Flanges allow sections of a system to be joined or separated easily, simplifying everything from installation to inspection and routine maintenance. However, not all flanges are created equal. Choosing the wrong type for your application can lead to inefficiencies, unexpected leaks, or even system failure. In this article, we’ll focus on two common flange types: threaded flanges and socket weld flanges. Let’s break down how they work, where they shine, and which one gives you the most reliable seal in real-world conditions.
Overview of Threaded Flanges
Design and Structure
Threaded flanges—sometimes called screwed flanges—are designed with internal threads that allow them to be screwed directly onto pipes with external (male) threads. This mechanical connection eliminates the need for welding, making them a go-to option in systems where welding is not practical or permitted (such as in explosive environments). Most threaded flanges conform to standards like ANSI B16.5 and are commonly used in smaller pipe sizes, typically 2 inches and below.
The key appeal of this design lies in its simplicity. The flange slips over the pipe, the threads engage, and you’ve got a connection. A gasket is typically added between the flange face and the mating component to enhance the seal, especially in liquid systems.
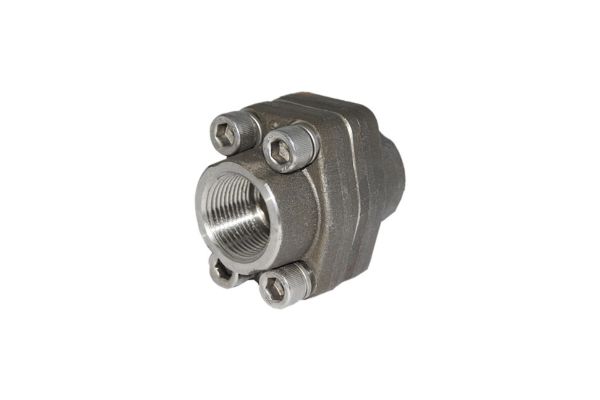
Advantages of Threaded Flanges
- Ease of Installation One of the biggest advantages of threaded flanges is that they require no welding. This means installation can be performed with basic tools and minimal training, making them ideal for on-site repairs, temporary setups, or areas where welding poses a fire risk. You don’t need a hot work permit or a certified welder—just proper torque and threading.
- Convenience for Maintenance Threaded flanges are easy to disassemble, which makes them a favorite for systems that require frequent maintenance, inspection, or replacement of components. You can unscrew and reattach them without damaging the flange or pipe ends—saving both time and cost in maintenance-heavy environments like water treatment facilities, mechanical rooms, or temporary process lines.
Limitations of Threaded Flanges
- Leakage Risk Threaded connections are more prone to leaks than welded connections. If the threads are not cut perfectly—or if the pipe expands or contracts due to temperature changes—small gaps can form, leading to seepage or full-on leaks. Over time, vibration or stress in the system may cause the connection to loosen. That’s why thread sealant or PTFE tape is commonly used, but even that’s not always foolproof in high-pressure applications.
- Pressure and Temperature Constraints Threaded flanges aren’t built for extreme conditions. They’re best suited for low-pressure (typically <300 PSI) and low- to moderate-temperature applications. In high-pressure or high-heat systems, the threads can become a weak point, potentially failing under thermal expansion or pressure surges. For these reasons, they’re often excluded from critical process systems in industries like petrochemical or power generation.
Threaded flanges serve a clear purpose in the flange world: quick, low-pressure, no-weld connections. But when the stakes are high—when pressure and reliability are everything—you may want to explore stronger options like socket weld flanges, which we’ll cover next.
Overview of Socket Weld Flanges
Design and Structure
Socket weld flanges are engineered for strength and stability. Unlike threaded flanges, they do not rely on mechanical engagement. Instead, these flanges have a recessed socket into which the pipe is inserted. Once the pipe bottoms out (with a small gap to allow for expansion), a fillet weld is applied around the outer edge of the pipe, permanently securing it to the flange.
This design creates a smooth inner bore, allowing for uninterrupted fluid flow and reduced turbulence—something especially important in high-velocity systems. Socket weld flanges are commonly used in small-bore piping (typically under 2 inches) and are found in high-pressure hydraulic, steam, and chemical process systems where leaks simply aren’t an option.
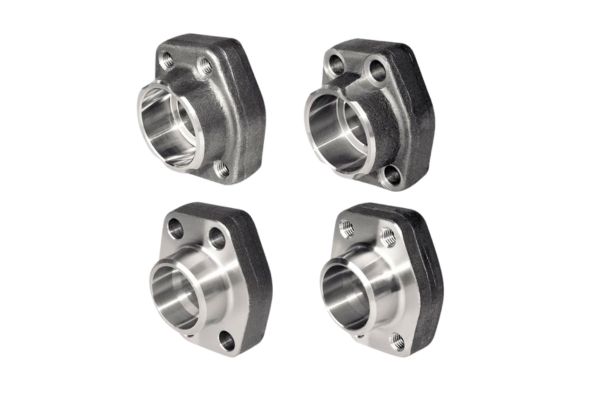
Advantages of Socket Weld Flanges
- Superior Sealing Capability The biggest advantage of socket weld flanges lies in their leak-tight performance. Since the pipe is welded to the flange rather than just threaded in, there are no spiral leak paths. The weld itself acts as a robust seal, preventing even microscopic seepage under high pressure or elevated temperatures. This makes socket welds ideal for critical systems in power plants, oil & gas operations, and industrial manufacturing.
- Enhanced Strength and Durability Socket weld flanges offer a strong, rigid connection capable of withstanding high mechanical stresses. The fillet weld distributes stress evenly around the pipe, minimizing the risk of fatigue failure, vibration damage, or joint loosening over time. This makes them a reliable choice for long-term, high-demand applications, especially where pipe movement or pressure cycling is common.
Limitations of Socket Weld Flanges
- Complex Installation Installing a socket weld flange isn’t plug-and-play. It requires skilled welding, precise alignment, and proper gap allowance between the pipe and socket base (usually around 1/16 inch) to avoid weld cracking under thermal expansion. In most cases, you’ll need a certified welder, proper permits, and safety precautions—especially in environments with flammable materials. This translates to higher upfront labor costs and longer installation times.
- Maintenance Challenges Once a socket weld flange is installed, it’s not coming off easily. These joints are permanent, and any maintenance, system modification, or replacement requires cutting the pipe. This limits flexibility in systems where reconfiguration is common and can lead to increased downtime and maintenance complexity when repairs are needed.
Socket weld flanges are the heavyweight champions when it comes to sealing strength and system integrity, but that strength comes at a cost—higher labor and lower flexibility. They’re best used in permanent, high-pressure systems where safety, performance, and durability outweigh the convenience of easy disassembly. Up next, we’ll directly compare both types so you can decide which one’s the right fit for your setup.
Comparative Analysis: Threaded vs Socket Weld Flanges
Choosing between threaded and socket weld flanges comes down to one thing: what your system needs most—flexibility or sealing strength. Both flange types serve different roles, and neither is universally better than the other. Instead, the “better seal” depends entirely on the environment you’re working in. Let’s compare them head to head:
Sealing Performance
- Threaded Flanges: These rely entirely on the threads and a sealant (like PTFE tape or pipe dope) to keep fluids contained. Over time, with vibration, heat, or system movement, those threads can loosen—resulting in small leaks or even full system failure. Best for: Low-pressure, non-critical systems.
- Socket Weld Flanges: The fillet weld on socket weld flanges creates a much more reliable, leak-resistant connection. Because the pipe is physically welded to the flange, there are no threads or potential pathways for leakage. Best for: High-pressure, high-temperature, or vibration-prone systems.
Installation and Disassembly
- Threaded Flanges: No welding required. You just screw them on—quick, clean, and easy. This makes them perfect for fieldwork, quick repairs, and temporary systems. They’re also easy to remove and reuse. Great for: Speed, convenience, and systems that get opened up often.
- Socket Weld Flanges: Installation requires a skilled welder, proper gap alignment, and post-weld inspection. They’re permanent—cutting is required for disassembly or rework. Great for: Systems where maintenance access isn’t needed regularly.
Durability and Strength
- Threaded Flanges: While simple, they’re not ideal for high-pressure use. Threads can wear or strip, and sealing compounds can degrade over time.
- Socket Weld Flanges: Designed to handle heavy-duty work. The welded connection resists vibration, pressure cycles, and thermal expansion much better than threads can.
Which Flange Offers a Better Seal?
Socket weld flanges typically offer superior sealing performance compared to threaded flanges. Their welded design eliminates the risk of leaks through thread paths, making them a more dependable option for high-pressure systems.
They also hold up better under thermal expansion and mechanical stress, while threaded flanges are more prone to loosening or misalignment over time.
That said, choosing between threaded and socket weld flanges should be based on your system’s needs. If quick installation and the ability to disassemble are important, threaded flanges are the more convenient option. But if a strong, leak-tight connection is critical, socket weld flanges are the better choice.
Factors to Consider When Choosing Between Threaded and Socket Weld Flanges
Selecting the right flange type isn’t just a technical decision—it’s a practical one. The wrong choice can mean costly leaks, downtime, or constant rework. Before you decide between threaded and socket weld flanges, here are the key factors you should seriously weigh:
System Pressure and Temperature
This is priority number one. The operating conditions of your system—specifically pressure and temperature—should dictate your flange choice from the start.
- Threaded Flanges are best for:
- Low-pressure systems, typically under 300 PSI
- Mild temperatures, where thermal expansion is minimal
- Non-critical systems, like water lines or air distribution
- Socket Weld Flanges excel in:
- High-pressure applications, including steam, oil, or hydraulic fluid
- Systems with temperature fluctuations that can stress a threaded joint
- High-vibration environments where a rigid welded connection is safer
If your system exceeds 300 PSI or runs hot, threaded flanges are a risk.
Installation and Maintenance Requirements
Think about who’s installing the system—and how often you’ll need to take it apart.
- Threaded Flanges are perfect when:
- Welding isn’t an option (due to fire risk or site regulations)
- You need quick and easy installation
- The system requires frequent disassembly for inspections, cleaning, or component changes
- Socket Weld Flanges are ideal when:
- You want a permanent, secure connection
- There’s no need to modify the line once installed
- You’re okay with bringing in certified welders and dealing with permits
Threaded = flexibility. Socket weld = permanence.
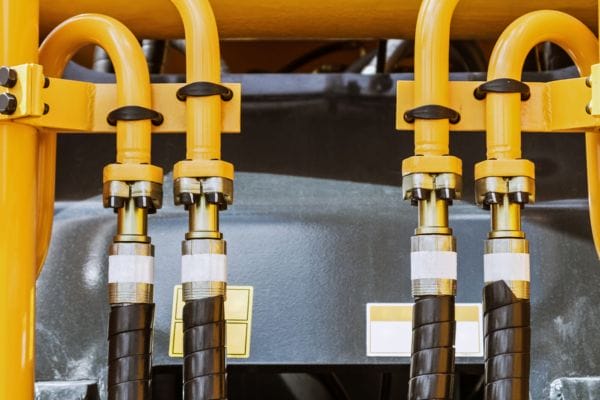
Cost Implications
Cost isn’t just about the flange price tag—it’s about the total project cost including materials, labor, maintenance, and potential downtime.
- Threaded Flanges usually cost less upfront:
- No welding, no special tools
- Less skilled labor required
- Shorter install time = lower labor cost
- Socket Weld Flanges come with higher initial costs:
- Welding labor and inspection
- Longer installation time
- BUT: They reduce leak risk and require less maintenance down the road
For small-scale or temporary jobs, threaded flanges save time and money. For long-term, high-demand systems, socket weld flanges offer better ROI.
Factor | Threaded Flanges | Socket Weld Flanges |
Sealing Performance | Moderate – relies on thread sealant | High – welded joint eliminates leak paths |
Pressure Suitability | Low to moderate pressure | High-pressure systems |
Temperature Resistance | Limited – threads may loosen | Excellent – withstands thermal expansion |
Installation | Easy – no welding required | Requires skilled welding and proper fit-up |
Maintenance Access | Removable and reusable | Permanent – requires cutting for removal |
Durability | May loosen over time | Strong and vibration-resistant |
Labor & Tools Needed | Basic tools, no special permits | Welding equipment and certified labor |
Upfront Cost | Lower installation cost | Higher due to labor and prep |
Best Use Case | Temporary or low-stress piping systems | Critical, high-stress applications |
Quick Tip
Ask yourself:
- Will this system run under pressure or high heat?
- Do I need to access it regularly for maintenance?
- What’s the long-term cost if it leaks or fails?
Conclusion
Choose threaded flanges if you need flexibility, and ease of disassembly, and you’re working with a low-stress, low-pressure system. Choose socket weld flanges when sealing integrity, pressure resistance and long-term durability are top priorities—and you’re okay with a permanent connection. Still weighing your options? Let your system’s pressure rating, maintenance expectations, and installation environment guide your decision.
FAQ
Which flange type offers a better seal?
Socket weld flanges provide a stronger, more leak-resistant seal than threaded flanges.
Are threaded flanges suitable for high-pressure systems?
No, threaded flanges are typically used in low-pressure applications.
Can socket weld flanges be easily removed?
No, they require cutting for removal since they are permanently welded.
Do threaded flanges need welding?
No, they are screwed onto the pipe and require no welding.
When should I use socket weld flanges?
Use them in high-pressure, high-temperature, or vibration-heavy environments.
Are threaded flanges easier to install?
Yes, they can be installed quickly without specialized tools or welding.