Quick couplers facilitate the rapid exchange of hydraulic tools and attachments, allowing operators to switch between different functions quickly and safely, thereby minimizing downtime and maximizing productivity. However, despite their robust design, quick couplers are not immune to wear and tear. Regular maintenance is crucial to ensure that these components continue to function effectively, as neglecting maintenance can lead to leaks, reduced performance, or even system failures.
Understanding Quick Coupler Components
Overview of Key Components
1. Coupler Body:
The coupler body is the main structure of the quick coupler, typically made from durable materials such as steel, brass, or aluminum, depending on the application. It houses the internal components and provides the necessary strength to withstand high-pressure hydraulic fluids. The coupler body is designed to endure harsh working conditions, including extreme temperatures and exposure to corrosive elements, making it a critical part of the coupler’s overall functionality.
2. Seals and O-Rings:
Seals and O-rings are essential for maintaining a tight, leak-proof connection within the quick coupler. These small but vital components are typically made from rubber or other elastomeric materials that can withstand hydraulic fluid exposure and pressure fluctuations. They prevent hydraulic fluid from leaking out and contaminants from entering the system, ensuring that the hydraulic circuit remains efficient and clean.
3. Locking Mechanism:
The locking mechanism is what allows the quick coupler to connect and disconnect rapidly and securely. This component typically consists of a set of locking balls or a sleeve that slides into place to hold the two halves of the coupler together. The locking mechanism must be robust and reliable, as any failure here could result in accidental disconnection, leading to hydraulic leaks or even system failure.
4. Dust Caps and Plugs:
Dust caps and plugs are accessories that protect the quick coupler’s connections when they are not in use. They prevent dust, dirt, moisture, and other contaminants from entering the coupler, which could otherwise lead to wear or damage over time. These protective components are especially important in environments where the equipment is exposed to outdoor elements or dusty conditions.
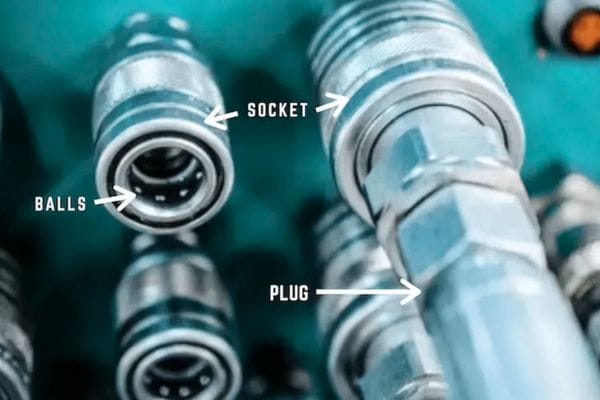
Function of Each Component
Each of these components plays a crucial role in the overall performance of the quick coupler. The coupler body provides the structural integrity required to handle high-pressure operations. Seals and O-rings ensure that the hydraulic fluid remains within the system, preventing leaks that could reduce system efficiency or cause damage. The locking mechanism enables the quick and secure attachment and detachment of hydraulic lines, which is essential for maintaining workflow efficiency. Finally, dust caps and plugs protect the coupler from environmental contaminants, extending the life of the coupler and reducing the need for frequent maintenance.
Common Wear and Tear
Over time, the various components of a quick coupler are subject to wear and tear, which can impact their performance.
Coupler Body: The coupler body can suffer from corrosion, especially if it is exposed to harsh chemicals or moisture. Additionally, physical damage such as dents or scratches can weaken the structural integrity of the body.
Seals and O-rings: These components are prone to degradation due to constant exposure to hydraulic fluids and pressure changes. Over time, seals and O-rings can become brittle, crack, or wear out, leading to leaks and reduced efficiency.
Locking Mechanism: The locking mechanism may experience wear from repeated use, leading to a loose or unreliable connection. Dirt and debris can also clog the mechanism, making it difficult to operate or causing it to fail.
Dust Caps and Plugs: While these components are designed to protect the coupler, they can also wear out, especially if they are not regularly cleaned or if they are frequently removed and replaced. Cracked or missing dust caps can lead to contamination of the coupler’s internal components.
Importance of Regular Maintenance
Preventative vs. Reactive Maintenance
When it comes to maintaining hydraulic quick couplers, there are two primary approaches: preventative and reactive maintenance. Preventative maintenance involves regularly scheduled inspections, cleanings, and part replacements to prevent potential issues before they occur. This proactive approach is designed to catch wear and tear early, ensuring that the coupler remains in optimal working condition and reducing the likelihood of unexpected failures.
On the other hand, reactive maintenance is performed after a problem has already occurred. This approach involves fixing or replacing parts once they fail or when a malfunction becomes apparent. While reactive maintenance may seem more convenient, as it only requires action when something goes wrong, it can lead to more significant issues over time. System failures can result in costly downtime, emergency repairs, and potentially even damage to other components in the hydraulic system.
Preventative maintenance is generally preferred over reactive maintenance for several reasons. First, it allows for the identification and resolution of minor issues before they escalate into major problems. This proactive approach reduces the likelihood of unexpected breakdowns, which can disrupt operations and lead to expensive repairs. Additionally, preventative maintenance helps maintain the overall efficiency of the hydraulic system, ensuring that it operates at peak performance.
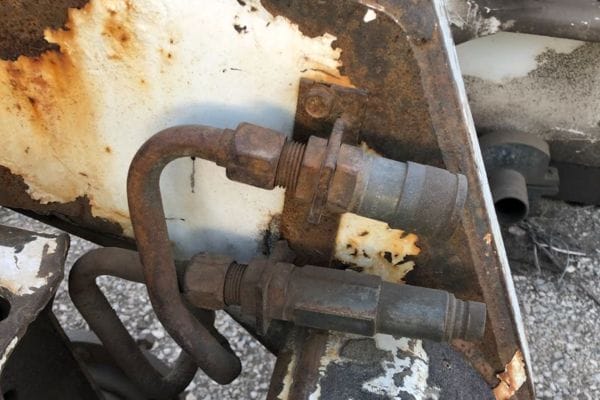
Benefits of Regular Maintenance
Improved Performance and Efficiency: Regular maintenance ensures that quick couplers are always in optimal condition, allowing them to perform their function efficiently. Well-maintained couplers provide secure, leak-free connections, which is crucial for maintaining consistent hydraulic pressure and flow. By keeping the components clean and in good working order, operators can avoid the gradual performance decline that often occurs when maintenance is neglected. This not only improves the immediate efficiency of the hydraulic system but also contributes to long-term operational success.
Extended Lifespan of the Coupler: Quick couplers are built to withstand harsh working conditions, but without regular maintenance, their lifespan can be significantly shortened. Components such as seals, O-rings, and the locking mechanism are particularly susceptible to wear and tear. By regularly inspecting and replacing these parts as needed, the overall lifespan of the coupler is extended. This reduces the frequency of replacements, saving time and money in the long run. Proper maintenance also prevents the cumulative damage that can lead to more severe issues, further prolonging the service life of the coupler.
Reduced Risk of System Failures and Downtime: One of the most significant benefits of regular maintenance is the reduced risk of system failures and unplanned downtime. Hydraulic systems rely on quick couplers to function correctly, and a failure in one coupler can lead to a complete system shutdown. Regular maintenance helps identify potential problems before they lead to failures, ensuring that the system remains operational. This proactive approach minimizes the likelihood of costly downtime, which can have a significant impact on productivity, especially in industries where continuous operation is critical.
Step-by-Step Guide to Quick Coupler Maintenance
Daily Checks
Visual Inspection for Damage or Wear: Start each day with a thorough visual inspection of your quick couplers. Look for any visible signs of damage, such as cracks, dents, or deformation in the coupler body. Pay close attention to the locking mechanism and ensure it appears intact and functional. Additionally, inspect the dust caps and plugs to ensure they are in place and not damaged. A quick visual check can help identify potential issues before they escalate into more significant problems.
Checking for Leaks and Ensuring Connections are Tight: Hydraulic fluid leaks are a common issue with quick couplers and can lead to performance degradation or system failure if not addressed promptly. During your daily inspection, check all connections for signs of leaks, such as fluid accumulation around the coupler joints. If you notice any leaks, tighten the connections or replace the seals as necessary. Ensuring that all connections are secure and leak-free is crucial for maintaining system pressure and preventing contamination.

Weekly Maintenance
Cleaning the Coupler Body and Components: Regular cleaning is essential to prevent dirt, debris, and contaminants from entering the hydraulic system through the coupler. Once a week, clean the coupler body and its components with a suitable cleaning solution or a soft brush. Focus on removing any accumulated grime from the locking mechanism, seals, and O-rings. Avoid using harsh chemicals that could degrade the materials of the coupler or its seals. After cleaning, thoroughly dry the components to prevent moisture from causing corrosion.
Lubricating the Locking Mechanism: The locking mechanism is a critical part of the quick coupler, and regular lubrication is necessary to keep it functioning smoothly. Apply a light, high-quality lubricant to the moving parts of the locking mechanism once a week. This will reduce friction, prevent wear, and ensure that the coupler can be easily connected and disconnected. Be careful not to over-lubricate, as excess lubricant can attract dust and debris, which can cause additional wear over time.
Inspecting and Replacing Worn-Out Seals and O-rings: Seals and O-rings are essential for maintaining a leak-proof connection, but they can wear out over time due to constant pressure and fluid exposure. During your weekly maintenance routine, inspect these components for signs of wear, such as cracks, flattening, or brittleness. If any seals or O-rings appear damaged or worn, replace them immediately to prevent leaks and maintain the integrity of the hydraulic system.
Monthly/Periodic Maintenance
Full Disassembly and Deep Cleaning: At least once a month, perform a full disassembly of the quick coupler for a more thorough inspection and cleaning. Disassemble the coupler according to the manufacturer’s instructions, taking care to keep track of all components. Clean each part individually, paying particular attention to areas where dirt and debris may have accumulated. This deep cleaning helps prevent the build-up of contaminants that can cause wear and reduce the coupler’s efficiency.
Inspecting Internal Components for Corrosion or Damage: With the coupler disassembled, inspect all internal components for signs of corrosion, wear, or damage. Corrosion can weaken the metal parts of the coupler, leading to failure under pressure. Look for any discoloration, pitting, or rust on the metal surfaces. Additionally, check for any signs of mechanical wear, such as grooves or scratches, which could indicate that parts are rubbing against each other. Address any issues immediately, either by cleaning and lubricating the affected areas or by replacing damaged components.
Replacing Damaged or Worn Components: During the monthly maintenance routine, replace any components that show signs of significant wear or damage. This includes seals, O-rings, springs, and any other parts that are not functioning as intended. Using high-quality replacement parts that meet the manufacturer’s specifications is essential to ensure the continued reliability of the coupler. Keeping spare parts on hand will help streamline this process and minimize downtime.
Annual Maintenance
Professional Inspection and Pressure Testing: Once a year, it’s advisable to have your quick couplers professionally inspected and pressure tested by a certified technician. A professional inspection can identify issues that may not be visible during regular maintenance, such as internal stress fractures or subtle degradation of materials. Pressure testing ensures that the coupler can withstand the hydraulic system’s operational pressures without leaking or failing. This annual checkup is crucial for preventing catastrophic failures and ensuring the safety and reliability of the system.
Replacing Major Components as Needed: Based on the results of the professional inspection and pressure testing, you may need to replace major components of the quick coupler. This could include the entire locking mechanism, the coupler body, or other critical parts that have reached the end of their service life. Replacing these components proactively, rather than waiting for them to fail, helps maintain the overall health of the hydraulic system and prevents unexpected downtime.
Conclusion
Implementing the maintenance practices outlined in this guide will not only enhance the efficiency and reliability of your hydraulic quick couplers but will also contribute to the overall longevity of your hydraulic systems. By staying on top of routine maintenance, you can avoid the pitfalls of reactive repairs, ensuring that your equipment remains in top condition and continues to perform at its best. Taking the time to care for your quick couplers will yield long-term benefits, including reduced operational costs, minimized downtime, and increased safety for your equipment and personnel.
FAQ
How often should I inspect my hydraulic quick couplers?
It’s recommended to perform daily visual inspections, weekly cleanings, and monthly deep cleanings, with a professional inspection annually.
What are the common signs of wear in quick couplers?
Common signs include visible cracks, leaks, difficulty connecting or disconnecting, and worn seals or O-rings.
How can I prevent leaks in my quick couplers?
Regularly check and replace seals and O-rings, ensure tight connections, and clean the coupler components to prevent debris buildup.
What should I do if my quick coupler is difficult to connect or disconnect?
Clean the locking mechanism, lubricate moving parts, and inspect for any worn or damaged components that may need replacement.
Can I use any lubricant on my quick coupler?
Use a high-quality lubricant recommended by the manufacturer to avoid damaging the coupler or attracting excessive dirt and debris.
When should I replace the seals and O-rings in my quick coupler?
Replace seals and O-rings during your weekly maintenance if you notice any signs of wear, such as cracks or brittleness, or if you experience leaks.