Gate valves and ball valves are among the most commonly used options, each offering unique benefits and ideal use cases. Selecting the appropriate type isn’t just about preference—it’s crucial for maintaining flow control, system durability, and operational efficiency.
What Are Gate Valves?
Definition
A gate valve is a type of valve used in fluid control systems to start or stop the flow of liquid or gas. It achieves this by lifting a “gate” out of the path of the fluid. Gate valves are particularly effective for applications requiring a full, unobstructed flow, and they’re commonly found in systems where high-pressure resistance is essential, such as water treatment plants, oil pipelines, and various industrial environments.
How Gate Valves Work
Gate valves operate using a linear motion to open or close the valve. When the valve’s handwheel or actuator is turned, the gate inside the valve is either lifted or lowered, moving perpendicular to the flow direction. This vertical movement allows the valve to fully open or close, which provides minimal resistance when fully open, reducing pressure drop across the valve. Gate valves aren’t ideal for throttling or flow modulation due to their slower operation time, as they require multiple turns to move between open and closed positions. Additionally, partially open gate valves can suffer from excessive wear and vibration.
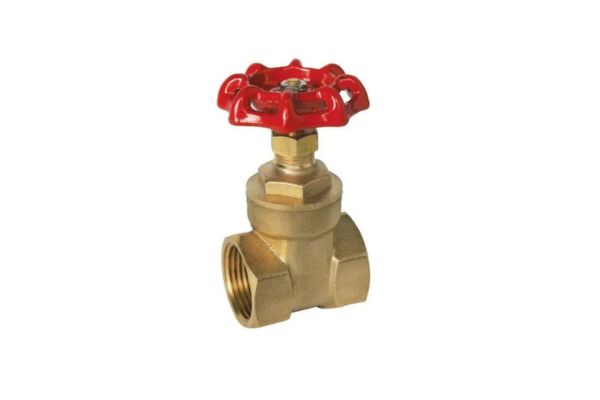
Types of Gate Valves
Rising Stem Gate Valve: In this type, the stem rises as the valve opens, providing a visible indicator of whether the valve is open or closed. However, it requires more installation space and is typically not ideal for confined areas.
Non-Rising Stem Gate Valve: The stem does not move upward as the valve opens, making it a good option for applications with limited vertical space. The stem remains inside the valve, with only the gate itself moving.
Wedge Gate Valve: Known for its ability to provide a tight seal, the wedge gate valve has a gate shaped like a wedge that presses firmly into the seat to prevent leaks. It is commonly used in high-pressure applications.
Parallel Slide Gate Valve: This type of gate valve has a parallel gate design instead of a wedge. It’s typically easier to open and close, with less risk of jamming under high pressures.
Key Features of Gate Valves
Flow Control: Gate valves are best suited for applications requiring either a fully open or fully closed position. When fully open, they allow unobstructed flow with minimal pressure drop, making them highly efficient for applications demanding maximum throughput.
Resistance to Pressure: Due to their robust construction, gate valves are highly resistant to pressure. This makes them a preferred choice for high-pressure environments, such as pipelines and industrial processing.
Slow Operation Time: Unlike quick-action valves, gate valves have a slower operation time due to the multiple turns required to fully open or close the gate. This characteristic makes them unsuitable for applications requiring frequent or rapid changes in flow.
What Are Ball Valves?
Definition
A ball valve is a type of valve used to control the flow of fluids through a rotary motion. It features a spherical ball with a hole through the center, which, when aligned with the pipeline, allows fluid to flow through. Ball valves are known for their reliability and ability to provide a tight seal, even after extended periods of disuse, making them ideal for rapid on/off control in a range of applications, from residential plumbing to complex industrial systems.
How Ball Valves Work
Ball valves operate using a quarter-turn mechanism. When the handle of the valve is turned 90 degrees, the ball inside rotates to either open or block the flow path. In the open position, the hole in the ball aligns with the flow direction, allowing fluids to pass freely. In the closed position, the solid part of the ball blocks the flow. This simple mechanism provides a fast and efficient way to control fluid flow, requiring only a short turn to fully open or close, unlike the multi-turn process required for gate valves. Ball valves are especially useful for applications where quick, frequent adjustments are needed.
Types of Ball Valves
Full Port Ball Valve: In a full port ball valve, the bore (or hole) in the ball matches the diameter of the pipeline, allowing for an unrestricted flow. This reduces pressure drop across the valve and is beneficial in applications where high flow rates are critical.
Standard Port Ball Valve: This type has a slightly smaller bore than the pipeline diameter, creating a small pressure drop. While it is less costly than a full port valve, it is suitable for applications where a minor reduction in flow is acceptable.
Trunnion Mounted Ball Valve: In this design, the ball is anchored at both the top and bottom, allowing it to handle higher pressures with reduced operating torque. Trunnion mounted valves are commonly used in larger pipelines and high-pressure applications.
Floating Ball Valve: The ball in this type is held in place by the valve seats but is otherwise free to “float” in the valve body. When the valve is closed, the pressure from the fluid pushes the ball against the downstream seat, creating a tight seal. Floating ball valves are generally used for smaller pipe diameters.
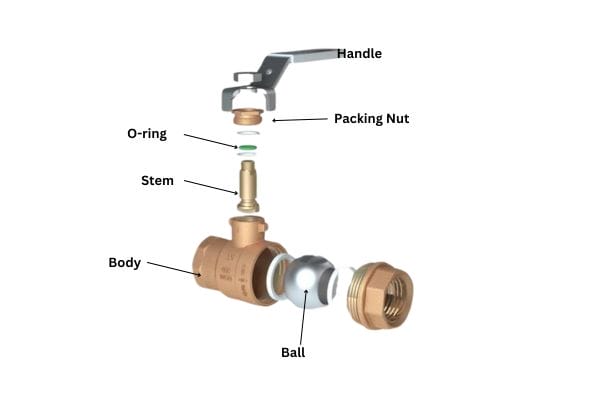
Key Features of Ball Valves
Quick Operation: Due to their quarter-turn mechanism, ball valves are extremely quick to operate. This makes them ideal for applications where rapid opening and closing are necessary.
Suitable for On/Off Control: Ball valves provide reliable on/off control without significant wear. They are highly effective in applications requiring immediate shutoff or full flow without throttling.
Pressure Handling: Ball valves are capable of handling high-pressure environments, particularly trunnion-mounted designs that support the ball securely, reducing stress on the valve seats.
Gate Valve vs Ball Valve: Key Differences
Understanding the distinctions between gate valves and ball valves is essential for selecting the appropriate valve for a given application. Here’s a comparison of their main differences:
Mechanism
Gate Valve: Utilizes a linear motion mechanism where a gate or wedge moves up and down perpendicular to the flow direction. This motion requires multiple turns to open or close the valve completely, making it a multi-turn valve.
Ball Valve: Operates with a rotary motion using a quarter-turn mechanism. A simple 90-degree turn of the handle or actuator rotates the ball inside, opening or closing the flow path quickly. This makes it highly effective for rapid on/off control.
Operation Speed
Gate Valve: Due to its multi-turn operation, a gate valve has a slower response time, making it suitable for gradual control in applications where quick shutoff is not a priority.
Ball Valve: With its quarter-turn mechanism, a ball valve offers instantaneous operation. This quick response is ideal for applications that need immediate shutoff or rapid on/off cycling.
Flow Control and Tightness
Gate Valve: Offers precise control over flow when used in fully open or fully closed positions. However, when partially open, it is less effective at sealing and may experience turbulence and wear, which can lead to leakage over time.
Ball Valve: Known for its leak-tight seal, even in high-pressure systems, ball valves are excellent for on/off control but not as ideal for precise throttling. Their simple design and tight shutoff make them highly effective in maintaining leak resistance.
Durability and Maintenance
Gate Valve: Gate valves are generally durable in high-pressure applications but are prone to wear and tear if frequently operated. The multi-turn mechanism can lead to mechanical wear, and maintenance may require more effort due to the complex internal structure.
Ball Valve: Ball valves have a longer lifespan and are easier to maintain due to their simpler design. The ball’s smooth surface minimizes wear, especially in low-friction applications. However, in abrasive environments, the valve seats may need replacement over time.
Installation and Cost Factors
Gate Valve: Typically, gate valves are more costly to install and maintain, especially in large pipelines, due to their larger size and multi-turn mechanism. They also require more space for operation, particularly rising stem types.
Ball Valve: Generally less costly to install and maintain compared to gate valves, ball valves are compact and require minimal space. They have lower installation and replacement costs, making them a cost-effective choice for most applications.
Pressure and Temperature Tolerance
Gate Valve: Suitable for high-pressure and high-temperature environments, gate valves are commonly used in demanding industrial applications where these factors are critical.
Ball Valve: Ball valves also perform well in high-pressure environments and can handle a broad range of temperatures, depending on the materials used. However, in extremely high-temperature applications, they may require specialized materials to maintain performance.
How to Choose: Gate Valve or Ball Valve?
Selecting between a gate valve and a ball valve depends on the unique demands of your system and the specific conditions in which the valve will operate. Here are some essential decision factors and common scenarios to help you make the best choice.
Decision Factors
1. System Requirements
Pressure: Consider the operating pressure of your system. Gate valves are typically better suited for applications with very high pressures, as their multi-turn mechanism and robust construction offer excellent resistance under extreme conditions. Ball valves can also handle high pressure, but specific designs, like trunnion-mounted ball valves, are better for very high-pressure systems.
Temperature: High-temperature environments may demand materials that can withstand extreme heat. Gate valves are often used in such scenarios. Ball valves, depending on their seat material, are also versatile but may require special construction for very high temperatures.
Flow Conditions: If precise control over flow rate is required, a gate valve may be preferable, as it can handle gradual flow changes better than a ball valve. For simple on/off control, however, the ball valve is typically the better choice due to its quick operation and ease of use.
2. Frequency of Use
Durability in Frequent Operations: If the valve will be operated frequently, ball valves are generally more durable and require less maintenance for high-cycle use, thanks to their simple quarter-turn operation. Gate valves, while durable, are better suited for applications with less frequent operation as their multi-turn mechanism can wear out with excessive use.
Long-Term Reliability: For applications where valves remain open or closed for extended periods, both valve types can be reliable. However, ball valves tend to maintain a tighter seal over time, making them more suited for applications where minimal leakage is essential.
3. Environment
Clean Environments: In clean environments, such as food processing or pharmaceutical applications, ball valves are often preferred due to their ease of cleaning and fewer internal parts that could trap contaminants.
Harsh Industrial Settings: In environments with abrasive particles, sludge, or other contaminants, gate valves might be a better choice. They are less likely to trap debris within the valve body and are typically constructed from materials that handle tough conditions.
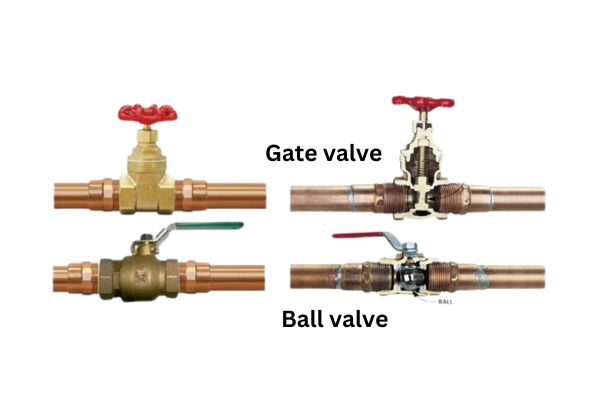
Common Scenarios: When to Choose a Gate Valve vs Ball Valve
High-Pressure Pipelines: For large, high-pressure pipelines that are opened and closed infrequently, a gate valve is often the preferred choice due to its robust design and ability to handle pressure fluctuations without excessive wear.
On/Off Flow Control: In applications where rapid shutoff is crucial—such as in water treatment, HVAC systems, or emergency shut-off lines—a ball valve is typically ideal. Its quarter-turn mechanism allows for instant on/off control, reducing response time.
Gradual Flow Control Applications: When precise flow adjustments are necessary, such as in certain chemical processing applications, a gate valve offers more control. Its slower, multi-turn mechanism allows for more gradual adjustments, which can be important in systems where pressure surges need to be minimized.
Corrosive or Clean Fluids: For clean or moderately corrosive fluids, ball valves are often preferred due to their ease of maintenance and reliable sealing properties. Their compact design is also beneficial in settings where space is limited.
Conclusion
Have you used gate or ball valves in your operations? If you have any questions or need more guidance on selecting the right valve for your application, please feel free to ask – we’re here to help!
FAQ
What is the main difference between a gate valve and a ball valve?
Gate valves use a multi-turn, linear motion to open/close gradually, while ball valves use a quarter-turn rotary motion for quick on/off control.
Which valve is better for high-pressure applications?
Both valves can handle high pressure, but gate valves are generally preferred for very high-pressure and high-temperature environments due to their robust design.
Can gate valves be used for frequent on/off operations?
Gate valves are less suitable for frequent operation as their multi-turn mechanism wears faster with repeated use. Ball valves are a better choice for frequent on/off control.
Are ball valves suitable for flow modulation?
Ball valves are best for on/off applications and do not offer the precision needed for gradual flow control. Gate valves are more suitable for modulating flow.
Which valve type requires less maintenance?
Ball valves usually require less maintenance due to their simpler design and durable sealing capabilities, especially in systems with high usage.
How can I choose between a gate valve and a ball valve?
Consider factors like pressure, temperature, flow control needs, and operational frequency. Gate valves are better for gradual control, while ball valves are ideal for quick, frequent operation.