Hydraulic fittings are not just simple connectors; they are vital for maintaining the integrity of the hydraulic system, preventing leaks, and ensuring that the system operates at peak efficiency. Incorrect or low-quality fittings can lead to severe consequences, including leaks, pressure drops, or even catastrophic system failures. Such failures not only disrupt operations but can also lead to significant financial losses, costly repairs, and potential safety hazards.
Understanding the Application Requirements
A. Analyzing the Operational Environment
Selecting the right hose fittings begins with a thorough analysis of the operational environment in which they will be used. The environment can significantly impact the performance and longevity of the fittings, making it crucial to consider several key factors.
Temperature:
Importance: Temperature is a critical factor in the selection of hose fittings. Both the ambient temperature (surrounding environment) and the fluid temperature within the hose can affect the material and performance of the fittings. Extreme temperatures can cause materials to expand, contract, or degrade over time.
Considerations:
In high-temperature environments, fittings made from materials like stainless steel or certain high-grade plastics may be necessary due to their heat resistance.
For low-temperature applications, materials that maintain flexibility and strength in cold conditions, such as certain alloys or thermoplastics, should be selected.
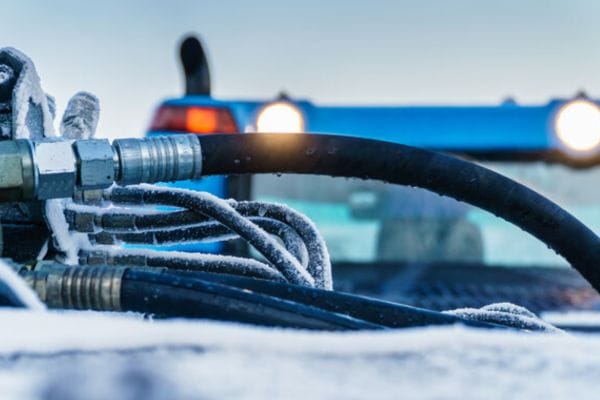
Pressure:
Importance: The pressure within the hydraulic system directly influences the type of fitting required. High-pressure applications demand fittings that can withstand the operational forces without leaking or bursting.
Considerations:
Fittings should be rated for a pressure higher than the maximum expected in the system to ensure safety and longevity.
The design of the fitting, including the wall thickness and thread quality, plays a significant role in pressure tolerance.
Fluid Type:
Importance: The type of hydraulic fluid used in the system can affect the material choice for fittings. Different fluids have varying chemical properties that can interact with fitting materials.
Considerations:
Compatibility between the fluid and fitting material is crucial to prevent chemical reactions that could degrade the fittings or cause leaks.
Common hydraulic fluids include mineral oils, water-glycol solutions, and synthetic fluids, each requiring different material considerations.
B. Determining the Type of Hydraulic Hose Fitting Needed
Once the operational environment has been thoroughly analyzed, the next step is to determine the appropriate type of hydraulic hose fitting for the application. The type of fitting you choose will depend on various factors, including the environment, operational needs, and system requirements.
Overview of Different Types
JIC (Joint Industry Council):
Description: JIC fittings feature a 37-degree flare seating surface, commonly used in fluid power applications.
Applications: Suitable for high-pressure applications and widely used in military, aerospace, and industrial sectors.
Advantages: Offers excellent sealing capabilities and ease of assembly without special tools.
NPT (National Pipe Tapered):
Description: NPT fittings have tapered threads that create a seal through thread deformation.
Applications: Common in general plumbing and hydraulic systems, especially in North America.
Advantages: Simple design and widely available, but may require thread sealant to prevent leaks.
BSP (British Standard Pipe):
Description: BSP fittings are similar to NPT but with a different thread pitch and angle. Available in two types: BSPP (parallel) and BSPT (tapered).
Applications: Widely used in Europe, Asia, and Australia in various hydraulic systems.
Advantages: BSP fittings offer a reliable connection and are commonly used in international applications.
ORFS (O-Ring Face Seal):
Description: ORFS fittings feature a flat face with an O-ring that provides a leak-proof seal.
Applications: Ideal for high-pressure systems where leak prevention is critical, such as in hydraulic machinery and heavy equipment.
Advantages: Excellent leak resistance and suitable for high-vibration environments.
Matching the Fitting Type to the Application
Environment:
Example: In high-vibration environments like heavy machinery, ORFS fittings are often preferred due to their superior sealing capabilities.
Considerations: Assess the operational conditions, such as pressure fluctuations and mechanical stresses, to determine the best fitting type.
Operational Needs:
Example: For applications requiring frequent disassembly and reassembly, such as maintenance operations in industrial plants, JIC fittings may be ideal due to their ease of installation and removal.
Considerations: The fitting type should align with the operational demands, whether that involves withstanding high pressures, accommodating corrosive fluids, or enduring extreme temperatures.
System Compatibility:
Example: In systems where international compatibility is necessary, BSP fittings might be chosen due to their global standardization.
Considerations: Ensure that the selected fitting type is compatible with the existing system components, such as hoses, valves, and other fittings.
Material Compatibility
A. Importance of Material Compatibility
Material compatibility is a critical consideration when selecting hose fittings. The materials used in both the fittings and the hoses must be compatible with each other and with the hydraulic fluid to ensure the system’s longevity and reliability.
How Different Materials React Under Various Conditions:
Chemical Reactions: Some materials may react negatively with certain hydraulic fluids, leading to degradation, corrosion, or even complete failure of the fitting. For example, brass fittings may corrode when used with certain aggressive fluids, while steel fittings could rust in the presence of water-based fluids.
Thermal Expansion: Different materials expand and contract at different rates when exposed to temperature fluctuations. This can cause fittings to loosen or tighten excessively, potentially leading to leaks or system failure.
Pressure Resistance: Materials have varying degrees of strength and elasticity. A fitting made from a material with insufficient pressure resistance may deform or burst under high-pressure conditions.
Impact of Using Incompatible Materials:
Reduced System Performance: Incompatibility can lead to reduced efficiency due to leaks, pressure drops, or blockages caused by material degradation.
Increased Maintenance Costs: Frequent replacements or repairs may be required if materials degrade or corrode quickly, leading to higher maintenance costs.
Safety Hazards: Incompatible materials can cause catastrophic failures, leading to dangerous situations for operators and equipment.
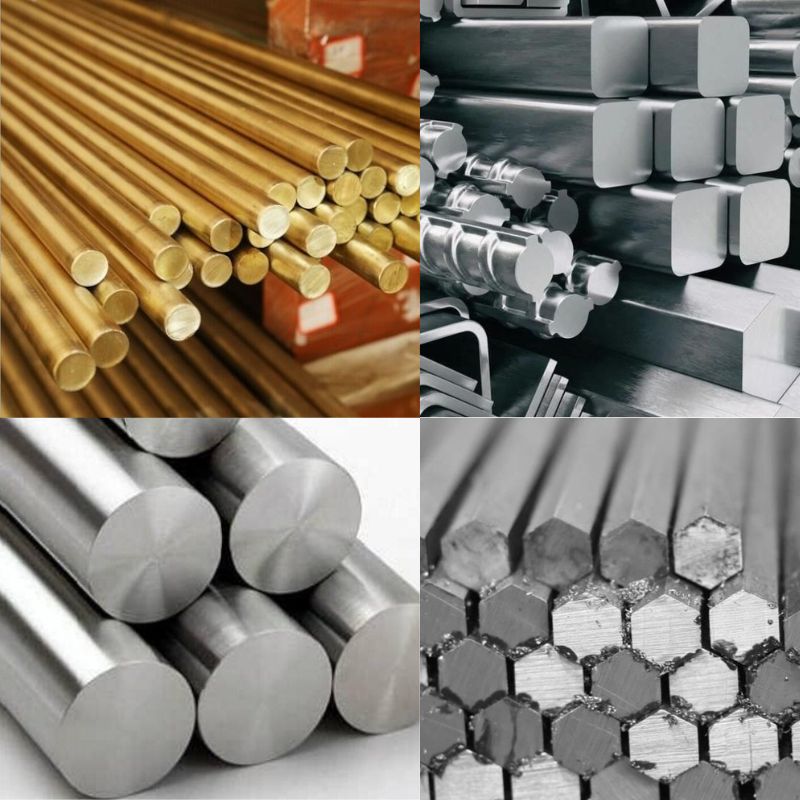
B. Common Materials Used in Hydraulic Fittings
Understanding the properties of common materials used in hydraulic fittings can help in selecting the right one for your application.
Steel:
Typical Applications: Steel fittings are widely used in industrial and heavy-duty applications due to their strength and durability.
Advantages:
High tensile strength makes steel suitable for high-pressure applications.
Versatile and cost-effective.
Disadvantages:
Susceptible to corrosion, especially in the presence of water-based fluids unless coated or treated.
Can be heavy, adding weight to the system.
Stainless Steel:
Typical Applications: Stainless steel fittings are used in corrosive environments, such as marine or chemical processing industries.
Advantages:
Excellent resistance to corrosion and high temperatures.
Suitable for both high-pressure and low-pressure applications.
Disadvantages:
More expensive than regular steel or brass.
Can be difficult to machine, increasing manufacturing costs.
Brass:
Typical Applications: Brass fittings are commonly used in low to medium-pressure systems, particularly in plumbing and water-based applications.
Advantages:
Good corrosion resistance, particularly with water and mild chemicals.
Easy to machine and assemble.
Disadvantages:
Not suitable for high-pressure applications due to lower strength.
Can corrode when exposed to certain fluids, such as ammonia or saltwater.
Aluminum:
Typical Applications: Aluminum fittings are often used in lightweight applications where weight reduction is a priority, such as in the aerospace and automotive industries.
Advantages:
Lightweight and corrosion-resistant.
Good thermal conductivity, which helps dissipate heat in high-temperature applications.
Disadvantages:
Lower strength compared to steel and stainless steel, limiting its use in high-pressure applications.
More susceptible to deformation under stress.
D. Material Compatibility Charts
Material compatibility charts are valuable tools for quickly determining whether a particular fitting material is compatible with the fluid and environmental conditions in your hydraulic system.
Introduction to Compatibility Charts:
Description: Compatibility charts list various materials and fluids, indicating whether they are compatible, partially compatible, or incompatible.
How to Use:
Identify the hydraulic fluid used in your system.
Locate the fluid on the compatibility chart and check its compatibility with different fitting materials.
Choose a material that is fully compatible to avoid any risks of degradation or failure.
Fitting Style and Design
A. Overview of Different Fitting Styles
Crimped Fittings:
Description: Crimped fittings are permanently attached to the hose using a crimping machine, which compresses a metal sleeve around the hose, securing the fitting in place.
Function: These fittings create a strong, leak-proof connection by deforming the metal sleeve to grip the hose tightly.
Applications: Commonly used in high-pressure systems, industrial machinery, and applications where a permanent, durable connection is required.
Reusable Fittings:
Description: Reusable fittings can be disassembled and reattached, making them ideal for situations where hoses need to be replaced frequently or the fitting needs to be reused.
Function: These fittings typically screw onto the hose, creating a secure seal without the need for special tools.
Applications: Suitable for low to medium-pressure systems, maintenance operations, and field repairs where quick and easy hose replacement is necessary.
Push-On Fittings:
Description: Push-on fittings are designed for easy assembly without the need for clamps or crimping tools. The hose is pushed onto a barbed fitting, creating a secure connection.
Function: The barbs on the fitting grip the inside of the hose, preventing it from slipping off under pressure.
Applications: Commonly used in low-pressure systems, such as fuel lines, air hoses, and lubrication systems, where ease of assembly and flexibility are key considerations.
Compression Fittings:
Description: Compression fittings use a compression ring (ferrule) that is compressed against the hose or tubing to create a seal.
Function: The compression ring deforms to create a tight seal around the hose or tubing, ensuring a secure connection.
Applications: Often used in instrumentation and low-pressure hydraulic systems where precise, leak-proof connections are required.
C. Choosing the Right Fitting Style for Your System
Selecting the appropriate fitting style for your hydraulic system involves considering several factors that impact the system’s overall performance and maintenance needs.
Ease of Assembly and Disassembly:
If your system requires frequent hose replacement or maintenance, reusable or push-on fittings might be the best choice due to their ease of assembly and disassembly.
For systems where reliability and permanence are critical, crimped fittings provide the most secure connection.
Maintenance Requirements:
Systems that operate in harsh environments or under high pressures may require fittings that are less likely to need maintenance, such as crimped fittings.
If the system is subject to regular inspection and maintenance, reusable fittings could offer cost savings and convenience.
System Pressure and Application Demands:
High-pressure systems typically demand the strength and security of crimped fittings.
For low-pressure applications, such as fuel lines or air hoses, push-on or compression fittings may be adequate and more cost-effective.
D. Impact of Fitting Design on System Performance
The design of a hydraulic fitting can significantly affect the overall performance of a hydraulic system. Understanding how different designs contribute to system efficiency, safety, and reliability is essential for optimizing performance.
How Fitting Design Affects Performance:
Flow Efficiency: Fittings with smooth internal surfaces and streamlined designs reduce turbulence and pressure drops, improving flow efficiency.
Leak Prevention: Fittings designed with precise sealing mechanisms, such as O-rings in ORFS fittings, help prevent leaks and maintain system pressure.
Durability: The durability of a fitting is influenced by its design features, such as reinforced walls or corrosion-resistant coatings, which help extend the lifespan of the fitting in challenging environments.
Ensuring Proper Assembly and Installation
A. Importance of Proper Assembly
Proper assembly and installation of hose fittings are crucial for the reliability and safety of a hydraulic system. Improper assembly can lead to several issues, including leaks, pressure drops, and even catastrophic system failures.
How Improper Assembly Can Lead to System Failure:
Leaks: Improperly assembled fittings may not form a secure seal, leading to fluid leaks. Even small leaks can result in significant pressure loss, reduced system efficiency, and potential environmental hazards.
Pressure Drops: If fittings are not installed correctly, they can create points of turbulence or resistance within the system, causing pressure drops that can impair the performance of hydraulic actuators and other components.
System Failures: In severe cases, improper assembly can lead to complete system failure, such as hoses detaching under pressure or fittings bursting, which can pose safety risks to operators and damage equipment.
The Role of Torque and Alignment in Fitting Installation:
Torque: Applying the correct amount of torque during fitting installation is essential to ensure a secure and leak-free connection. Under-tightening can result in leaks, while over-tightening can damage the fitting or hose, compromising the integrity of the connection.
Alignment: Proper alignment of fittings is equally important. Misalignment can lead to uneven stress distribution, causing premature wear, leaks, or fitting failure. Ensuring that hoses and fittings are aligned correctly during installation will help maintain system reliability and extend the life of the components.
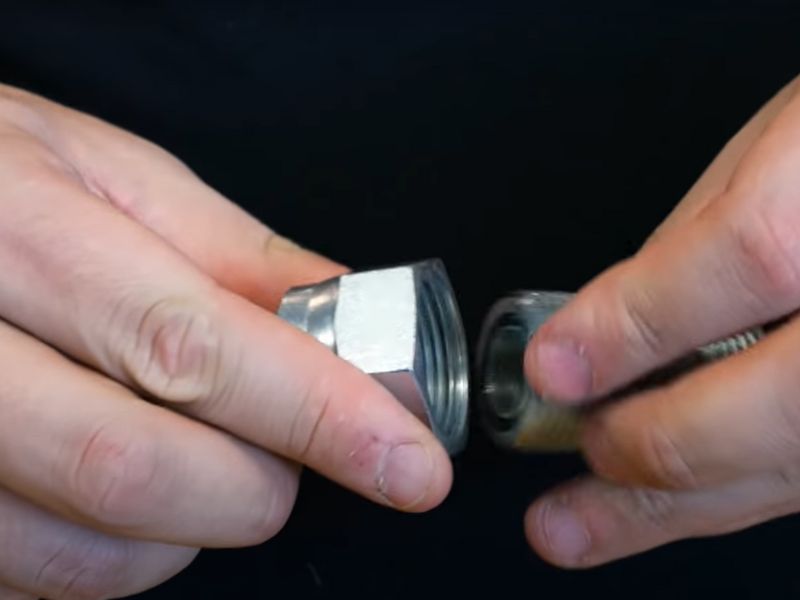
B. Step-by-Step Guide to Proper Installation
A systematic approach to installing hose fittings can prevent many common issues and ensure a secure, reliable connection.
Step 1: Prepare the Hose and Fitting
Cut the hose to the correct length using a sharp hose cutting tool to ensure a clean, straight cut. Avoid using tools that could crush or fray the hose.
Inspect the hose ends for any debris or irregularities and clean them if necessary.
Tools Required: Hose cutting tool, clean rags, and possibly a vice for holding the hose steady.
Step 2: Insert the Fitting
For crimped fittings, insert the hose into the fitting until it bottoms out against the internal stop. Ensure that the hose is seated correctly and is fully engaged with the fitting.
For push-on or reusable fittings, insert the hose over the fitting’s barb or threads, applying consistent pressure until it is fully seated.
Tools Required: For reusable fittings, a wrench may be required. For crimped fittings, a crimping machine is necessary.
Step 3: Crimping or Securing the Fitting
If using crimped fittings, place the fitting into the crimping machine according to the manufacturer’s instructions. Ensure the fitting is aligned correctly in the machine, then apply the crimp.
For reusable fittings, tighten the fitting using a wrench, ensuring it is securely fastened without over-tightening.
Tools Required: Crimping machine for crimped fittings, wrench for reusable fittings.
Step 4: Inspect the Assembly
Check the fitting for any visible gaps, misalignments, or deformities. Ensure that the hose is properly seated and that the fitting is securely attached.
Tools Required: Visual inspection, calipers or gauges to check fitting dimensions if needed.
C. Common Installation Mistakes to Avoid
Avoiding common mistakes during the installation process can help ensure a leak-free and secure hydraulic system.
Under-Tightening or Over-Tightening:
Overview: Under-tightening can cause leaks, while over-tightening can damage the fitting, hose, or threads, leading to premature failure.
Tips: Always use a torque wrench to apply the correct torque specified by the fitting manufacturer. Avoid using excessive force, which can strip threads or distort the fitting.
Improper Hose Length:
Overview: Using a hose that is too short or too long can cause stress on the fittings and lead to failures due to stretching, bending, or kinking.
Tips: Measure and cut the hose to the correct length, accounting for any movement or flexibility needed in the system. Ensure there is adequate slack to prevent strain on the fittings.
Incorrect Fitting Selection:
Overview: Choosing the wrong fitting type or material for the application can lead to compatibility issues, corrosion, or inadequate pressure handling.
Tips: Verify that the selected fitting matches the system’s requirements, including pressure ratings, material compatibility, and environmental factors.
Ignoring Alignment:
Overview: Misaligned fittings can create stress points that lead to leaks or premature wear.
Tips: Ensure that hoses and fittings are aligned correctly during installation. Use alignment tools or guides if necessary to achieve proper alignment.
Conclusion
In conclusion, choosing the right hose fittings involves careful consideration of four key factors: understanding the specific application requirements, ensuring material compatibility, selecting the appropriate fitting style, and following proper assembly and installation procedures. Each of these elements is crucial for optimizing system performance and preventing costly failures. For specialized or challenging applications, it’s important to pay extra attention to these factors and, when in doubt, consult with Topa.
FAQ
What are the most common types of hose fittings?
The most common types include JIC, NPT, BSP, ORFS, and SAE fittings, each designed for specific applications and pressure requirements.
How do I choose the right material for my hydraulic fittings?
Select the material based on the fluid type, operating pressure, and environmental conditions. Common materials include steel, stainless steel, brass, and aluminum.
Why is the proper assembly of hydraulic fittings important?
Proper assembly ensures a leak-free, secure connection that prevents system failures and maintains optimal performance.
Can I reuse hydraulic hose fittings?
Reusable fittings can be disassembled and reattached, making them ideal for maintenance and repair, but not all fitting types are reusable.
What should I do if my hydraulic fitting is leaking?
Check for proper torque and alignment, inspect for damage or wear, and consider replacing the fitting if the issue persists.
How often should I inspect my hydraulic fittings?
Regular inspections should be part of your maintenance routine, ideally every few months, to catch any signs of wear or damage early.