduled Inspections
Regular inspections are crucial for maintaining the integrity of compression fittings. Schedule periodic checks to look for signs of wear, corrosion, or loosening. This proactive approach helps identify potential issues before they become significant problems.
Preventative Maintenance Practices
Tightening Checks: Regularly check the tightness of the compression fittings, especially in systems subject to vibrations.
Cleaning: Keep the fittings clean and free from debris that could interfere with the seal.
Replacement of Worn Components: Replace any components showing signs of wear or damage to prevent leaks.
Addressing Vibration Issues
Methods to Minimize Vibrations
Secure Mounting: Ensure pipes and fittings are securely mounted to minimize movement.
Use of Flexible Hoses: In areas prone to vibration, consider using flexible hoses to absorb the movement and reduce stress on the fittings.
Vibration Dampening: Install vibration-dampening supports or pads to absorb mechanical vibrations and protect the fittings.
Use of Vibration-Dampening Supports
Vibration-dampening supports can significantly reduce the impact of vibrations on compression fittings. These supports are designed to cushion the pipes and fittings, preventing loosening and leaks. Use them in areas with high mechanical activity or where frequent movements occur.
Material Quality Assurance
Choosing High-Quality Fittings
Investing in high-quality compression fittings is essential for ensuring long-term reliability and performance. Choose fittings from reputable manufacturers known for their stringent quality control and superior materials.
Verification of Material Compatibility
Ensure the materials of the fittings are compatible with the pipes and the fluids being transported. Using incompatible materials can lead to corrosion, degradation, and eventual leaks. Verify compatibility based on industry standards and manufacturer recommendations.
Fixing Wear and Tear
Identify Wear and Tear
Regularly inspect the fittings for signs of wear and tear, such as visible cracks, corrosion, or deformation. Pay attention to the ferrules, nuts, and pipe surfaces where they make contact.
Replace Worn Components
Remove the Old Fitting: Carefully disassemble the fitting by loosening the compression nut and removing the ferrule and pipe from the fitting body.
Inspect the Pipe End: Check the pipe end for any damage. If the pipe is compromised, cut back the damaged section and prepare the new end as described in the installation guide.
Install a New Fitting: Follow the proper installation techniques to install a new compression fitting. Ensure that the replacement fitting is of high quality and compatible with the pipe and fluid being transported.
Use Corrosion-Resistant Materials
In environments where corrosion is a concern, opt for compression fittings made from corrosion-resistant materials such as stainless steel or brass. These materials can withstand harsh conditions better than standard metals, reducing the likelihood of leaks caused by material degradation.
Apply Protective Coatings
Consider using protective coatings or treatments on the fittings and pipes to enhance their resistance to wear and tear. These coatings can provide an additional layer of protection against environmental factors, extending the lifespan of the fittings.
By implementing these solutions, you can effectively address and prevent leaks in compression fittings caused by wear and tear. Proper installation, regular maintenance, quality assurance, vibration management, correct sizing, and addressing wear and tear are all essential components of a leak-free system.
Conclusion
In summary, leaks in compression fittings can arise from several common causes, including improper installation, wear and tear, poor quality materials, vibration, and incorrect sizing or type selection. To address these issues, it is essential to follow proper installation techniques, perform regular maintenance and inspections, ensure material quality, minimize vibrations, and select the correct size and type of fittings. Proper installation and maintenance of compression fittings are crucial for ensuring leak-free and reliable connections in various applications. By adhering to best practices, such as correct tightening, regular inspections, using high-quality materials, and addressing wear and tear, you can prevent common issues that lead to leaks.
FAQ
The most common causes include improper installation, wear and tear, poor quality materials, mechanical vibrations, and using incorrect size or type of fittings.
Ensure the pipes are clean and cut squarely, align the pipes and fittings correctly, and tighten the compression nut according to the manufacturer’s guidelines without over-tightening.
First, check for proper alignment and tightness. If the leak persists, disassemble and inspect the fitting for damage or wear, and replace any compromised components.
Regular inspections should be scheduled based on the system’s operating conditions, but typically, every 6 to 12 months is recommended for most applications.
Stainless steel and brass are commonly used materials that offer good resistance to corrosion and are suitable for most environments.
No, for high-pressure applications, you should use double ferrule fittings which provide a more robust seal. Always ensure the fittings are rated for the specific pressure of your system.