Hose clamps are commonly used in automotive cooling systems, securing fuel lines, and in various other applications where hoses need to be firmly attached to fittings. The effectiveness of these clamps lies not just in their design but also in how well they are tightened. A properly tightened hose clamp prevents leaks, ensures a stable connection, and prolongs the lifespan of the hose and the overall system. Conversely, improper tightening can lead to leaks, hose damage, and even system failure, highlighting the importance of understanding how to correctly use these small yet vital components.
Understanding Hose Clamps
Hose clamps are versatile tools used to secure hoses over fittings, ensuring that fluids or gases do not escape from the system. There are several types of hose clamps, each designed for specific applications and conditions.
Worm Gear Clamps
Worm gear clamps are among the most commonly used hose clamps, known for their versatility and reliability. They consist of a stainless steel band with a screw housing and a captive screw. As the screw is tightened, the band tightens around the hose, securing it in place.
Typical Uses: Worm gear clamps are widely used in automotive applications, particularly in securing hoses in cooling systems, fuel lines, and air intakes. They are also common in household plumbing, where they secure hoses in dishwashers, washing machines, and garden hoses. Due to their ability to apply consistent pressure, worm gear clamps are ideal for applications where a strong, adjustable hold is required.
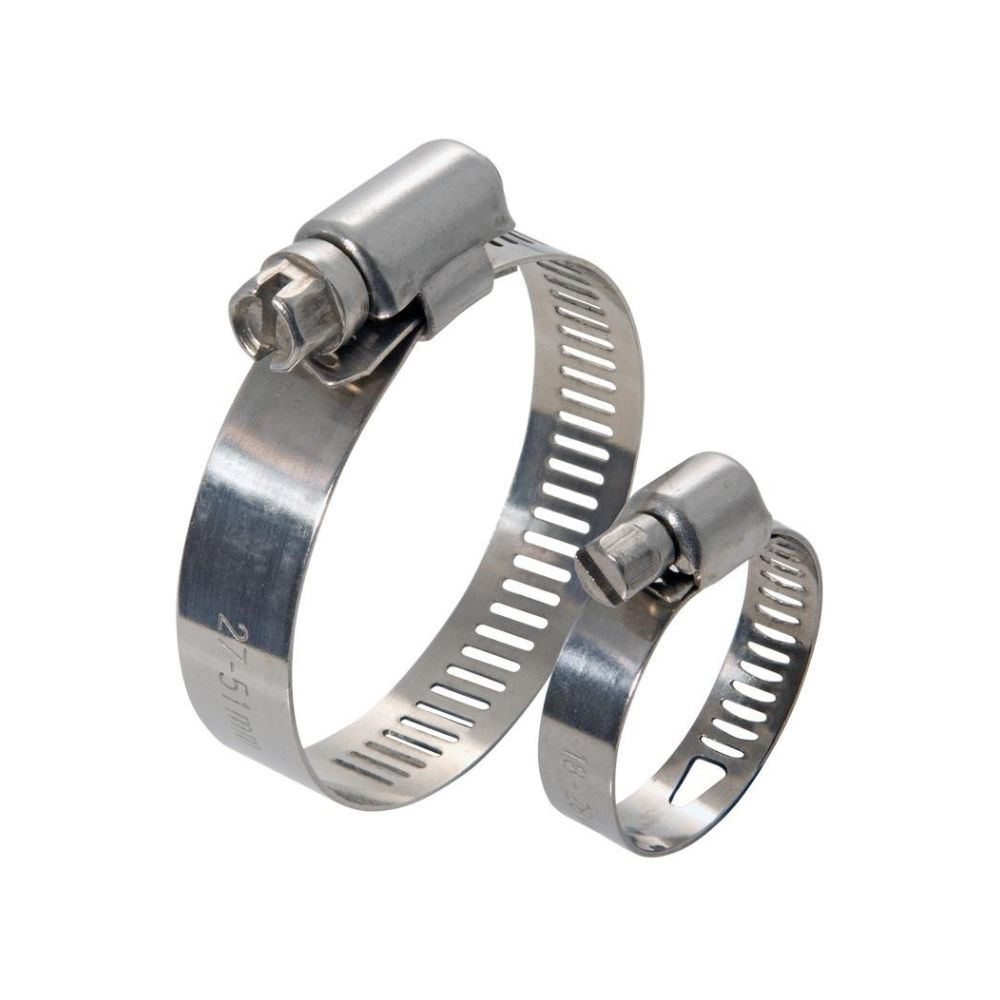
T-Bolt Clamps
T-bolt clamps are heavy-duty clamps designed for high-pressure applications. They feature a steel band and a T-bolt, which is tightened using a nut. This design allows for a strong and even clamping force, making them suitable for heavy-duty applications.
Typical Uses: T-bolt clamps are typically used in industrial settings, such as securing hoses in high-pressure hydraulic systems, turbochargers in automotive engines, and in heavy machinery where extreme conditions demand a robust clamping solution. Their ability to maintain a tight seal under high pressure makes them a preferred choice in performance and industrial applications.
Spring Clamps
Spring clamps, also known as constant-tension clamps, are made from a band of spring steel. They maintain constant tension by expanding and contracting with temperature changes, ensuring a consistent seal.
Typical Uses: Spring clamps are often used in automotive cooling systems where the hose material may expand and contract with temperature fluctuations. They are particularly effective in maintaining a tight seal on rubber hoses, preventing leaks even as the material changes size. Spring clamps are also used in some home appliance connections where temperature variations are expected.
Ear Clamps
Ear clamps, also known as Oetiker clamps, are a type of clamp that is fastened by closing the “ear” with a special tool, which tightens the clamp around the hose. These clamps are often made of stainless steel and provide a tamper-proof seal.
Typical Uses: Ear clamps are commonly used in applications requiring a permanent, secure seal, such as in pneumatic and hydraulic systems. They are also used in medical devices and food processing equipment where a consistent, leak-free connection is critical. Ear clamps are ideal for applications where the clamp will not need to be removed and where a streamlined, low-profile clamp is beneficial.
Others
While worm gear, T-bolt, spring, and ear clamps are among the most common, other types of hose clamps are used for specific needs:
- Screw/Band Clamps: Similar to worm gear clamps but typically lighter-duty, these are used in low-pressure applications where a quick and easy adjustment is needed. They are often found in home plumbing and garden hoses.
- Quick-Release Clamps: These clamps are designed for applications where hoses need to be frequently removed and reattached. They feature a quick-release mechanism that allows for fast and easy operation without the need for tools. They are commonly used in automotive and marine applications where speed and convenience are essential.
- Robust Clamps: These clamps are similar to T-bolt clamps but with added features for extreme durability, such as reinforced bands and high-torque bolts. They are used in applications with extreme pressure or where the connection is subject to heavy vibrations.
Essential Tools for Tightening Hose Clamps
Tightening hose clamps properly requires the right tools to ensure a secure and leak-free connection. Different clamps may require different tools, and selecting the correct tool can make the process smoother and more effective.
Screwdrivers
Screwdrivers are one of the most common tools used for tightening hose clamps, particularly for worm gear clamps.
Types:
- Flathead Screwdrivers: These have a single, flat blade that fits into the slotted screw heads of some hose clamps. Flathead screwdrivers are simple and widely available, making them a common choice for basic worm gear clamps.
- Phillips Screwdrivers: Featuring a cross-shaped tip, Phillips screwdrivers are designed to fit into the corresponding cross-head screws. They provide better grip and reduce the chance of slipping compared to flathead screwdrivers.
Suitability for Different Clamps:
Flathead screwdrivers are suitable for older or simpler hose clamps that have slotted screw heads. However, they can be prone to slipping, especially if the clamp is tight or if the screwdriver blade is not a perfect fit.
Phillips screwdrivers are generally more reliable for tightening clamps with cross-head screws, as they offer better engagement with the screw, reducing the risk of stripping the screw head and providing more consistent torque.
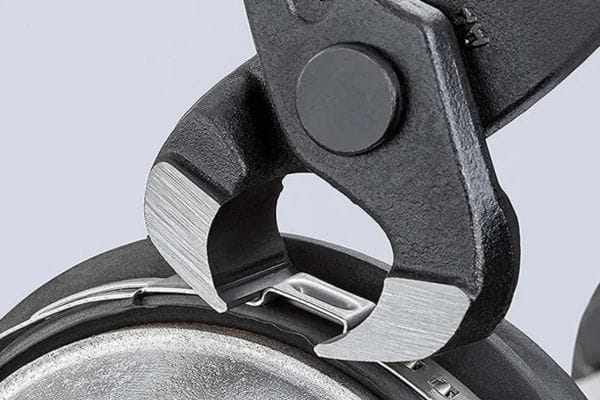
Socket Wrenches
Socket wrenches are versatile tools that can apply more torque than screwdrivers, making them ideal for tightening hose clamps that require a strong and even clamping force.
Benefits:
- Higher Torque: Socket wrenches allow you to apply greater torque compared to screwdrivers, ensuring that the clamp is tightened evenly and securely. This is particularly important for larger clamps or those used in high-pressure applications.
- Precision: Socket wrenches are available in various sizes, allowing you to select the perfect fit for the clamp’s screw head. This reduces the risk of stripping the screw and ensures a more precise and secure tightening process.
Suitability for Different Clamps:
Socket wrenches are particularly useful for T-bolt clamps and heavy-duty worm gear clamps, where more torque is needed to achieve a tight and secure fit. They are also effective in situations where space is limited, as they can reach areas where screwdrivers might not fit easily.
Torque Wrenches
Torque wrenches are specialized tools designed to apply a specific amount of torque to a fastener, ensuring that it is neither too loose nor too tight.
Importance:
- Accurate Tightening: Using a torque wrench ensures that the hose clamp is tightened to the manufacturer’s specified torque value, which is crucial for maintaining a secure connection without damaging the hose or fitting.
- Consistent Results: Torque wrenches provide consistent tightening across multiple clamps, which is especially important in professional or industrial applications where uniformity is required.
Suitability for Different Clamps:
Torque wrenches are ideal for applications where precise clamping force is essential, such as in automotive, industrial, or high-pressure hydraulic systems. They are often used with T-bolt clamps and other heavy-duty clamps where consistent pressure is critical.
Pliers
Pliers are versatile tools that can be used to tighten certain types of hose clamps, particularly those that do not have a screw mechanism.
When and How to Use Pliers:
- Spring Clamps: Pliers are commonly used to install and tighten spring clamps. These clamps rely on the tension of the steel band to maintain a secure fit, and pliers are used to compress the clamp during installation.
- Ear Clamps: For ear clamps, specialized pliers (often called pincer tools) are used to crimp the “ear” of the clamp, tightening it around the hose.
Suitability for Different Clamps:
Pliers are most effective for spring clamps and ear clamps, where the clamping force is applied through compression or crimping rather than through a screw mechanism.
Specialized Tools
In addition to the common tools, there are specialized tools designed for specific types of hose clamps, offering more precision and ease of use.
Hose Clamp Pliers:
These are specialized pliers designed specifically for removing and installing spring clamps. They often feature a locking mechanism that holds the clamp in the open position, making installation easier, especially in tight spaces.
Ear Clamp Pincers:
Pincers are used to crimp ear clamps, ensuring a tight and permanent seal. They are designed to provide the necessary force to close the clamp’s ear securely, ensuring a leak-free connection.
Flexible Hose Clamp Drivers:
These tools feature a flexible shaft that allows for the tightening of clamps in hard-to-reach areas. They are particularly useful in automotive and HVAC applications where access is limited.
Step-by-Step Guide to Tightening Hose Clamps
Preparation Before Tightening
Inspecting the Hose and Clamp
Before you begin tightening a hose clamp, it’s essential to inspect both the hose and the clamp for any signs of damage or wear:
Hose Inspection:
Check the hose for any visible cracks, splits, or abrasions, especially near the ends where the clamp will be positioned. Even minor damage can lead to leaks or hose failure under pressure.
Feel the hose to ensure it is flexible and not brittle. If the hose has become stiff, it may not seal properly even when clamped tightly.
Clamp Inspection:
Examine the clamp for any signs of corrosion, especially if it’s been used in a harsh environment. Rust or corrosion can weaken the clamp, leading to potential failure.
Ensure that the screw mechanism (for worm gear or T-bolt clamps) operates smoothly. If it’s stiff or difficult to turn, it might not tighten evenly.
For spring or ear clamps, check that the clamp retains its shape and tension. If the spring action feels weak or the ear is misshapen, the clamp may not provide an adequate seal.
Positioning the Clamp
Proper positioning of the clamp on the hose is vital for a secure connection:
Placement on the Hose:
Position the clamp about 1/4 inch (6mm) from the end of the hose, ensuring that it is not too close to the edge, which could cause the hose to slip off the fitting when tightened.
Make sure the clamp is evenly spaced around the hose, with no part of the clamp hanging off the edge or sitting on a bulge. Uneven placement can lead to an inadequate seal and potential leaks.
Aligning with the Fitting:
The clamp should be placed over the section of the hose that is seated on the fitting’s barbed or ribbed area. This ensures that the clamp compresses the hose material firmly against the fitting, creating a tight seal.
Avoid placing the clamp directly over the barb’s edge, as this can cause the clamp to cut into the hose when tightened, potentially leading to leaks or hose damage.
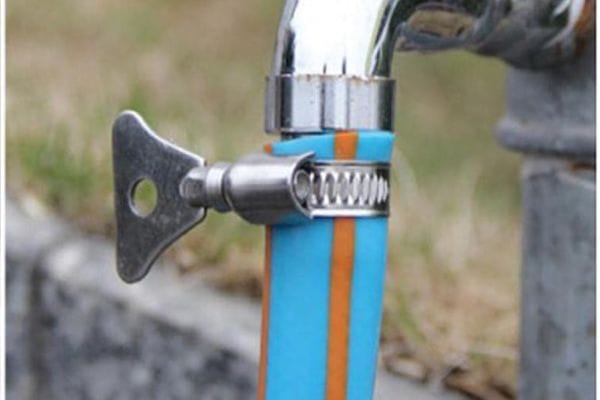
Pre-Tightening Tips
Before you start tightening, here are a few tips to ensure everything is properly aligned:
- Align the Hose: Ensure the hose is fully seated on the fitting and is aligned straight. Twisted or angled hoses can create uneven pressure, leading to leaks.
- Hold the Hose in Place: If the hose tends to slip or move while tightening the clamp, you can temporarily secure it with a piece of tape or a second clamp positioned loosely until the first clamp is tightened.
- Check the Clamp’s Position: Make a final check to ensure the clamp is in the correct position and that the screw or tightening mechanism is easily accessible.
Tightening Process
Once the hose and clamp are properly positioned, you can proceed with tightening. The tool you use will depend on the type of clamp.
Using a Screwdriver
Screwdrivers are commonly used for worm gear clamps and other clamps with a screw mechanism. Here’s how to tighten using a screwdriver:
- Select the Right Screwdriver: Choose a screwdriver that fits the clamp’s screw head perfectly. A flathead or Phillips screwdriver can be used depending on the screw type.
- Position the Screwdriver: Insert the screwdriver into the screw head, ensuring it is fully engaged to avoid stripping the screw.
Tighten the Clamp:
- Turn the screwdriver clockwise to tighten the clamp. Apply steady pressure and turn the screw evenly.
- Tighten the clamp until it feels snug but not overly tight. The goal is to create a firm seal without crushing the hose.
- Check the Seal: Once tightened, inspect the clamp to ensure it’s evenly applied and that the hose is securely attached to the fitting.
Using a Socket Wrench
Socket wrenches are ideal for clamps requiring higher torque, such as T-bolt clamps. Here’s how to tighten using a socket wrench:
- Choose the Correct Socket: Select a socket that matches the size of the clamp’s bolt or nut.
- Attach the Socket: Attach the socket to the wrench and fit it over the clamp’s bolt or nut.
Tighten the Clamp:
- Turn the wrench clockwise to tighten the clamp. Socket wrenches allow for greater torque, so apply pressure gradually.
- Continue tightening until the clamp feels secure. Avoid overtightening, which can damage the hose or the fitting.
- Inspect the Fit: After tightening, check the clamp and hose for a secure, even seal.
Using a Torque Wrench
- Torque wrenches are used when precise torque is required to avoid under or over-tightening. Here’s how to use one:
- Set the Torque: Refer to the manufacturer’s specifications for the recommended torque setting for your clamp. Adjust the torque wrench to the specified setting.
- Position the Wrench: Fit the torque wrench over the clamp’s bolt or nut, ensuring a snug fit.
Tighten to Specification:
- Turn the wrench clockwise to tighten the clamp. The wrench will provide resistance as you approach the set torque.
- The wrench will “click” or indicate when the desired torque is reached, signaling that the clamp is properly tightened.
- Verify the Seal: Double-check the clamp to ensure it’s securely fastened without overtightening.
Special Considerations for Different Clamp Types
Different types of clamps require specific tightening techniques:
Spring Clamps:
Use pliers to compress the clamp and slide it over the hose and fitting.
Release the pliers to allow the clamp to contract and create a tight seal. Ensure the clamp is evenly positioned around the hose.
Ear Clamps:
Use a pincer tool to crimp the “ear” of the clamp, tightening it around the hose.
Ensure the crimp is even, and the clamp is securely in place without gaps.
Quick-Release Clamps:
Adjust the clamp to the correct size and position it over the hose.
Use the quick-release mechanism to secure the clamp in place. Double-check that the clamp is firmly attached.
Post-Tightening Inspection
After tightening the clamp, it’s essential to perform a thorough inspection to ensure everything is secure.
Checking for Leaks
Once the clamp is tightened, check the connection for leaks:
- Visual Inspection: Look for any signs of moisture or fluid seeping from the connection point. Pay close attention to the areas around the clamp.
- Pressure Test: If possible, run the system at low pressure and observe the connection for leaks. Gradually increase the pressure on the system’s operating level while continuing to monitor for leaks.
Final Adjustments
If any issues are identified during the inspection, make the necessary adjustments:
- Tightening: If there is a minor leak, carefully tighten the clamp a little more. Use the same tool you initially used, and avoid overtightening.
- Repositioning: If the hose or clamp has shifted during tightening, loosen the clamp slightly, reposition it, and then re-tighten.
- Replacing the Clamp: If the clamp appears to be defective or unable to secure a leak-free connection, replace it with a new one.
Common Mistakes and How to Avoid Them
Over-Tightening
Dangers of Over-Tightening
Over-tightening hose clamps is a common mistake, often made with the intent of ensuring a tight seal. However, this approach can lead to several problems:
- Hose Damage: When a clamp is tightened too much, it can compress the hose excessively, causing it to become pinched or crushed. This damage weakens the hose structure, making it more prone to leaks, cracks, or even complete failure under pressure.
- Reduced Clamp Effectiveness: Over-tightening can also deform the clamp itself, particularly if it’s a worm gear or band clamp. The screw threads can strip or the band can warp, reducing the clamp’s ability to maintain a consistent seal over time. This can lead to gradual loosening and potential leaks.
How to Avoid Over-Tightening
- Use a Torque Wrench: To prevent over-tightening, use a torque wrench to apply the manufacturer’s recommended torque. This ensures that the clamp is tightened to the correct level without exceeding the hose’s tolerance.
- Regular Inspection: Periodically check the condition of the hoses and clamps, particularly after initial installation. Look for signs of hose deformation or stress, which could indicate over-tightening.
- Gradual Tightening: Tighten the clamp gradually, checking the hose for compression as you go. Stop tightening as soon as the hose feels secure and there are no visible signs of excessive compression.
Under-Tightening
Risks of Under-Tightening
Under-tightening is another common mistake that can lead to significant issues:
- Leaks: A hose clamp that is not tightened sufficiently may fail to create a proper seal, allowing fluids or gases to escape. This can lead to leaks, which in turn can cause system inefficiencies, contamination, or even hazardous conditions, depending on the application.
- Clamp Slippage: Without enough tension, the clamp may not hold the hose securely in place. Over time, vibration or pressure changes can cause the hose to slip off the fitting, resulting in a sudden and potentially catastrophic failure.
How to Avoid Under-Tightening
- Ensure Proper Tool Use: Use the correct tool for the type of clamp. A socket wrench or torque wrench is often more effective than a screwdriver for achieving the right amount of tension.
- Check for Secure Fit: After tightening, give the hose a gentle tug to ensure it is firmly attached to the fitting and that the clamp holds securely. There should be no movement between the hose and the fitting.
- Monitor During Use: Particularly in high-pressure or high-vibration environments, regularly inspect the hose clamps to ensure they have not loosened over time. Retighten as necessary to maintain a secure connection.
Misalignment of Clamps
Problems Caused by Improperly Aligned Clamps
Misalignment of hose clamps is a frequent issue that can undermine the effectiveness of the connection:
- Uneven Pressure: If a clamp is not aligned correctly, it may apply uneven pressure to the hose, leading to an inadequate seal. This can cause leaks at the point where the pressure is weakest.
- Hose Damage: Misalignment can also cause the clamp to cut into the hose or create points of stress, increasing the risk of hose failure. Over time, this can lead to wear and tear, reducing the lifespan of both the hose and the clamp.
How to Avoid Misalignment
- Proper Placement: Ensure the clamp is positioned evenly around the circumference of the hose, about 1/4 inch from the hose end. It should be placed directly over the fitting’s barbed or ribbed area for optimal sealing.
- Double-Check Alignment: Before final tightening, check that the clamp is parallel to the hose end and that no part of the clamp is hanging off the hose or seated on a bulge.
- Use Markers: For critical installations, consider marking the hose and fitting to guide the correct placement of the clamp, ensuring consistent alignment.
Incorrect Tool Usage
Impact of Using the Wrong Tools or Incorrect Techniques
Using the wrong tools or applying incorrect techniques can compromise the clamp’s effectiveness:
- Tool Slippage: Using an improperly sized screwdriver or socket can lead to tool slippage, stripping the clamp’s screw, or damaging the hose. This can prevent the clamp from being adequately tightened and may require replacement.
- Inconsistent Tightening: The wrong tool can also result in uneven or inconsistent tightening, creating weak points in the seal where leaks can develop.
How to Avoid Incorrect Tool Usage
- Choose the Right Tool: Match the tool to the clamp type. For example, use a socket wrench for T-bolt clamps, a torque wrench for precise tightening, and the appropriate screwdriver (flathead or Phillips) for worm gear clamps.
- Use Specialized Tools: For spring or ear clamps, use specialized tools like hose clamp pliers or pincer tools to achieve a secure fit without damaging the clamp or hose.
- Follow Best Practices: Apply consistent pressure and avoid over-rotating or forcing the tool. If a tool feels difficult to use, reassess whether it’s the right choice for the job.
Ignoring Maintenance
Importance of Regular Inspections and Maintenance for Long-Term Effectiveness
Neglecting regular inspection and maintenance can lead to gradual deterioration of the hose clamp connection:
- Wear and Tear: Over time, hose clamps can loosen due to vibration, thermal expansion, or material fatigue. Without regular checks, these changes can go unnoticed until a failure occurs.
- Corrosion and Damage: Clamps exposed to harsh environments, such as marine or industrial settings, can corrode or degrade. If not identified and addressed early, this can lead to leaks or clamp failure.
How to Avoid Ignoring Maintenance
- Scheduled Inspections: Establish a routine for inspecting hose clamps, especially in critical or high-pressure systems. Look for signs of wear, corrosion, or loosening.
- Replace as Needed: If a clamp shows signs of damage or corrosion, replace it promptly to prevent system failure.
Conclusion
Throughout this guide, we’ve highlighted the importance of using the right tools, such as screwdrivers, socket wrenches, and torque wrenches, to apply the correct amount of torque and avoid over-tightening or under-tightening. We’ve also discussed the need for proper clamp alignment and the risks associated with using incorrect tools or techniques. By following the detailed steps and tips provided, you can ensure that your hose clamps are installed effectively, reducing the risk of leaks and system failures.
FAQ
What is the best tool to use for tightening hose clamps?
A screwdriver, socket wrench, or torque wrench is typically used, depending on the clamp type and the level of precision required.
How tight should a hose clamp be?
A hose clamp should be tightened until it’s snug but not so tight that it damages the hose. Using a torque wrench can help apply the correct amount of torque.
Can over-tightening a hose clamp cause problems?
Yes, over-tightening can crush or damage the hose, leading to leaks or hose failure.
How often should I inspect hose clamps?
Hose clamps should be inspected regularly, especially in high-pressure or high-vibration environments, to ensure they remain secure and free of corrosion or damage.
What should I do if my hose clamp is leaking?
Check if the clamp is properly positioned and tight. If necessary, tighten it further or replace the clamp if it’s damaged.
Can I reuse hose clamps?
Some hose clamps can be reused if they are in good condition and not deformed or corroded. However, spring and ear clamps are generally designed for single use.