Standard hydraulic fittings are often designed for general industrial applications and are simply not designed to withstand the severe stresses that characterize the mining and chemical industries. Similarly, in chemical plants, exposure to a variety of corrosive substances – acids, solvents, alkalis, and even salt water environments – can rapidly reduce the corrosion resistance of non-specialized materials. This chemical attack can lead to catastrophic failures, jeopardizing safety and production. This guide is designed to provide engineers, maintenance managers and purchasing professionals in the mining and chemical industries with the knowledge to help you select hydraulic connectors for use in harsh environments.
Understanding the Unique Challenges in Mining and Chemical Industries
To select the most resilient hydraulic connectors, it’s crucial to first deeply understand the specific environmental and operational onslaught they will face. While both mining and chemical industries are categorized as ‘harsh,’ the nature of their challenges can differ significantly, demanding tailored solutions.
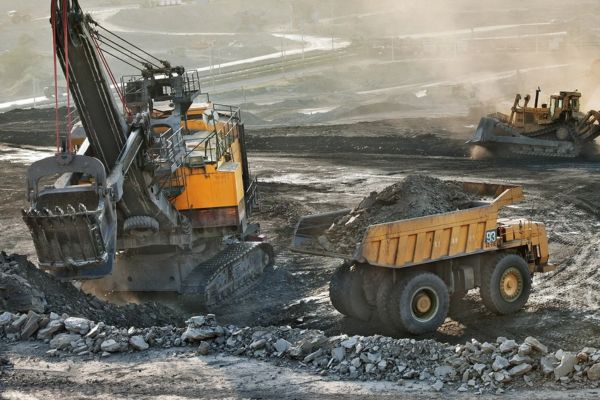
The Abrasive Reality of Mining Operations
Mining environments are characterized by relentless mechanical stress and particulate contamination, creating a uniquely challenging scenario for hydraulic systems.
- Dust and Particulate Contamination: Mines are inherently dusty. Fine rock dust, ore particles, and other abrasive materials are constantly airborne and can settle on equipment. These particles can work their way into hydraulic connector threads and sealing interfaces, causing abrasive wear that compromises seal integrity and leads to leaks. Over time, this ingression can also damage the connector bodies themselves.
- Vibration and Shock Loads: Heavy machinery used in mining, such as excavators, haul trucks, crushers, and drilling rigs, generates significant and often constant vibration. Additionally, impact events and shock loads are common. Standard connectors can loosen under such conditions, leading to leakage, reduced system pressure, and eventual catastrophic failure. Cyclic stresses can also induce fatigue in connector materials.
- Extreme Temperature Fluctuations: Mining operations can occur in diverse geographical locations, from scorching deserts to frigid arctic conditions. Equipment might also experience rapid temperature changes, for instance, when moving from a sun-baked surface into a cooler underground area, or due to the heat generated by the hydraulic system itself. These fluctuations can affect material properties, seal performance, and fluid viscosity, all of which impact connector reliability.
The Corrosive Threat in Chemical Processing
Chemical plants present a different, but equally severe, set of challenges, primarily centered around chemical attack and the need for stringent material compatibility.
- Aggressive Chemical Exposure: The very nature of chemical processing involves a vast spectrum of potentially corrosive substances. These can range from strong acids (e.g., sulfuric, hydrochloric) and bases (e.g., sodium hydroxide) to various solvents, oxidizers, and specialized process chemicals. Each chemical, or combination thereof, can interact differently with connector materials, leading to various forms of corrosion if an incompatible material is chosen.
- High Humidity and Saltwater Exposure: Many chemical plants are located in coastal areas or regions with high ambient humidity. This moisture, especially saline, can significantly accelerate corrosion rates, particularly for less resistant materials. Even atmospheric exposure can be a concern.
- Specific Material Compatibility Requirements: Beyond general corrosion, certain chemicals can cause specific issues like stress corrosion cracking (SCC), pitting, or crevice corrosion in susceptible materials. The process fluids themselves, or even cleaning agents used in the plant, dictate strict material compatibility to prevent contamination of the process medium or premature failure of the hydraulic component.
Comparison of Environmental Stressors: Mining vs. Chemical Industry
Stressor Factor | Mining Industry | Chemical Industry | Common Impact on Connectors |
Primary Contaminants | Abrasive dust (rock, ore, coal), mud, water | Corrosive chemicals (acids, bases, solvents), vapors, process fluids | Wear, seal damage, clogging, material degradation, corrosion |
Mechanical Stress | High vibration, shock loads, impacts, heavy loads | Often lower, but can have pump/pipe vibration, pressure cycling | Fatigue, loosening of connections, seal extrusion, cracking |
Temperature Extremes | Wide ambient fluctuations (desert heat to arctic cold), equipment-generated heat | Process-specific (cryogenic to very high temps), ambient conditions | Material embrittlement/softening, seal failure, fluid viscosity changes |
Chemical Attack | Generally lower, but can involve acidic mine water, de-icing salts | Primary concern; wide range of aggressive substances | Severe corrosion, material dissolution, stress corrosion cracking |
Humidity/Moisture | Variable; can be high underground or in wet processing | Often high, especially coastal; process steam/water | Atmospheric corrosion, accelerates chemical corrosion |
Pressure Conditions | High pressures common in hydraulic machinery | Variable; can range from vacuum to very high pressures | Leakage, burst failure, fatigue |
UV Exposure | Outdoor equipment subject to sunlight | Outdoor installations subject to sunlight | Degradation of non-metallic components (e.g., some seals, hoses) |
Material Matters: Selecting the Right Alloys for Resilience
The choice of material is arguably the most critical factor in determining a hydraulic connector’s ability to withstand the harsh conditions prevalent in mining and chemical industries. Standard carbon steel, while adequate for many general-purpose applications, often falls short when faced with severe abrasion, aggressive chemicals, or extreme temperatures.
Beyond Basic Steel: The Need for Specialized Materials
In environments where connectors are constantly bombarded by corrosive media or abrasive particles, the limitations of basic carbon steel become quickly apparent. Corrosion can rapidly degrade carbon steel, leading to leaks, reduced structural integrity, and eventual failure. Abrasion can wear down sealing surfaces and threads.
Stainless Steel Grades and Their Applications
Stainless steels are a family of iron-based alloys containing a minimum of 10.5% chromium. This chromium content forms a passive, self-repairing oxide layer on the surface, which provides corrosion resistance. Different grades offer varying levels of corrosion resistance and mechanical properties.
- 304 Stainless Steel 304 stainless steel (often referred to as 18/8 due to its 18% chromium and 8% nickel content) is a widely used austenitic stainless steel. It offers good corrosion resistance in many environments and has excellent formability and weldability. However, it is susceptible to chloride-induced stress corrosion cracking and pitting, making it less suitable for environments with significant chloride exposure (e.g., coastal chemical plants, or when handling certain chloride-containing chemicals).
- 316/316L Stainless Steel 316 stainless steel contains molybdenum (typically 2-3%) in addition to chromium and nickel. This molybdenum addition significantly enhances its resistance to general corrosion and, crucially, to pitting and crevice corrosion, especially in chloride-containing environments. 316L is the low-carbon version of 316, which minimizes sensitization (the formation of chromium carbides at grain boundaries during welding) and thus maintains corrosion resistance in the heat-affected zone of welds. For these reasons, 316/316L is often the go-to material for hydraulic connectors in chemical processing and marine applications.
- Duplex Stainless Steels Duplex stainless steels have a mixed microstructure of austenite and ferrite (typically in a 50/50 ratio). This structure provides them with higher strength (often twice that of austenitic grades like 316) and excellent resistance to stress corrosion cracking, pitting, and crevice corrosion. Common grades include 2205 and 2507 (super duplex). They are particularly well-suited for high-pressure applications in corrosive environments, such as offshore oil and gas (which shares similarities with some chemical plant conditions) and demanding mining applications where both strength and corrosion resistance are paramount.
- Titanium Titanium and its alloys offer an exceptional strength-to-weight ratio and outstanding corrosion resistance, especially to oxidizing acids, chlorides, and seawater. While more expensive than stainless steels, its long service life in highly corrosive environments can justify the initial investment. It is often used in specialized chemical processing and marine applications.
Material Properties and Suitability for Harsh Environments
Material | Common Grades | Corrosion Resistance (General) | Resistance to Chlorides | Strength | Temperature Limit (Approx.) | Relative Cost | Typical Applications in Harsh Environments |
Carbon Steel | e.g., 1018, 12L14 | Poor | Poor | Moderate | ~200°C (392°F) | Low | General hydraulics in non-corrosive, protected environments (not recommended for harsh) |
304 Stainless Steel | 304, 304L | Good | Fair (Pitting risk) | Moderate | ~800°C (1472°F) | Medium | Mildly corrosive environments, food processing, some mining (low chloride) |
316 Stainless Steel | 316, 316L | Very Good | Good | Moderate | ~800°C (1472°F) | Medium-High | Chemical processing, marine, mining with moderate chlorides, pharmaceuticals |
Note: Temperature limits and corrosion resistance are highly dependent on the specific chemical concentration, exposure time, and other environmental factors. Always consult detailed material datasheets and corrosion handbooks for specific applications.
Seal Material Compatibility Chart (General Overview)
Seal Material | Common Name(s) | Temperature Range (Approx.) | Petroleum-Based Fluids | Water/Glycol Fluids | Dilute Acids | Concentrated Acids |
NBR | Nitrile, Buna-N | -40°C to 120°C (-40°F to 248°F) | Excellent | Good | Fair | Poor |
FKM | Viton® | -20°C to 200°C (-4°F to 392°F) | Excellent | Fair | Good | Fair-Good |
EPDM | EPDM | -50°C to 150°C (-58°F to 302°F) | Poor | Excellent | Good | Poor |
FFKM | Kalrez®, Chemraz® | -15°C to 320°C (5°F to 608°F) | Excellent | Excellent | Excellent | Excellent |
PTFE | Teflon® | -200°C to 260°C (-328°F to 500°F) | Excellent | Excellent | Excellent | Excellent |
HNBR | Hydrogenated Nitrile | -40°C to 150°C (-40°F to 302°F) | Excellent | Good | Fair | Poor |
VMQ (Silicone) | Silicone | -60°C to 230°C (-76°F to 446°F) | Fair (Special grades better) | Good | Poor | Poor |
Connector Design and Type: Optimizing for Performance and Safety
Beyond the crucial choice of materials, the design and type of hydraulic connector significantly influence its performance, reliability, and safety in harsh mining and chemical environments. Different designs offer varying strengths in terms of pressure handling, vibration resistance, ease of assembly, and leak integrity. Understanding these differences is key to optimizing your hydraulic system.
Threaded Connectors
Threaded connectors are widely used due to their familiarity and broad availability. However, their suitability for harsh environments depends heavily on the specific thread type and sealing mechanism.
- NPT (National Pipe Taper): NPT threads create a seal through metal-to-metal wedging of the tapered threads, typically requiring a sealant (tape or paste) to ensure a leak-tight connection.
- JIC (Joint Industry Council) / SAE J514 37° Flare: JIC connectors use a 37° flared tube end that mates with a 37° seat in the fitting body, creating a metal-to-metal seal.
- BSPP (British StandardPipe Parallel) / ISO 1179: BSPP ports have parallel threads and require a bonded seal or O-ring on a spot face to create the seal. The threads themselves provide mechanical strength but not the primary seal.
- ORFS (O-Ring Face Seal) / SAE J1453: ORFS connectors feature a straight thread and an O-ring in a groove on the face of the male fitting, which compresses against a flat face on the female fitting.
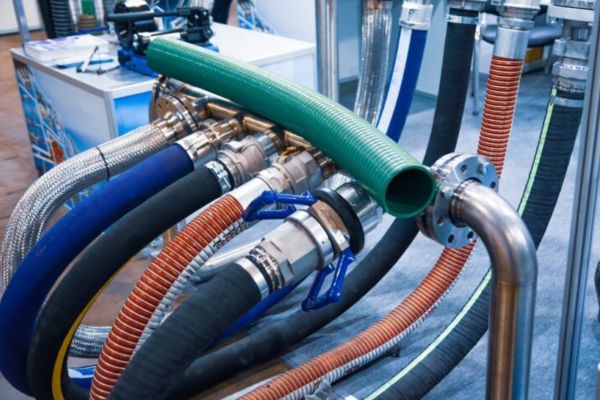
Welded Connectors
For applications demanding the highest level of leak integrity, particularly in critical chemical processing lines or permanent installations, welded connectors offer a permanent, robust solution.
Socket Weld vs. Butt Weld:
Socket Weld: The pipe or tube is inserted into a recessed area of the fitting, then welded around the outside. Easier to align than butt weld fittings.
Butt Weld: The pipe/tube and fitting ends are beveled and welded together, creating a smooth internal bore. Generally preferred for higher integrity and less flow restriction.
Considerations for installation and inspection: Welding requires skilled, certified welders and often involves more complex installation procedures (e.g., purging for certain materials). Inspection (e.g., radiographic, dye penetrant) is critical to ensure weld quality. Not suitable for components that require frequent disassembly.
Quick-Connect Coupling
Quick-connect couplings allow for fast and easy connection and disconnection of hydraulic lines without tools, which can be beneficial for maintenance or reconfigurable equipment.
- Material and design considerations for harsh duty: For mining and chemical use, quick-connects must be made from corrosion-resistant materials (e.g., stainless steel) with durable seals compatible with the fluids and environment. Designs should minimize dirt ingression when disconnected and provide robust locking mechanisms to prevent accidental disconnection under pressure or vibration.
- Spillage and contamination risks: While some designs (e.g., flat-face) minimize spillage and air inclusion, there is always a higher risk compared to permanent connections. Careful selection and operation are necessary to mitigate these risks, especially when handling hazardous chemicals.
Selecting the appropriate connector design involves a trade-off between factors like pressure capability, leak resistance, vibration handling, ease of assembly, and cost. The specific demands of the mining or chemical application will guide the optimal choice.
Beyond Material and Type: Critical Selection Factors
While choosing the right material and connector type forms the foundation of a resilient hydraulic connection, several other critical factors must be meticulously evaluated to ensure optimal performance and safety in the demanding environments of mining and chemical industries. Overlooking these aspects can lead to premature failures, even with high-quality materials and designs.
Pressure Ratings and Safety Factors
Understanding and respecting pressure ratings is paramount for safe hydraulic system operation.
Understanding Working Pressure, Proof Pressure, and Burst Pressure:
- Maximum Allowable Working Pressure (MAWP): This is the maximum pressure the connector is designed to sustain continuously under normal operating conditions. It should never be exceeded during regular operation.
- Proof Pressure: This is a quality control test pressure (typically 2x MAWP) that the connector must withstand without permanent deformation or leakage. It verifies the structural integrity of the design and manufacturing.
- Burst Pressure: This is the pressure at which the connector is expected to fail (typically 4x MAWP for many hydraulic components). It provides a margin of safety.
Importance of Derating for Temperature and Dynamic Loads: Published pressure ratings are often specified at ambient temperature (e.g., 70°F or 20°C). As operating temperatures increase, the strength of materials (both metallic and elastomeric seals) decreases, which can necessitate a reduction (derating) of the MAWP. Similarly, systems experiencing significant pressure spikes, surges, or high-cycle dynamic loads may require connectors with higher safety factors or specific designs to handle these stresses.
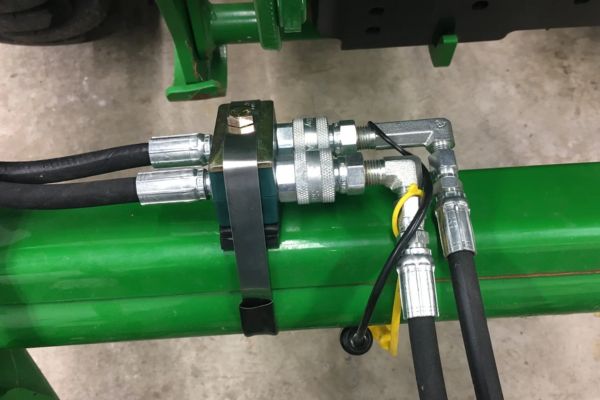
Temperature Considerations: Ambient and Fluid
Temperature extremes, both from the surrounding environment and the hydraulic fluid itself, can significantly impact connector performance.
- Ambient Temperature: In mining, equipment can be exposed to sub-zero temperatures or extreme desert heat. Chemical plants might have localized hot spots near reactors or cryogenic processes. The connector body and seal materials must maintain their mechanical properties and sealing capability across the entire expected ambient temperature range.
- Fluid Temperature: The hydraulic fluid temperature can rise due to system inefficiencies, high workloads, or proximity to heat sources. High fluid temperatures can accelerate seal degradation, reduce fluid viscosity (potentially affecting lubrication and sealing), and lower the effective pressure rating of the connector. Conversely, very low temperatures can make seals brittle and increase fluid viscosity, straining pumps and potentially affecting connector performance.
Vibration and Mechanical Stress Resistance
As discussed earlier, vibration is a major concern, especially in mining. Connectors must be selected for their ability to resist loosening and fatigue under such conditions.
- Anti-vibration Features and Designs: Certain connector designs inherently offer better vibration resistance (e.g., ORFS, flange connectors). Some threaded connectors may incorporate features like elastomeric locknuts, thread-locking compounds (ensure chemical compatibility), or specific torque procedures to enhance their security. Proper routing and clamping of hoses can also significantly reduce stress on connectors.
Certifications and Standards Compliance (e.g., NACE, API, ISO)
Adherence to recognized industry standards and certifications provides an assurance of quality, performance, and often, material traceability.
- NACE MR0175/ISO 15156: Specifies material requirements for resistance to sulfide stress cracking in sour gas environments (relevant for some chemical and petrochemical applications, and occasionally in mining where sour conditions exist).
- API (American Petroleum Institute) Standards: While primarily for oil and gas, some API standards for high-pressure fittings or materials can be relevant for demanding hydraulic applications.
- ISO (International Organization for Standardization) Standards: Many hydraulic connectors (e.g., ISO 6162 for flange connectors, ISO 8434 for various threaded connectors) are governed by ISO standards, ensuring interchangeability and minimum performance criteria.
- Other relevant certifications: Depending on the application, certifications related to pressure equipment directives (e.g., PED in Europe), specific industry approvals (e.g., MSHA for mining safety), or third-party type approvals can be important.
By systematically considering these factors in conjunction with material and connector type, users in the mining and chemical industries can significantly enhance the reliability and safety of their hydraulic systems, moving beyond a simple component purchase to a strategic selection process.
Conclusion
Choosing the right hydraulic connector is critical for system safety and durability, especially in harsh environments. From material selection to design compatibility, every detail matters. At Topa, we combine expert guidance, custom solutions, and a wide product range to meet your toughest challenges. Don’t risk failure with the wrong fittings—partner with Topa for connectors that perform under pressure. Contact us now to discuss your needs or place an order.
FAQ
How do I choose fittings for mining or chemical applications?
Start by analyzing environmental factors like abrasion, vibration, extreme temperatures, and chemical exposure.
Why is material selection so important for harsh duty fittings?
The right material ensures resistance to corrosion, wear, and temperature damage—critical for long-term system integrity.
Which fitting designs are best for high-vibration systems?
ORFS, flanged, and welded designs are preferred because they provide secure, leak-resistant connections under stress.
What pressure and temperature ratings should I look for?
Always select fittings with appropriate safety margins above your system’s maximum operating conditions.
How can I reduce connector failures in critical systems?
Use certified products, follow industry best practices, and consult with experts for proper sizing and selection.
Does Topa offer support for custom harsh-duty applications?
Yes, our engineers can help you design or choose the best connectors for extreme environments based on your exact needs.