You pick a fitting with a 5,000 PSI rating, assuming it’s safe for your 4,500 PSI system. But a sudden pressure spike causes a catastrophic failure, spraying hot oil and halting your operation.
Hydraulic fitting pressure ratings are classified by a combination of the fitting’s design standard (like ORFS, JIC, DIN), its size, and its material. The published rating is the Maximum Allowable Working Pressure (MAWP), which is the burst pressure divided by a 4:1 safety factor.
What is the Fundamental Principle Behind a Pressure Rating?
You see a pressure rating stamped on a fitting, but what does it truly represent? Is it the absolute maximum pressure the fitting can ever withstand before it breaks?
No, the number you see is the Maximum Allowable Working Pressure (MAWP). It’s a safe, continuous operating limit. The actual burst pressure is much higher, typically four times the MAWP, to account for real-world pressure spikes, vibration, and temperature changes.
This is the most important concept to grasp. A hydraulic fitting is not like a chain that breaks the instant you exceed its load limit. It’s an engineered component with a built-in safety buffer. This buffer is called the Safety Factor (SF).
Understanding the 4:1 Safety Factor
The industry standard for dynamic hydraulic systems—systems where pressures change, valves open and close, and loads move—is a 4:1 safety factor. The formula is simple:
Burst Pressure / Safety Factor = Maximum Allowable Working Pressure (MAWP)
This means if a fitting has a published MAWP of 5,000 PSI, the manufacturer has tested it and guarantees that it will not burst until at least 20,000 PSI.
Component | Minimum Burst Pressure | Safety Factor (SF) | Maximum Allowable Working Pressure (MAWP) |
Hydraulic Fitting | 20,000 PSI | 4:1 | 5,000 PSI |
Hydraulic Fitting | 12,000 PSI | 4:1 | 3,000 PSI |
Why Is Such a Large Safety Factor Necessary?
A 4:1 ratio might seem excessive, but it is essential for safety and reliability. Hydraulic systems are not static. The safety factor is there to absorb the energy from:
- Pressure Spikes: A valve slamming shut or a cylinder stopping abruptly can cause instantaneous pressure surges that are two to three times the normal operating pressure.
- Vibration: Constant machine vibration can cause fatigue in the metal over time.
- Temperature Changes: As temperatures rise, the strength of the metal can slightly decrease.
- Assembly Variations: Minor differences in how the fitting is tightened can affect its performance.
The 4:1 safety factor ensures that even with all these real-world stresses, the fitting will operate reliably for its entire service life.
How Do Different Fitting Standards Determine Ratings?
You have two fittings that are the same size, but one is a JIC fitting and the other is an ORFS fitting. Why is one rated for significantly higher pressure than the other?
The pressure rating is directly tied to the fitting’s sealing mechanism. An O-Ring Face Seal (ORFS) fitting creates a highly contained, robust seal suitable for extreme pressures, while a tapered pipe thread (NPT) fitting relies on thread deformation and is rated for much lower pressures.
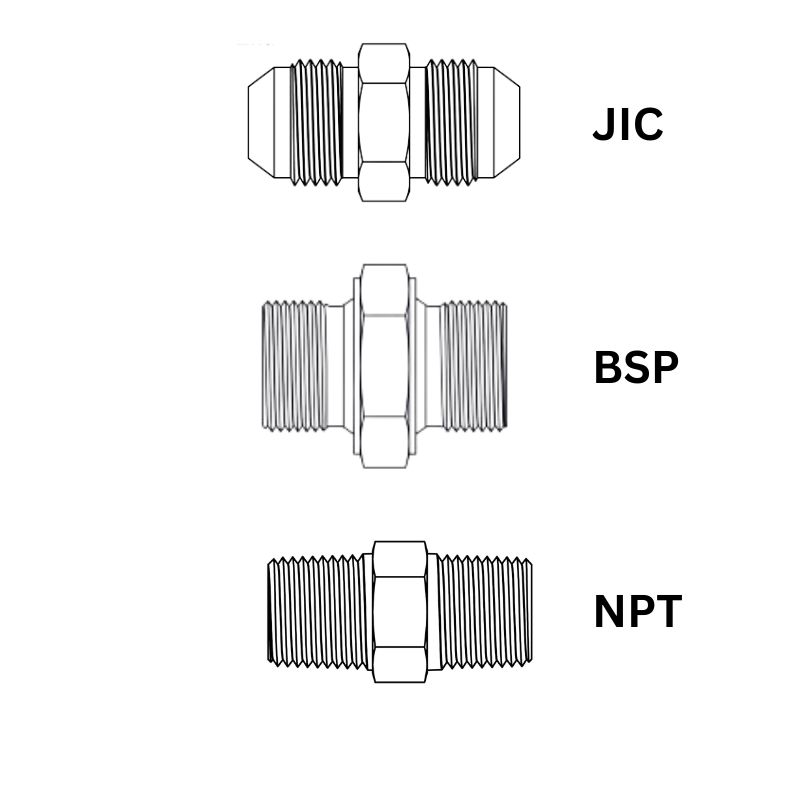
The design standard is the single biggest factor influencing a fitting’s pressure rating. How a fitting creates a seal dictates how well it can contain high pressure without leaking or failing. As a supplier, this is one of the first things we clarify with a customer.
A Comparison of Common Fitting Sealing Designs
Let’s look at how the most common standards are designed and how that affects their ability to handle pressure.
Fitting Standard | Sealing Mechanism | Typical Pressure Range | Key Advantage |
ORFS (O-Ring Face Seal) | O-Ring compressed against a flat face | Very High (up to 6,000 PSI+) | Virtually leak-proof, excellent for vibration |
DIN (Metric Bite Type) | Hardened ferrule bites into the tube | High (up to 8,000 PSI for S Series) | Excellent grip, very popular in Europe/Asia |
JIC (37° Flare) | Metal-to-metal seal on a 37° cone | Medium to High (up to 5,000 PSI) | Very common, reliable, easy to assemble |
NPT (Tapered Pipe Thread) | Threads deform and mash together | Low | Simple, widely available for general use |
Why a Better Seal Equals a Higher Rating
The O-Ring Face Seal (ORFS) fitting is a perfect example of design driving performance. The seal is not made by the threads at all. The threads simply provide the clamping force to press two flat faces together, compressing a soft O-ring in a groove. This creates a seal that is incredibly resistant to vibration and can handle very high pressures.
In contrast, a National Pipe Taper (NPT) fitting creates a seal by having the tapered threads of the male and female fittings literally crush into each other. This metal-on-metal deformation seal is prone to leakage without a sealant like PTFE tape and is not structurally sound enough for high-pressure hydraulic applications. This is a mistake I often see with buyers who are new to hydraulics; they try to adapt lower-pressure pipe fittings for high-pressure systems, which is extremely dangerous.
Why Does Fitting Size Dramatically Change the Pressure Rating?
You successfully used a 1/4 inch JIC fitting in a 5,000 PSI system. So you assume that a larger 1 inch JIC fitting made of the same material will also be safe at 5,000 PSI. This is a common and dangerous misunderstanding.
As a fitting’s diameter increases, so does the surface area that the pressure acts upon. To prevent failure, the maximum allowable working pressure must be decreased for larger sizes of the same fitting style to maintain the required 4:1 safety factor.
This inverse relationship between size and pressure rating is a fundamental principle of physics, but it often catches people by surprise. The reason is simple: Force equals Pressure multiplied by Area (F = P x A
).
The Physics of Pressure and Size
Imagine the fluid inside a hydraulic hose. The pressure (PSI, or pounds per square inch) is pushing outwards on every square inch of the interior surface.
- For a small 1/4 inch fitting, the internal surface area is small. At 5,000 PSI, the total separating force trying to push the fitting apart is manageable.
- For a large 1 inch fitting, the internal surface area is sixteen times greater. At the same 5,000 PSI, the total separating force is now sixteen times higher. The walls of a realistically sized fitting cannot withstand this immense force.
To keep the fitting safe, manufacturers must “de-rate” the allowable pressure as the size goes up.
Example Pressure Ratings by Size (JIC 37° Flare – Steel)
Every fitting catalog, including ours at Topa, includes a chart that shows this relationship clearly. Here is an illustrative example for a common JIC steel fitting.
Fitting Size (Dash) | Tube OD (inches) | MAWP (PSI) |
-04 | 1/4″ | 5,000 |
-06 | 3/8″ | 5,000 |
-08 | 1/2″ | 4,000 |
-10 | 5/8″ | 3,500 |
-12 | 3/4″ | 3,000 |
-16 | 1″ | 2,500 |
-20 | 1 1/4″ | 2,000 |
This is why, when a client sends an inquiry for a list of fittings, we don’t just check the thread type. We check the size and cross-reference it with their stated operating pressure to ensure every single fitting on their list is correctly rated for the job.
How Critically Do Material Choices Affect the Pressure Rating?
You see three identical fittings, but one is made of brass, one of carbon steel, and one of stainless steel. Does the material they are made from change how much pressure they can safely handle?
Yes, the material is a critical factor. Carbon steel is the standard for high-pressure hydraulics due to its high strength and cost-effectiveness. Stainless steel offers corrosion resistance with comparable strength, while brass has much lower strength and is only suitable for low-pressure applications.
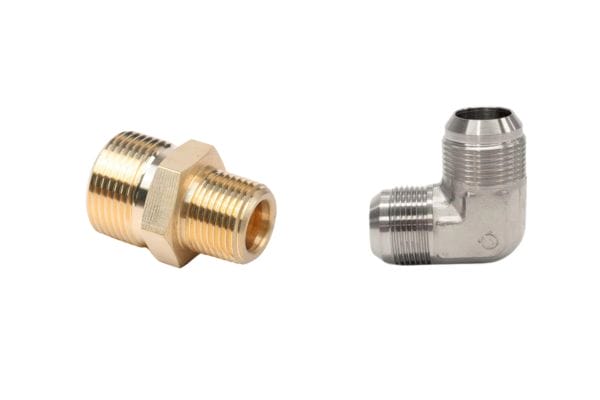
The strength of the material, specifically its tensile strength (the ability to resist being pulled apart), directly impacts the pressure rating. Choosing the right material is a balance of strength requirements, environmental corrosion, and cost.
Comparing the Big Three Materials
- Carbon Steel (e.g., 1045, 12L14): This is the default choice for most hydraulic applications. It possesses very high tensile strength, it’s easy to machine, and it’s economical. To protect it from rust, we plate it with a durable zinc coating (often trivalent zinc for better corrosion resistance and environmental compliance). Nearly all the high-pressure JIC, ORFS, and DIN fittings we supply are made from high-quality carbon steel.
- Stainless Steel (e.g., SS 316): The primary advantage of stainless steel is its excellent corrosion resistance. This makes it essential for food processing, marine, and chemical applications. The strength of 316 stainless steel is very good, and its pressure ratings are often identical or only slightly lower than their carbon steel counterparts. A professional buyer from the UAE working on a desalination plant will specify stainless steel not for extra pressure, but for survival against the salty environment.
- Brass: Brass is an alloy of copper and zinc. It’s easy to machine and has good corrosion resistance for water and air, but it has significantly lower tensile strength than steel. As a result, brass fittings are never used in high-pressure hydraulic systems. Their use is limited to automotive fluid lines, plumbing, and low-pressure pneumatic systems. Using a brass fitting in a place where a steel fitting is required is one of the most dangerous material substitutions possible.
How Do Invisible Pressure Spikes Affect Your Fittings?
Your system’s pressure gauge always reads a steady 3,000 PSI, well below your fittings’ 4,000 PSI rating. Yet, after some time, a fitting develops a leak or fails. Why does this happen?
The gauge only shows the average pressure. Your system experiences invisible, instantaneous pressure spikes (hydraulic shock) that can be double or triple the working pressure. The fitting’s 4:1 safety factor is specifically designed to withstand thousands of these spikes over its lifetime.
This is a concept that is critical for anyone in maintenance or equipment design to understand. Static pressure is easy to manage; it’s the dynamic forces that wear a system down.
What Causes Hydraulic Shock?
Hydraulic shock, sometimes called water hammer, happens when a moving column of hydraulic fluid is forced to stop or change direction suddenly. Think about the momentum of that incompressible fluid. That energy has to go somewhere, and it converts into a high-pressure shockwave that travels through the system at the speed of sound. Common causes include:
- Valves closing rapidly: This is the most common cause.
- A hydraulic cylinder reaching the end of its stroke at high speed.
- A pump starting or stopping suddenly.
- A heavy load on an actuator being abruptly halted.
The Role of the Safety Factor and Fitting Type
A failure due to pressure spikes is a fatigue failure. The fitting doesn’t break on the first spike. It breaks after being subjected to thousands or millions of these high-stress cycles. This is precisely why the 4:1 safety factor exists. It keeps the stress from each spike well below the material’s ultimate failure point, allowing it to survive for years of service.
This is also where premium fitting designs show their value. The O-ring in an ORFS fitting acts as a small cushion and creates a seal that is extremely resistant to being loosened by these repeated shockwaves, making it the preferred choice for systems with high cyclic rates and shock potential.
What Is the “Weakest Link” Rule for Your Hydraulic Assembly?
You have meticulously selected a high-quality hose rated for 6,000 PSI and robust fittings rated for 6,000 PSI. You assume the complete hose assembly is now rated for 6,000 PSI. Is this assumption correct?
Not necessarily. A hydraulic system’s maximum pressure is always dictated by its single lowest-rated component. You must check the rating of the hose, and every single fitting and adapter in the line. The lowest number is the true MAWP of the assembly.
This is the final and most crucial check that must be performed when designing or repairing any hydraulic system. It’s a simple rule, but it is frequently overlooked, especially when adapters are involved.
An Example of the Weakest Link Rule in Action
Let’s build a common hydraulic line and see how this works.
- Component 1: Hydraulic Hose: Rated for 5,000 PSI.
- Component 2: Fitting (Hose End): A JIC fitting rated for 5,000 PSI.
- Component 3: Adapter (Bulkhead): Another JIC fitting rated for 5,000 PSI.
- Component 4: Adapter (90° Elbow): A JIC elbow fitting. Due to the geometry, it is only rated for **4,000 PSI**.
In this scenario, many people would assume the system is safe to 5,000 PSI. This is incorrect. The entire assembly, from the hose to the final connection, has a Maximum Allowable Working Pressure of **4,000 PSI**. Running this system at 4,500 PSI would mean you are operating without an adequate safety factor, risking a premature failure at the elbow fitting.
Our Commitment as Your Supplier
This is why our team at Topa is trained to be so detail-oriented. When we get an order from a customer, we don’t just see a list of part numbers. We see a system. We help our clients by reviewing their lists and pointing out potential rating mismatches. Our goal is not just to sell fittings; it is to provide our clients with safe, reliable hydraulic systems that last. This commitment to detail is what turns a simple transaction into a long-term partnership.