In the intricate world of fluid control systems, small hydraulic ball valves stand as unsung heroes, silently regulating the flow of liquids with remarkable precision. These compact yet powerful components play a critical role in various hydraulic applications, where their reliability directly impacts system efficiency and operational safety. However, like any mechanical device, their performance and lifespan depend significantly on proper maintenance practices.
Understanding Small Hydraulic Ball Valves
Basic Structure and Components
Hydraulic ball valves operate on a simple yet effective principle. At their core is a spherical ball with a hole (port) through its center, positioned within the valve body. When the valve handle is aligned with the flow path, the hole in the ball allows fluid to pass through. Rotating the handle 90 degrees turns the ball so that the solid portion blocks the flow path, effectively shutting off the fluid.
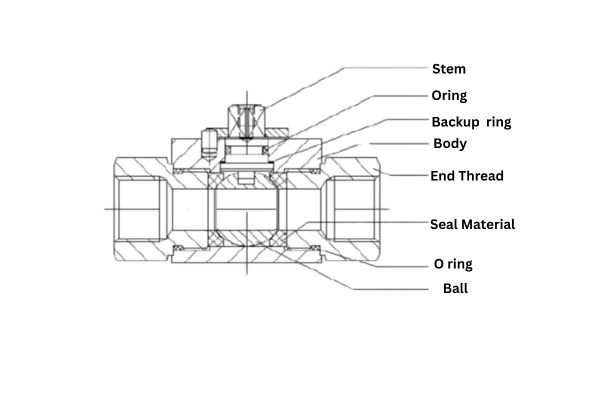
The main components of a small hydraulic ball valve include:
- Valve Body: Typically made of brass, stainless steel, or other corrosion-resistant metals, the body houses all internal components and connects to the hydraulic system.
- Ball: The spherical component with a bore that controls fluid flow. In small hydraulic applications, this is usually precision-machined from stainless steel or chrome-plated brass for durability and smooth operation.
- Valve Seats: These create a seal between the ball and the valve body, preventing leakage when the valve is closed. They’re commonly made from PTFE (Teflon), PEEK, or other engineered polymers that provide excellent sealing properties while minimizing friction.
- Stem: Connects the ball to the external handle, transferring the rotational movement that opens or closes the valve.
- Stem Seals: Prevent fluid leakage around the stem, typically using O-rings or packing materials.
- Handle: Usually designed as a lever for manual operation, providing visual indication of valve position (open or closed).
- End Connections: May feature threaded connections, compression fittings, or flanged ends depending on the application requirements.
Types of Small Hydraulic Ball Valves
Small hydraulic systems typically utilize several types of ball valves:
- Two-Way Ball Valves: The most common type, allowing flow in a straight line when open and blocking flow when closed.
- Three-Way Ball Valves: Feature an L-shaped or T-shaped bore, enabling flow diversion between two outlet ports.
- Full-Port (Full-Bore) Ball Valves: The bore diameter matches the pipe diameter, minimizing flow restriction and pressure drop.
- Reduced-Port Ball Valves: Have a smaller bore diameter than the connecting pipe, offering more control but with higher pressure drop.
- Floating Ball Valves: The ball is suspended and “floats” between two seats, pushed against the downstream seat by pressure.
- Trunnion-Mounted Ball Valves: The ball is supported by a trunnion at the top and bottom, reducing friction and wear during operation.
For small hydraulic applications, floating ball designs are most common due to their simplicity, reliability, and cost-effectiveness.
The Importance of Regular Maintenance
Proper maintenance of small hydraulic ball valves is not merely a recommendation—it’s a necessity for several compelling reasons:
- Extended Service Life: Regular maintenance can significantly extend the operational lifespan of ball valves, delaying the need for costly replacements.
- Improved System Reliability: Well-maintained valves operate more predictably, reducing the risk of unexpected failures during critical operations.
- Enhanced Safety: Properly functioning valves help prevent dangerous situations such as sudden pressure releases or hydraulic fluid leaks.
- Optimized Performance: Clean, well-lubricated valves operate more efficiently, maintaining proper flow rates and pressure control.
- Reduced Operational Costs: Preventive maintenance is invariably less expensive than emergency repairs or premature replacements.
- Minimized Downtime: Scheduled maintenance can be planned during non-critical periods, avoiding unexpected system shutdowns.
The cost of neglecting ball valve maintenance can be substantial, potentially leading to complete system failures, safety hazards, and significant production losses. Investing time and resources in preventive maintenance represents a small price compared to these potential consequences.
Preventive Maintenance Best Practices
1. Regular Inspection Routines
Implementing a systematic inspection schedule is the foundation of effective ball valve maintenance. For small hydraulic ball valves, consider the following inspection frequencies:
- Daily Visual Checks: Quick visual inspections for obvious leaks, unusual noises, or vibrations.
- Monthly Detailed Inspections: More thorough examinations of valve operation, sealing, and external condition.
- Quarterly Comprehensive Assessments: Complete operational testing and detailed inspection of all accessible components.
During these inspections, pay particular attention to:
- Leakage: Check for fluid seepage around the stem, body joints, and end connections.
- Operation Smoothness: Verify that the valve opens and closes smoothly without excessive force.
- Handle Condition: Ensure the handle is securely attached and properly indicates valve position.
- External Corrosion: Look for signs of corrosion or damage to the valve body and connections.
- Mounting Security: Confirm that the valve is securely mounted and properly aligned with connected piping.
Document all findings in a maintenance log, noting any changes from previous inspections. This historical record can help identify developing issues before they become critical failures.
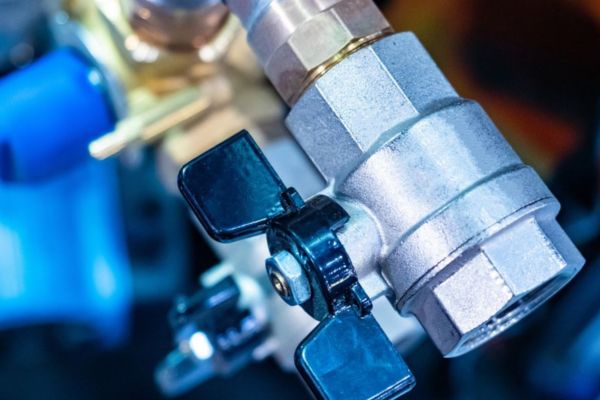
2. Proper Cleaning Procedures
Contamination is a primary enemy of hydraulic systems, and ball valves are particularly vulnerable to performance degradation from dirt and debris. Follow these cleaning guidelines:
- External Cleaning:
- Wipe down the valve exterior with a clean, lint-free cloth.
- Remove any accumulated dirt, especially around the stem area.
- For stubborn deposits, use a soft brush and appropriate cleaning solution compatible with the valve material.
- Internal Cleaning (during scheduled maintenance):
- Isolate and depressurize the valve before disassembly.
- Carefully disassemble according to manufacturer guidelines.
- Clean all components with appropriate solvents or cleaning agents.
- Pay special attention to the ball surface and seats.
- Inspect for wear or damage during cleaning.
- Ensure all parts are completely dry before reassembly.
For small hydraulic ball valves, cleaning frequency depends on operating conditions:
- Clean environments: Annual internal cleaning may be sufficient.
- Dirty or harsh environments: Consider quarterly or even monthly cleaning.
3. Lubrication Essentials
Proper lubrication is critical for smooth operation and longevity of small hydraulic ball valves. Follow these lubrication guidelines:
- Lubricant Selection:
- Use only lubricants specifically recommended for hydraulic applications.
- Select water-insoluble, synthetic, or oil-based lubricants appropriate for the valve material and operating conditions.
- Never use solid or clay-based lubricants that can accumulate in the valve cavity.
- Consider temperature range, pressure requirements, and compatibility with the hydraulic fluid.
- Lubrication Points:
- Focus on the stem and stem seals where friction occurs.
- Apply lubricant to ball surfaces if recommended by the manufacturer.
- Ensure even distribution without excess that might contaminate the hydraulic fluid.
- Lubrication Frequency:
- Follow manufacturer recommendations for lubrication intervals.
- Increase frequency for valves in high-cycle applications.
- Some modern ball valves come pre-lubricated and may not require additional lubrication during their service life.
Remember that over-lubrication can be as problematic as under-lubrication, potentially attracting contaminants or interfering with valve operation.
4. Proper Operation Practices
How a ball valve is operated significantly impacts its longevity. Train operators and maintenance personnel on these best practices:
- Smooth Operation: Open and close valves slowly and steadily to prevent pressure spikes and water hammer effects.
- Complete Positioning: Always fully open or fully close ball valves—partial positioning can cause uneven wear on seats and reduce sealing effectiveness.
- Regular Exercise: Periodically operate valves that remain in one position for extended periods to prevent sticking and ensure continued functionality.
- Avoid Forcing: Never force a valve that doesn’t move freely—investigate the cause instead.
- Position Indication: Maintain clear visual indicators of valve position to prevent accidental operation.
- Thermal Considerations: Allow for thermal expansion and contraction in extreme temperature applications.
By following these operation guidelines, you can significantly reduce wear and extend the service life of small hydraulic ball valves.
Comprehensive Maintenance Schedule
Implementing a structured maintenance schedule ensures no critical maintenance tasks are overlooked. Here’s a recommended maintenance timeline specifically for small hydraulic ball valves:
Daily Maintenance Tasks
- Check oil levels in hydraulic power units.
- Monitor for temperature changes in the hydraulic fluid.
- Inspect for visible leaks around valve connections and stem.
- Listen for unusual noises during valve operation.
- Verify pressure gauge readings are within normal ranges.
- Wipe clean any fluid accumulation around valves.
Monthly Maintenance Tasks
- Test valve operation through complete open-close cycles.
- Check and tighten any loose connections.
- Inspect valve handles for secure attachment.
- Clean external surfaces thoroughly.
- Check for signs of corrosion or external damage.
- Verify proper alignment with connected piping.
Quarterly Maintenance Tasks
- Conduct more detailed leak testing.
- Check tightness of bolts, nuts, and other hardware.
- Inspect for mineral buildup or corrosion.
- Verify correct operation of ball valves during opening and closing.
- Check accuracy of position indicators.
- Ensure adequate area ventilation and air filtration.
Semi-Annual Maintenance Tasks
- Lubricate valve stems and other moving parts as recommended.
- Check for wear on seals and seats if accessible.
- Conduct pressure testing where appropriate.
- Inspect for internal contamination if possible without disassembly.
- Review maintenance logs for recurring issues.
Annual Maintenance Tasks
- Schedule planned downtime for thorough inspection.
- Remove valves from the system where practical.
- Disassemble and clean internals according to manufacturer guidelines.
- Replace worn components, with special attention to seals and rubber parts.
- Conduct comprehensive pressure testing after reassembly.
- Update maintenance records with all findings and actions taken.
This schedule should be adjusted based on:
- Manufacturer recommendations
- Operating conditions (temperature, pressure, cycling frequency)
- Criticality of the application
- Historical performance and maintenance findings
For high-pressure or high-cycle applications, consider increasing the frequency of inspections and maintenance activities.
Troubleshooting Common Ball Valve Issues
Even with diligent maintenance, ball valves may occasionally develop problems. Here’s how to identify and address the most common issues:
1. Valve Won’t Shut Off Completely
Possible Causes:
- Debris trapped between the ball and seat
- Worn or damaged seats
- Ball surface damage
- Misalignment of valve components
Solutions:
- Isolate the valve and release pressure
- Cycle the valve several times to dislodge debris
- If unsuccessful, disassemble and clean internal components
- Replace seats or the entire valve if damage is evident
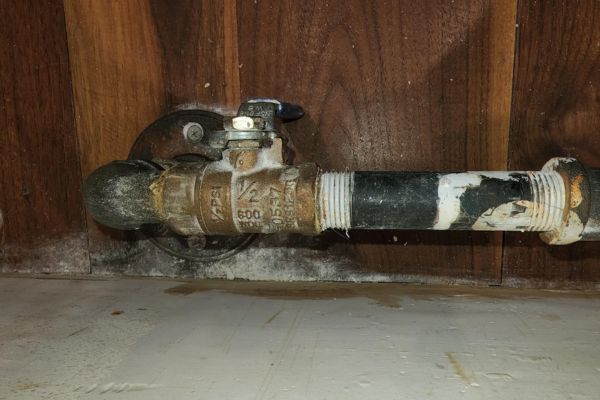
2. Difficult Operation (Stuck or Hard to Turn)
Possible Causes:
- Lack of lubrication
- Corrosion or scale buildup
- Thermal expansion/contraction
- Excessive system pressure
- Damaged stem or internal components
Solutions:
- For minor sticking, try cycling the valve several times
- Apply appropriate lubricant to the stem
- If accessible, clean and lubricate internal components
- For severe cases, isolate, depressurize, and service the valve
- Replace damaged components or the entire valve if necessary
3. Stem Leakage
Possible Causes:
- Worn or damaged stem seals
- Loose packing nut
- Stem damage
- Improper assembly after maintenance
Solutions:
- Tighten the packing nut slightly (avoid over-tightening)
- Replace stem seals or packing
- Check for stem damage and replace if necessary
- Verify proper assembly sequence
4. Body Leakage
Possible Causes:
- Loose body bolts
- Damaged body seal
- Cracked valve body
- Excessive pressure or temperature
Solutions:
- Tighten body bolts to specified torque
- Replace body seals
- For cracked bodies, replace the entire valve
- Verify operating conditions are within valve specifications
5. Inconsistent Flow Control
Possible Causes:
- Partial blockage within the valve
- Damaged ball or seats
- Improper valve sizing for the application
- System pressure fluctuations
Solutions:
- Clean internal components to remove blockages
- Replace damaged components
- Verify valve is properly sized for the application
- Check system pressure regulation
6. Unusual Noises
Possible Causes:
- Cavitation due to pressure drops
- Loose components
- Flow turbulence
- Worn bearings or supports
Solutions:
- Check for appropriate pressure conditions
- Tighten all fasteners and connections
- Verify proper installation orientation
- Replace worn internal components
When troubleshooting, always start with the simplest potential solutions before progressing to more complex interventions. Document all troubleshooting steps and outcomes to build a knowledge base for future reference.
Advanced Maintenance Considerations
Material Compatibility
Small hydraulic ball valves interact with both the hydraulic fluid and the external environment. Consider these material compatibility factors:
- Hydraulic Fluid Compatibility: Ensure valve materials (especially seals) are compatible with the specific hydraulic fluid in use. Incompatibilities can cause swelling, deterioration, or failure of seals.
- Environmental Compatibility: Consider exposure to:
- Chemicals or corrosive atmospheres
- UV radiation
- Temperature extremes
- Humidity or moisture
- Abrasive particulates
- Pressure and Temperature Ratings: Verify that valve materials maintain their integrity throughout the full range of operating conditions.
For specialized applications, consult with valve manufacturers regarding material selection for optimal compatibility and longevity.
Storage and Handling
Proper storage of spare ball valves and components is essential for maintaining their integrity:
- Storage Environment:
- Store in a cool, dry place away from direct sunlight.
- Maintain temperature between 0°C (32°F) and 49°C (120°F).
- Protect from dust, dirt, and other contaminants.
- Keep away from chemicals that might damage valve materials.
- Handling Precautions:
- Keep protective caps or covers in place until installation.
- Avoid dropping or impacting valves.
- Handle by the body, not by handles or stems.
- Keep threaded ends and sealing surfaces protected.
- Prevent entry of foreign materials into valve openings.
- Long-Term Storage:
- Apply appropriate preservatives to prevent corrosion.
- Periodically inspect and rotate valve positions.
- Maintain proper documentation of storage conditions and duration.
Proper storage and handling practices ensure that replacement valves will be ready for immediate use when needed.
Training and Documentation
Effective maintenance depends not only on proper techniques but also on well-trained personnel and comprehensive documentation:
- Personnel Training:
- Provide specific training on small hydraulic ball valve maintenance.
- Include both theoretical knowledge and hands-on practice.
- Cover safety procedures, especially regarding pressurized systems.
- Ensure understanding of hydraulic principles and system impacts.
- Implement competency verification before independent maintenance.
- Documentation Requirements:
- Maintain detailed maintenance logs for each valve.
- Record all inspections, findings, and actions taken.
- Document replacement parts used and their specifications.
- Keep manufacturer documentation readily accessible.
- Update procedures based on field experience and manufacturer bulletins.
- Knowledge Management:
- Create a centralized repository for maintenance information.
- Develop troubleshooting guides based on historical issues.
- Implement a system for sharing best practices among maintenance personnel.
- Regularly review and update maintenance procedures.
Proper training and documentation create a foundation for consistent, high-quality maintenance practices that extend valve life and improve system reliability.
Conclusion
By treating small hydraulic ball valves as the critical components they are and implementing these maintenance best practices, you’ll ensure reliable operation, minimize downtime, and maximize the return on your hydraulic system investment.
If you need specialized hydraulic ball valves, contact Topa and we will solve all your questions!
FAQ
How often should I perform maintenance on my ball valve?
Regular maintenance should be done every 6-12 months, depending on usage and operating conditions.
What are the signs that my ball valve needs maintenance?
Look for leaks, unusual noises, difficulty in operation, or changes in pressure or flow rate.
Can improper installation affect the performance of my ball valve?
Yes, incorrect installation can lead to sealing issues, premature wear, and valve failure.
What types of lubricants are recommended for ball valves?
Use lubricants compatible with your valve material and the fluids in your system, such as food-grade or high-temperature lubricants.
How do I know if my valve seals need replacing?
If you notice leaks, reduced sealing efficiency, or visible wear, it’s time to replace the seals.
What should I check during a ball valve inspection?
Inspect the valve body, seat, seals, stem, and torque control for wear, corrosion, and any signs of damage.