A Banjo bolt is a key component in hydraulic systems, providing a unique method of connecting and securing hydraulic hoses to components such as valves, pumps, and cylinders. These bolts feature a hollow center, allowing fluid to pass through them efficiently, and they are often used in applications where space is limited or where conventional fittings might be too bulky.
The Basics of a Banjo Bolt: Anatomy and Function
A Banjo bolt is a specialized fastener used primarily in fluid systems to provide secure, leak-free connections. It features a unique design that sets it apart from traditional bolts, making it ideal for applications that require fluid flow through the bolt itself. Understanding the anatomy and function of a banjo bolt is key to selecting the right fitting for your hydraulic or fluid transfer system.
Key Components of a Banjo Bolt
The Banjo bolt is composed of a few key parts that give it its distinctive design and functionality:
The Bolt Shaft: This is the main body of the bolt, typically threaded on both ends. It’s used to fasten the bolt securely into the receiving component or fitting.
The Hollow Center: The most notable feature of a Banjo bolt is its hollow center, which allows fluid to pass through it. This is essential for transferring fluid from one part of the system to another, while still maintaining a secure connection.
The Banjo Fitting: The bolt is usually paired with a Banjo fitting, which has a circular shape with a hole in the center. The bolt passes through this fitting, creating a fluid-tight connection.
The Seal: To ensure no leakage, Banjo bolts typically use sealing washers or O-rings placed on either side of the Banjo fitting. These seals help to prevent fluid from leaking around the connection point.
The Banjo bolt’s unique design allows it to accommodate high-flow fluid systems in a compact space, making it a go-to choice for a wide range of industries.
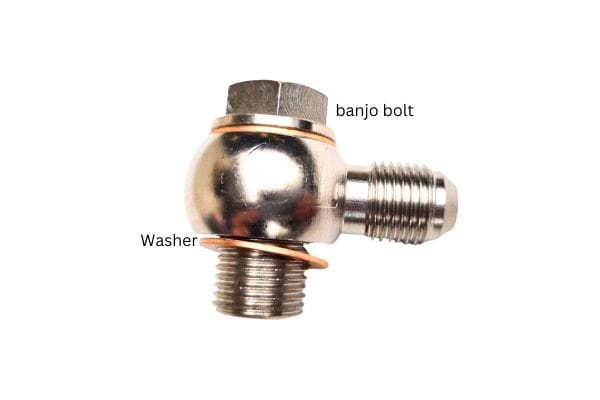
How Banjo Bolts Work in Fluid Transfer Systems
In hydraulic and fluid systems, Banjo bolts provide a critical function by enabling fluid to pass through various components while maintaining a secure and reliable connection. The bolt is threaded into the hydraulic component, and the Banjo fitting, which is mounted on the hose or tubing, is secured around the bolt. The hollow center of the Banjo bolt acts as a passageway for the fluid, directing it from one part of the system to another.
The Banjo bolt design allows for efficient fluid flow, even under high-pressure conditions. When used correctly, the bolt ensures that the system operates without leaks, minimizing potential damage or system inefficiencies. The flexibility in design makes it especially effective in compact or high-pressure systems where traditional fittings might not work as efficiently.
Common Dimensions and Thread Types
Banjo bolts come in various sizes and thread types, depending on the requirements of the hydraulic system. The dimensions of the Banjo bolt are crucial because they must match the corresponding Banjo fitting to ensure a proper seal and prevent leaks.
Common Diameters: Banjo bolts typically come in diameters ranging from 1/8 inch to 1 inch (or larger, depending on the application). The exact size needed will depend on the specific flow rate and pressure requirements of the system.
Thread Types: Banjo bolts can feature different thread types, including:
NPT (National Pipe Thread): Common in North America, used for tapered thread connections.
BSP (British StandardPipe): Often used in European and international systems, featuring a parallel thread design.
Metric Threads: Used in global applications, with measurements based on the metric system.
Choosing the right size and thread type ensures a proper fit and function, reducing the risk of leaks and performance issues.
Understanding Pressure Ratings and Load Capacities
When selecting Banjo bolts, it’s essential to consider the pressure ratings and load capacities, as these factors determine the strength and durability of the connection. The pressure rating refers to the maximum pressure that the Banjo bolt and fitting can withstand without failure, while the load capacity indicates the maximum force the bolt can handle before it deforms or breaks.
Pressure Ratings: Banjo bolts are available in various pressure ratings, from low-pressure applications (around 150 PSI) to high-pressure systems that can exceed 10,000 PSI. It’s crucial to match the Banjo bolt’s pressure rating with the pressure requirements of your system to ensure safe and efficient operation.
Load Capacities: Load capacity depends on the material of the Banjo bolt (e.g., steel, aluminum, brass) and the overall design. Typically, Banjo bolts made of steel will have a higher load capacity than those made of softer materials like aluminum or brass.
The Role of the Banjo Bolt in Fluid Power Systems
In fluid power systems, where the movement of liquids or gases is harnessed to do work, Banjo bolts play a crucial role in maintaining efficient flow while preventing leaks. These systems, which include hydraulic presses, automotive braking systems, and aerospace machinery, rely on the Banjo bolt’s unique ability to transfer fluids in confined spaces.
Ensuring Proper Fluid Flow: In fluid power systems, maintaining a steady flow of fluid is essential for smooth operation. Banjo bolts allow for this by facilitating uninterrupted fluid transfer through their hollow center, which ensures that the system operates at optimal pressure and flow rates.
Minimizing System Failures: Because Banjo bolts are designed to provide a secure and reliable seal, they help prevent fluid leakage, which could lead to system inefficiency or failure. This is particularly important in high-stakes industries like aerospace, automotive, and industrial manufacturing, where even minor leaks can result in catastrophic failures.
Different Banjo Bolt Sizes: Finding the Right Fit for Your Application
Choosing the correct Banjo bolt size is crucial to the performance and safety of any hydraulic or fluid transfer system. An improperly sized bolt can lead to leaks, system inefficiencies, or even catastrophic failures in high-pressure applications. The right size ensures that the connection is secure, the fluid flows correctly, and the system operates optimally. In this section, we will explore standard sizes, custom options, and how to choose the right size for your specific needs.
Standard Sizes vs. Custom Sizes
Banjo bolts are available in a range of standard sizes designed to fit the most common applications in hydraulic, automotive, and industrial systems. Standard sizing ensures compatibility and ease of replacement, making maintenance and repairs more straightforward. However, there are situations where custom sizes may be necessary to meet specific system requirements.
Standard Sizes: Banjo bolts come in various standard sizes, often defined by their thread size, bolt diameter, and overall length. These sizes are commonly used in many industrial, automotive, and hydraulic systems.
Custom Sizes: In some cases, a hydraulic system may require Banjo bolts of non-standard sizes. This might happen when working with unique system designs, custom machinery, or specialized pressure requirements. Custom Banjo bolts can be made to specific diameters, lengths, and thread configurations to fit the unique needs of a project.
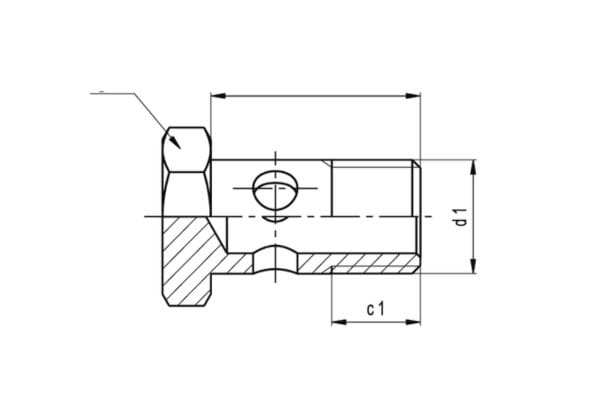
How to Choose the Right Size for Your System
Selecting the right Banjo bolt size for your system requires careful consideration of several factors. An improper size can lead to poor performance or even system failure. Here are the key elements to keep in mind when determining the appropriate size for your Banjo bolt:
System Flow Rate and Pressure: The size of the Banjo bolt must match the flow rate and pressure specifications of your system. Larger bolts with bigger diameters allow for higher fluid flow and are better suited for high-flow systems. On the other hand, smaller bolts may be more appropriate for lower-flow systems or applications with limited space. It’s crucial to consider the pressure rating of the Banjo bolt and fitting to ensure it can handle the demands of the system without leaking or failing.
Compatibility with Banjo Fittings: The Banjo bolt and Banjo fitting work together to create a secure, leak-proof connection. Therefore, the size of the bolt must be compatible with the Banjo fitting. This means matching thread types (NPT, BSP, Metric, etc.) and bolt diameters with the corresponding fittings. The inner diameter of the Banjo fitting should allow for the fluid to pass through the bolt without restrictions. Ensuring that both the bolt and fitting are of the correct size will optimize fluid flow and minimize the risk of leaks.
Material and Strength Considerations: The material of the Banjo bolt (steel, brass, aluminum, etc.) also plays a role in its suitability for different sizes. For example, larger bolts made of steel may be needed for high-pressure systems where strength and durability are essential, whereas smaller aluminum or brass bolts might be sufficient for low-pressure or non-corrosive applications. Ensure the material is selected based on the pressure, environment, and fluid being transported.
The Banjo Fitting Standard: Key Considerations for Engineers
The Banjo fitting standard is a critical set of guidelines for engineers involved in designing and manufacturing fluid transfer systems. These standards ensure that Banjo bolts and fittings meet specific requirements for size, material, pressure ratings, and sealing methods, ultimately guaranteeing optimal performance and safety. Understanding these standards is essential for creating reliable and efficient hydraulic and fluid systems. Below are the key considerations engineers should keep in mind when working with Banjo fittings.
Industry Standards and Certifications for Banjo Bolts
Banjo bolts and fittings are subject to various industry standards and certifications to ensure that they perform consistently and safely across different applications.
ISO (International Organization for Standardization): ISO 8434-2 is the main international standard for hydraulic fluid power systems, including Banjo fittings. It sets the guidelines for the dimensions, design, and pressure ratings of hydraulic connectors. ISO standards are widely adopted and help ensure global compatibility.
SAE (Society of Automotive Engineers): SAE J514 is a key standard for hydraulic hose fittings and includes guidelines for Banjo fittings in automotive applications, particularly in fluid systems in vehicles, heavy equipment, and machinery.
DIN (Deutsches Institut für Normung): DIN 2353 is a German standard that applies to Banjo bolts and other hydraulic components. It establishes the specifications for thread types, material grades, and pressure tolerances.
ANSI (American National Standards Institute): ANSI B31.3 provides guidelines for pipe and tubing fittings used in process systems. While not exclusively for Banjo fittings, it offers useful information on material standards and pressure tolerances for fluid systems.
How Standards Impact Performance and Longevity
In addition to enhancing safety, adhering to Banjo fitting standards also has a significant impact on the performance and longevity of hydraulic systems. By ensuring that the right materials, dimensions, and pressure ratings are used, engineers can design systems that perform efficiently over the long term, reducing maintenance costs and downtime. Here’s how standards contribute to better system performance:
Consistency in Performance: Banjo bolts and fittings that meet industry standards are designed to deliver consistent performance, ensuring that fluid flow is uninterrupted, pressure is maintained, and no leaks occur. This helps the overall system work smoothly without unexpected breakdowns, which can reduce operational efficiency.
Improved Durability: When components are designed and manufactured according to established standards, they are built to last longer under harsh conditions. For example, using the correct material for the Banjo bolt (e.g., stainless steel for corrosion resistance) and ensuring it meets the necessary pressure rating extends the life of the fitting. Properly adhering to standards ensures that the fitting can withstand wear and tear over time, reducing the frequency of replacement and system failures.
Maximizing Efficiency: Properly sized Banjo bolts and fittings allow fluid to flow efficiently through the system, reducing energy consumption and increasing the overall efficiency of the fluid transfer process. When the right size and materials are selected based on industry standards, the system operates more efficiently, lowering the operational costs and enhancing system output.
Reduced Maintenance and Downtime: Systems that use standardized Banjo bolts are more likely to experience fewer failures, requiring less maintenance and reducing downtime. Standardization allows engineers to predict performance accurately and quickly source replacement parts, keeping the system running smoothly and avoiding costly repairs.
Lower Total Cost of Ownership: By following the Banjo fitting standard, engineers can design systems that are more durable and efficient, reducing the total cost of ownership (TCO). This is especially important in industries where uptime is critical, such as aerospace, automotive, and industrial manufacturing. Ensuring that components meet standards upfront helps avoid expensive repairs or replacements later.
Banjo Bolt Torque: Getting It Just Right
When installing a Banjo bolt, getting the torque value just right is crucial for ensuring a secure, leak-proof connection and preventing damage to both the bolt and the surrounding components. Torque refers to the amount of rotational force applied to a bolt to tighten it. Improper torque can cause a variety of issues, including leaks, stripped threads, or even complete system failure.
What Is Torque and Why Does It Matter?
Torque is the measure of the rotational force applied to a fastener like a Banjo bolt. It is typically measured in units like foot-pounds (ft-lbs) or Newton-meters (Nm). When installing a Banjo bolt, applying the correct amount of torque ensures that the fitting is tightly secured, but without over-tightening it, which could damage the components.
Ensures Leak-Free Connections: A proper torque value is necessary to create a tight, leak-free seal between the Banjo bolt, fitting, and surrounding parts. Too little torque can leave gaps or spaces in the seal, while excessive torque can crush gaskets or O-rings, compromising the integrity of the connection.
Prevents Over-Stretching or Damage: Correct torque prevents the Banjo bolt from being stretched or deformed, which could weaken the bolt and lead to premature failure. Torque is critical for ensuring that the bolt functions effectively without damaging the surrounding components, such as the Banjo fitting or the hose.
Maintains System Pressure: Hydraulic and fluid power systems often operate under high pressure, and a properly torqued Banjo bolt ensures that the connection can withstand these forces without leaking or coming loose. Without the correct torque, there is a risk of pressure loss and system inefficiency.
Calculating the Correct Torque for Your Banjo Bolt
Calculating the correct torque value is essential to ensure the Banjo bolt is properly installed. The appropriate torque depends on several factors, including the size and material of the bolt, the type of seal used, and the specific application. Here’s how to determine the correct torque for your Banjo bolt:
Consider the Bolt Size and Material: The torque required to secure a Banjo bolt depends on the size and material of the bolt. Larger bolts typically require more torque, while smaller bolts require less. For example:
A 1/4-inch Banjo bolt might require around 8-12 ft-lbs (11-16 Nm) of torque.
A 1/2-inch Banjo bolt may need approximately 20-30 ft-lbs (27-40 Nm).
Additionally, the material of the bolt plays a role in the torque value. Stainless steel bolts generally require more torque compared to aluminum bolts due to their higher strength and friction characteristics.
Consider the Type of Seal: Banjo bolts are often used with washers or O-rings to ensure a tight seal. The material of the sealing component (e.g., copper, rubber, or elastomeric seals) may affect the torque value. Soft seals typically require lower torque to avoid crushing, while harder seals can withstand more force.
Use a Torque Wrench: To achieve the correct torque, a torque wrench should be used. This tool allows you to apply a precise amount of torque, reducing the risk of under- or over-tightening. When using a torque wrench, it’s important to apply the torque in stages and in a crisscross pattern (especially for multiple bolts) to ensure even pressure distribution.
Temperature and Environmental Factors: Temperature fluctuations can affect the torque values, particularly in extreme conditions. As temperatures increase, materials expand, potentially altering the fitting’s tightness. Always account for temperature differences when installing Banjo bolts in environments with significant temperature variation.
Conclusion
As we’ve explored throughout this guide, understanding the banjo bolt standard is key to optimizing the performance, safety, and longevity of fluid power systems. Whether you’re designing hydraulic systems or maintaining existing ones, ensuring that your Banjo bolts meet the correct specifications is critical for efficient operation. By adhering to the Banjo bolt standard, you can prevent issues such as leaks, pressure loss, and equipment failure, ultimately leading to a more reliable system.
FAQ
What is a banjo bolt?
A banjo bolt is a fastener used in hydraulic and fluid systems to connect hoses or pipes to other components. It has a hole in the center that allows fluid to flow while securing the connection.
How do I know which size banjo bolt to use?
The correct banjo bolt size depends on your system specifications. Always refer to the manufacturer’s guidelines for sizes and pressure ratings and consider the size of the hose or pipe you are using.
Can Banjo bolts be made from any material?
Banjo bolts are available in a variety of materials, such as stainless steel, brass and aluminum. Please choose your material based on factors such as corrosion resistance, pressure resistance and environmental conditions.
What happens if a banjo bolt is overtightened or overtightened?
Over-tightening can damage the bolt, seals or surrounding components, leading to leaks or system failure. Under-tightening can lead to loose connections and fluid leaks, reducing system performance and safety.
How do I install a banjo bolt correctly?
When installing banjo bolts, make sure you use the correct size and material, check the seals, and apply the correct torque with a torque wrench. Follow the manufacturer’s specifications to ensure a secure leak-free connection.
What are some common applications for banjo bolts?
Universal bolts are commonly used in hydraulic systems, automotive applications, fuel lines and fluid transfer systems where compact connections are required for efficient fluid flow.